^ Introducing automated processing methods to the facility, robots are used in the gluing process of the smaller plates.
2023 stands before us all as a looming question mark. But with uncertainty comes possibility. If the well-known proverb tells us “necessity is the mother of invention,” an unprecedented energy crisis, war in Europe, and urgency for meaningful environmental policies certainly classify as a time of necessity. Fortunately for our industry, the heat exchanger is a key piece of equipment for the most likely future energy scenarios.
By Ellie Pritchard, Heat Exchanger World
Tranter is a global manufacturer of gasketed and welded plate heat exchangers and a service provider, and the company’s extensive reach and experience tells them that, for the heat exchanger industry, the future is bright. I was able to speak with the Tranter team about the trends they see in emerging applications and the unique technology of the company’s manufacturing facility in Vänersborg (Sweden), which enables
them to offer solutions for these new industries.
For a well-rounded insight, I spoke with Thomas Cassirer (Director of EPC & Energy), Van Aznavour (Sales Manager – Benelux & Germany), Madeleine Sestan Bach (Global Marketing Manager), and Tomas Örtendahl (Plant Manager – Vänersborg).
Emerging markets
Van Aznavour has been working for Tranter for five years and is the regional sales manager for capital sales in Germany and the Benelux region, as well as country manager for Germany. Amongst his many other responsibilities, Van focuses on new trends and applications and has a keen understanding of what his regional customers are calling for.
“Geothermal is one very interesting and important application, not only in Germany, but all over the world,” says Van. “There is still much to do and although much progress has been made over the past ten years, there are still many new possibilities for using geothermal energy for heating.”
Thomas Cassirer holds a strategic global position observing current market trends and driving business in their direction. Thomas also works alongside EPC contractors to understand their needs and translate those into solutions. “Saving heat is a very important part of the energy situation right now. There are a lot of changes happening in the industrial sector in particular,” Thomas confirms. “For example, we are seeing an increase in LNG projects due to the Russia-Ukraine war. High demand, combined with increased urgency, means an increased demand for fast-tracked products.”
There has already been an increase in LNG projects with the majority appearing in Germany and the Netherlands. Although few and far between, the scale of the projects always results in huge opportunities where heat exchangers are concerned. One example of such a project was carried out with Nederlands Gasunie through a UK based EPC company.
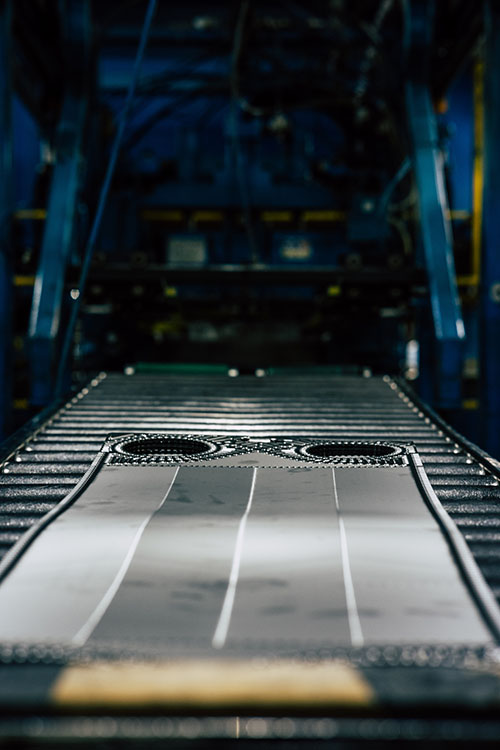
Tranter was contracted to provide a dockside heat source for an LNG regasification plant in Eemshaven, the Netherlands. It was the company’s EU-based production which ensured it could meet a tight 14-week deadline (from instruction to delivery), along with the coil stock and press capacity of the Vänersborg facility. The project contributes to the diversification of energy supply, an issue of global scale since the Russian invasion of Ukraine and the loss of Russian gas supply.
Both Thomas and Van, from their respective global and regional perspectives, see a shift in approach to heat recovery processes with heat now being seen for its valued energy potential. What used to be considered an idealist but expensive solution is now an obvious alternative to using expensive gas.
“Companies have much higher costs to calculate than before, so they can now see the sense in investing in more efficient heat recovery systems,” says Van.
Predicting the near future
Looking to the coming years, both Thomas and Van see the traditional market sectors remaining stable but enjoying a boost from increased demand for renewable energy applications, such as geothermal due to a rise in district heating networks, hydrogen, LNG, and carbon capture systems (CCUS).
“Total growth rate (industry demand) for plate and frame heat exchangers is currently more than 5%,” Thomas confirms. “Industry demand for hydrogen is set to grow by 20-25% and we expect a similar growth for carbon capture systems. We aim to become a trusted advisor in these sectors.” “Developments in green and blue hydrogen are especially important in Asia Pacific and Europe, as well as renewable energy applications to produce the hydrogen,” he adds. “These processes require multiple heat exchangers in their systems, so they are another good source business for us.”
“In general, we also see an increased demand in CCUS applications, as the global focus has also become more environmentally conscious,” says Van. “So, the key thing to understand is that the process industries have many different focuses at the moment: The environment, war, energy supply in general, and the cost of living. And carbon capture is one part of the solution to these global problems.”
