Active Pharmaceutical Ingredient (API) industries require multi-purpose plants capable of handling highly corrosive fluids. This need is even more critical for Contract Development and Manufacturing Organizations (CDMOs), which frequently change production processes, necessitating flawless equipment cleanliness and reliability.
Text & images by Italprotec Industries

The shift from graphite to silicon carbide heat exchangers
Historically, impregnated graphite heat exchangers were widely used due to a lack of viable alternatives. However, graphite presents several issues: it is porous, prone to degradation, and can release dust contaminants—posing a significant risk to the purity of pharmaceutical substances. Given that APIs are often delicate and expensive, contamination can lead to severe financial and regulatory consequences.
To address these challenges, heat exchangers with Silicon Carbide (SiC) tubes have been developed. Silicon Carbide, being a ceramic material with excellent thermal conductivity, eliminates contamination risks and reduces equipment size due to its high heat exchange coefficient. A prominent Italian API company has already implemented FLOWSiC® exchangers with SiC tubes, replacing traditional graphite exchangers for enhanced efficiency and safety.
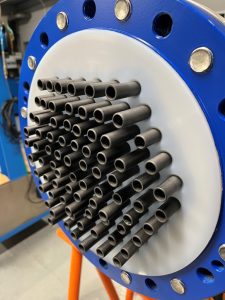
Advanced features of FLOWSiC® heat exchangers
FLOWSiC® exchangers are designed with PFA-lined steel tube plates, ensuring robust construction and simple PED qualification. The process fluid is typically directed through the tubes, with PFA- or enamel-lined heads providing full resistance against corrosive substances. Additionally, sealing O-rings made of FFKM perfluoroelastomer further enhance durability. In cases where the process fluid is placed on the shell side, a PFA- or enamel-lined shell is also available for superior corrosion protection.
Standard design parameters include operational temperatures ranging from -25°C to +200°C and pressure tolerances from full vacuum to 6 bar. Custom configurations are available to meet specialized industrial requirements. With heat exchange surfaces exceeding 20 square meters, FLOWSiC® heat exchangers offer long-term reliability, safety, and absolute contamination-free performance.
Conclusion
The transition to Silicon Carbide heat exchangers marks a significant advancement in API manufacturing. By eliminating contamination risks, enhancing thermal efficiency, and providing a durable solution for corrosive applications, FLOWSiC® exchangers set a new standard for safety and performance in pharmaceutical production.
Table 1. Thermal conductivity of various materials.
MATERIAL |
THERMAL CONDUCTIVITY W(m/K) |
IMPREGNATED GRAFITE | 129 |
SILICON CARBIDE | 120 |
TANTALUM | 57.5 |
ZIRCONIUM | 22.7 |
TITANIUM | 21.9 |
STAINLESS STEEL | 17 |
HASTELLOY | 11 |
GLASS | 2 |
PTFE | 0.25 |
About this Technical Story
This Technical Story was first published in Heat Exchanger World Magazine in March 2025. To read more Technical Stories and many other articles, subscribe to our print magazine.
Technical Stories are regularly shared with our Heat Exchanger World community. Join us and share your own Technical Story on Heat Exchanger World online and in print.