The design, fabrication, and installation of heat exchangers represent a critical aspect of various industrial processes where the efficient transfer of heat is essential. However, the longevity and performance of these crucial components can be significantly compromised by corrosion, and among the various corrosion mechanisms, pitting and crevice corrosion pose unique challenges. In this comprehensive exploration, we will delve deep into the intricacies of heat exchanger design, fabrication, and installation, with a specific focus on understanding, preventing, and mitigating pitting and crevice corrosion.
By Omari Hussein Sabuni, Mechanical Engineer – Kinyerezi Power Plant
Pitting corrosion
Pitting corrosion is a highly localized form of corrosion that manifests as the formation of small, isolated pits or craters on the metal surface. Unlike uniform corrosion, where the corrosion occurs evenly across the material, pitting corrosion concentrates its destructive effects in specific areas. The mechanism behind pitting corrosion involves the breakdown of the protective oxide layer that typically forms on the metal surface, leaving it vulnerable to aggressive ion attacks.
The initiation of pitting corrosion often begins with the local disruption of the passive oxide film, allowing aggressive ions to access specific points on the metal surface. These points become the nucleation sites for pits. Once initiated, pits can propagate rapidly and deeply into the material, creating irregular cavities. This penetration into the metal structure can lead to the compromise of mechanical properties, structural integrity, and ultimately result in material failure.
Influencing factors
- Chemical environment: Pitting corrosion is highly dependent on the chemical environment surrounding the metal. One of the most common factors contributing to pitting corrosion is the presence of aggressive chemicals, particularly chloride ions. Coastal environments, where salt-laden air is prevalent, and industrial settings with the use of chloride-containing substances, are especially prone to chloride-induced pitting. The chloride ions destabilize the passive oxide layer, making the metal susceptible to localized corrosion.
- Material susceptibility: The susceptibility of materials to pitting corrosion varies, with certain alloys exhibiting higher resistance than others. Austenitic stainless steels, characterized by their high chromium and nickel content, are generally more resistant to pitting corrosion. However, ferritic and martensitic stainless steels may be more prone to pitting, especially in aggressive environments.
- Temperature variations: Rapid and frequent temperature changes contribute significantly to the initiation and propagation of pits. This phenomenon is often observed in situations where thermal cycling occurs. Thermal cycling creates thermal gradients across the metal surface, leading to the breakdown of the protective oxide layer. The cyclic expansion and contraction of the material during temperature variations facilitate the onset of pitting corrosion.
Prevention and mitigation strategies
- Material selection: Choosing corrosion-resistant materials is a fundamental strategy in preventing pitting corrosion. High-alloyed stainless steels, such as 316 stainless steel, with increased chromium and nickel content, offer enhanced resistance to pitting. Additionally, selecting materials with proven corrosion resistance in specific environments is crucial.
- Protective coatings: Applying protective coatings or inhibitors that form a barrier against aggressive ions can help prevent the breakdown of the oxide layer and mitigate the risk of pitting. These coatings act as an additional layer of defence, inhibiting the initiation and progression of corrosion.
- Controlled environment: Controlling the chemical environment, particularly in industrial processes, is vital for preventing pitting corrosion. Minimizing the presence of aggressive substances, such as chloride ions, through proper material handling and process control, can significantly reduce the likelihood of pitting.
- Temperature control: Implementing measures to control and stabilize temperatures can mitigate the effects of thermal cycling. This can include insulation to minimize temperature fluctuations or engineering designs that reduce thermal stress on the material.
Crevice corrosion
Crevice corrosion represents a localized and highly destructive form of corrosion that occurs in confined spaces or crevices on metal surfaces. Unlike general corrosion, which affects the entire exposed area uniformly, crevice corrosion targets specific regions within joints, flanges, or areas where two surfaces meet. The mechanism of crevice corrosion involves the development of aggressive electrochemical cells within these confined spaces, leading to accelerated metal deterioration.
The initiation of crevice corrosion is typically facilitated by the creation of a differential concentration cell. In crevices, there is limited access to oxygen, and aggressive ions accumulate due to stagnant or slow-flow conditions. The restricted oxygen availability sets up an electrochemical gradient between the confined space and the surrounding area, leading to the establishment of anodic and cathodic regions within the crevice.
