I recently had the pleasure of speaking with Conflux Technology – hailing from Victoria, Australia, the company specialises in additive manufactured heat transfer solutions. In an interview with CEO Michael Fuller and newly appointed Chief Product Officer Dan Woodford, we discussed the story of Conflux, both the possibilities and challenges posed by AM in the process industries, and how the company is working to exploit and address these respectively.
By Ellie Pritchard
The conflux story
We begin by discussing Michael’s wealth of background experience. In the pursuit of his boyhood dream to work with racing cars, Michael spent many years working in the motorsport industry with such institutions as Formula1, World Rally Championship, and LeMans 24 Hour Racing.
“I was exposed to the pains of thermal system efficiency and management and the specification for heat transfer devices, ranging from radiators to charge air coolers and electronics cooling as well,” Michael explains. “But it also gave me early adopter exposure to this new platform manufacturing technology, which is now known as additive manufacturing but at the time was called 3D printing.”
After moving back to Australia and taking on some consultancy work, Michael suffered a broken leg and found himself using this new ‘down time’ to design a heat exchanger using additive manufacturing. “I’d always had this idea in my head that I could make use of AM and bring some of the key inherent benefits of it, such as geometric freedoms, to a heat exchanger device.”
With a curiosity for how to commercialise such an idea, Michael worked on the concept throughout 2014, and in 2015 he patented his first design and built up a team of experts. A key turning point came in 2017 with an investment from AM Ventures – German specialist strategic investor in additive manufacturing technologies.
“Now, in 2022, we are proud to have almost 20 employees,” says Michael. “And we supply heat transfer technology to a number of different industries, including the energy sector with such applications as nuclear, renewables, and oil and gas.”
The Conflux team is also experienced in providing solutions in the general automotive and motor sport industries, aviation and aerospace (commercial and defence), semiconductors, and general industry. Their customer base spans a range of market verticals, and they are active in North America, Europe, and Asia.
Evolution
