One of Argentina’s largest methanol plants currently faces unique challenges in maintaining its complex heat transfer systems, particularly as its equipment ages beyond its originally intended lifespan. In this interview, Nicolás Giménez, Head of Stationary Equipment Inspection at YPF, discusses the plant’s ongoing challenges, the impact of high-temperature and high-pressure operations on heat exchangers, and the innovative solutions being implemented to ensure long-term operational success.
By Iryna Mukha, Heat Exchanger World
YPF Complejo Industrial Plaza Huincul is a refinery and petrochemical facility located in the heart of Neuquén Province, near the world-renowned unconventional oil and gas deposit, Vaca Muerta. The facility consists of a small refinery with an atmospheric distillation process, a naphtha reforming plant, and a storage tank park supplying naphtha and gasoil to northern Patagonia. Additionally, it houses one of Argentina’s largest methanol plants, operational since 2002.
The methanol plant plays a crucial role not only in the industrial sector but also in the local community. It provides employment opportunities and supports regional economic growth, making it an essential asset for the province and its people.
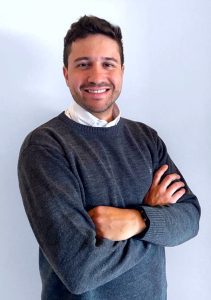
Methanol is a critical raw material used in biodiesel production and pharmaceutical manufacturing. Its production process involves several integrated sub-processes that transform natural gas and steam into high-purity liquid methanol, stored in tanks. The process comprises four primary stages:
- Sulfur elimination
- Gas reforming
- Methanol synthesis
- Methanol distillation
Nicolás Giménez, Head of Stationary Equipment Inspection at YPF Complejo Industrial Plaza Huincul, leads a team responsible for non-destructive testing (NDT) on both refinery and petrochemical equipment. His role encompasses overseeing new and existing stationary equipment, including storage tanks, pipelines, and heat transfer systems. With a degree in mechanical engineering and a decade of experience in stationary equipment engineering, commissioning, and maintenance, Nicolás shared insights into the heat transfer challenges his team has faced over the past ten years.
What are the main challenges your plant is experiencing with heat transfer?
Methanol production is a highly integrated and complex process. Our plant was originally designed with a 20-year operational lifespan, meaning that much of our stationary equipment is reaching the point where refurbishment or replacement is necessary to maintain nominal production levels. The biggest challenges stem from high equipment replacement frequency, short turnaround windows, and constant production demands.”
“These issues significantly impact all stationary equipment, particularly heat exchangers. The methanol process operates under high temperature and pressure conditions. For instance, our exhaust gas duct utilizes high-temperature combustion gases to generate high-pressure steam in a vertical exchanger. This steam powers a turbine that drives a high-pressure compressor, which in turn compresses synthesis gas for the distillation stage. If this vertical exchanger fails, the entire process must be halted.”
How do heat exchangers in a methanol plant differ from those in a typical refinery?
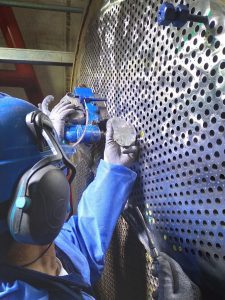
“Methanol plant heat exchangers must withstand much harsher conditions than those found in standard refinery operations. The choice of materials, manufacturing processes, and design considerations are far more demanding. High-temperature-resistant materials, complex welding techniques, and rare filler materials are all required.”
“For example, in the exhaust gas duct, temperatures can reach up to 900°C, and the exchangers, arranged in a vertical configuration, must endure tube skin temperatures of up to 650°C. This necessitates the use of stainless steel or low-alloy steels.”
“Another critical example is our water preheater, where water is pressurized at 110 kg/cm². The tubesheet in this exchanger is 300 mm thick, and the tubes are welded only on the tube side. A small gap between the tubes and the holes in the tubesheet allows water ingress via capillary action. Due to the high temperatures of the reformed gas, this water vaporizes, causing chemical accumulation. The combination of residual and in-service stresses, along with high heat flux, induces stress corrosion cracking, ultimately leading to welding joint failures. This results in water losses to the reformed gas stream, directly impacting production efficiency.”
“Similarly, our process gas boiler is tasked with cooling reformed gas at 850°C by transferring heat to water in the shell side to generate high-pressure steam, which powers the synthesis gas compressor. To withstand these conditions, the boiler’s inlet features a refractory lining composed of bricks and a metal cover sheet with ferrules backed by castable refractory. However, due to the complexity of the design and limited expertise in refractory maintenance, heat has, over time, penetrated the tubesheet (A 182 P11), causing severe cracking. This has extended turnaround times from 10 to 30 days.”
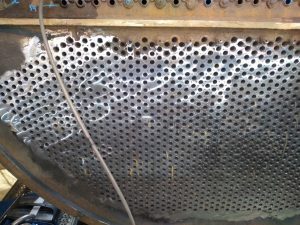
What are the main difficulties you’ve encountered over the last ten years from a maintenance perspective?
“From a maintenance standpoint, one of our greatest difficulties is that the plant’s original design did not prioritize ease of repair. The need for frequent inspections and maintenance is at odds with the plant’s design constraints. Furthermore, our remote location adds another layer of complexity, as sourcing specialized labour for inspections and repairs is both challenging and costly.”
What solutions have you implemented to address these challenges?
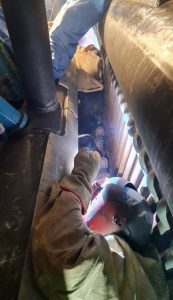
“Given the design limitations of our plant, we’ve had to adapt and optimize our approach to maintenance and reliability. With over 20 years of operational experience, we’ve leveraged our accumulated knowledge and data to prevent failures and mitigate equipment damage. We actively develop and implement risk-based inspection (RBI) strategies, integrity operating windows (IOW), and corrosion control documents (CCD) to improve predictive maintenance.”
“To bridge the experience gap, we also work closely with our maintenance contractors, ensuring that best practices are followed. Additionally, we’ve taken steps to enhance the design of equipment nearing replacement by incorporating lessons learned from past issues.”
“One of our major improvements has been upgrading materials in key heat exchangers. We have replaced certain components with advanced alloys that provide greater corrosion resistance and durability under high-temperature conditions. For example, in our vertical exhaust gas duct heat exchangers, we are evaluating alternatives such as stainless steel to better withstand the extreme heat and chemical exposure.”
“For instance, we’ve replaced brick refractory linings with gunning refractory in our process gas boiler to make maintenance more efficient, leveraging our experience in contractor-based gunning applications. We are also in the process of procuring a new water preheater designed with inner bore welding for the tubesheet-tube joint, which will improve durability. Moreover, we are evaluating material changes in our vertical exhaust gas duct heat exchangers to better accommodate high temperatures.”
“In summary, our methanol plant relies on a highly integrated system of stationary equipment operating under extreme conditions. A single equipment failure can disrupt the entire process. Balancing process efficiency, personnel safety, regulatory compliance, and budget constraints is no easy task, but our goal remains clear: continuously improve our approach to reliability and maintenance to achieve long-term operational success. At the same time, we are mindful of the plant’s significance to the local economy and community, ensuring that our operations continue to provide jobs and support regional development.”
About this Featured Story
Why Subscribe?
Featured Stories are regularly shared with our Heat Exchanger World community. Join us and share your own Featured Story on Heat Exchanger World online and in print.