3D Metalforge (3DMF) is a global Additive Manufacturing (AM) company. 3DMF recently announced the successful delivery of additively manufactured heat exchanger parts to Shell Jurong Island, a dedicated chemical site based in Singapore and owned by Royal Dutch Shell plc (“Shell”).
All text and images courtesy of 3D Metalforge
Singapore is Shell’s largest petrochemical production and export centre in the Asia Pacific region. Shell Jurong Island manufactures chemical intermediates to meet the strong and fast-growing demand for these products in the region and beyond.
Heat exchanger tube components are thin-walled metal tubes inserted into the inlet-end of condensers and heat exchangers to transfer heat or help prevent tube failures within the heat exchanger tube inlet-end. In this case, 3D Metalforge’s goal in working with Shell Jurong Island was to help extend the life-span of the existing equipment and produce replacement parts faster and more cost-effectively, particularly in time-sensitive situations where downtime or replacement create a signifi cant impact on clients’ operations.
Certification
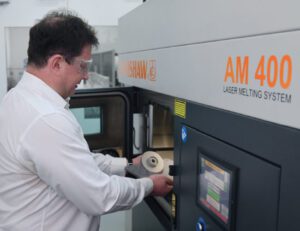
Shell Jurong Island’s engineers chose to use 3D Metalforge and additive manufacturing to reduce the required lead time to manufacture heat exchanger tube components. The company worked closely with Shell Jurong Island engineers to understand the part’s performance requirements.
Routine collaboration between 3DMF’s engineering staff and customers’ own technologists means the company’s products are engineered and manufactured to specifically address the demands of each customer, part, use, and their geographic (supply chain) challenges. The company’s design team then created a digital file for the parts prior to production. Following 3D print production, during the post-production quality review, parts were subjected to integrity detection tests to assure these components met client specifications. Certification to industry, API and ISO, standards mean all 3DMF’s product quality is guaranteed. Complete documentation on each customer solution improves overall quality, assures customers that the company has met their specifications and as a result provides customers with greater flexibility in their operations.
3DMF was able to successfully complete the required parts, manufacture, certification and delivery, in a record timeframe of two weeks.
Timely delivery and quality parts
“We appreciate 3D Metalforge for their exceptional technical services and their timely and successful delivery of quality parts to Shell Jurong Island”, commented Pina Joshi, Asset Rejuvenation Senior Reliability Engineer in Shell Jurong Island.
The scope of this project demonstrates the 3D Metalforge’s continuing commitment to leading the way in the development of new additive manufacturing technologies; custom-engineered solutions and streamlined processes that deliver a faster response and the shorter turn-around times customers need. It also validates the company’s strategy that fit-for-purpose additive manufacturing capabilities can result in signifi cant cost savings for clients.
“We were extremely pleased to provide our additive manufacturing technologies for this project for Shell Jurong Island in record time which ultimately helped improve the lifespan of existing equipment. Our primary goal is to be a trusted service provider, this is what customers desire over everything else. We work every day to provide greater value to our clients and this is an excellent validation of the benefits of our technology and of the increasing adoption of additive manufacturing.” said Matthew Waterhouse, 3D Metalforge CEO.
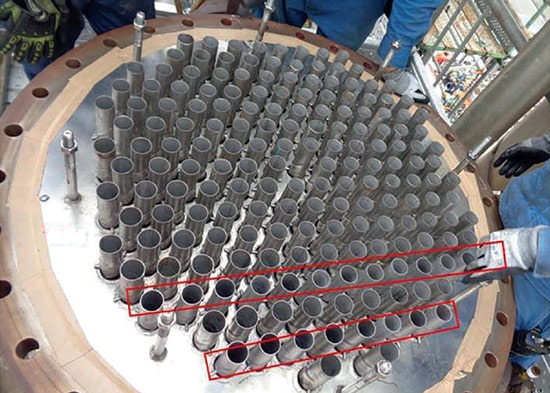
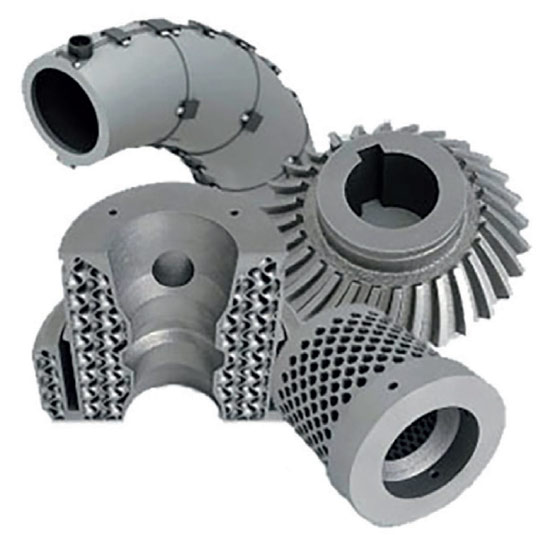
About 3D Metalforge
3D Metalforge, founded in 2015, is a leading additive manufacturing company supporting a growing multinational industry-leading client base with advanced proprietary 3D additive manufacturing systems. It offers a full range of in-house AM printing services from design and engineering, material advisory, diagnostics and testing, to printing and post-production certification to the latest industry and API standards. The companys’s approach to industrial production, its proprietary processes, and eco-friendly technology produce high-demand parts faster and more cost effectively with less environmental impact and greater sustainability than conventional manufacturing. The resulting product improvements, and savings in time and costs result in enhanced profitability and return on manufacturing investment.