Lida Faramarzi and Rickard Nikander at Alleima headquarters.
Over the course of their 162-year history, Alleima has established itself as a stronghold in manufacturing of high value-added tubes in advanced stainless steels and special alloys. Focused on their customers’ needs and genuine care for the future of the planet, the company stays one step ahead by perfecting their solutions while keeping them as sustainable as possible.
Founded in 1862 in Sweden, Alleima has carved a niche in manufacturing of superior quality products using advanced stainless steel and special alloys. The company’s range of materials includes duplex grades, high nickel and high temperature grades, titanium, and zirconium for advanced processes and applications in the most demanding industries. Staying true to their origins, Alleima’s headquarters remain in Sweden, but their global presence has reached 80 countries with approximately 6,500 employees.
Provided by the insight from Barinder J S Ghai, Director Technical Marketing and New Business Development, Rickard Nikander Senior Product Manager for High Temperature and Heat Exchanger Tube EMEA, and Lida Faramarzi, Product Specialist Application Tubing EMEA, we explored the company’s promising future, showcasing its impressive range of technical expertise and capabilities, and its proficiency in tackling a wide spectrum of material-related issues.
Extensive product range
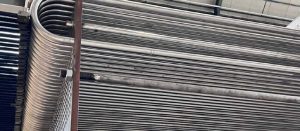
With over 900 advanced grades recipes, one can’t help but marvel at the versatility embedded within Alleima’s HX tube portfolio. Whether it’s the imperial and metric sizes ranging from 12 mm to 40 mm in diameter or the customizable lengths up to an impressive 30 meters, the company has tailored its products to cater to an extensive range of specifications. This adaptability is further exemplified by their U-bent tubes, designed for applications where straight tubes might fall short, ensuring a precise fit for every unique customer requirement.
Alleima’s pioneering spirit is evident in their material development as well. The introduction of Sanicro® 35 and SAF™ 3006 is a game-changer in this sector. Sanicro® 35 stands out by bridging the gap between cost and performance of conventional stainless steel and expensive nickel alloys, while SAF 3006 is uniquely tailored to withstand the harsh conditions of acidic and caustic environments.
These strides in material science and engineering ensure that Alleima’s heat exchanger tubes are not only capable of withstanding extreme conditions but also significantly reduce life-cycle costs.
Prioritizing quality
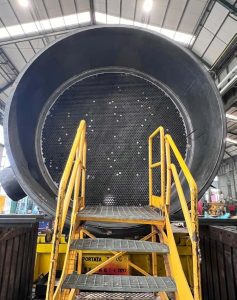
Through a meticulous and thorough approach, Alleima collaborates with clients to evaluate their unique needs. Barinder Ghai explains, “Our process is we send a checklist to the customer, asking them for the process conditions. We then review it to suggest the next best alternative. Our goal isn’t to sell the highest priced grade, it’s to find the right fit for any given case.” Alleima thus ensures that clients receive the most suitable material for their heat exchangers, reducing frequent breakdowns and cutting down repair costs, production losses, and potential contamination issues in the long run.
Choosing the right material for heat exchanger applications is crucial for optimizing performance and cost-efficiency. Different materials offer varying degrees of resistance to corrosion, temperature, and pressure, which can significantly affect the lifespan and reliability of the equipment. Alleima’s comprehensive evaluation process involves understanding the specific environmental conditions, such as temperature fluctuations, acidity levels, and potential contaminants that the heat exchanger will encounter. By tailoring material recommendations to these precise conditions, Alleima helps clients avoid common pitfalls like premature aging, stress corrosion, or metal fatigue.
For instance, in processes involving high chloride concentrations, materials like Sanicro® 28 provide superior performance due to their enhanced corrosion resistance. Conversely, if a process requires a high resistance to pitting and crevice corrosion, a different alloy might be more appropriate. The focus is always on ensuring the longevity and efficiency of the heat exchangers, thus maximizing return on investment.
Barinder highlights “Sanicro® 28 is the most widely used metallic material for evaporator tubes in the manufacture of phosphoric acid by the “wet “ method. Several units have now been in service for more than 10 years. The graphite heat exchangers, replaced by Sanicro® 28, often had repeated problems with broken tubes and loss of production.”
