In the fast-paced world of design, success often hinges on seamless collaboration, efficient processes, and a deep understanding of the workflow. Yet, for many designers, the elusive quest for a complete and structured design workflow remains ongoing. Frustrated by the lack of comprehensive resources, I embarked on a mission to develop a guide that unravels the intricacies of the design process, providing designers with the tools and knowledge they need to excel.
By Muhammad Rehan – Mechanical Engineer
This two-part article aims to unravel the intricacies of the design process, providing designers with the tools and knowledge they need to excel. In Part 1, we will delve into the initial steps of the design workflow, from defining requirements and specifications to the preliminary design, thermal design, and mechanical design phases. By understanding these fundamental principles and best practices, designers can lay a solid foundation for creating impactful heat exchanger designs.
Design workflow
Developing an engineering design and fabricating a shell and tube heat exchanger typically involves several steps. Here is a logical workflow one can follow.
1. Define Requirements and Specifications:
-
- Understand the purpose, performance requirements, and operating conditions of the heat exchanger.
- Determine the desired heat transfer rate, temperature ranges, pressure limits, fluid properties, and any other relevant specifications.
2. Preliminary Design:
-
- Select the heat exchanger type (shell and tube).
- Determine the number of tubes, tube diameter, and tube length based on the heat transfer requirements and available space.
- Decide on the shell diameter and length.
- Estimate the overall size and dimensions of the heat exchanger.
3. Thermal Design:
-
- Calculate the heat duty (heat transfer rate) based on the temperature difference between the hot and cold fluids and their flow rates.
- Choose appropriate correlations and perform thermal calculations to determine the required surface area for heat transfer.
- Determine the heat exchanger effectiveness and the number of transfer units (NTU) to optimize the design.
4. Mechanical Design:
-
- Determine the tube layout, including the number of tube passes, baffles, and their spacing.
- Perform mechanical calculations to ensure structural integrity and pressure vessel compliance.
- Select appropriate materials for the tubes, shell, baffles, and other components based on the process conditions and corrosion considerations.
- Design the tube supports, tie rods, and tube sheets.
- Consider the expansion and contraction of tubes due to temperature changes.
5. Flow and Pressure Drop Analysis:
-
- Analyze the flow patterns and pressure drop of the fluids inside the heat exchanger.
- Calculate the pressure losses in the tubes, shell, and other flow paths.
- Optimize the flow distribution to minimize pressure drops while maintaining effective heat transfer.
6. Detailed Design and Drawings:
-
- Prepare detailed engineering drawings, including assembly drawings, manufacturing drawings, and part specifications.
- Specify tolerances, surface finishes, and welding requirements.
- Incorporate safety features, such as pressure relief devices and access points for maintenance.
7. Fabrication and Quality Assurance:
-
- Fabricate the heat exchanger according to the design specifications.
- Conduct quality checks during the manufacturing process to ensure compliance with design requirements.
- Inspect welds, conduct non-destructive testing (NDT), and perform pressure tests to verify the integrity of the heat exchanger.
8. Installation and Commissioning:
-
- Install the heat exchanger in its intended location.
- Connect the necessary piping, valves, and instrumentation.
- Conduct performance tests to verify the heat exchanger’s functionality and efficiency.
