Plate heat exchangers (PHE) are composed of fixed frame, movable frame, plates, gaskets, etc. But today we will talk about the heart of the heat exchanger: the plate. It’s a key component which is essential to ensure optimal performance of the equipment. Unfortunately, occasionally they are also the root of many problems that companies face when designing or using their PHE.
By Lei Tao, HFM. Images by HFM.
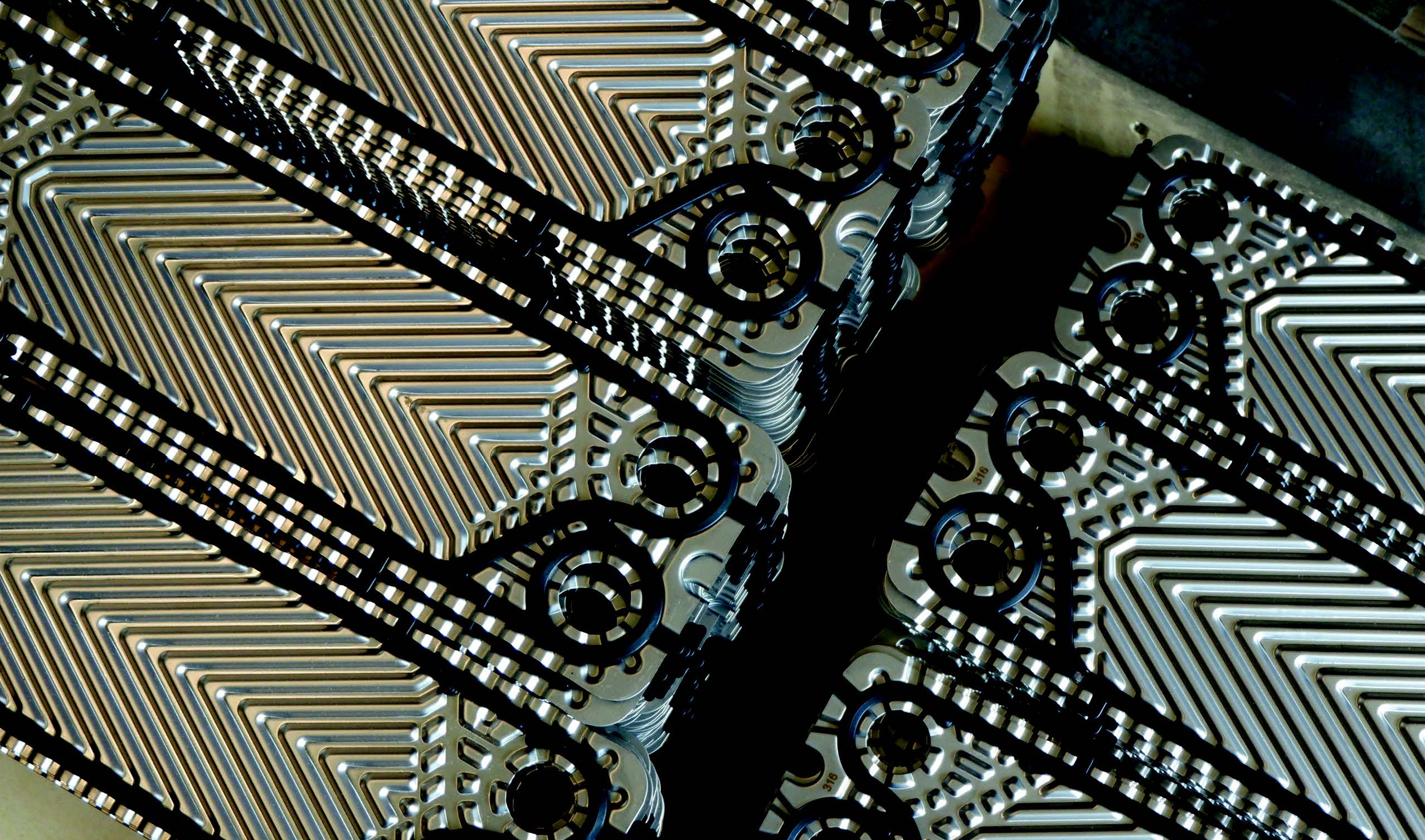
Since PHE can be used by a wide variety of industries, numerous problems, such as leaks, corrosion, clogging, deformation and many others, can arise if the chosen plates are not suitable for the certain applications.
Therefore, this guide aims to provide a quick, but general explanation of the main features of plates and what aspects you should consider when you designing your PHE.
