Dr Reza Javaherdashti is a materials scientist and metallurgical engineer with a PhD in corrosion. At the end of 2021, he established the company MICCOR, a consultancy for trouble-shooting corrosion related issues in industrial processes, with a special focus on microbial corrosion (MIC). It is a topic the Dr feels must be given closer consideration in order to save money, resources and, in some cases, lives.
By Ellie Pritchard
I spoke with Dr Javaherdashti about the dangers of MIC for heat transfer equipment, common misconceptions surrounding the topic, and how to manage and protect against corrosion.
Dr Javaherdashti begins: “Metals are preferred for almost all heat exchanger components due to their strength, high resistance to stresses, and high thermal conductivity. Typically, the preferred metals are copper, stainless steel, and titanium. It is important to understand that all so-called engineering materials (except titanium) are susceptible to MIC.”
The multiple costs of corrosion
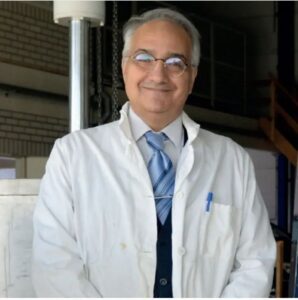
The cost of corrosion can be divided into multiple categories; financial cost, asset cost, and human cost. According to Dr Javaherdashti, the financial cost of corrosion accounts for between 3% to 6% of a country’s gross national product (GNP); within this, 10-40% could be attributed specifically to MIC. Zooming in even further onto the heat transfer sector, a 2001 study found that in power plants where heat exchangers are commonly used, the cost of corrosion is about USD 7 billion [1].
This can be further supported by a 2016 study by NACE International which concluded that the annual global cost of corrosion amounts to USD 2.5 trillion [2].
“My personal view is that the cost of MIC is well above 10% of this overall corrosion cost,” states
Dr Javaherdashti. “But even with 10%, it is clear that this is a major drain on resources and money – it is immensely important to manage the resources we have in order to control this cost.”
When looking to the other dangers associated with mismanaged corrosion, Dr Javaherdashti cites multiple occasions in which a corroded heat exchanger has led to environmental contamination or damage, the release of poisonous products, or explosion.
“In 2010, an incident in a refinery plant unfortunately led to 7 fatalities,” he offers as an example. “A carbon steel shell and tube heat exchanger, lined with stainless steel 316, was subject to a high temperature hydrogen attack (a form of corrosion) which then caused the escape of hot hydrogen and naphtha. The autoignition between these two substances caused the fatal fire”. Further examples cover galvanic corrosion between carbon steel and titanium cladding in heat exchange equipment, and a 2012 case in which a shell and tube unit was operational for only 36 months before microbial corrosion reduced the wall thickness from 6,2mm to 2mm.
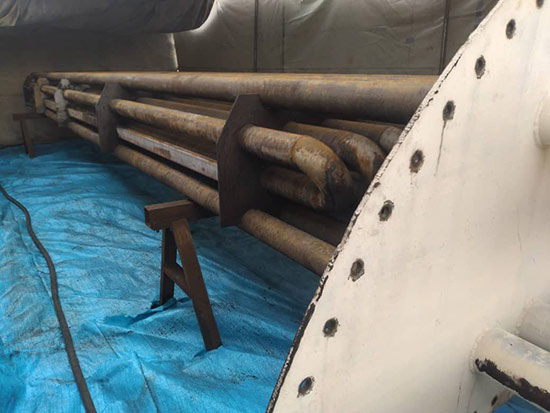
What is microbial corrosion?
Microbial corrosion (MIC) is brought about by the activities and presence of microbes. this occurs in several forms and can be managed by traditional control methods including application of biocides. This process of degeneration chiefly acts on met-als (ferrous such as steels and non-ferrous such as copper-nickel alloys) as well as non-metals, such as polymers, composites and concrete. Apart from bacteria, microbial corrosion can also be influenced by archaea, micro algae and algae. this form of corrosion affects industry plants like power plants and chemical industries where heat exchangers and cooling systems are frequently used. (source: corrosionpedia)
How does MIC occur?
