Enabling staff to accurately identify undefined problems ahead of time and the cause of defined problems allows plants to operate much more reliably and efficiently, says Precognize’s Chen Linchevski.
OEM independent SAM GUARD can be easily applied to all process industry facilities, he stresses.
By Chen Linchevski, CEO, Precognize, Israel
Problems in process plants can be loosely categorized into two main types: predefined or repeating problems, and undefined or non-repeating ones. While both types cause loss of income and unnecessary outlay, undefined problems have a far greater impact on revenue and productivity. Let’s look at how each type fits into the rubric of predictive analytics, and how Precognize’s SAM GUARD can predict and prevent both types of problems, generating clear return on investment. Our core competence is in identifying and solving the undefined, non-repeating problems, however SAM GUARD of course also has a solution for the defined problems, which are actually much easier to deal with.
Defined problems
Predefined, repeating problems are when the problem is known. It’s something that has happened before and repeats fairly often. Repeating problems are common around process improvement, like aiming to maintain the golden batch. Engineers can use Precognize’s SANDBOX to find out which tags are relevant for that problem, to spot the causes of the problem and find the parameters and monitor them if relevant. The SANDBOX can connect between seemingly unrelated parameters, identifying the root cause. A bigger challenge lies in alerting plant engineers to non-repeating, undefined problems that arise. Predicting defined and undefined problems in process plants seemingly out of nowhere, because there’s no historical data to prepare you for such events.
Undefined, non-repeating problems
Undefined problems are ones that do not repeat themselves, like most cases in the process industry. In these cases, the issue never occurs in the same place or in the same way twice, making it unexpected. Examples of undefined problems include equipment failures, small process deviations, and changes to the operating process because of equipment failure, malfunction, or abnormality. In process plants, non-repeating problems occur more often than repeating problems, but they remain harder for most solutions to predict and analyze. Here are several examples of non-repeating problems, and how SAM GUARD identified them and created new value for the plants:
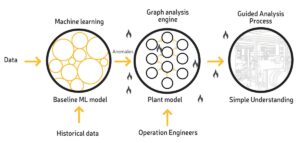
Petrochemical example: partial blockage in heat exchanger
At a petrochemical plant, SAM GUARD alerted due to substantial differences in temperature, combined with multiple parameters measured in the heat exchanger and other related parts of the plant. All of the measurements showed an accelerated fouling process, indicating a partial blockage in the heat exchanger which was the operational root cause. As a result of this combined alert, the heat exchanger was cleaned, and the partial blockage was removed. It was determined that while the heat exchanger had been partially blocked it had led to higher energy costs and increased fluid velocity, causing potential erosion problems; if it had not been fixed in time, it would have eventually led to a plant shutdown and lost production.
Solving undefined problems
Most predictive analytics solutions use machine learning (either supervised or unsupervised) to identify problems in process plants. Every plant has thousands, if not tens of thousands, of sensors, covering every asset. Only machine learning can make sense out of this onslaught of data; it is far too much for a human analyst to process. However, supervised machine learning is dependent on historical examples, to “train” the model, and this is impossible for non-repeating problems. Without enough historical examples, supervised machine learning can’t be used, and by definition, non-repeating problems have few, if any, historical examples. At the same time, unsupervised machine learning isn’t relevant, because the torrent of data is overwhelming. With so many data points and possible states, unsupervised machine learning cannot define any “normal” state to serve as a background against which to spot anomalies. From an unsupervised machine learning point of view, a standard petrochemical or chemical processing plant is made up entirely of anomalies. Also, not very helpful. Traditional predictive analytics solutions are of limited use in these situations, because the lack of defined tags and problems prevents the engineer from analyzing the problem, and the volume of data is too great for traditional solutions to spot patterns and come up with warnings ahead of time.
SAM GUARD predicts defined AND undefined problems
The good news is that there is a solution that can cope with undefined problems. Precognize SAM GUARD is unique in combining human domain knowledge with machine learning, enabling plant engineers to identify the causes and pinpoint solutions even for undefined, non-repeating problems. SAM GUARD draws on a plant domain model that takes into consideration the specific structure and behavior of the plant. This is rapidly created at the start of the engagement and it enhances the machine learning, guiding users to the right areas of the plant to identify potential issues that may never have occurred before. It can be easier to predict and thus prevent the defined problems, but the undefined ones occur much more frequently and can be a massive headache to plant owners and operators. Avoiding these unforeseen problems is the ultimate goal of every predictive analytics program in petrochemical and chemical plants and this adds much more value to the plant as a whole. With the help of SAM GUARD, plants can prevent these undefined, non-repeating problems.
SAM GUARD IN A NUTSHELL
SAM GUARD background
• Covers the entire plant: with few historical events and the interconnectedness of process plants, you never know where the next failure will appear; with SAM GUARD you don’t need to pick and choose what to monitor, simply track everything.
• No alert fatigue: instead of hundreds of alerts per day, SAM GUARD generates up to 5 alerts, giving you early, actionable warning.
• 1-2 weeks implementation: with a swift implementation process and no hardware required, SAM GUARD is up and running quickly, analyzing your plant’s data, triggers actionable alerts.
• No data-scientist needed: alerts are analyzed by the plant’s operation staff, with no specialized training needed.
SAM GUARD enables you to
• Detect equipment failures ahead of time
• Identify suspicious process behavior
• Identify suspicious operation modes
• Analyze root cause
Time prior to failure (based on historical events)
• 3 weeks to a few hours
Number of alerts, False alert ratio
• An average of 5 alerts a day (depending on plant’s stability)
• 30% attribute to events which are not equipment failure (planned maintenance, new operation method etc.)
User categories
• Process engineers, control room technicians, maintenance engineers, production managers, and shift leaders
Number of tags per plant supported by the solution
• From 100 to 10000s historian tags per plant.
Implementation requirements
• Cloud-based or on your corporate network
• SAM GUARD can be installed on any Virtual Machine running Linux. Space can be provided on our server, free of charge, or install the application on your own servers
MEET THE AUTHOR
Chen Linchevski, CEO, Precognize. Chen, a true believer in the ability of the industrial sector to transform itself and increase efficiency, took raw ideas and transformed them into promising companies. Throughout the execution Chen demonstrated true leadership and vision. Precognize, of which he’s CEO today, was nominated by the World Economic Forum as Tech Pioneer of 2018 and acquired by Samson Group. During his career, Chen worked with key industrial companies such as GE, BASF, Shell, and LG, specializing in the design and analysis of complex industrial systems. More info: www.precog.co
About this Featured Story
This Featured Story was first published in the May 2021 issue of Heat Exchanger World Magazine. To read more Featured Stories and many other articles, subscribe to our print magazine.
Featured Stories are regularly shared with our Heat Exchanger World community. Join us and share your own Featured Story on Heat Exchanger World online and in print.