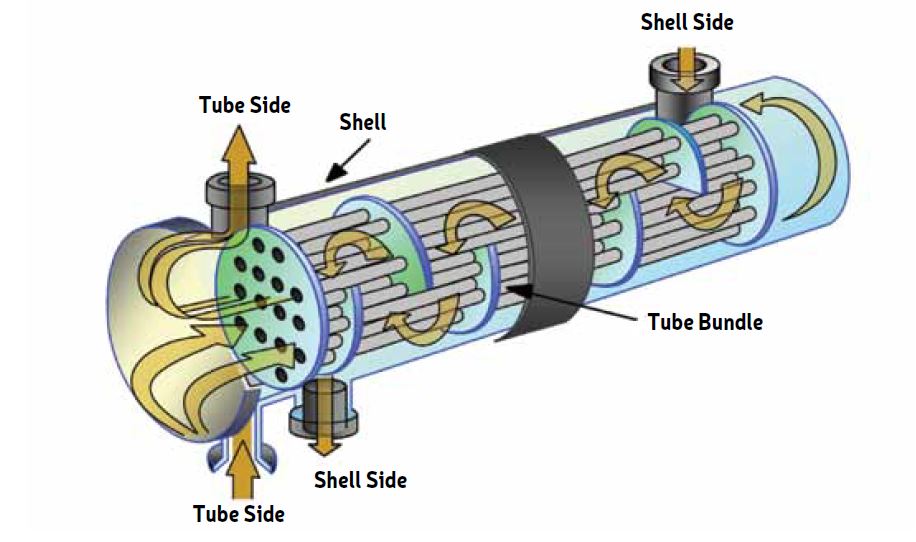
Define requirements and specifications
The first step establishes the foundation for the design and fabrication process. The following information is collected in this phase.
Project scope:
- Identify the purpose and objectives of the heat exchanger project. Determine the desired outcomes and performance goals.
- Define the boundaries of the project, including the specific system or process where the heat exchanger will be integrated.
- Consider any constraints, such as budget limitations, timeline requirements, or regulatory compliance.
Performance requirements:
- Specify the performance requirements for the heat exchanger, including heat transfer rates, temperature ranges, flow rates, and pressure limits.
- Determine the desired level of efficiency, effectiveness, and reliability for the heat exchanger operation.
- Consider any specific industry or application standards that need to be met.
Operating conditions:
- Identify the operating conditions under which the heat exchanger will function, including the types of fluids involved, their properties (such as viscosity, density, and heat capacity), and their temperature and pressure ranges.
- Consider factors such as corrosiveness, fouling potential, and thermal conductivity of the fluids.
Interface requirements:
- Identify the interfaces with other components or systems that the heat exchanger will interact with, such as piping systems, pumps, valves, or control systems.
- Consider the compatibility and integration requirements of the heat exchanger with these interfaces.
Safety and environmental considerations:
- Consider safety regulations and standards related to the design, operation, and maintenance of the heat exchanger.
- Assess any potential environmental impacts or concerns associated with the heat exchanger’s operation.
The delivery of this phase is a comprehensive document or specification that captures the project scope and requirements. This document may be referred to as the “Heat Exchanger Design Brief” It serves as a reference for the subsequent design and fabrication steps, ensuring that the heat exchanger meets the intended objectives, performance criteria, and regulatory requirements. The document should clearly outline the project goals, performance parameters, operating conditions, interface requirements, and any specific safety or environmental considerations.
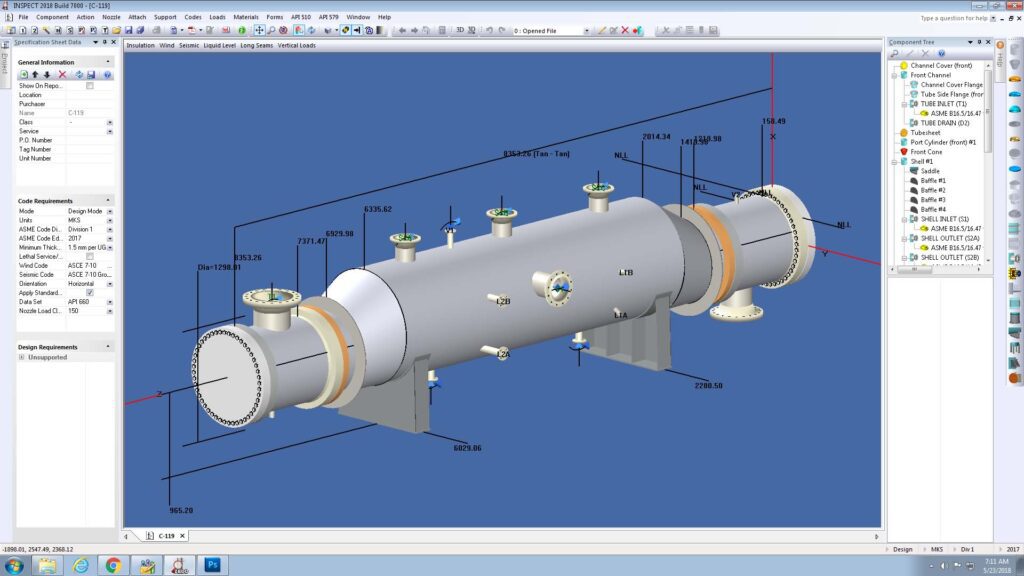
Preliminary design phase
Preliminary Design phase is a set of specifications and preliminary drawings that define the basic parameters and dimensions of the shell and tube heat exchanger.
