Alkaline electrolyzers operate within a temperature range of 80–90°C, with a design temperature typically closer to 120°C. The widely used standard stainless steel 304L can provide satisfactory service life in caustic environments such as the pulp and paper industry. However, in the case of alkaline electrolyzers, it is necessary to eliminate or minimize corrosion to keep the systems clean and ensure a long service life with minimal maintenance and part replacement.
In strongly caustic solutions, chromium is the key element in stainless steel to resist corrosion. Duplex grades are generally higher alloyed in chromium than austenitic grades and have proven to perform very well in caustic service at high temperatures. This makes them suitable materials for alkaline electrolyzers, especially in heat exchangers and piping that are not exposed to high-pressure hydrogen gas.
By Jonas Höwing and Angela Philipp, Technical Marketing – EMEA, Alleima
In the industrial transition towards more sustainable and less carbon dioxide-intensive operations, the use of clean hydrogen is seen as a means to reduce the reliance on fossil fuels and enable energy storage. Water electrolysis is the most viable method for large-scale hydrogen production, excluding fossil-based technologies such as steam methane reforming (SMR). When hydrogen is produced using electricity from renewable sources, it is classified as ‘green hydrogen’. Certain industrial processes, such as steel production, ammonia-based fertilizers, chemicals, and renewable fuels, are specifically targeted for utilizing green hydrogen due to their potential for significant environmental benefits.
There are three major technologies for water electrolysis: polymer electrolyte membrane (PEM) electrolysis, alkaline electrolysis, and high-temperature solid oxide electrolysis cell (SOEC). Of these, alkaline electrolysis is the oldest and most mature technology, which has been commercially used for over a century. The different techniques have their advantages and disadvantages, with PEM being compact and efficient but expensive, alkaline electrolysis being low-cost and robust but bulky and less efficient, and SOEC being highly efficient but operating at high temperatures and suffering from material degradation and slow startup and shutdown.
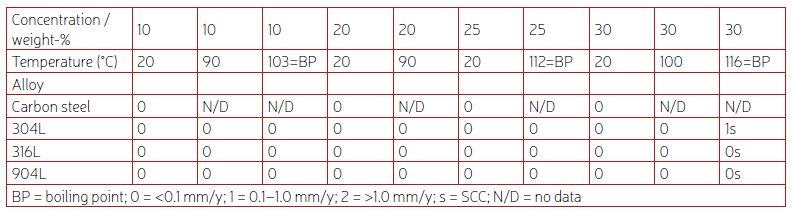
Alkaline electrolyzers
This article focuses on alkaline electrolyzer technology, which today is the most used or considered technology for large-scale hydrogen plants. In alkaline electrolyzers, as suggested by the name, the electrolyte is a caustic solution, commonly 30% potassium hydroxide (KOH). The water in the electrolyte is split into oxygen and hydrogen through the reactions summarized below:
Cathode reaction: 2 H₂O(l) + 2e- → H₂(g) + 2 OH¯(aq)
Anode reaction: 2 OH¯(aq) → ½O₂(g) + H₂O(l) + 2e¯
Overall reaction: H₂O (l) → H₂(g) + ½O₂(g)
The electrolyzer is commonly operated at 80–90°C and has a working pressure of 30 bar at the electrodes, although the pressure is lower in other parts of the system. As water is consumed in the process, it must be continuously replenished.
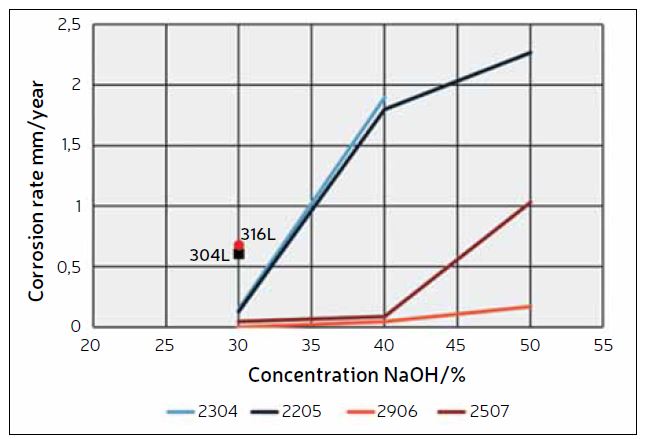
Furthermore, the added water must be of high purity as any impurities added through the water will accumulate in the electrolyzer system. Over time, this can cause scaling in piping systems and on electrodes and can also poison the catalysts on the electrodes.
