Metal additive technologies are increasingly being deployed to design and manufacture heat exchangers. GE continues to push forward the capabilities and performance of highly complex heat exchangers in many industries, such as aerospace.
By Curt Hogan, Staff Engineer – GE Additive
Today’s metal additive manufacturing (AM) technologies are already helping designers produce heat exchangers with features of competitive or equivalent thickness to those that have been conventionally manufactured.
At the fundamental level, utilizing the full volume of a design space to increase the surface area of heat exchangers can be harnessed to create very efficient systems that have lighter weights and better thermal management – if the part’s correct geometric and material integrity is maintained.
Applying AM to heat exchangers
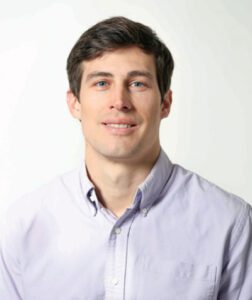
A key benefit of AM is the design freedoms it offers. Other benefits include reduced manufacturing and supply times. It is possible to design much more complex shapes to enhance the structural integrity, durability, and performance of a heat exchanger, while reducing the stress on the part. In many cases, it is also possible to adopt new shapes that wouldn’t otherwise be producible using conventional manufacturing methods.
With AM, users can design, print, test and analyze the performance of a part in a few weeks or less, and then do it all again with a different geometry until the ideal part is achieved. This faster design and iteration loop can help to better understand the air dissipation properties of a heat exchanger than expensive computational fluid dynamics (CFD) methods. Test results are also reliable and representative of real-world operations, which in turn can be used to improve the analysis.
This quicker turnaround time for the design of the part can also be translated into a quicker production time. Once all the relevant design files and parameter sets have been digitized, they can be used on a metal 3D printer anywhere.
Another key benefit of metal AM is reduced manufacturing and supply times. Producing heat exchangers additively offers manufacturers the option of setting up an in-house supply chain to print parts on demand when they are needed. This is not possible with other conventional approaches, and while it may not be suitable for all industries. For low- to mid-volume requirements, in the aerospace sector, for example, AM can offer a transformational way of bringing the supply chain and production directly to companies.
The challenges of making AM heat exchangers:
The need for better education
When GE additively manufactures heat exchangers, there are various factors our engineers need to consider when creating their design. It is all well and good being able to create a part out of a desired material, but it is often the post-processing stages that are the most important. This is where final material properties are set and where testing, inspection and validation protocols become necessary to ensure that the part is functioning as intended.
We need to challenge an ethos that once the part is printed, it is ready to go. While heat exchangers can be manufactured using additive, we need to continue educating users to ensure that all parts in their operating environment are going to be robust and fit for use—from both a material and functional standpoint.
How best to implement AM into customers’ manufacturing strategies is not unique to heat exchangers, but there is still a need within the heat exchanger community to ensure that parts are being created to the highest possible standard.
Design time and working with large CAD files
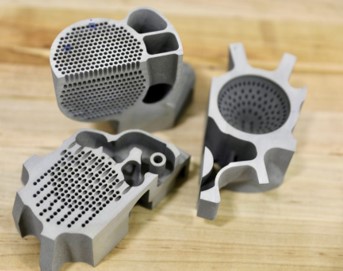
Another challenge GE encountered when designing heat exchangers were the very large CAD file sizes of the designs. This is typically a limitation that has been specific to heat exchangers because of the large number of surfaces—and in turn a large surface area—that are present within the internal makeup of a heat exchanger.
The implications of a large fi le don’t just stop at the design phase. While large CAD files can slow down the design and 3D modeling process—and even crash the computers rendering the design—the delays can permeate into the slicing and preparation stages of the additive process, as well as the inspection phase, because additive users are having to work with large and cumbersome CAD files.
Our engineers and modelers have managed to find optimal ways of keeping the file sizes low, as well as figuring out the best way to transport these files and adopt control systems that ensure multiple users across the production chain can handle these files easily. However, for new additive users, large CAD files are not an obvious issue, but is something that they should be aware of when designing heat exchangers as it can drastically slow down design time.
Small channels and surface roughness
Small channels are not necessarily a limitation, but they can become one if the size of the passages is too small and the flow path too complex, as this can trap leftover powder from the printing stage in the channels. It can be extremely difficult to remove that powder later in the post-printing stages—increasing time and driving up costs. In addition, the trapped powder might prevent the heat exchanger from working properly and result in scrapped parts.
So, the part needs to be designed with these factors in mind, and while small channels may be of benefit to the application, it is important to ensure that they are still large enough to be functional—as there are methods developed to remove loose powder if the channels are designed with those methods in mind.
Surface roughness of the internal channels also needs to be considered, as it is difficult to post-process such small channels. This often comes down to understanding the capabilities of each additive modality and resulting surface finish of the final part. Here it is important to choose a modality, orientation, parameter set, and design that best suits each application, because the surface roughness could affect fluid flow dynamics, which could result in unanticipated pressure losses across the heat exchanger.