This includes:
- Heat exchanger Type: The selection of shell and tube as the heat exchanger type.
- Number of Tubes and Tube dimensions: The determination of the number of tubes required for the heat transfer process and the preliminary selection of tube diameter and length based on the heat transfer requirements and space constraints.
- Shell dimensions: The preliminary determination of the shell diameter and length based on the overall size and dimensions required for the heat exchanger.
- Overall size and dimensions: An estimation of the heat exchanger’s overall size, shape, and dimensions based on the initial design considerations.
The deliverables at this stage may also include some preliminary sketches or diagrams that illustrate the proposed design concept. These specifications and preliminary drawings serve as a foundation for further detailed design and analysis in subsequent steps.
The specific name of the document that mentions the preliminary design details can vary depending on the company or organization’s internal documentation practices. However, it is common to refer to this document as the “Preliminary Design Report” or “Preliminary Design Specification.” These documents typically outline the design decisions made during the preliminary design phase and provide a comprehensive overview of the heat exchanger’s basic parameters and dimensions.
The Preliminary Design Report may include sections such as:
- Introduction: Provides an overview of the project and the purpose of the heat exchanger.
- Design requirements: Summarizes the performance requirements, operating conditions, and specifications that guided the preliminary design.
- Design Approach: Describes the selected heat exchanger type (shell and tube) and the reasoning behind the choice.
- Tube and shell parameters: Presents the number of tubes, tube dimensions (diameter and length), and shell dimensions (diameter and length) determined during the preliminary design phase.
- Overall size and dimensions: Provides an estimation of the heat exchanger’s overall size, shape, and dimensions.
- Preliminary sketches or diagrams: Includes any preliminary drawings or sketches that help illustrate the proposed design concept.
Thermal design
Thermal Design phase is a set of calculations, data, and design parameters that determine the required surface area and effectiveness of the shell and tube heat exchanger. The main deliverables at this stage include:
- Heat duty calculation: The calculation of the heat transfer rate (heat duty) based on the temperature difference between the hot and cold fluids and their respective flow rates.
- Surface Area calculation: Using appropriate heat transfer correlations and calculations, the determination of the required surface area for effective heat transfer. This involves considering factors such as heat transfer coefficients, fouling factors, and log mean temperature difference (LMTD).
- Heat exchanger effectiveness and Number of Transfer units (NTu): The calculation of the heat exchanger effectiveness and the number of transfer units (NTU) to evaluate the heat exchanger’s performance and optimize the design.
The Number of Transfer Units (NTU) is a dimensionless parameter used in the thermal design of heat exchangers. It quantifies the effectiveness of heat transfer between two fluid streams in a heat exchanger. NTU is defined as the ratio of the heat transfer surface area to the product of the mass flow rate and specific heat capacity rate of one of the fluids involved.
Mathematically, NTU is expressed as: NTU = (UA) / (Cmin)
NTU: Number of Transfer Units
UA: Overall heat transfer coefficient multiplied by the heat transfer surface area.
Cmin: Minimum specific heat capacity rate of the two fluid streams (the fluid with the lower specific heat capacity rate)
The NTU value provides insight into the efficiency of heat transfer in the heat exchanger. A higher NTU value indicates a higher level of heat transfer and better performance. Conversely, a lower NTU value implies lower heat transfer efficiency.