“MIC is enhanced, or sometimes even decelerated, by the action of certain bacteria, fungi, or algae,” Dr Javaherdashti explains. “There is now a lot of knowledge about the way that bacteria can contribute to corrosion. Some of these bacteria are capable of producing sulphuric acid with a pH of 1 which is quite acidic. Some are able to change the chemistry of the environment, rendering it more vulnerable to a higher rate of corrosion.” “But, most of the time these different types of bacteria come together and establish communities, to which many refer to as ‘biofilm’. I no longer use this term ‘biofilm’ as what we are referring to is not a film, but rather patchy in nature. It is also not 100% biological – only around 3% of the dry weight of biofilm is composed of biological materials – the rest is non-biological.”
Instead, Dr Javaherdashti proposes the Greek term ‘Temenos’ which means ‘cut off’ – this emphasises that the conditions under the so-called biofilm are far differ-ent to exterior conditions.
“The external environment could have oxygen, the pH could be neutral, everything could look normal,” he explains. “But beneath the “film”, the story could be very different – it could be acidic or have a low oxygen level. In the case of heat exchangers, bacteria collected under Temenos can cause inefficient heat transfer due to an additional layer through which heat transfer was supposed to take place.”
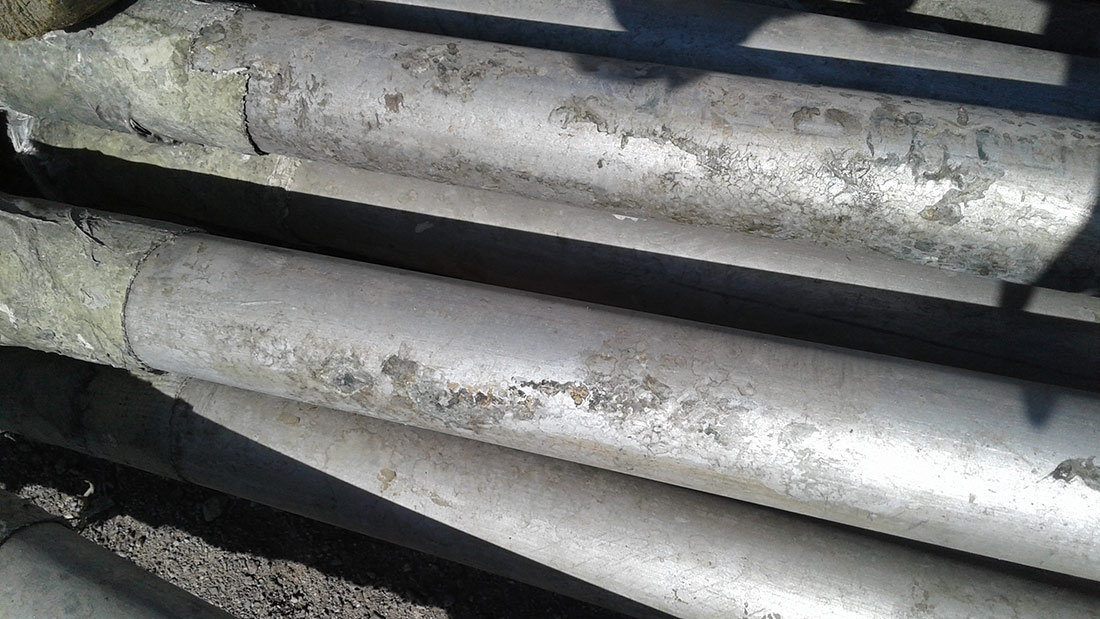
Prevention over treatment
As the many different forms of corrosion (from galvanic, to stress corrosion cracking, to MIC) appear to as-sist each other, Dr Javaherdashti advocates for a holistic approach towards corrosion management.