As a demonstration of Conflux’s growth, Dan Woodford has been recently appointed as the company’s first Chief Product Officer, and he aims to develop the company from a services and bespoke design business model to have a more generic and configured product engagement with the market. At the time of our interview, Dan is in his third week with Conflux, and both he and Michael are fresh from a trip around the US where they spent two weeks meeting customers and technology partners. “A lot of R&D has gone on over the years,” Dan explains. “We’ve begun a strategy of productisation, allowing focus on par-ticular markets and applications of the technology to solve specific use cases around heat exchange.”
He continues: “Conflux is now able to leverage some of the amazing facets of AM, like being able to rapidly reconfigure and reprint parts without needing to redesign, reprint, retool. So, a lot of my job is figuring out how to apply that really configurable benefit of AM to selling products into markets. In particular, making heat exchangers that can be developed and prototyped extremely fast.”
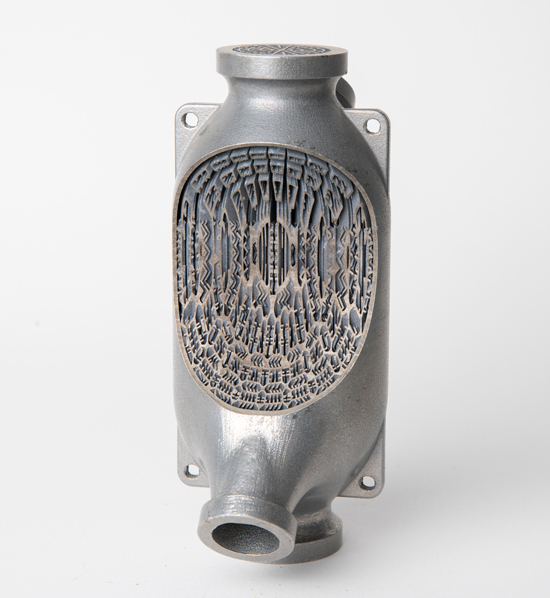
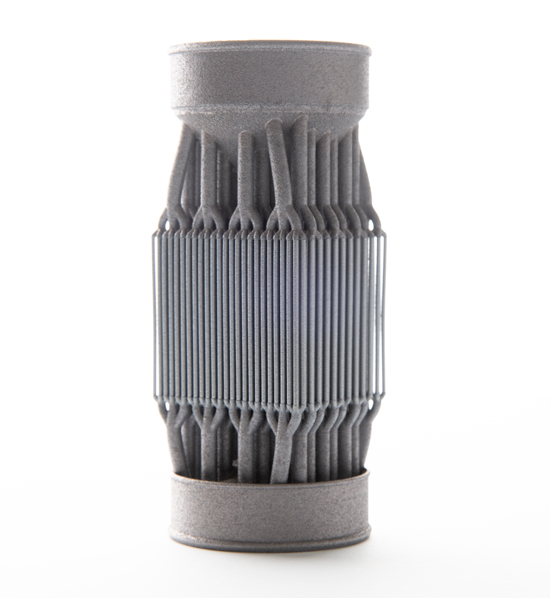
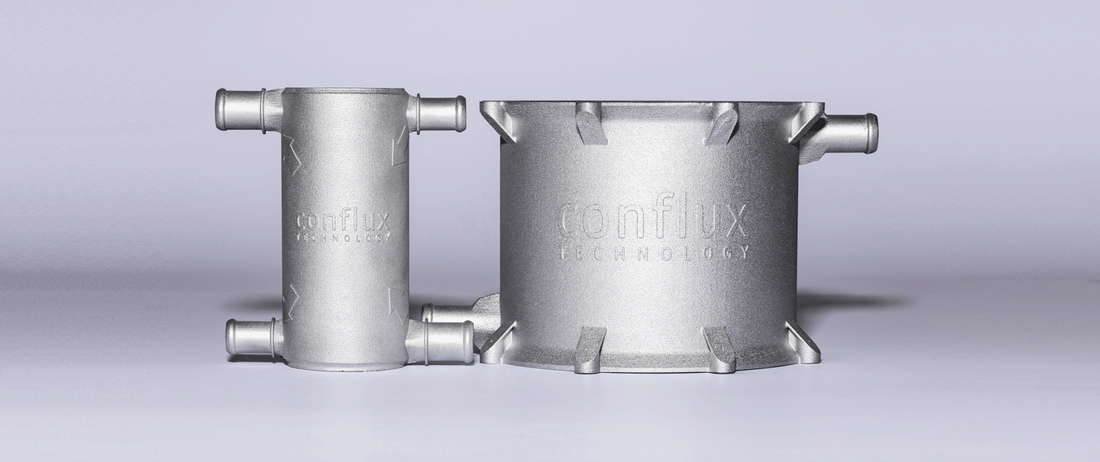
Complexity decoupled from cost
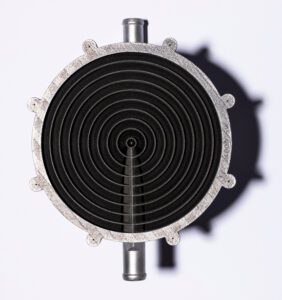
Conflux’s website claims that additive manufacturing has the capability to build highly efficient, complex geometries not possible with traditional manufacturing, and that it will ultimately disrupt the global supply chain. I asked them to expand on these claims.
“In terms of complex geometries, it’s hard to wrap your head around the profound implications of these developments,” says Michael. “To put it simply, a heat exchanger’s performance is based on its geometry.”
He asserts that, contrary to popular belief, it is not possible to 3D print anything and everything but that Conflux prides itself on pushing the limits of what AM can do. “As with most engineering disciplines, you design within the limitations of the manufacturing technologies available to you. But AM does facilitate geometries that were previously not possible.”
Complex geometries allow a highly intensified process of heat transfer, enabling high transfer levels for pressure drop trade-offs. This comes from being able to adapt the geometry dependent on the fluid boundary conditions. Michael offers an example: “The density of a fluid moving through a heat exchanger changes due to the temperature – we can modify the geometry through the fluid domain and adapt it for the changing thermal properties of the fluid. This means that we can achieve more heat exchange in a smaller form.”