The NTU value is often used in conjunction with the heat exchanger effectiveness (ε) to evaluate and optimize heat exchanger designs. The effectiveness is a measure of how effectively the heat exchanger transfers heat between the fluids and is related to the NTU as:
ε = (1 – exp (-NTU (1 – Cr))) / (1 – Cr * exp (-NTU (1 – Cr)))
where:
ε: Heat exchanger effectiveness
Cr: Capacity rate ratio of the two fluid streams (Cmin / Cmax, where Cmax is the maximum specific heat capacity rate)
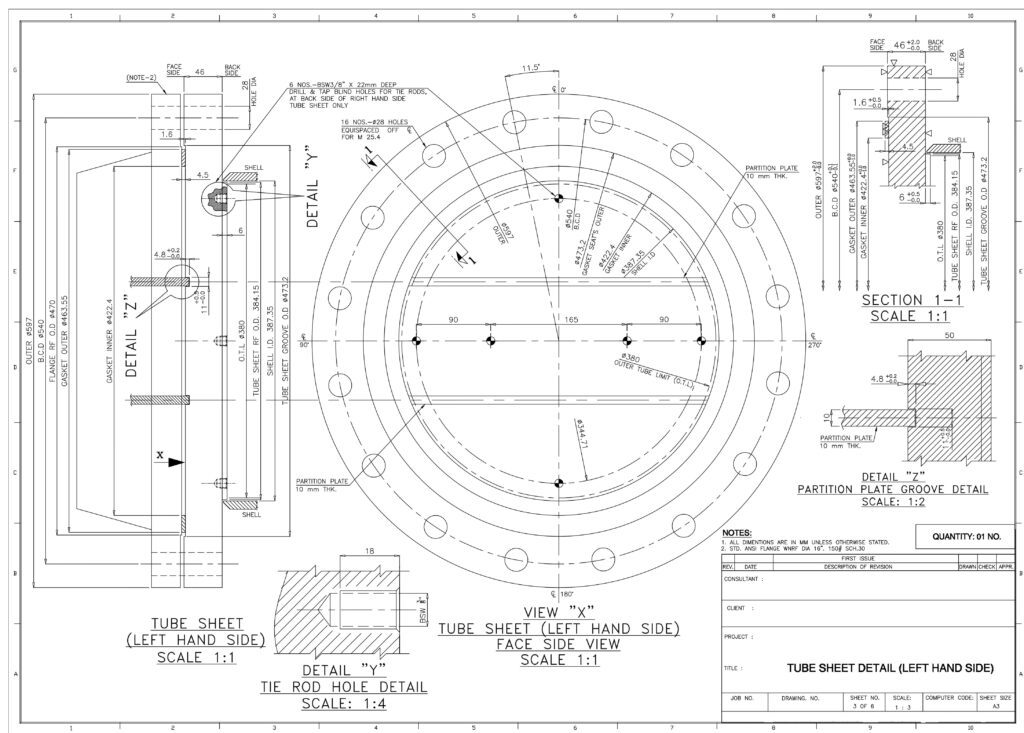
By calculating the NTU and effectiveness, engineers can assess the heat exchanger’s performance, determine the required surface area, and make design decisions to optimize heat transfer efficiency.
- Thermal efficiency Analysis: Assessing the thermal efficiency of the heat exchanger design and adjusting if necessary to achieve desired performance.
- Heat exchanger sizing and performance specifications: Establishing specific sizing parameters, such as tube length, tube diameter, and overall dimensions, based on thermal design calculations.
- Heat Transfer Analysis: Detailed analysis of the heat transfer mechanisms and performance within the heat exchanger, including temperature profiles and fluid flow patterns.
The deliverables of the Thermal Design phase are crucial in determining the required specifications and parameters for achieving the desired heat transfer performance in the shell and tube heat exchanger. These calculations and analyses serve as a basis for the subsequent mechanical design and detailed engineering of the heat exchanger.
The specific name of this document is the “Thermal Design Report” or “Thermal Design Calculation Sheet.” These documents typically outline the calculations, methodologies, and results of the thermal design phase for the shell and tube heat exchanger.