The alkaline electrolyzer generally consists of the cell stack, where the electrolysis occurs, gas separators, tanks for electrolyte and water replenishment (as water is consumed in the process), and piping for electrolyte and gases. There are also heat exchangers for cooling and balance of plant, where the cooling media will largely depend on the electrolyzer plant’s location. If the plant is located inland or far from an open water source, a closed-loop system with cooling towers will most likely be used. Seawater or freshwater will most likely be used for the cooling system in coastal areas or close to open water sources.
This will put different demands on the metallurgy used for the heat exchangers in the cooling system. The material of construction (MOC) for alkaline electrolyzers has generally been standard austenitic stainless steel such as 304L or 316L, which in many cases provides a suitable service life. However, any corrosion in the electrolyzer system can result in the accumulation of corrosion products that can block small-diameter tubes, lead to scaling, and the presence of metal ions in the electrolyte, which can be detrimental to the electrodes.
Corrosion resistance of stainless steel in strong caustic solutions
Below is a non-exhaustive summary of the corrosion resistance of some austenitic and duplex stainless steels used in caustic industrial applications. Due to the strong oxidation properties of oxygen, the high flammability of hydrogen, and the diffusivity of hydrogen through polymers, plastic and fiberglass parts are generally unsuitable as MOC for hydrogen electrolyzer systems.
Austenitic stainless steel in caustic processes
In caustic water solutions, such as sodium hydroxide (NaOH), chromium plays a crucial role in maintaining the passivity of stainless steels.1 Nitrogen is another beneficial alloying element for corrosion resistance, while a high nickel content can help reduce the corrosion rate in cases of active corrosion.1 The pulp and paper industry handles a lot of caustic solutions, and welded 304L, with approximately 18% chromium and 10% nickel, offers a good service life for piping. In such piping applications, the caustic concentration is seldom higher than 30% NaOH, and the temperature is usually below 80°C. However, as shown in Table 1, when exposed to higher temperatures, 304L can start to corrode, and there is also a risk of stress corrosion cracking (SCC) at atmospheric boiling points.2 Since 316L is usually slightly lower in chromium content than 304L, and also suffers from SCC at similar temperatures, 316L does not offer any advantages compared to 304L. Additionally, the higher-alloyed austenitic stainless steel grade 904L is susceptible to SCC when exposed to boiling 30% NaOH solution. The typical chemical compositions of 304L, 316L, and 904L stainless steel are listed in Table 2.

Duplex stainless steel in caustic processes
For more demanding or critical applications, it is common to use a duplex grade such as duplex stainless steel (DSS) 2304 or 2205 instead of austenitic grades. The duplex grades have higher chromium and nitrogen content compared to 304L, 316L, or 904L, resulting in an inherently higher corrosion resistance in caustic media. They can provide a good service life in both more concentrated solutions and at higher operating temperatures. Duplex grades are also lower in nickel content than austenitic ones, making them more cost-efficient. Finally, duplex stainless steels have higher mechanical strength and better thermal conductivity than standard austenitic grades. They can be utilized to achieve more efficient heat exchangers or reduce the weight of an installation. The typical chemical compositions of some duplex grades are shown in Table 3.
Figure 1 shows a graph depicting the measured corrosion rates of various stainless-steel grades in boiling NaOH solutions as a function of NaOH concentration.3 The duplex grades exhibit superior corrosion resistance compared to the standard austenitic grades. It is also evident that DSS 2304 and DSS 2205 demonstrate very similar levels of corrosion resistance, DSS 2507 is better, while DSS 2906 exhibits the best corrosion resistance of the tested grades. This further supports the notion that chromium is the most important alloying element for materials used in caustic solutions.
