Image © Alfa Laval
Innovative technologies that optimize energy efficiency will play a critical role in reducing the energy demand of numerous applications, thereby lowering the overall projected demand and meeting the Paris climate goals. One forward-looking example is the use of industrial waste heat generated during the production of green hydrogen and fed directly back into the manufacturing process.
By Sven Schreiber – Managing Director, Alfa Laval Mid Europe
The world is currently facing a double challenge. On the one hand, global energy demand is constantly rising due to economic growth, and, according to the projections of the International Energy Agency (IEA), it will be 54% higher than today as early as 2050.¹ On the other hand, society must drastically reduce carbon consumption and emissions to avoid severe environmental consequences in line with the Paris Climate Agreement.
There is no ‘one’ simple solution to reducing carbon emissions. Instead, it requires the implementation of numerous new technologies and fuels across all sectors of the economy. A major contribution will come from energy efficiency, which means realizing as much output as possible with minimal input. Energy efficiency, combined with access to renewable energy sources such as solar and wind, and a transition from fossil fuels to new energy sources such as biofuels and green hydrogen, is essential to a successful transition toward sustainability. In those industries that cannot do without fossil fuels, carbon capture technology must be used. So currently, we are indeed on the brink of an energy revolution in both industry and society, moving away from fossil fuels and embracing new environmentally friendly technologies.
Driving innovative technologies forward
Most of the technologies needed to halve emissions by 2030 are already available today. However, achieving the goal of net-zero emissions by 2050, as enshrined in the European Climate Change Act, will be more challenging. According to the IEA, half of the emissions reductions will rely on technologies that are still in the prototype or demonstration phase. Green hydrogen, carbon capture, long-term energy storage – all will require large investments to become reality. To accelerate decarbonization, a two-pronged strategy is needed. Firstly, more investment must go into deploying the technologies that are already available and commercialized to make industry more sustainable. Simultaneously, efforts must be made to drive the development of new technologies for a long-term energy transition and the establishment of an efficient circular economy. Sustainable partnerships play a crucial role in achieving these goals. Collaboration across countries, industries, and sectors is essential for making a meaningful impact. It is about rethinking and developing new business models to achieve climate goals while maintaining company visibility.
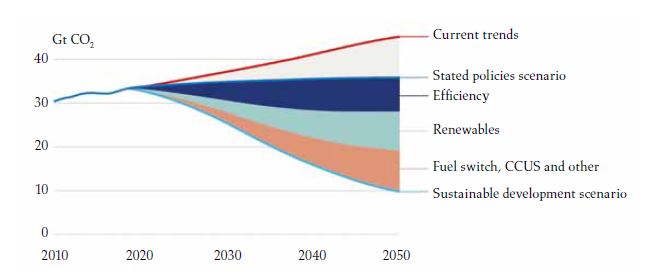
Energy efficiency as a key factor
The issue of energy efficiency is crucial in achieving the targets set by the Paris Climate Agreement. According to IEA forecasts, 40% of emissions reductions could be achieved through energy efficiency by 2040. There is enormous potential. The technology is there, we just need to use it. Energy efficiency should be at the top of the agenda in every context. After all, there is nothing more sustainable than energy that is not consumed in the first place.
One example of collaboration to accelerate the development as well as the implementation of energy-efficient technologies is the Energy Efficiency Movement, launched as an open platform by Swiss technology company ABB and now gaining momentum. Alfa Laval is the first member to join the movement. Together, the participants want to draw attention to the topic of energy efficiency and promote its implementation.
Energy efficiency is not only important for existing industries and applications but also for the development of new climate-friendly technologies ranging from green hydrogen and power-to-X to energy storage, carbon capture, and biofuels. Efficient solutions are urgently needed everywhere to increase the scalability of these technologies and thus accelerate the transition to a carbon-free future.
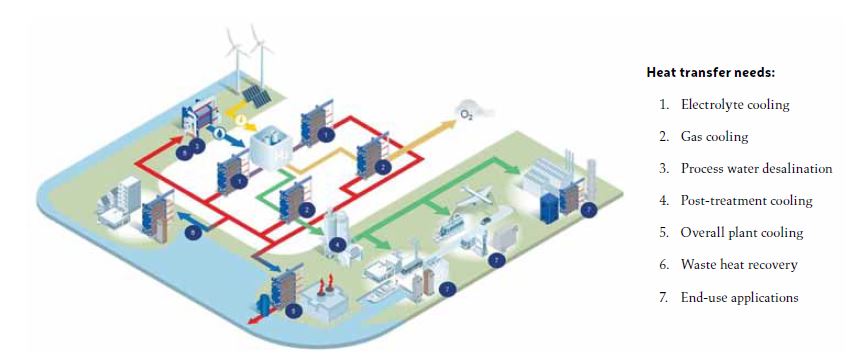
Green hydrogen as a clean energy carrier
One energy carrier with particularly great potential in the future energy landscape is hydrogen. In the net-zero scenario, for example, 22% of the world’s energy needs could be met by clean hydrogen by 2050.² This includes both green hydrogen produced through electrolysis and blue hydrogen. In the latter, carbon capture is added to conventional production based on natural gas or coal. Overall, the hydrogen economy will grow significantly in the long run.