The Thermal Design Report may include sections such as:
- Introduction: Provides an overview of the project and the purpose of the thermal design.
- Design requirements: Summarizes the heat transfer requirements, operating conditions, and specifications that guided the thermal design calculations.
- Heat duty calculation: Presents the calculations and methodology used to determine the heat transfer rate (heat duty) based on the temperature difference between the hot and cold fluids and their respective flow rates.
- Surface Area calculation: Describes the heat transfer correlations, equations, and calculations employed to determine the required surface area for effective heat transfer, considering factors such as heat transfer coefficients, fouling factors, and LMTD.
- Heat exchanger effectiveness and NTu calculation: Outlines the methodology and calculations used to determine the heat exchanger effectiveness and the number of transfer units
(NTU) for evaluating the heat exchanger’s performance. - Thermal efficiency Analysis: Provides an analysis of the thermal efficiency of the heat exchanger design and any adjustments made to optimize its performance.
- Sizing and performance specifications: Presents the specific sizing parameters, such as tube length, tube diameter, and overall dimensions, derived from the thermal design calculations.
- Heat Transfer Analysis: Includes detailed analysis of the heat transfer mechanisms, temperature profiles, and fluid flow patterns within the heat exchanger.
Remember, the specific name and structure of the document can vary across organizations, but the content encompasses thermal design details and serves as a reference for further design iterations and analysis.
Mechanical design
The deliverable in this phase is typically a detailed mechanical design of the shell and tube heat exchanger, which includes various calculations, drawings, and specifications. The main deliverables at this stage include:
- Tube layout: The detailed layout of tubes within the heat exchanger, including the number of tube passes, arrangement, and pitch.
- Baffle design: The design of baffles that enhance heat transfer by promoting fluid turbulence and directing flow through the tubes.
- Structural design: Calculations and specifications related to the structural integrity of the heat exchanger, including tube supports, tie rods, and tube sheets.
- Material selection: Specifications regarding the selection of materials for tubes, shell, baffles, and other components based on factors such as process conditions and corrosion considerations.
- Expansion and contraction Analysis: Considerations for thermal expansion and contraction of the tubes due to temperature variations, including allowances and support mechanisms.
- Welding requirements: Specifications for welding procedures, welding types, and quality standards to ensure proper joining of components.
- Tolerance and surface finish specifications: Specifications for tolerances, surface finishes, and dimensional requirements for various components of the heat exchanger.
- Manufacturing drawings: Detailed engineering drawings that provide manufacturing instructions, including part drawings, assembly drawings, and fabrication details.
The document that consolidates these mechanical design details can be called the “Mechanical Design Report,” “Mechanical Design Specification,” or “Engineering Design Package.” It serves as a comprehensive reference for the mechanical design phase of the shell and tube heat exchanger and provides guidance for the fabrication and construction stages.
Summary
In Part 1 of this comprehensive guide, we explored the crucial initial steps in designing and fabricating a shell and tube heat exchanger. From defining requirements and specifications to the preliminary design, thermal design, and mechanical design phases, we covered the essential aspects of a successful design workflow. By following these principles and best practices, designers can establish a strong foundation for their heat exchanger projects. In Part 2, we will continue our journey, exploring the remaining steps, including flow and pressure drop analysis, detailed design and drawings, fabrication and quality assurance, and installation and commissioning. Stay tuned for the next installment, where we will unlock further insights into the art of heat exchanger design and fabrication.
About the author
Muhammad Rehan is a Mechanical Engineer in petrochemical industry. He has twelve years of experience in engineering, reliability, construction, commissioning and inspection management of pressure equipment, piping systems, fired heaters, and heat exchangers.
About this Featured Story
This Featured Story was first published in Heat Exchanger World Magazine in October 2023. To read more Featured Stories and many other articles, subscribe to our print magazine.
Featured Stories are regularly shared with our Heat Exchanger World community. Join us and share your own Featured Story on Heat Exchanger World online and in print.