“We are dealing with a world which is constantly changing; bacteria can adapt and be resistant to high temperatures or low acidic environments,” says Javaherdashti. “It is so important to think of prevention rather than treatment, because the latter is so expensive and the former can save us money.”
There are 5 methods through which corrosion can be managed:
• Physical: application of coatings – physically separating the corrosive environment from the vulnerable substrate
• Chemical: using corrosion inhibitors or biocides
• Electrical: cathodic protection
• Mechanical: Pipeline Inspection Gauge (PIGs) – running PIGs within pipes destroys Temenos formed in the pipeline
• Design change or material upgrade – this could be using stainless steel instead of carbon or titanium instead of copper
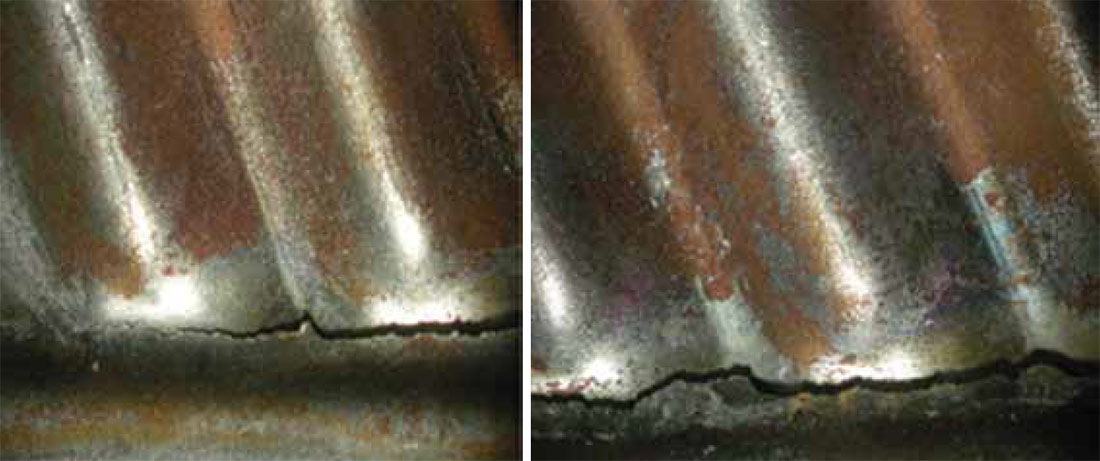
Coatings – a more sustainable option
However, with many of these methods come environmental repercussions. Biocides, for example, release dangerous chemicals into the environment, and material upgrade requires further stainless steel to be produced through an energy intensive process. Javaherdashti refers to official standards which do recommend material upgrade as a measure for better corrosion management particularly in case of MIC option [3].
For this reason, Javaherdashti’s work has focused on protective coatings: “In my opinion, coatings are the more sustainable option.”
Invented by Dr Arezoo Assarian, CEO of Eninco Engineering BV, and supervised by Dr Javaherdashti, a coating has been produced which does not kill the bacteria but instead creates an uninhabitable environment.
“Most of the time when people are dealing with corrosion, the optimal solution is believed to be eradicating the bacteria,” he explains. “But our philosophy is that every part of nature is there for a reason, and we do not have the right to destroy it even if it is damaging our assets – it is an essential part of our universe. Instead, we can create an environment in which these bacteria will no longer thrive and feel comfortable, thus deterring them from even spawning.”
Dr Assarian has invented a coating method which can be coded to a user’s desired requirements. “It is a very sophisticated technology,” affirms Javaherdashti. “We hope that by being pro-environment, we can prove to the paint and coatings industry that we really don’t need to be polluting our environment in order to protect our assets.”
