The following article explores the application of KLAREN self-cleaning fluidized bed heat exchangers as an ideal solution for indirect heating of laterite nickel slurry in High-Pressure-Acid-Leach (HPAL) plants.
Text & images by Taprogge GmbH
Self-cleaning fluidized bed heat exchangers are able to solve severe fouling problem in indirect heat transfer due to the circulation of cleaning particles through the tubes of vertical shell and tube exchangers. Moreover, self-cleaning fluidized bed heat exchangers perform with constant heat transfer at low liquid velocities, which makes new designs of shell and tube configurations possible. Furthermore, self-cleaning fluidized bed heat exchangers show a strong shear thinning effect in non-Newtonian liquids. All the above characteristics make the self-cleaning fluidized bed heat exchanger an ideal tool for the indirect heating of laterite nickel slurry in High-Pressure-Acid-Leach (HPAL) plants.
Background HPAL
Nickel and cobalt are often found together in ores. Among other processing methods, the High-Pressure-Acid-Leach (HPAL) process is a hydrometallurgical technique for the extraction of valuable metals, particularly nickel and cobalt, from laterite ores. Laterite ores are a type of ore that is rich in iron and low in sulphur, but also contains significant amounts of nickel and cobalt. The HPAL process addresses the challenges posed by low nickel content and high impurity levels in these ores and has as a major benefit the ability to quickly leach nickel and cobalt from laterite ores. The HPAL process involves subjecting laterite ores to high-pressure acidic leaching, wherein sulfuric acid reacts with the ore under elevated temperature (roughly 255°C) and pressure conditions (roughly 50 bar or 725 psi).
The HPAL process works as follows: ore is mined and crushed to create a fine material. This fine material is mixed with water to create a slurry which is then preheated. The hot slurry is heated from approximately 65°C to a temperature of 230°C and pumped into an autoclave where acid is added. The slurry and acid then react as they flow through several compartments within the autoclave (temperature increases to 260°C). Upon leaving the high pressure and temperature atmosphere of the autoclave the slurry must be returned to atmospheric conditions. This is accomplished through two or more flash stages. Once the slurry is at atmospheric conditions it is washed and separated at which point the nickel and cobalt can be recovered from the liquid fraction. In most plants direct heating by steam or vapor injection, is used to heat the slurry.
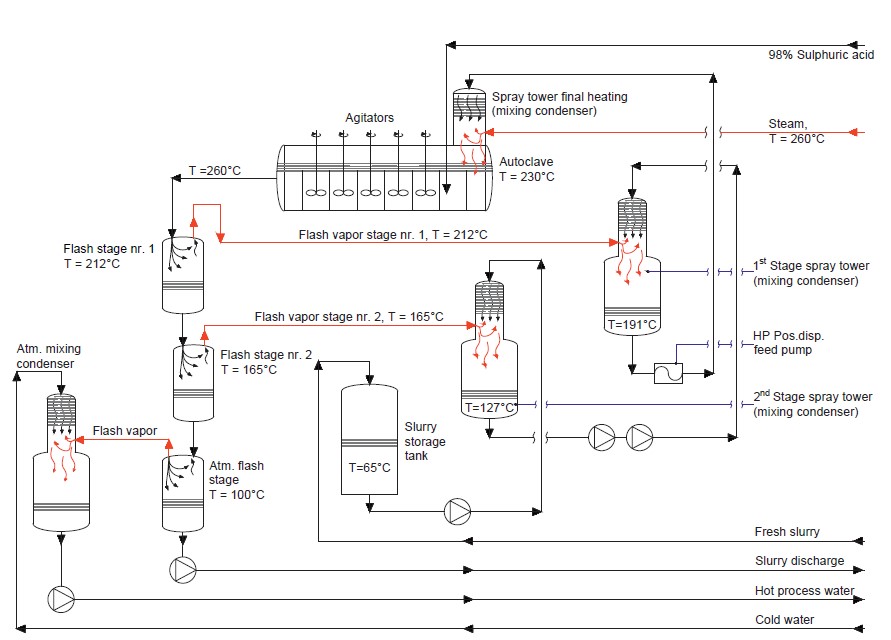
Figure 1 shows a flow diagram of a HPAL plant heating cold incoming slurry and recovering heat from the hot discharged slurry, while applying direct contact heat transfer by mixing the cold slurry with the flash vapor produced from the hot slurry in spray-towers/mixing condenser and using high pressure steam in a spray-tower/mixing condenser as the final heating step. The disadvantages of using direct heat transfer by employing direct steam injection is that the fresh slurry feed is diluted with the condensates in the various mixing condensers, which will result in larger equipment and more acid required for the HPAL process.