Converting NaOH data to KOH
Since NaOH is a very common chemical in the process industry, almost all published corrosion data for high-concentration caustic media is from tests conducted in NaOH aqueous solutions. By contrast, the caustic solution commonly used in alkaline electrolyzers is KOH, for which published data is very scarce. Moreover, most published data for NaOH solutions is expressed with a concentration in weight-%. However, due to the difference in weight between Na+ and K+, 22.99 g/mole and 39.10 g/mole, respectively, mass percentages of NaOH and KOH are not equivalent.
However, in a caustic solution containing NaOH or KOH, the Na+ and K+ ions are inactive in the corrosion process. Therefore, the corrosivity of a caustic solution at a certain temperature is a function of the molar concentration of hydroxide ions (OH-). Thus, by calculating the molar concentration of a NaOH solution, the available corrosion data for that concentration of NaOH can be recalculated for the corresponding concentration of KOH. This is illustrated in Figure 2. It can be observed that a KOH solution with a certain weight-% concentration will always have a lower molar concentration of OH- and therefore be less corrosive than a NaOH solution with the same weight-% concentration. For example, as shown in Figure 2, 30% KOH corresponds to 23% NaOH. Therefore, applying data for 30% NaOH when selecting MOC for a system using 30% KOH would yield a conservative result.
Material selection criteria for alkaline electrolyzers
Different materials of construction can be used depending on the operating and design criteria of the alkaline electrolyzer. As mentioned earlier, non-metallic materials are generally unsuitable for alkaline electrolyzers due to flammability and hydrogen permeability, and metallic materials are used.
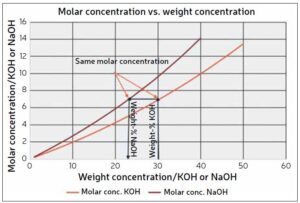
shows that 30 weight-% KOH corresponds to ~23 weight-% NaOH.
Table 4 shows some typical operation and design values for an alkaline electrolyzer. It should be noted that the caustic brine after the electrolyzer will have a higher concentration of KOH as water has been consumed. Therefore, these parts may show higher corrosion rates than other parts.
Standard MOC
As already mentioned, many alkaline electrolyzers are constructed using 304L or 316L austenitic stainless steel. These austenitic grades can withstand certain upset process conditions and temperatures with little corrosion damage and a limited risk of material failure. The MOC will often provide a suitable service life for the application, although part replacement is to be expected. DSS 2304 or 2205 can be used with a limited increase in material cost to achieve reduced corrosion and longer service life.
Advanced MOC
In some cases, there is a requirement for the electrolyzer to operate without any part replacements for up to 30 years. This also means the MOC should withstand upset operating conditions without corrosion or cracking. It is important to keep in mind that even a low corrosion rate of 0.05 mm/year will result in a significant material loss of 1.5 mm over a period of 30 years. Therefore, an adequate corrosion allowance must be applied to the installed components, or a MOC must be chosen to minimize any corrosion. Furthermore, from a fouling perspective, extremely low corrosion rates will be essential to keep the electrolyzer clean throughout its 30-year service life.
For these applications, the MOC must be immune to corrosion at the design criteria specified in Table 4. By consulting the information in Table 1 and Figure 1, along with the conversion diagram in Figure 2, it becomes clear that DSS 2304 and DSS 2205 do not provide sufficient corrosion resistance. On the other hand, DSS 2906 shows zero corrosion in boiling 30% NaOH (approximately 39% KOH), making it a suitable choice as an MOC in these extreme cases, even during upset conditions. DSS 2507 could also be used, but this grade may not offer complete corrosion resistance during operational upsets.

Additional considerations for parts after electrolyzer stack and gas separation
After the electrolyzer stack, parts of the alkaline electrolyzer system will be exposed to highly pressurized hydrogen and oxygen. Hydrogen has been shown to cause loss of ductility and embrittlement of austenitic stainless steels with low nickel content, as these grades are prone to forming deformation martensite upon cold working.4 Also, due to containing ~50% ferrite, duplex grades will likely lose mechanical properties when exposed to hydrogen gas under high pressure.5 Therefore, higher-alloyed austenitic grades should be considered for these specific parts of the electrolyzer plant.
