Aeishwarya Chaudhari, a trailblazer in mechanical engineering, is driving innovation in sustainable energy. As a key figure at Vulcan Energy, she combines technical expertise with a passion for mentoring the next generation of engineers, advancing both technology and talent in the industry. Her leadership and vision made her an ideal choice to serve as Chairwoman of the Heat Exchanger World Conference Europe 2024. In this interview, Aeishwarya shares her insights into geothermal lithium production, the critical role of heat exchangers, and the exciting opportunities for innovation in green energy solutions.
By Iryna Mukha, Heat Exchanger World
Please outline your background; education and career, and the main steps that have brought you to your current position.
My name is Aeishwarya Chaudhari, and I am from Mumbai, India. I hold a degree in mechanical engineering and currently lead the mechanical engineering team at Vulcan Energy in Karlsruhe, Germany.
Reaching my current position has involved various factors, but I would like to emphasize a few key elements: passion, perseverance, stepping out of my comfort zone, networking, and immense family support. The latter is particularly crucial, as it often operates behind the scenes. As the saying goes, we only see the tip of the iceberg, but there is much more beneath the surface.
How large is the team you manage and what are the core skills of the members in it?
At Vulcan, I oversee the Mechanical Engineering Team, manage escalations to meet quality, cost, and schedule targets across all projects. I take on organizational responsibilities, exercise excellent judgment in decision-making, and provide support to colleagues and junior engineers.
My team and I are responsible for creating and reviewing technical requirements, specifications, and services for mechanical equipment, including pressure vessels, process columns, heat exchangers, storage tanks, etc. Duties involve preparing and reviewing datasheets, specifications, material requisitions, evaluating technical bids, reviewing vendor documents, and coordinating engineering efforts with vendors and other engineering disciplines. Additionally, provides technical guidance to engineering contractors as required. We are also tasked with finalizing spare parts strategies and selecting the appropriate construction materials through discussions with operations leaders, as well as technology and process experts. We also collaborate with various engineering contractors during the conceptual and basic engineering phases. Given this approach, our team size typically peaks at around 5-6 engineers. This number is expected to increase as we move into the execution phase of the project.
Can you give us a brief description of the Lionheart project and why it is unique? How/where are heat exchangers deployed in this project?
Vulcan’s Phase One Lionheart Project is Europe’s most advanced integrated sustainable lithium and renewable energy project. I feel fortunate to be part of a team making history in the lithium industry. The integrated lithium and renewable energy project adapt existing, commercially proven technology to produce battery-quality lithium from naturally heated subsurface brine in the Upper Rhine Valley, to deliver a local source of sustainable lithium for the European battery industry, with a co-product of renewable energy. The project spans the Upper Rhine Valley for upstream and midstream activities, and the Frankfurt region for downstream operations.
As we know, heat exchangers play a vital role in the chemical and process industry, and their importance is indispensable in this project as well. We plan to use various types of heat exchangers, including shell and tube, plate and frame, and air-cooled heat exchangers, along with falling film evaporators. These will be utilized for several applications, such as cooling industrial water, cooling brine, and evaporation in downstream chemical processes.
The use of geothermal energy is gaining traction as a green energy source. Can you discuss how this is developing and discuss some of the general opportunities for heat exchanger manufacturers in this sector?
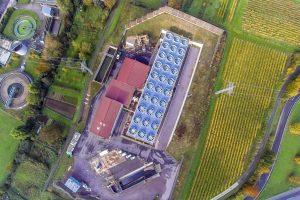
Geothermal energy is rapidly gaining traction as a sustainable and reliable green energy source. Following could be some areas of key developments and opportunities for heat exchanger manufacturers in this sector:
- Technological knowhow and advancement: Innovations in drilling and hydraulic fracturing, originally developed for the oil and gas industry, can be brainstormed and adapted for use in geothermal energy.
- Global potential: Geothermal energy has the potential to significantly contribute to global electricity demand. Research and statistics indicate that with ongoing technological advancements and cost reductions, geothermal energy could account for up to 15% of the growth in global electricity demand by 2050.
- Uninterrupted and reliable source: In contrast to solar and wind, geothermal energy offers continuous, 24/7 power, making it a stable and dependable energy source that can effectively complement other renewables.
Opportunities for heat exchanger manufacturers
- Specialized coatings: A key challenge in geothermal energy is managing the corrosive and scaling properties of geothermal brines. Developing innovative solutions, such as specialized corrosion-resistant coatings for equipment handling these highly corrosive fluids, is crucial. These coatings must endure the entire design life of the plant, which typically ranges from 15 to 25 years of continuous operation.
- Material innovations: Capital cost is a critical factor in project investments, driving efforts to optimize expenditure. There is a continuous focus on developing heat exchangers using cost-effective materials without sacrificing performance. For instance, replacing stainless steels or duplex stainless steels with low-alloy steels can significantly reduce costs while maintaining corrosion resistance through the application of advanced coatings. Chromium based alloys are significantly expensive as compared to the low alloy steels.