However, to make this a reality, we still face several challenges related to technology deployment, scalability, and commercialization. These challenges span the entire hydrogen value chain, from the production of green hydrogen to its final application as a molecule or energy carrier. Hydrogen can be used in many ways, including as a feedstock for industrial processes such as ammonia, methanol, and steel production, as a power source in fuel cells, and as a fuel in the transportation sector. While there are numerous possibilities, investments are needed to make the coming hydrogen economy a reality. The future is likely to witness a mix of centralized and decentralized solutions, both on a small and large scale. To achieve the full hydrogen economy needed for the net-zero emissions scenario by 2050, green hydrogen production must be scaled up, appropriate infrastructure built, and reliable balancing ensured.
It is important to consider scaling at the development stage. This means investing in solutions that are also cost effective in the long term. When it comes to heating and cooling, optimal heat transfer is necessary in almost every industrial process – including the hydrogen value chain.
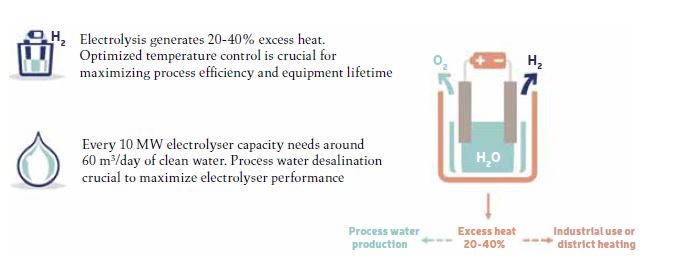
Recovery of excess heat
One example is the production of green hydrogen. Currently, the most mature electrolysis technologies are PEM electrolyzers and alkaline electrolyzers, which are expected to remain dominant in the market for the next few years. They operate at temperatures approximately between 50 and 80°C. Regardless of the specific technology used, temperature control is paramount to ensure both maximum productivity and efficiency of the electrolyzer, as well as maximum equipment lifespan.
During the electrolysis process, approximately 20–40% of the electrolyzer’s capacity is converted to excess heat. Despite the relatively low operating temperature, this heat should not be wasted. The use of heat recovery technologies allows this energy to be absorbed and used elsewhere. As a rule, recovered waste heat should be integrated back into the process in a suitable way.
Alternatively, if the infrastructure allows, the heat can be sold and used on neighboring sites, for industrial processes or in the district heating network. It is also possible to use it for heat conversion processes such as the production of chilled, distilled, or hot water, as well as electricity.
However, options are limited with the low-temperature heat generated during green hydrogen production. Current projections indicate a potential electrolysis capacity of 90 GW by 2030,² which would generate 18–36 GW of waste heat. As more countries adopt hydrogen economy strategies and technologies continue to evolve, capacity is expected to further increase. To stay on track for the net-zero emissions target by 2050, we would need a capacity of 200-250 GW by 2030.² In order for green hydrogen production to be energy efficient and cost competitive in the long term, it is important to consider waste heat as a valuable resource.
Direct waste heat utilization in hydrogen production
A simpler solution for utilizing waste heat is to integrate it directly into the green hydrogen production process. For every 10 MW of electrolysis capacity, approximately 50–60 m³ of clean water is required, highlighting the importance of efficient water recovery. With a projected capacity of 90 GW by 2030, this translates to a global demand of up to 540,000 m³ of water per day, roughly equivalent to the daily water consumption of the city of Los Angeles.
The treatment of the supplied water depends on its quality, which varies depending on the water source. In most cases, however, purification is necessary. The most common process for purifying water for electrolysis is reverse osmosis using chemicals. An alternative solution is vacuum evaporation, which uses the waste heat from the electrolyzer to demineralize the water and achieve the required quality for electrolysis. This process allows for direct reintegration of waste heat into hydrogen production.
With Alfa Laval HyDuo, two processes can be done at the same time: electrolyzer cooling, ensuring the right temperature of the hydrogen production process, and water purification, producing the right water quality for electrolysis. Utilizing waste heat as an energy source in the water purification process comes with many advantages, including lower dosage of chemicals, smaller footprint, greater reliability, and lower electricity consumption. Moreover, it improves process efficiency by up to 27%.