It has been established that highly oxidizing environments can increase the susceptibility of stainless steel to SCC.6 Consequently, the highly oxidizing power of oxygen gas may increase the susceptibility of stainless steel to caustic SCC. However, this has not been thoroughly investigated, so further experiments are required to verify if this can inhibit the use of certain stainless steel grades in these parts of an electrolyzer.
Cooling system
The complete alkaline electrolyzer plant also includes auxiliary cooling systems, which can be either of a direct type or an indirect type. In the direct type, the caustic electrolyte is cooled directly using cooling water in a heat exchanger, while in the indirect type, a closed loop
system is used, using, for example, a glycol solution. Due to the cooling effect on the heat exchanger tubes for direct cooling systems, the corrosion rate will be lower than experienced in the electrolyzer. Depending on the cooling media employed, DSS 2205 can be a suitable material for sweet water systems if some corrosion on the caustic side is acceptable. If no corrosion is tolerable on the caustic side, DSS 2507 or 2906 should also be considered for sweet water cooling. For direct cooling systems using seawater, DSS 2507 is recommended due to its superior corrosion resistance in seawater compared to DSS 2906.
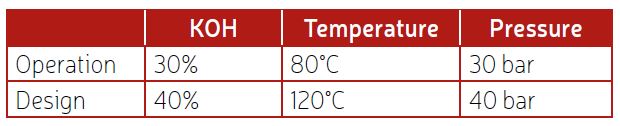
Conclusion
Alkaline electrolysis of water to produce hydrogen is the most mature and cheapest technology available. The MOCs commonly used for alkaline electrolyzers are often standard austenitic grades such as 304L or 316L, which are relatively cheap while still providing a good service life. However, in certain cases, it is desirable to have a very long service life of the equipment, up to 30 years, with minimal or no maintenance or part replacement throughout that time. This places a very high demand on the corrosion resistance of the MOCs used, and the standard austenitic grades may not be suitable for such requirements.
It has been shown in this article that duplex grades have superior corrosion resistance in caustic environments compared to 304L and 316L. Specifically, duplex grade 2906 has been shown to have suitable corrosion resistance in caustic environments to achieve more than 30 years of service life without significant material loss, even under upset conditions involving higher caustic concentrations and temperatures. DSS 2507 is a suitable material choice for heat exchangers using brackish water or seawater for direct cooling. This is because the corrosivity of the caustic stream will be lower in a cooling service, and DSS 2507 has better corrosion resistance in chloride-bearing cooling waters compared to DSS 2906.
However, duplex grades are not suitable for service in contact with high-pressure hydrogen gas. For these parts of the electrolyzer, high-alloyed austenitic grades should be used. There remains a question regarding the potential increased susceptibility of stainless steel grades to caustic stress corrosion cracking (SCC) in the presence of high-pressure oxygen. Further investigation is needed to explore this topic in greater detail.
References
- Leander, D., & Philipp, A. (2019). tappi pEErS: Conference proceedings 19pEErS.
- Alleima Technical Center, Corrosion tables, Sodium Hydroxide.
- Leander, D., & Juhlin, A. (2004). AB Sandvik Materials Technology. R&D report 040134tE.
- International Journal of Hydrogen Energy 35.18 (2010): 9736–9745.
- San Marci, C., & Somerday, B. P. (2012). Sandia report SAnd2012-7321.
- Francis, R. “Duplex Stainless Steels and Chloride SCC – How resistant are they?” paper presented at the duplex World Seminar & Summit 2022, Rotterdam, the Netherlands.
About this Featured Story
This Featured Story was first published in Heat Exchanger World Magazine in September 2023. To read more Featured Stories and many other articles, subscribe to our print magazine.
Featured Stories are regularly shared with our Heat Exchanger World community. Join us and share your own Featured Story on Heat Exchanger World online and in print.