Benefits of indirect heating
There has always been a drive to apply indirect heating in HPAL plants because of the benefits of indirect heating in comparison with direct heating:
• Increase autoclave production capacity;
• Reduced acid consumption;
• Reduced neutralising agent consumption;
• Recovery of demineralised condensate and process condensate.
Challenges of indirect heating
However, while indirect heating methods can be effective in some situations, they come with certain issues and challenges in the context of HPAL:
• Heat Transfer Inefficiency:
Indirect heating methods often result in lower heat transfer
efficiency compared to direct steam injection. The heat must pass through heat exchangers, leading to potential losses and slower heat transfer rates. This inefficiency can impact the overall performance of the leaching process.
• Temperature Control Challenges:
Achieving precise temperature control is more challenging with indirect heating. The heat transfer rate is influenced by factors such as the design of the heat exchangers, the flow rate of the heating medium, and the nature of the slurry. This can lead to difficulties in maintaining the optimal temperature for the leaching reaction.
• Equipment Complexity and Maintenance:
Indirect heating systems can introduce additional complexity to the overall process design, including the incorporation of heat exchangers, pumps, and associated control systems. This complexity may result in higher maintenance requirements and increased risk of equipment fouling or scaling.
• Potential for Corrosion and Fouling:
The use of indirect heating methods may involve the circulation of corrosive slurries through heat exchangers, which can lead to corrosion over time. Additionally, the slurry may contain impurities that could contribute to fouling or scaling on heat transfer surfaces, reducing efficiency.
Application of KLAREN Technology in HPAL
With the KLAREN self-cleaning heat exchanger technology, most of these issues and challenges can be overcome. In addition to the mitigation of fouling effects, several other significant benefits for slurry heating are afforded by the mode of operation of the self-cleaning fluidized bed heat exchangers. Increased turbulence at the slurry/tube interface is imparted by the action of the fluidized particles, resulting in very high heat transfers at relatively low liquid velocities. Furthermore, given the thixotropic nature of most process slurries, the action of the fluidized particles imparts additional shear to the process slurry, resulting in shear thinning effects with a consequent reduction in pressure drop and enhancement of heat transfer across the heat exchanger. The benefits provided by the self-cleaning fluidized bed heat exchanger make it a good option for the indirect heating of laterite nickel slurry for High-Pressure-Acid-Leach (HPAL) plants.
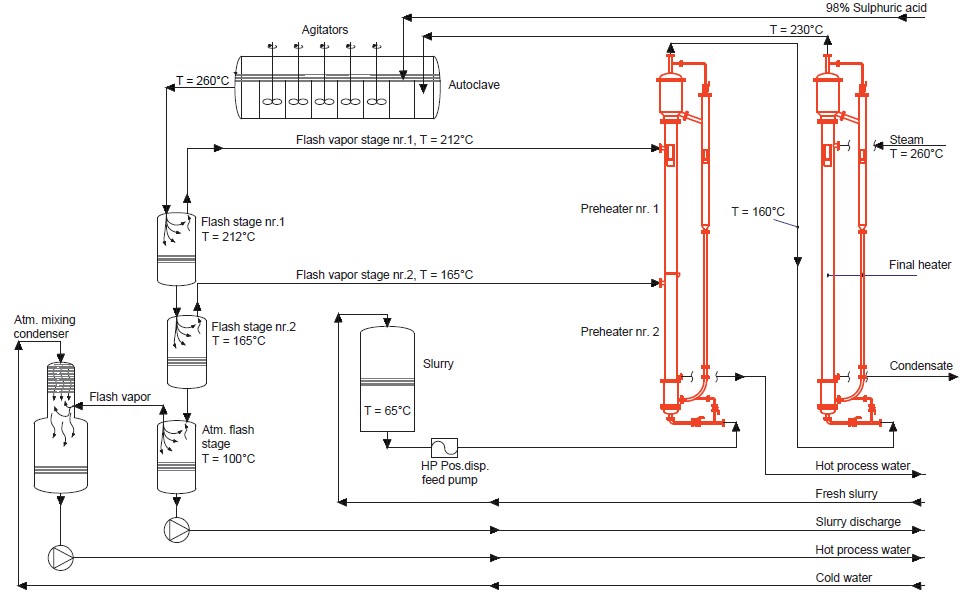
Figure 2 shows a typical flow diagram for a HPAL plant utilizing KLAREN self-cleaning heat exchangers. This figure shows only two heat exchanger shells in series. One shell contains both preheaters, while a second shell contains the final heater. The advantages of using indirect heat transfer by employing heat exchangers is that the fresh slurry feed is not diluted with the condensates in the various mixing condensers. This then results in a higher utilization of high-pressure autoclaves allowing an increased nickel and cobalt throughput per cubic metre of autoclave volume.