If it were possible to do this through standard methods, the tooling cost would be incredibly high whereas Conflux claims that, for them, the complexity is decoupled from cost.
“Obviously, there’s the initial design overhead and you need to pay experienced and knowledgeable people to use the tools to create these geometries,” Michael acknowledges. “But once that’s done, there’s not a massive overhead and it’s certainly not connected to the complexity.” Michael attests that AM technology is in fact in a structural cost decline, meaning Conflux can bring AM heat exchangers to more markets without sacrificing high efficiency and low pressure drops through their geometries.
Disrupting the supply chain
For most process industry applications, supply chains offer the biggest delays, resulting in costly prolonged downtime. Thanks to the nature of additive manufacturing, however, Conflux has built its own decentralised near point-of-use manufacturing process.
“In the US they are called Jobbing Shops, in Germany Bureau Services, but essentially, they are contract manufacturers located all over the world capable of operating the machines we use; they can print a part on demand, avoiding materials being shipped back and forth across the globe. We can have near point-of-use production with all of the supply chain efficiencies that come with decentralised manufacture, but this hybridisation of components into a monolithic structure also means that you have a much more simplified supply chain as well.”
Michael refers to the multinational conglomerate General Electric which has incorporated this frame of manufacturing, reducing bills of materials for certain aero engine structures from 300 parts to 2 parts.
“So that step-change happens, we see this with our own heat exchangers. One example is the microtube heat exchanger; this is essentially a shell and tube unit but comprising of a multitude of thin, hypodermic needle-type microtubes with ultra-thin walls, making for highly efficient heat transfer,” Michael explains. “A unit you could hold in your hands could have 20,000 tubes which all need to be assembled and joined. But we can manufacture this in a lights-off facility – all being well, we flip the switch and the machine does the work whilst we sleep.”
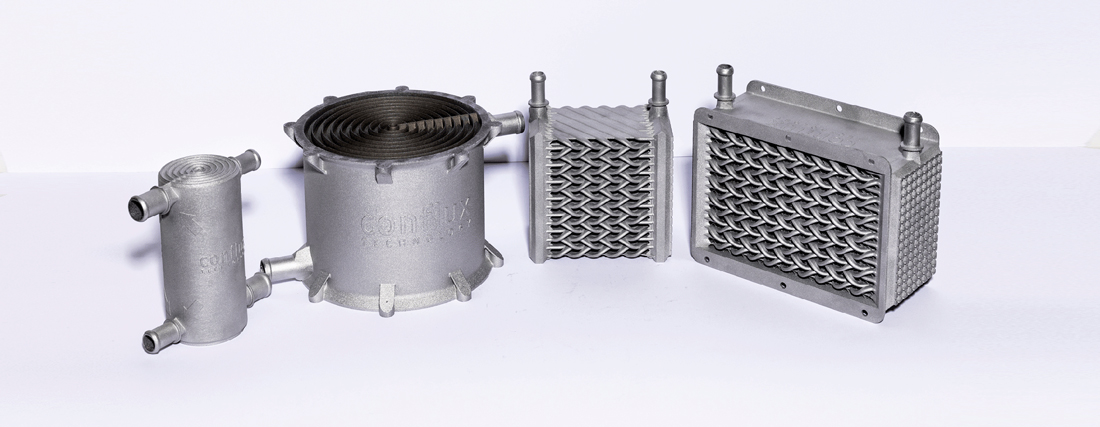
Compelling possibilities.
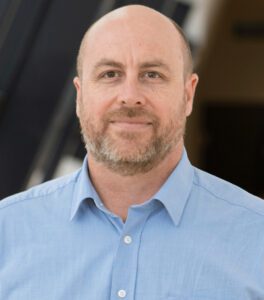
Conflux claims that the opportunities are profound; the AM technology is young, the process is becoming more productive, build volumes are growing larger, piece prices are going down. “For those considering AM as a part of their future, they are absolutely spot on,” Michael asserts. “And for those who think it’s going away – I do caution people to check what they mean when they say ‘it’ll never catch on’, because we are already creating heat exchangers that are beating the incumbent best in class in the world.” In terms of industrial scale additive manufacturing, dependent on the sector, strides have been made to print enormous parts; for example, companies such as AMCM (Additive Manufacturing Custom Machines) have printers capable of printing 1,5 – 2 metres in Z height (450 x 450 x 2000 mm build volume).