Materials: depending on the flow media
The plates cannot have chemical reactions with the fluids which pass through the heat exchanger, so that it does not affect their composition and there is no corrosion in the plate. At the same time, suitable materials also are those ones that can resist the temperature and pressure that they are going to be subjected to. Some of the main materials include:
Stainless steel 304
This is the most widely used and inexpensive steel material. It is suitable for general organic, inorganic media, and other normal medium such as water, lubricating oil, ethanol, etc.
Stainless steel 316
This sort of stainless steel is also used for organic and inorganic media, but it is more resistant and less reactive than the 304 type. It is generally used for water, steam, oil, and low concentration acid and base solution, also low concentration chloride solution, etc.
254SMO
Ultra-low-carbon stainless steel with MO content to improve 316 stainless steel. It is suitable for media containing salt water and inorganic acids that cannot be suitable for stainless steel 316.
Titanium
This metal is commonly known for its resistance to chlorine-ion corrosion and H2S solution, because it can naturally generate a protective film. It is generally used for media such as seawater and low concentration chloride solution. It also has good corrosion resistance in oxidizing acid but bad corrosion resistance in reducing acid.
Titanium-Palladium Alloy
Titanium palladium alloy is an alloy formed by adding a small amount of precious metal Pd to pure titanium, which has excellent corrosion resistance to acidic media. And due to the addition of Pd element, the resistance to crevice corrosion in high chloride ion concentration media has been greatly improved. Titanium palladium alloy is highly suitable for high temperature, high concentration, and low pH chloride solutions.
Hastelloy C276
Ultra-low carbon nickel alloy is almost unaffected by chloride ions in low pH media. It is widely used in organic acids, hydrofluoric acid hydrochloric acids, phosphoric acid, chloride and fluoride and so on. It also has excellent corrosion resistance to various sulfuric acids especially for 98% sulfuric acid below 95ºC.
Nickel 200/201
Pure nickel plate containing more than 99% nickel. Mainly used for high temperatures (up to boiling point) and high concentration (50%-70%) caustic solutions (NaOH, KOH, etc.)
The corrugation shape: the core of heat transfer
The corrugated form is important because it will determine the flow of the fluid and therefore, the turbulence and the pressure drop that the fluids will be subjected to, which affects the efficiency they exchange heat.
Herringbone corrugation
The herringbone corrugation is a highly optimized corrugation design in plate heat exchangers. Its main feature is that the ripples present alternating V-shaped or inverted V-shaped patterns, forming a pattern similar to a herringbone. This design has a significant impact on heat transfer performance and fluid flow.
- Enhance turbulence effect: The herringbone corrugations create complex flow paths for fluid between heat exchange plates through staggered corrugation directions. The staggered ripples will increase the turbulence level of the fluid. The enhancement of turbulence helps to break the boundary layer of fluid on the plate surface, promoting the efficiency of heat transfer from hot fluid to cold fluid. This makes the heat transfer performance of the herringbone ripple very superior, especially in situations where efficient heat transfer is required.
- Reduce fouling accumulation: Due to the ability of herringbone ripples to increase the turbulence level of fluids, the turbulence formed on the surface of the ripples can reduce the deposition of dirt. This characteristic makes the herringbone corrugation particularly effective in handling fluids with high fouling coefficients, reducing the cleaning frequency and maintenance costs of the heat exchanger.
- High mechanical strength: The staggered corrugated structure enables the plate to distribute stress more evenly when subjected to fluid pressure, reducing the possibility of plate deformation. Therefore, the herringbone ripple is particularly suitable for high-pressure and high-temperature environments.
- Design optimization: In the design and manufacturing process, the angle (usually between 60°and 120°) and depth of the herringbone corrugation can be optimized according to specific applications. This customized design enables the heat exchanger to achieve optimal performance in practical applications. Therefore, it is widely used in petrochemical, natural gas, food and beverage, HVAC, marine and other occasions.
Wide gap channel shape
The wide gap plate heat exchanger is a type of heat exchanger specifically designed to handle fluids with high viscosity, containing particles or fibers. Compared with traditional plate heat exchangers, the plate design of wide channel plate heat exchangers is significantly different to meet special application requirements.
Large channel: The ripple shape of this type of plate is usually relatively gentle to ensure that a certain turbulence effect can still be maintained in a wider channel. The channel width between the plates is generally between 5 millimeters and 20 millimeters, depending on the properties of the fluid and application requirements. Compared to the deep ripple design of traditional plate heat exchangers, the ripples on the plates of wide gap plate heat exchangers may be closer to parallel ripples or shallow V-shaped ripples. This design can effectively prevent blockage of high viscosity fluids and reduce pressure drop, making wide channel heat exchangers particularly suitable for handling fluids containing particles, fibers, mud, or other difficult to handle fluids.