Limited material selection
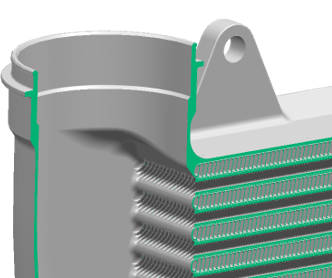
There is still a relatively limited, but expanding, library of metallic materials (pure and alloys) that can be used in additive manufacturing because of the work that needs to go into creating the production parameter sets and material databases for each type.
There are a lot of metals and metal alloys that could be used for a range of applications, but it does take focus, time, and investment to develop these materials processes and characterize behaviors at the bulk and feature level.
As it stands, heat exchangers can still be made from several materials—including aluminum, titanium, steel, or cobalt chromium. However, we expect the scope of materials to expand in the future as more alloys are matured for use with AM based on end-user requirements.
How these challenges are being tackled

Every new and existing manufacturing method has its own challenges and limitations. We are already seeing new ways of thinking and working, as well as emerging development protocols that are pushing the boundaries of what is possible.
It is important to consider the whole production system to get the most out of AM. Moreover, users should always try to consider the right materials and design choices for their specific applications and ensure that their designs can scale appropriately throughout all stages of production. Starting with the fundamental 3D-printing process, users need to start by optimizing both the orientation and the build parameters of the part. Doing this can have a positive impact on material properties, and it can also remove some of the limitations in the design. It is also key to consider the finish of the part and ensure that the surface finish is understood across the part and in line with application requirements. This can be achieved by using fluid and mechanical analysis while accounting for things like the build orientation of the part and measuring the surface finish across multiple surfaces in the part. Without this, the sizing and pressure drop prediction tools may not match your hardware test results, because the large number of surfaces will impart localized differences in surface fi nish and performance. Fluid and mechanical optimization helps us to understand how that surface roughness is going to impact the pressure loss or the fatigue capability of the part and if anything needs to be done to improve a certain feature within the heat exchanger.
A lot of the success of creating additively manufactured heat exchangers has stemmed from extensive testing and data collection protocols that provide insights into the heat exchanger performance for different applications.
3D CT scans have become a go-to option for looking at the internal features inside additively manufactured heat exchangers to see if there is any debris in the channels that can then be removed.
By incrementally improving all the processes, the data collected at each stage can be used to optimize all the different analyses and provide an ecosystem where decisions are made based on accurate information and engineering know-how. Having certifi ed systems at all stages also helps to produce high-quality products, because users know the capabilities of the AM equipment, the properties of the raw materials, and then just need to enhance the processes so that they can achieve uniformity in production.
Our teams have developed and implemented a quality management system to ensure control, and traceability of the raw material, the machine configuration, and the process control to ensure consistent and predictable production parts and has multiple high volume flight certified AM components in certified engines today and many more coming in new engine platforms that are allowing step changes in engine performance. One of the overarching concepts that we have learned through our own additive experience is that there is not a one-size-fits-all solution when it comes to designing and additively manufacturing heat exchangers. That is why we offer a range of geometrical options and methods to meet application design requirements. We have developed an extensive IP portfolio and expertise across critical AM heat exchanger designs, sizing tools, CAD tools and processing methods that are necessary for anyone wishing to enter the additive heat exchanger market. If a user is looking for a greater surface area, then trifurcating heat exchangers could be the solution. Does a user need more thermal compliance in an application? If so, then an application might best suit a tube-shell heat exchanger. Or if a higher-pressure solution is required, then the user might look to a matrix core heat exchanger. Understanding the ecosystem and how to lean on these different approaches to create a tailored solution is how we ensure we design and produce the right heat exchanger components for the system need.
Conclusion
The idea of using additive to create heat exchangers is not to take existing parts and try to simply recreate them faster; it is to find the best way of using materials, geometries, and the final part so that it performs at its highest level.
Yes, you can use AM to speed up production and bring production in house, but if reducing time is the only driving factor for using AM, then users are going to miss out on some of the key features and benefits of using the technology. It may not always be the most cost-efficient approach at a component level, but GE has shown significant advantages and winning business cases at a system level.
In those industries where heat exchangers need to perform at higher performance levels than they have in the past, AM offers the potential to print heat exchangers with more complex shapes, higher levels of customizability, improved durability, better thermal management properties, and lower weight while reducing the time and cost taken to get the product to market. However, whether you will benefit from additive or not is dependent on your application and the unique solutions that it can enable to provide benefi t to the customer.
About the Company
GE Additive is a leader in metal additive design and manufacturing, a pioneering process that has the power and potential to transform businesses. Through its integrated offering of additive experts, advanced machines, and quality powders, the company empowers its customers to build innovative new products. Products that solve manufacturing challenges, improve business outcomes, and help change the world for the better. www.ge.com/additive
Contact for enquiries: additive.enquiry@ge.com