In the process industries, space can be extremely limited such as on offshore platforms. This is where AM equipment can prove invaluable, as equipment volume and weight can be significantly reduced.
“We have designed an 800MW heat exchanger for an energy industry client comprising of modular blocks. Existing joining techniques are used to join the modular blocks together,” explains Michael. “But the main benefit is that, thanks to the complex geometries, a unit can be much smaller and lighter than its traditional counterpart.”
“The opportunity to reduce weight is what keeps our customers coming back because it is compelling. All of the barriers that we’ve got in our minds about the adoption of this technology, we just can’t help but want to overcome them because it’s a compelling performance proposition.” In terms of scale, Conflux acknowledges that there is still work to be done, but the team is ready for that: “We will continue to be driven as humans to make it bigger, faster, cheaper additive manufacturing is at a much younger stage of the technology maturity curve than perhaps people think.”
To echo Michael’s sentiment, Dan offers that as a newcomer to the scene the transformations both in the company and in AM technology have been impressive. “I remember seeing Rubix cube-sized parts printed exclusively in plastic about 15-20 years ago,” he says. “And now companies are printing bridges and houses and using a vast array of materials – the scaling is already there in certain materials.”
Materials
Conflux works mostly with 316l stainless steel, and high nickel alloys when high temperatures are required. Titanium (ti-6Al-4v) is also used, although as difficult to handle in AM as it is in other standard manufacturing techniques. But there are new materials being developed all the time. The powder metal industry sees AM as a new avenue so there is a lot of development in powders for the powder bed fusion processes.
Standards and certification
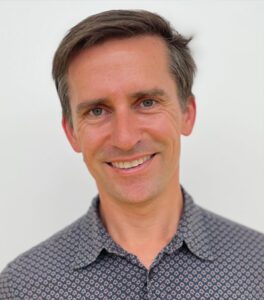
Although the company does not yet have a large array of modular units in service at this time, Conflux acknowledges that it is certainly possible. But the barriers its faces are not unique to additive manufacturing.
“We have 150 years of heat exchanger incremental development and a massive database of material conditions and mechanical characteristics, welding, bends, processing data etc. All of these things have standard codes,” says Michael. “But the standards for the technology itself need to be developed in certain applications. Some are ahead of others, for example the aerospace industry already has a lot of AM products on commercial aircraft – they’ve gone through that arduous process of getting certification. Earning certification in the aviation industry is one of the hardest things to do, so we know that if companies such as GE have been able to do it, we can certainly do it for our own applications.”
According to the Conflux team, it is a case of strong willpower, resources, and an ability to demonstrate compelling reasons in order to make the investments and to get customers and partners on board to help develop the database of certification.
Non-destructive testing
Conflux benefits from unique access to the Ansto Australian synchrotron, close to them in nearby Melbourne which runs a synchrotron (beam accelerator). They use this for non-destructive testing; large components can be placed in the high resolution ct scan and the team will have a full set of data very quickly. they are able to look at porosity, pore density distribution, pore morphology, wall thicknesses, feature distances, surface roughness – all can be quantified utilising conflux’s proprietary in-house software, conflux QuantifytM, and comparisons can be observed with process parameter changes.
Conflux can very rapidly take boundary conditions and turn them into a configurable product. Heat exchangers can be sized very quickly with the simplified tools underpinned by the very sophisticated tools. This is key to what the company is able to provide for customers.
About this Featured Story
This Featured Story was first published in Heat Exchanger World Magazine in May 2022. To read more Featured Stories and many other articles, subscribe to our print magazine.
Featured Stories are regularly shared with our Heat Exchanger World community. Join us and share your own Featured Story on Heat Exchanger World online and in print.