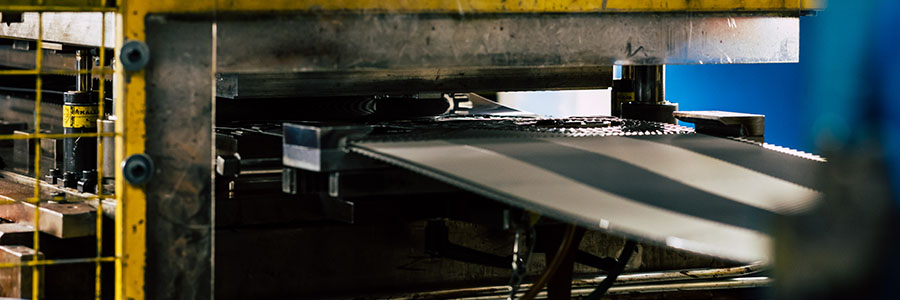
It is therefore clear that a holistic approach is needed – a variety of solutions are required to tackle a variety of challenges, and heat exchangers are necessary for many of these solutions. For many manufacturers, the challenge is ensuring that their product range is well-equipped to handle these new applications. This is where Tranter’s Vänersborg facility plays its part.
“To face these demands, you of course first need the right product,” Van explains. “For these applications, we normally need very high temperatures, very small logarithmic temp differences/very small temperature approaches, and high NTUs – that means that the temperature jump is very high and for this you need long plates/long thermal length. This is what Tranter does. Due to the high temperature deeper pressed plates can be advantageous, because those plates will be assembled with thicker gaskets which last longer.”
Beyond this, both Thomas and Van acknowledge the importance of continuing a communicative relationship with customers. “Smart services are another new focus for us, helping to build lasting partnerships with customers. Ideally, they give us their operating process data so that we can analyse and help them reduce their downtime, by suggesting preventive maintenance, and so on,” says Thomas. “Suppliers must take more responsibility for reducing the total cost of ownership.”
Vänersborg facility
The Vänersborg facility is a vital part of the Tranter production line. Its unique pressing machines facilitate longer, deeper pressed plates which are ideal for large-scale applications. The process is unique in that sheets are fed through continuously, pressed and then cut, meaning that Tranter can provide plates of impressive scale at a fast rate – medium sized plates in 30 seconds, and large plates in minutes. All scrap material is collected and recycled, and the facility produces its own geothermal energy for heating, only purchasing renewable energy.
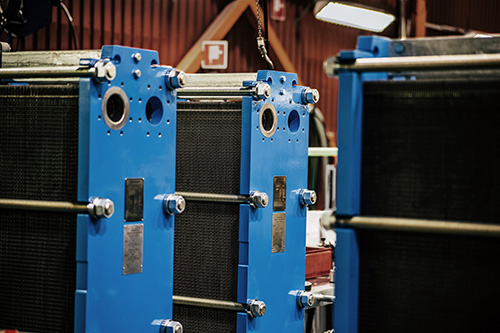
In addition to the deeper press, the plates also have application-specific formations such as hexagonal and chevron designs. The machines in the Vänersborg facility enable the easy switching of presses so that all designs can be produced in the longer lengths. Most plates are produced in stainless steel or, in cases of seawater cooling, titanium – for green hydrogen, nickel alloys or exotic materials are preferred.
The longest plates so far produced for a customer measured 3,5 metres in length, but the Vänersborg facility proudly displays a 6-metre-long plate in its workshop, a fun reminder to its team that anything is possible. “It is very unlikely that a customer will have a need for such large plates,” Plant Manager Tomas Örtendahl admits with a smile. “But, should the opportunity ever arise, we are the only facility capable of producing plates to this scale.”
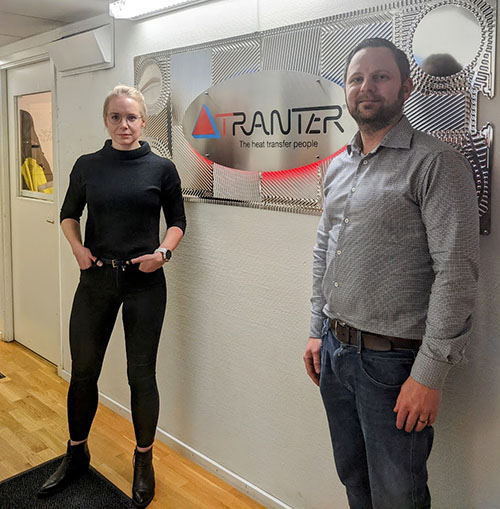
Another feature of the facility is its automated processing, transitioning to a highly skilled workforce supported by digitisation. For example, robots are used in the gluing process of the smaller plates, whilst the larger plates require human hands to apply the glue.
Madeleine explains that there is more focus on a lean but highly trained workforce. “Tranter sees a future in a workforce which is competent in a multitude of skills, and acknowledges that digitisation is part of the solution, but not the be-all-end-all answer to wider industry’s challenges,” says Madeleine. “For us, this begins with the implementation of a new ERP (enterprise resource planning) connected to a marketing automation system to be able to provide the ultimate customer experience.”
To future-proof the company’s problem-solving capabilities, a diversely trained workforce ensures that Tranter will be capable of answering the yet unknown issues in years to come.
“In general, we don’t see ourselves as simply a components supplier. We have so many customers now that need more than that due to these new emerging technologies,” Van states. “We need to work alongside them to learn more about how to tackle future challenges. They need alternatives, and to understand the reality of different options – In turn, we have to be informed and provide not only standard solutions, but intelligent ones.”
About this Featured Story
This Featured Story was first published in Heat Exchanger World Magazine in February 2023. To read more Featured Stories and many other articles, subscribe to our print magazine.
Featured Stories are regularly shared with our Heat Exchanger World community. Join us and share your own Featured Story on Heat Exchanger World online and in print.