Heat exchangers, integral to diverse industrial processes, serve as linchpins in the seamless transfer of thermal energy between fluids. Their role is pivotal, optimizing the efficiency of operations spanning from power generation to chemical production. Despite their critical significance, these components are susceptible to failure, and stress corrosion cracking (SCC) stands out as a formidable challenge contributing to their degradation.
By Omari Hussein Sabuni, Mechanical Engineer – Kinyerezi Power Plant
Concept of stress corrosion cracking (SCC)
Definition: Stress Corrosion Cracking (SCC) is a highly specialized and insidious form of corrosion that manifests under the combined infl uence of tensile stress and a corrosive environment. It stands out as a unique corrosion phenomenon due to the simultaneous presence of mechanical stress and a corrosive medium, both of which synergistically contribute to the degradation of materials.
Mechanism: The mechanism of stress corrosion cracking involves a complex interplay of mechanical and chemical factors. SCC typically begins at localized points on the material’s surface where there is a concentration of tensile stress. This stress can result from external loads, residual stresses from manufacturing processes, or a combination of both. The corrosive environment, which may include factors like moisture, chemicals, or specifi c gases, accelerates the corrosion process.
The synergistic effect of tensile stress and corrosion acts as a catalyst for the initiation and propagation of cracks. The cracks tend to initiate at microscopic defects or points of stress concentration, creating a pathway for the corrosive medium to penetrate the material. Once initiated, these cracks can propagate rapidly, leading to a decrease in the material’s structural integrity.
Types of stress corrosion cracking
1. Transgranular SCC
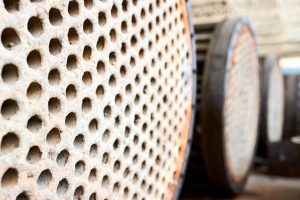
Definition: Transgranular SCC is characterized by cracking occurring along the grain boundaries of the material, traversing the individual grains.
Mechanism: The mechanism of transgranular SCC involves the propagation of cracks through the internal structure of the material. These cracks initiate and grow through the grains, causing disruptions along the boundaries. Several key aspects define the mechanism:
I. Grain boundary attack
- Cracks initiate and propagate predominantly within the grains, leading to a localized attack on the material.
- The choice of specific crystallographic orientations can influence the susceptibility of a material to transgranular SCC. Certain crystallographic planes and directions may be more prone to cracking.
II. Crystallographic orientations
- The propensity for transgranular SCC is often associated with specific crystallographic orientations of the grains.
- The anisotropic nature of materials, where properties vary with direction, can lead to preferential crack propagation along certain crystallographic planes.
III. Reduction in mechanical strength
- As cracks propagate through individual grains, they disrupt the continuity of the material, leading to a reduction in mechanical strength.
- The accumulated effect of multiple cracks can significantly compromise the structural integrity of the material.
IV. Susceptibility to stress intensity
- Transgranular SCC is often more sensitive to stress intensity factors, and the conditions that promote crack initiation and growth can be more localized.
2. Intergranular SCC
Definition: Intergranular SCC involves cracking that occurs across the grain boundaries of the material.
Mechanism: The mechanism of intergranular SCC is characterized by cracks following the grain boundaries, impacting the integrity of the material at the interfaces between grains. Key aspects of the mechanism include:
I. Path along grain boundaries
- Cracks propagate along the boundaries between adjacent grains, creating a path that extends across the material.
The intergranular nature of the cracking distinguishes it from transgranular SCC, where the cracks penetrate through individual grains.
II. Changes in microstructure
- Intergranular SCC is often associated with changes in the material’s microstructure, such as sensitization or precipitation of certain phases.
- These changes make specific grain boundaries more susceptible to cracking, often due to the formation of less corrosion-resistant phases.
III. Sensitization and precipitation
- Sensitization refers to the depletion of corrosion-resistant elements near the grain boundaries, making these regions more susceptible to corrosive attack.
- Precipitation of less corrosion-resistant phases along the grain boundaries can promote crack initiation and propagation.
IV. Selective attack on grain boundaries
- The cracking in intergranular SCC selectively targets grain boundaries, leading to a more distributed and interconnected network of cracks compared to transgranular cracking.
Factors contributing to stress corrosion
Environmental factors:
Presence of corrosive agents:
- Nature of fluid: The chemical composition of the fluid in contact with the heat exchanger is a critical factor. Corrosive agents such as chloride ions, sulfides, or acids can accelerate corrosion and promote stress corrosion cracking (SCC).
- Contaminants: The presence of impurities or contaminants in the fluid can exacerbate the corrosive effects, increasing the likelihood of SCC.
Temperature and pressure:
- Operating conditions: Elevated temperatures and pressures can intensify the severity of SCC. High temperatures accelerate the chemical reactions involved in corrosion, while increased pressure may enhance the penetration of corrosive agents into the material.
pH and chemical composition:
- Acidity or alkalinity: The pH level of the environment can influence the electrochemical reactions that drive corrosion. Environments with extreme acidity or alkalinity can be particularly aggressive in promoting SCC.
- Chemical composition: Specific chemicals in the environment can react with the material, leading to localized corrosion and stress corrosion.
Material factors:
Material susceptibility: alloy selection: different alloys exhibit varying levels of susceptibility to SCC. Some alloys may be inherently more resistant, while others may be prone to cracking under specific environmental conditions:
Microstructure: The microstructure of the material, including grain size and orientation, can influence its vulnerability to stress corrosion:
Heat treatment history:
- Manufacturing processes: The heat treatment history of the material during manufacturing plays a crucial role. Improper heat treatment can result in changes to the material’s microstructure, making it more susceptible to SCC.
- Sensitization: Certain heat treatments may lead to sensitization, reducing the corrosion resistance of the material and promoting SCC.
Mechanical factors
Residual stress:
- Welding and fabrication: Welding, forming, or other fabrication processes introduce residual stresses into the material. These residual stresses can act as localized areas of high stress concentration, providing sites for SCC initiation.
- Stress Riser: Residual stresses can create stress risers, making specific regions of the material more vulnerable to the combined effects of stress and corrosion.
Applied stress:
- Mechanical loads: External forces, such as mechanical loads or vibrations, can induce additional stress on the material. The presence of applied stress, combined with corrosive conditions, accelerates the initiation and propagation of cracks.
- Cyclic loading: Repeated or cyclic loading, common in many industrial applications, can contribute to fatigue and increase the susceptibility to SCC.
About the author
Omari Hussein Sabuni is an experienced mechanical engineer at Kinyerezi Gas Power Plant, specializing in heat exchanger design, optimization, troubleshooting and providing practical solutions for various heat exchanger problems. He is skilled in analyzing thermal systems and developing innovative solutions to enhance heat transfer efficiency and adept at conducting feasibility studies, performing risk assessments, and ensuring compliance with industry standards.
About this Featured Story
Why Subscribe?
Featured Stories are regularly shared with our Heat Exchanger World community. Join us and share your own Featured Story on Heat Exchanger World online and in print.