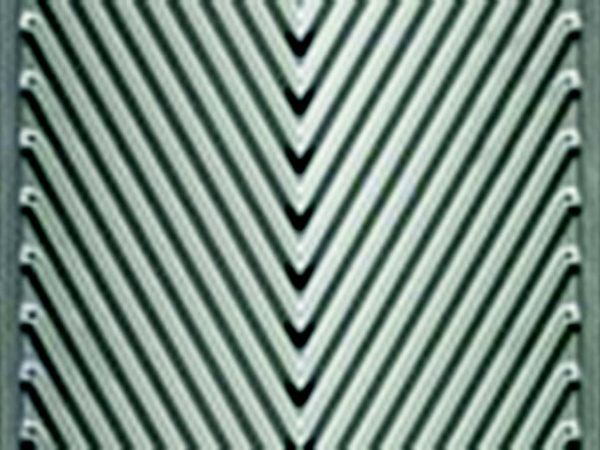
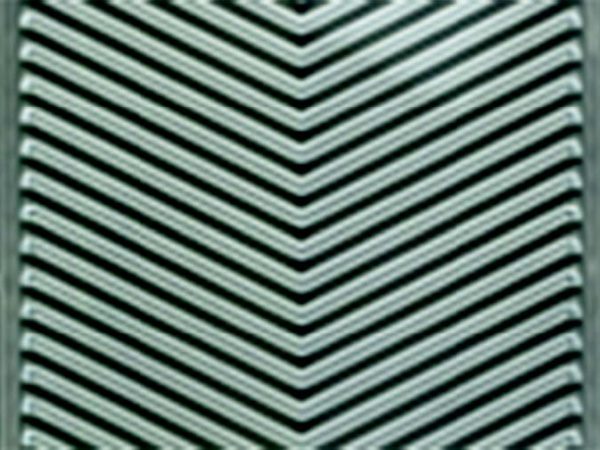
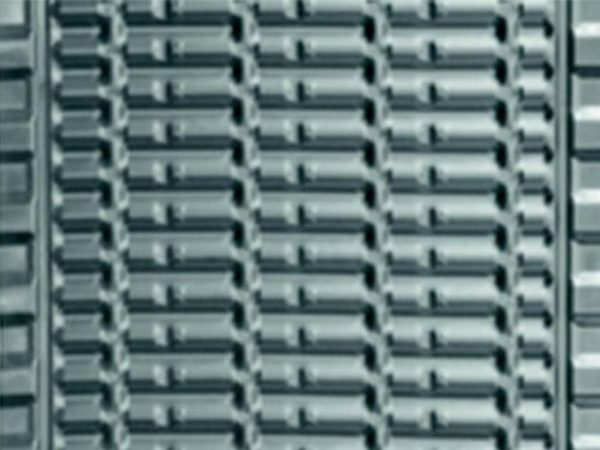
Although wide channel plates have significant advantages in handling complex fluids such as high viscosity, their heat transfer efficiency is usually lower than traditional plate heat exchangers due to their thicker plates and corrugated gaps.
Thickness and heat exchange area: the 3 dimensions of the plate
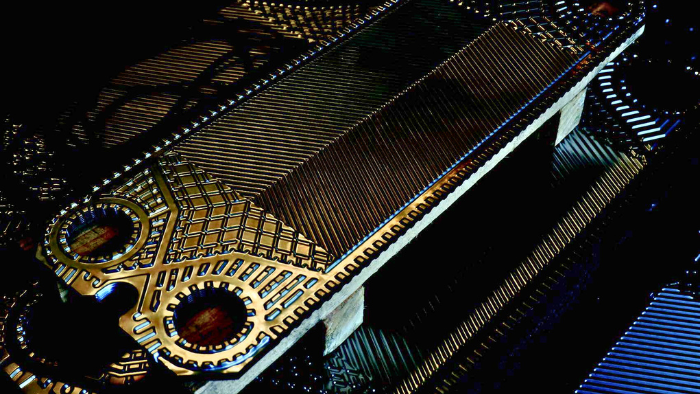
The thickness of the plates and the heat exchange area both significantly impact the performance and suitability of plate heat exchangers for different applications. Different aspects need to be taken in consideration, such as the cost, the space, the application and the kind of fluids to exchange heat.
Thicker plates
They are commonly chosen when the process requires higher mechanical strength due to high pressures or mechanical stress. It is also known for having a longer longevity, since their thickness give them better resistance to corrosion. They are most used in industrial processes involving corrosive fluids, high pressure steam heating and where the heat exchanger needs to be subject to constant disassembly and reassembly.