Recognized sustainability efforts
In a remarkable testament to their dedication to sustainability, Alleima has received a gold medal from EcoVadis, an organization that rates companies on their sustainability efforts. This places Alleima in the top 5% of more than 130,000 companies worldwide that were evaluated.
EcoVadis’ ratings are based on detailed sustainability standards and reviewed by experts from around the world. Alleima is thrilled with the upgrade from last year’s silver to this year’s gold, seeing it as a strong sign that the company’s sustainability practices aren’t only effective but also continue to improve.
Alleima also uses the EcoVadis rating to check the sustainability of their suppliers, ensuring their customers get the same high standard. With about 80% of their operations using recycled steel and European production units have run on 100% fossil-free electricity for many years, and globally, this figure is 96%, Alleima keeps their carbon footprint low. They also work hard to reduce their environmental and social impacts by using less water, managing chemicals safely, and making the most of by-products.
Alleima scores very high in the following specific EcoVadis areas: top 2% for basic iron and steel manufacturing, top 1% for sustainable sourcing, top 8% in environment and ethics, and top 11% in labor and human rights.
Biofuel and future of the energy
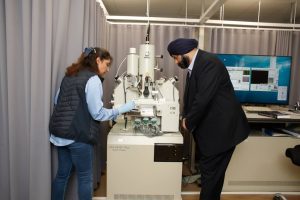
As one of the major steps in staying ahead of sustainability trends, Alleima is taking significant strides in the biofuel sector with the goal of eventually achieving net zero emissions. Barinder emphasizes “While we’ve started the journey towards net zero emissions, it’s still early days, with biofuel playing a crucial role in the reduction of our carbon footprint.”
Biofuel represents a transition from fossil to renewable feedstock, such as corn, tall oil, animal fat, etc. Despite being more costly than traditional fuels, biofuels significantly reduce CO2 emissions – up to 80%. It’s a major change that requires significant investment and strategy to continue.
The airline industry is particularly focused on sustainable aviation fuel (SAF), with many companies starting to adopt it. This involves converting the sustainable feedstocks into hydrocarbons comparable to those produced by fossil fuels. This process requires considerable treatment and significant work in refineries, including units for pre-treating feedstock and hydrocarbon units for producing the final product.
Alleima’s contribution to the biofuels sector includes advanced solutions like the aforementioned Sanicro®35, a cost-effective alternative for renewable processes which helps avoid corrosion challenges in bio-refineries. The company’s expertise in manufacturing superior quality materials for the biofuel industry aids in enhancing productivity and energy efficiency while minimizing environmental impact.
Despite all these advancements in the biofuel sector, Barinder points out that the strategy and funding part of the net zero journey still need to be addressed: “Although it’s a challenging journey, Alleima is committed to paving the way towards a sustainable future with our focus on biofuels.”
Moreover, Alleima prioritizes its function as a circular economy entity. As Barinder explains “Linear economy says ‘create, use, and throw away’, but circular economy says ‘create, use, recover, recycle, and reuse.’ This is exactly what we do with our steel and we always recover our scrap.”
Life Cycle Assessment
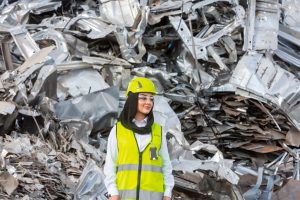
“Life Cycle Assessment, or LCA, is an essential tool in measuring the environmental impact of products,” explains Barinder. “The process analyzes all stages of a product’s life—from the extraction of the raw material, through the manufacturing process, right up to commercialization.”
The carbon footprint is calculated over the Cradle-to-Gate approach. This involves assessing greenhouse gas emissions from raw material gathering, material processing, and finally, product manufacturing. In this way, the company’s customers are empowered to make more environmentally conscious decisions and are equipped to calculate the carbon footprint of their products.