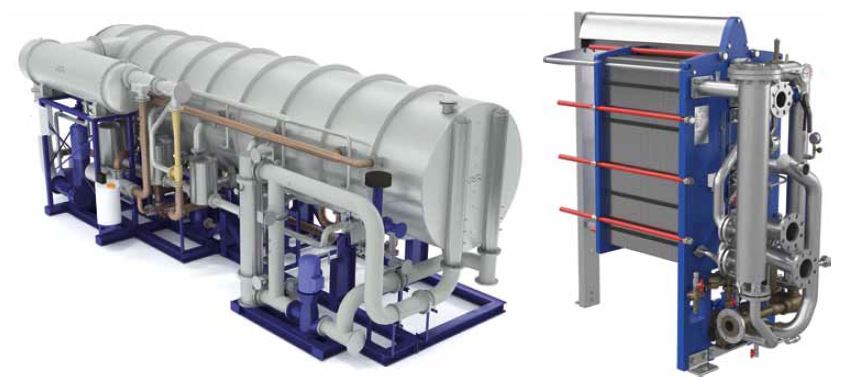
Image © Alfa Laval
Using excess heat to produce pure water
First, feed water enters the evaporation section of the plate pack, where the plates are warmed by the hot water that comes from the electrolyzer. This causes the water to evaporate at around 30–65°C in a vacuum of 75–99%, which is maintained by the brine/air ejector. (The exact temperature and vacuum ranges depend on the model of the freshwater generator and the temperature of the electrolyzer’s hot water). This means that only clean freshwater vapor reaches the condenser section of the plate pack, which is cooled by a flow of seawater. Here the vapor is condensed into fresh water, which is pumped out of the freshwater generator. The vapor produced during the evaporation stage rises into the separator section, where any droplets of entrained seawater are removed. Gravity causes these droplets to fall back into the brine sump at the bottom of the freshwater generator.
Thermal desalination processes have long been used on offshore oil and gas platforms to produce fresh water from seawater. This method can therefore be directly applied to hydrogen production and is particularly advantageous offshore and in areas where fresh water is scarce. With this technology, the required water quality can be achieved in most cases without additional post-treatment.
In contrast, traditional desalination systems typically rely on membrane-based solutions where various chemicals are essential for ensuring smooth operation (e.g., biocides, activated carbon, anti-scaling). This is due to the sensitivity of membranes to variations in water impurities. However, when using a thermal solution, the need for chemicals is dramatically reduced, with their use limited to anti-scaling purposes. In some cases, the anti-scaling chemicals can even be avoided if operations run using lower hot-water temperature.
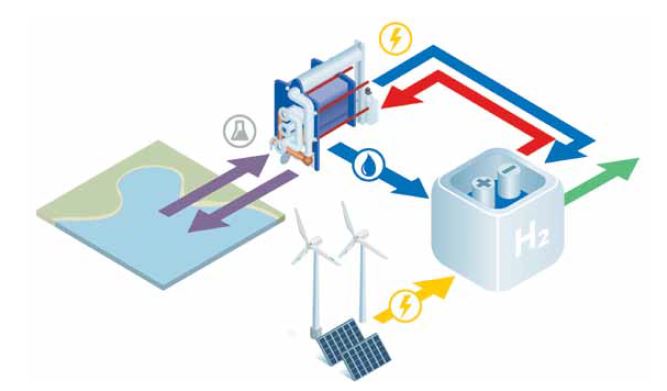
Establishing economical and scalable solutions
Until now, the industry has primarily focused on dissipating the heat generated during hydrogen production, for example through methods like sea cooling or ventilation. However, to increase the overall efficiency of the process, the waste heat must be recovered and used. The most obvious use is in other internal processes or in district heating. Sector coupling can also be considered. As shown, there is also the possibility of integrating the waste heat directly back into the process itself through the recovery of clean water.
The key now is to establish the required technologies in the market and scale them up for larger capacities. Innovative heat transfer technologies are critical to making hydrogen processes energy efficient and competitive – across the entire green hydrogen value chain.
Collaborative projects and partnerships aimed at finding new solutions and business models will be key drivers in enabling high-performance hydrogen solutions for a decarbonized future.
About the author
Sven Schreiber has been the Managing Director of Alfa Laval Mid Europe GmbH, the Alfa Laval subsidiary responsible for Germany, Austria and Switzerland, since 2019. The company is a global leader in key technologies for heat transfer, separation, and fluid handling. since January 2023, he has also served as a board member of the Power-to-X for applications working group at the german Engineering Federation (vdma), with the aim of accelerating the transformation process to achieve climate protection targets.
References
1. iEa. 2019. World Energy Outlook.
2. Hydrogen council & mcKinsey & company. (november 2021). Hydrogen for Net-Zero. A critical cost-competitive energy vector.
About this Featured Story
This Featured Story was first published in Heat Exchanger World Magazine in October 2023. To read more Featured Stories and many other articles, subscribe to our print magazine.
Featured Stories are regularly shared with our Heat Exchanger World community. Join us and share your own Featured Story on Heat Exchanger World online and in print.