Drs Assarian and Javaherdashti are currently working to develop this coating on an industrial scale. “The lab results have been beyond our expectations. We can even envisage this antimicrobial coating being applied beyond industrial use, to help reduce likelihood of contamination in more general applications – for example, public places such as train stations, hospitals, schools, shopping malls and the like.”
But the coating is not enough as Dr Javaherdashti stresses that just as important as the material is the application skills of the engineer or technician applying it. Any gap in the coating’s attachment to the substrate is an area vulnerable to corrosion, rendering the coating ineffective.
Training and monitoring
Besides treatment, Javaherdashti identifies other aspects of corrosion management which he feels must be addressed, namely a lack of adequate training and irregular monitoring of the systems.
“There is a serious knowledge gap in this industry, and it needs to be addressed,” he says. “There needs to be a better understanding of what corrosion is, and what it is not, how to manage it, the pros and cons of various methods for identifying and treating MIC. These are things that can only be covered fully in training programmes.” He has noticed that the younger generations of corrosion experts are coming mostly from China, whereas the European pool of experts are either approaching retirement or have already retired, thus leading towards an inevitable drain of knowledge and experience particularly in the field of MIC.
And on the topic of monitoring, Dr Javaherdashti promotes a scheduled routine for checking essential assets. “In the cases mentioned at the beginning, there were explosions, fires and, in the worst cases, fatalities – all of these can be avoided through a careful and regular corrosion monitoring system, in which MIC is also taken into account.” But this requires support which Dr Javaherdashti feels is lacking.
“We don’t currently have clear standards for this,” he says. “We have those for carrying out hydrotests in heat exchangers, or to inspect welding, and so on. But in MIC, we rely solely on the knowledge of the individual engineer working with the equipment – there are no set standards for MIC inspection.”
An MIC-safe heat exchanger requires:
• Correct material selection
• Careful welding – without forgetting post-weld treatment
• Coatings with highest possible adhesion to the substrate
• A known history – has it been hydrostatically tested, if so, under what conditions?
• A clearly defined monitoring schedule – possibly consulting a corrosion/Mic expert to avoid nasty surprises
• Engineers with specific training for dealing with corrosion
Spread the word
“In a LinkedIn post in September 2021, Egbert Stremmelaer, Managing Director of the Dutch association ‘ION’ (association of Industrial Surface Treatments) estimated that the minimum annual cost of corrosion to the Dutch economy was EUR20 billion per year – if this is indeed accurate, it would be fair to estimate a similar number across the EU, and including the UK.”
“Losing that amount of money per year for a country the size of Netherlands is no joke,” Dr Javaherdashti goes on to say. “And if we can assume that even 10% of this figure attributes to MIC, this is EUR2 billion per year. These are just relating to the direct cost of corrosion, let alone the indirect costs such as detrimental effects on the environment. But we have found that it is possible to save around 37% of this loss through more training and regular monitoring.”
Due to these figures and cases, Dr Javaherdashti feels the need to be spread the word urgently. “We have so much coverage over the topic of energy right now, but MIC is a big part of that we need to be discussing it more widely. Waste of material is just as important as following the green energy transition and it mainly comes about through corrosion. We need to spread the word about its dangers and costs.”
References
[1] Willem faes, steven lecompte, Zaaquib yunus Ahmed, Johan van bael, robbe salenbien, kim verbeken , Michel de paepe “corrosion and corrosion prevention in heat exchangers”, corrosion reviews, vol. 37, no. 2, 2019, pp. 131-155.
[2] http://impact.nace.org/economic-impact.aspx
[3] sAbp-A-087 , best practice, “identification, Monitoring, and Mitigation of Microbiologically-influenced corrosion (Mic)”, 4 february 2018.
About this Featured Story
This Featured Story was first published in Heat Exchanger World Magazine in April 2022. To read more Featured Stories and many other articles, subscribe to our print magazine.
Featured Stories are regularly shared with our Heat Exchanger World community. Join us and share your own Featured Story on Heat Exchanger World online and in print.