- Collaborative approach: International collaborations, such as the GEOHEX project, unite expertise from multiple countries to develop and test innovative heat exchanger technologies. These initiatives offer manufacturers the chance to lead in innovation and secure a competitive advantage. More information about the GEOHEX project can be found here.
Mentoring younger engineers seems to be a key part of your job, what are some of the challenges involved in this. Do you have tips for others in your position?
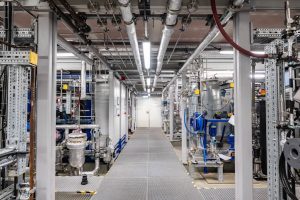
Mentoring younger engineers is indeed a crucial part of my role, but it comes with its fair share of challenges.
A key difficulty lies in fostering a passion for core engineering disciplines, such as those in the process and manufacturing industries. Many young engineers also face a gap between academic knowledge and industry demands, which can be addressed through closer collaboration between universities and industry representatives, such as interactive sessions or internships.
Another challenge is introducing them to practical knowledge, industry standards, and adapting to professional practices. Mentors also need to help develop essential skills like logical reasoning, problem-solving, communication, and accountability, all of which are critical for their growth.
For others in similar roles, structured and comprehensive mentoring is essential. Start with a clear onboarding process, regular feedback sessions, and tools like a ‘buddy’ program. Focus on hands-on learning and delegate tasks to build trust and responsibility. Ensure mentees are exposed to project details, standard operating procedures, and necessary tools or software.
Encourage participation in external learning opportunities like workshops and seminars. Foster a culture of knowledge sharing and continuous learning. Finally, guide them in setting long-term goals with a clear development plan to keep them motivated. Mentoring requires effort, but the results are worth it—for both the mentee and the mentor.
What are some of the challenges in working with multiple disciplines across a project? Do you have a particular strategy for this?
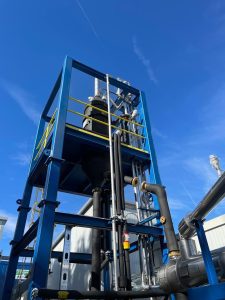
Working with multiple disciplines on a project often presents several challenges. Communication barriers, both technical and interpersonal, are common, as are cultural differences that can influence work styles and expectations. Teams sometimes work in silos, which hinders collaboration and alignment on the project’s common goals and value drivers.
A lack of clarity on the scope of work, roles, and responsibilities can lead to confusion or overlap. It’s crucial to have well-defined responsibilities and maintain thorough documentation, such as change logs, to keep all disciplines informed about updates.
To address these challenges, I focus on fostering collaboration and alignment through structured strategies. Regular interdisciplinary workshops and interactive project management sessions are invaluable for building understanding and coordination between teams. Conducting design reviews at various stages ensures alignment and helps identify potential issues early.
Clear communication and a shared commitment to project goals are key to successful interdisciplinary work. By creating an open and collaborative environment, teams can overcome differences and work toward delivering high-quality results.
Can you outline the procedures for verifying items delivered for projects? What are some common challenges you encounter with this, e.g. material quality, grades, etc.
Ensuring the receipt of equipment at the site as per project requirements involves several critical steps. Maintaining constant collaboration and communication with the equipment fabricator or supplier is essential. For equipment falling under the Pressure Equipment Directive (PED), coordination with relevant bodies such as TUV is vital, along with ensuring the CE mark is present on the nameplate. Reviewing equipment drawings and calculations to confirm compliance with harmonized PED codes and technical requirements is equally important. Performing all necessary non-destructive tests (NDEs) on the equipment is paramount, and aligning on Inspection Test Plans (ITPs) is crucial. Lastly, reviewing the packing and shipping notes ensures the equipment meets the project’s quality and requirements.
Sustainability is an important part of the Vulcan Energy philosophy; can you tell us something about how this is reflected in the materials/equipment/processes used?
Sustainability is the cornerstone upon which Vulcan was founded and we are committed to being a leader in Environmental, Social and Governance (ESG) initiatives and reporting. We believe that our purpose, to empower a carbon neutral future, clearly and succinctly represents Vulcan’s identity. It showcases why we exist, what problems we are working to solve and what we aspire to do. Our mission is to become Europe’s leading sustainable lithium business while also enabling energy security through geothermal energy and heat production.
Join the Heat Exchanger World Conference in 2026!
Keep the knowledge exchange going at the next edition of Heat Exchanger World Conference & Expo Europe, which will be held on 6th & 7th May 2026 in Rotterdam. Details will be released in 2025. For information, please contact Ms Iryna Mukha: i.mukha@kci-world.com
About this Featured Story
Why Subscribe?
Featured Stories are regularly shared with our Heat Exchanger World community. Join us and share your own Featured Story on Heat Exchanger World online and in print.