Corrosion initiates at the anodic sites, where metal dissolution occurs, and electrons are released. The electrons then migrate to the cathodic regions, where reduction reactions take place. The crevice environment, with the accumulation of aggressive ions, promotes the continuous progression of the corrosion process. The result is localized attack, often characterized by the formation of pits or crevice-like structures, compromising the structural integrity of the material.
Influencing factors
- Stagnation or low-flow conditions: Crevice corrosion is strongly associated with stagnant or low-flow conditions within the heat exchanger. Inadequate fluid movement in areas such as joints or dead-end zones creates an environment conducive to the accumulation of corrosive agents. Stagnation allows aggressive ions to concentrate, initiating and sustaining crevice corrosion.
- Material and crevice geometry: Both the material composition and the geometry of the crevice play crucial roles in the initiation and progression of crevice corrosion. The likelihood of crevice corrosion is heightened in narrow gaps or spaces where the accessibility of oxygen is restricted. Certain materials may be more susceptible, especially in the presence of aggressive chemicals that exacerbate the corrosion process.
Prevention and mitigation strategies
- Optimizing flow conditions: Ensuring proper fluid flow within the heat exchanger is vital for preventing crevice corrosion. Design modifications that minimize dead-end zones, promote turbulence, and maintain optimal flow rates can help mitigate the risk of crevice corrosion by reducing stagnant conditions.
- Material selection: Choosing materials resistant to crevice corrosion is paramount. High-alloyed stainless steels, titanium, and other corrosion-resistant alloys with enhanced resistance to aggressive environments are preferred choices for critical heat exchanger components.
• Surface finish: A smooth and polished surface finish on heat exchanger components helps minimize the formation of crevices and reduces the likelihood of corrosion initiation. Regular cleaning and maintenance practices are essential to preserve the integrity of the surfaces. - Corrosion inhibitors: Introducing corrosion inhibitors into the heat exchanger system can provide an additional layer of protection against crevice corrosion. These inhibitors work by forming a protective film on the metal surface, hindering the electrochemical processes that lead to corrosion.
- Regular inspection: Implementing routine inspections, including non-destructive testing techniques such as visual inspections and ultrasonic testing, allows for the early detection of crevice corrosion. Timely intervention can prevent the progression of localized corrosion and extend the service life of the heat exchanger.
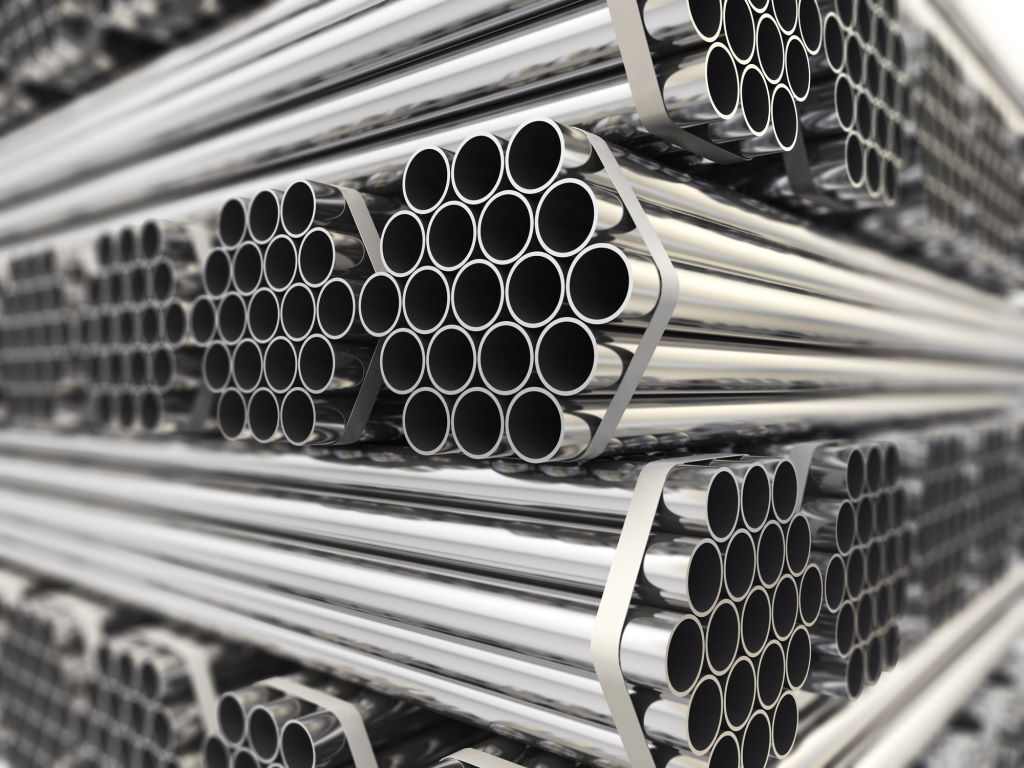
Design considerations
Material selection
Selecting the appropriate materials is a critical aspect of heat exchanger design, significantly influencing the system’s corrosion resistance and overall performance. The choice of materials plays a crucial role in mitigating the effects of pitting and crevice corrosion.