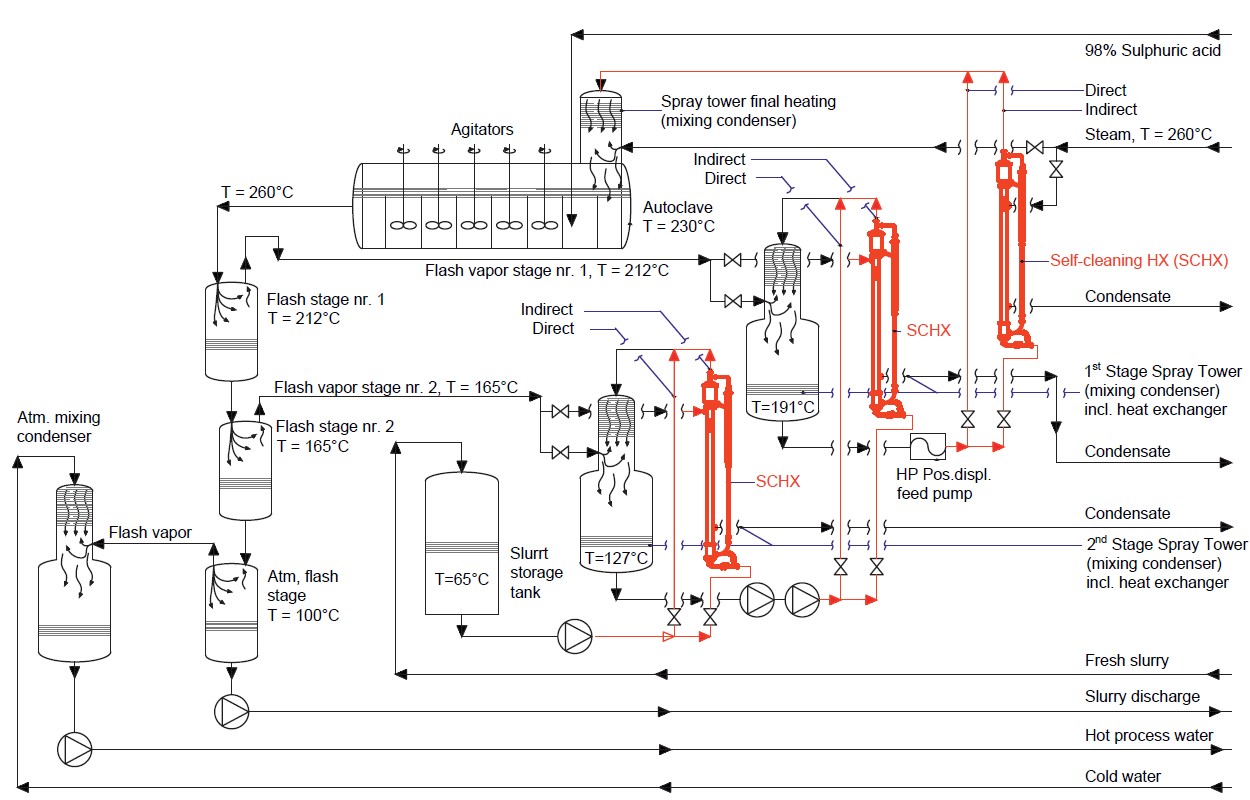
Figure 3 shows that it would also be possible to modify the existing directly heated laterite nickel processing plants into an indirectly heated configuration employing self-cleaning heat exchangers. Installing the indirectly heated flow path employing self-cleaning heat exchangers parallel to the existing directly heated flow path creates a unique flexibility in the operation of the plant enabling an easy return or fall-back from the ‘new’ technology on the ‘old’ technology, if necessary.
Because of the reliability of the self-cleaning heat exchangers, the fall-back possibility from ‘new’ on ‘old’ technology and the large benefits which can be achieved by the operation of the indirectly heated self-cleaning exchangers, the installation of full-size self-cleaning heat exchangers parallel to the existing directly heated installation should be considered, instead of rather costly small-scale pilot-plant testing prior to the installation of full-size self-cleaning heat exchangers.
About this Technical Story
This Technical Story was first published in Heat Exchanger World Magazine in April 2024. To read more Technical Stories and many other articles, subscribe to our print magazine.
Technical Stories are regularly shared with our Heat Exchanger World community. Join us and share your own Technical Story on Heat Exchanger World online and in print.