Thinner plates
These plates tend to provide more efficient heat transfer due to their reduced thermal resistance
and they tend to be more efficient as well as to be cheaper since they require less material to be manufactured. They are commonly used in HVAC systems, residential heating and cooling and other operations with non-corrosive fluids and lower pressure.
Plates with large heat exchange area
These plates promote higher heat transfer rates, which makes them suitable for applications that demand rapid heat exchange. They also tend to have reduced fouling as an effect of their large surface area, which prevents the contaminants to be concentrated small spots. They are commonly used in chemical processing, power generation and heating.
Plates with small heat exchange area
They tend to have reduced cost since they require a smaller amount of material to be manufactured and are easier to be maintained. They are also suitable for space-constrained installations, thanks to their reduced dimensions. They are commonly used in residential and small-scale applications and where a moderate heat transfer rate is enough to satisfy the usage requirements.
Best practices: ensuring optimal performance
Selecting the appropriate kind of plate is essential for the optimal performance of the PHE, but the best practices for installing it and maintaining this equipment is also key element that should not be taken for granted.
Location and orientation
It is important to ensure that the heat exchanger is installed on a level surface in order to prevent uneven stress on the plates and gaskets. Besides that, its location has to allow easy access for maintenance, inspection and cleaning, but at the same time, they should be located in a place where they are protected against external elements, such as weather or physical damage, especially for outdoor installations.
Piping connections
Careful alignment for the piping connections with the inlet and outlet ports of the heat exchanger are important to prevent stress on the connections and ensure proper fl ow distribution. Besides that, it is important to support the piping adequately to prevent strain on the heat exchanger and to maintain alignment over time.
Gasket and plate handling
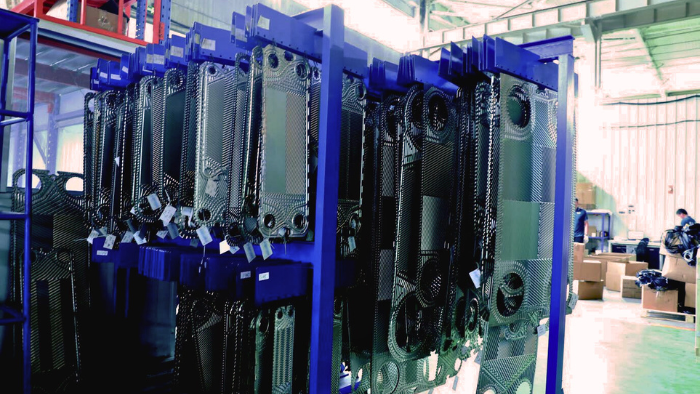
Both the plates and gaskets have to be handled carefully in order to avoid damage during the installation and has to be properly clean in order to prevent the presence of dust or other contaminants in the system.
Tightening procedures
It is important to use proper torque specifications when tightening bolts or clamps to secure the plates and gaskets. The bolts and clamps must be evenly tightened to ensure uniform pressure distribution. Over-tightening is a common mistake that can damage the plates, leading to gasket deformation and, subsequent leaks and corrosion.
Monitoring and maintenance
It is important to monitor the heat exchangers’ performance indicators, such as temperatures,
fl ow rate and pressure in order to detect potential abnormalities as early as possible. Besides that, operators should also establish a maintenance schedule that includes periodic inspection, cleaning, and replacement of gaskets as necessary.
Conclusion: a comprehensive approach to plate selection
As it can be concluded from this article, many aspects must be taken into consideration for the choice of the proper plate for a plate heat exchanger. Thus, it is necessary to take a holistic approach, considering an integral view of the process, such as the fluids to exchange heat, the purpose of the process, the budget, the expected PHE longevity, and even the physical space where the equipment is going to be installed. With a comprehensive selection process, you can ensure an efficient, reliable, and sustainable heat exchange solution tailored to your specific needs.
About the author
Lei Tao (Steven Lei), in his role as HFM’s CTO, boasts over 8 years of expertise in plate heat exchanger design and technical support, including his ability providing large-scale thermal engineering solution. Lei’s dedication to practical innovation has led to significant advancements, particularly in optimizing gasket performance within heat exchangers. Notable for his contributions to engineering solutions, Lei holds utility and invention patents, reflecting his focus on pioneering technologies. As a leader, Lei maintains a steadfast focus on technical precision and industry-leading standards, driving advancements in heat transfer technology. He can be reached via email at leitao@hfm-phe.com.
About this Technical Story
This Technical Story was first published in Heat Exchanger World Magazine in December 2024. To read more Technical Stories and many other articles, subscribe to our print magazine.
Technical Stories are regularly shared with our Heat Exchanger World community. Join us and share your own Technical Story on Heat Exchanger World online and in print.