- Corrosion-resistant alloys: Opting for corrosion-resistant materials is paramount to ensure the longevity and reliability of heat exchanger components. High-alloyed stainless steels, such as austenitic grades like 316 stainless steel, offer excellent corrosion resistance due to their elevated chromium and nickel content. These alloys form a protective oxide layer on the surface, acting as a barrier against aggressive ions that can lead to corrosion.
- Titanium: Titanium is another highly corrosion-resistant material commonly used in heat exchangers. It exhibits exceptional resistance to various corrosive environments, making it suitable for applications where corrosion is a significant concern. Titanium’s corrosion resistance, coupled with its strength and low density, makes it an ideal choice for critical heat exchanger components, especially in industries with aggressive chemical processes.
- Corrosion-resistant alloys: Other corrosion-resistant alloys, including nickel-based alloys and duplex stainless steels, may also be considered based on specific operational requirements. These alloys offer a balance of corrosion resistance and mechanical properties, providing versatility in addressing diverse corrosion challenges.
The selection of materials should be guided by a comprehensive understanding of the operational environment, including the types of fluids, temperatures, and potential corrosive elements involved.
Surface finish
The surface finish of heat exchanger components is a crucial factor influencing both corrosion resistance and operational efficiency. A smooth and polished surface offers several advantages:
- Deposition prevention: A smooth surface minimizes the risk of deposit accumulation on heat exchanger components. Deposits can create localized environments conducive to corrosion initiation. Regular cleaning and maintenance become more effective on smooth surfaces, reducing the potential for corrosion.
- Corrosion mitigation: A polished surface helps resist the adhesion of corrosive substances and promotes the formation of a more robust and uniform passive oxide layer. This layer acts as a protective barrier against corrosive agents, enhancing the overall corrosion resistance of the material.
- Enhanced heat transfer efficiency: Smooth surfaces improve heat transfer efficiency by reducing frictional resistance to fluid flow. This is crucial for maintaining optimal heat exchange performance, minimizing energy consumption, and ensuring the heat exchanger operates at peak efficiency.
- Avoidance of stagnation: Designing heat exchangers to prevent stagnation is vital for mitigating the risks of both pitting and crevice corrosion. Stagnant or low-flow conditions create an environment where corrosive agents can accumulate, leading to localized corrosion.
- Minimizing dead-end zones: Dead-end zones, where fluid flow is minimal or non-existent, should be minimized during the design phase. These areas can become breeding grounds for corrosion, especially in crevices and corners where stagnant conditions prevail.
- Optimizing flow rates: Ensuring proper fluid flow rates is essential for preventing corrosion.
Well-designed heat exchangers incorporate features that promote optimal flow, such as well-designed piping, strategically placed baffles, and efficientflow distribution mechanisms. This prevents the establishment of stagnant conditions and helps maintain a uniform environment, reducing the likelihood of localized corrosion. - Regular flow analysis: Continuous analysis of fluid flow dynamics within the heat exchanger, including the identification and mitigation of areas with inadequate flow, is crucial. Computational fluid dynamics (CFD) simulations and flow modelling can aid in optimizing the design to ensure uniform fluid distribution and mitigate the risks associated with stagnation.
Fabrication techniques
Precision in welding:
- Importance of precision: Precision in welding is paramount in the fabrication of heat exchangers to minimize the creation of crevices or defects that could serve as initiation sites for corrosion. Welding processes involve the joining of metal components, and any imperfections in the weld can compromise the integrity of the structure, leading to localized corrosion issues.