Barinder further underscores the role of LCA in his company’s operation. “By drilling down into specific product grades, like any given steel grade, we can map out their exact CO2 emissions,” he explains. This rigorous and transparent analysis of production data not only helps reduce the carbon footprint but also allows more informed communication with clients.
Express hollows
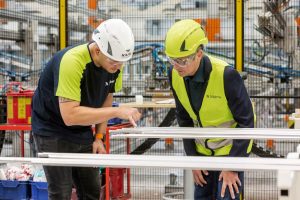
Rickard Nikander shares insights into Alleima’s unique express service program for heat exchanger tubes within the EMEA region. This game-changing service guarantees a quick 8-week turnaround for heat exchanger tubes, a vital component in large, complex refineries. “Heat exchanger tubes may only be a small part of a large and complex refinery, but when they fail unexpectedly it can force a shutdown and a significant loss of income,” says Rickard. However, it’s important to mention that the program is limited to selected grades and a maximum order capacity of 5 tons.
Furthermore, Rickard emphasizes the world-leading quality and unsurpassed delivery speed of their heat exchanger express program. At its core, the program aims to be closer to the customer’s needs, delivering the absolute best in tubing materials technology with unparalleled speed. “Our heat exchanger express program is yet another example of our commitment to always seeking to be closer to our customers. To work out what you need before you realize it yourself. It means you can get the absolute best in tubing materials technology, with the highest quality, in only eight weeks from order placement,” says Rickard. The tubes included in the program come in extensive ranges of advanced duplex, super-duplex, austenitic, and super-austenitic materials suitable for various types of heat exchangers.
This and many other carefully tailored solutions provided by Alleima reflect the blend of innovation, quality, and customer focus that positions it at the vanguard of the heat exchanger industry.
To gain more knowledge on Alleima’s research and technical insights, you can find the company’s Barinder Ghai and Denis Ruh presenting at the ADIPEC 2024 Conference on 4-7 November in Abu Dhabi.
Alleima’s team was at Heat Exchanger World and Duplex World Conference Europe:
Angela Philipp, speaker at Duplex World: “A comparative analysis of the corrosion behaviour of the super duplex UNS S32750 and UNS S83071.”
Jonas Höwing, speaker at Heat Exchanger World: “Metallic heat exchangers for phosphoric acid evaporators.”
Dilip Chandrasekaran, speaker at Heat Exchanger World: “Electrification of heating processes – the road towards a fossil free industry.”
Barinder Ghai, moderator at Heat Exchanger World: session on Materials Selection/Corrosion and Supply Chain and Availability Issues panel discussion.
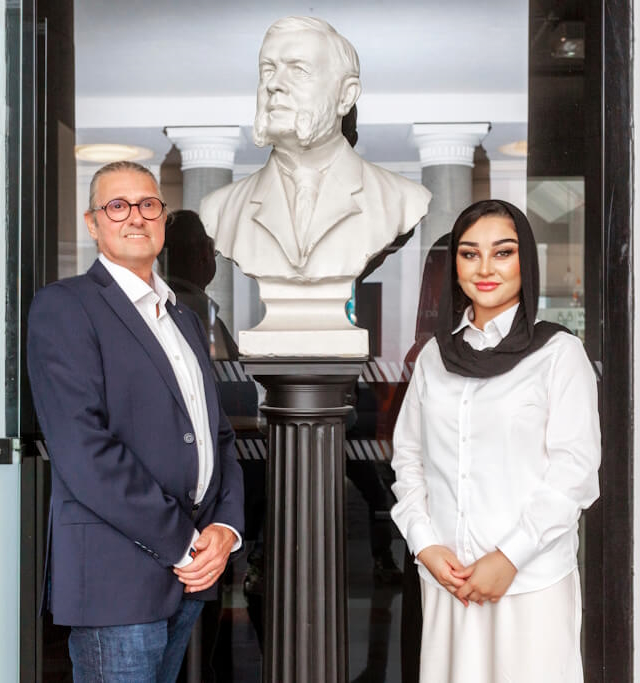
About this Featured Story
Why Subscribe?
Featured Stories are regularly shared with our Heat Exchanger World community. Join us and share your own Featured Story on Heat Exchanger World online and in print.