- Avoidance of crevices: Precision in welding ensures tight and uniform joints, reducing the likelihood of crevices where aggressive ions can accumulate. Proper welding techniques, such as TIG (Tungsten Inert Gas) welding or electron beam welding, allow for precise control over the welding parameters, minimizing the formation of crevices and defects.
- Use of corrosion-resistant welding consumables: Selecting welding consumables with corrosion-resistant properties is crucial. The choice of filler materials should align with the corrosion resistance of the base materials, preventing galvanic corrosion and ensuring the overall corrosion resistance of the welded joints.
- Post-weld treatment: Employing appropriate post-weld treatments, such as passivation or pickling, helps remove oxides and scale formed during welding. This enhances the corrosion resistance of the weld and the surrounding areas, reducing the vulnerability to localized corrosion.
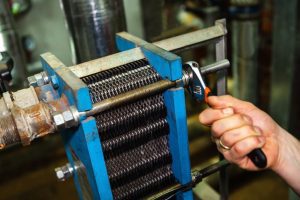
Quality control:
- In-process inspections: Rigorous quality control measures during the fabrication process involve continuous in-process inspections. Regular checks for weld quality, material integrity, and adherence to design specifications are essential. Non-destructive testing (NDT) techniques, such as radiography or ultrasonic testing, can be employed to identify hidden defects that could compromise the corrosion resistance of the heat exchanger.
- Material verification: Ensuring the correct selection and verification of materials is a critical aspect of quality control. Material inconsistencies or deviations from specifications can lead to corrosion vulnerabilities. Proper documentation and traceability of materials throughout the fabrication process are essential.
- Compliance with standards: Adherence to industry standards and codes is crucial for maintaining the quality and corrosion resistance of heat exchangers. Quality control processes should align with relevant standards to ensure that the fabricated components meet or exceed the specified requirements.
- Documentation and traceability: Comprehensive documentation and traceability of fabrication processes, materials, and inspections are vital for quality control. This documentation aids in identifying any issues that may arise during subsequent inspections, repairs, or maintenance, contributing to the long-term reliability of the heat exchanger.
Installation practices
Proper assembly:
- Gasket and joint considerations: Ensuring proper assembly involves meticulous attention to gaskets, joints, and connections. Properly sealing joints with suitable gaskets helps prevent the ingress of corrosive substances into crevices. Choosing gaskets made from corrosion-resistant materials is essential for maintaining the overall integrity of the heat exchanger.
- Precision in connection points: Similar to precision in welding, precision in connecting various components is crucial. Tight and well-fitted connections reduce the likelihood of creating crevices and ensure that the overall structure is free from defects that could lead to corrosion initiation.
Initial inspection:
- Thorough examination: Conducting a thorough inspection upon installation is the first line of defense against potential fabrication or assembly issues. This inspection involves visual examinations, dimensional checks, and, if necessary, non-destructive testing to identify any defects or irregularities that could compromise the corrosion resistance of the heat exchanger.
- Identification of potential corrosion sites: The initial inspection focuses on identifying potential corrosion sites, such as crevices, improperly sealed joints, or welding defects. Identifying these issues early allows for prompt remediation before the heat exchanger is put into service, minimizing the risk of corrosion-related problems during operation.
- Documentation of installation quality: Documenting the quality of the installation process is essential for future reference and maintenance. This documentation provides a baseline for subsequent inspections and serves as a valuable resource in troubleshooting and addressing any corrosion-related issues that may arise over the lifespan of the heat exchanger.
Conclusion
In conclusion, safeguarding heat exchangers against pitting and crevice corrosion demands meticulous attention from design to installation. Material selection, surface finish, precise fabrication, and vigilant quality control are imperative. This comprehensive approach ensures longevity, reliability, and optimal performance, safeguarding industrial processes reliant on efficient heat transfer.
About the author
Omari Hussein Sabuni is an experienced mechanical engineer at Kinyerezi Gas Power Plant, specializing in heat exchanger design, optimization, troubleshooting and providing practical solutions for various heat exchanger problems. He is skilled in analyzing thermal systems and developing innovative solutions to enhance heat transfer efficiency and adept at conducting feasibility studies, performing risk assessments, and ensuring compliance with industry standards.
About this Featured Story
Why Subscribe?
Featured Stories are regularly shared with our Heat Exchanger World community. Join us and share your own Featured Story on Heat Exchanger World online and in print.