Heat exchangers (HEs) play a crucial role in various industrial processes by efficiently transferring heat between fluids. However, like any mechanical equipment, they are prone to certain problems that can affect their performance and reliability. In this article, we will discuss the following three common heat exchanger problems encountered in process plants and explore potential solutions to mitigate these issues:
• Vibration Issues
• HE Thermal Leakage
• HE Premature metal failure:
By Omari Hussein Sabuni – Mechanical Engineer, Kinyerezi Power Plant
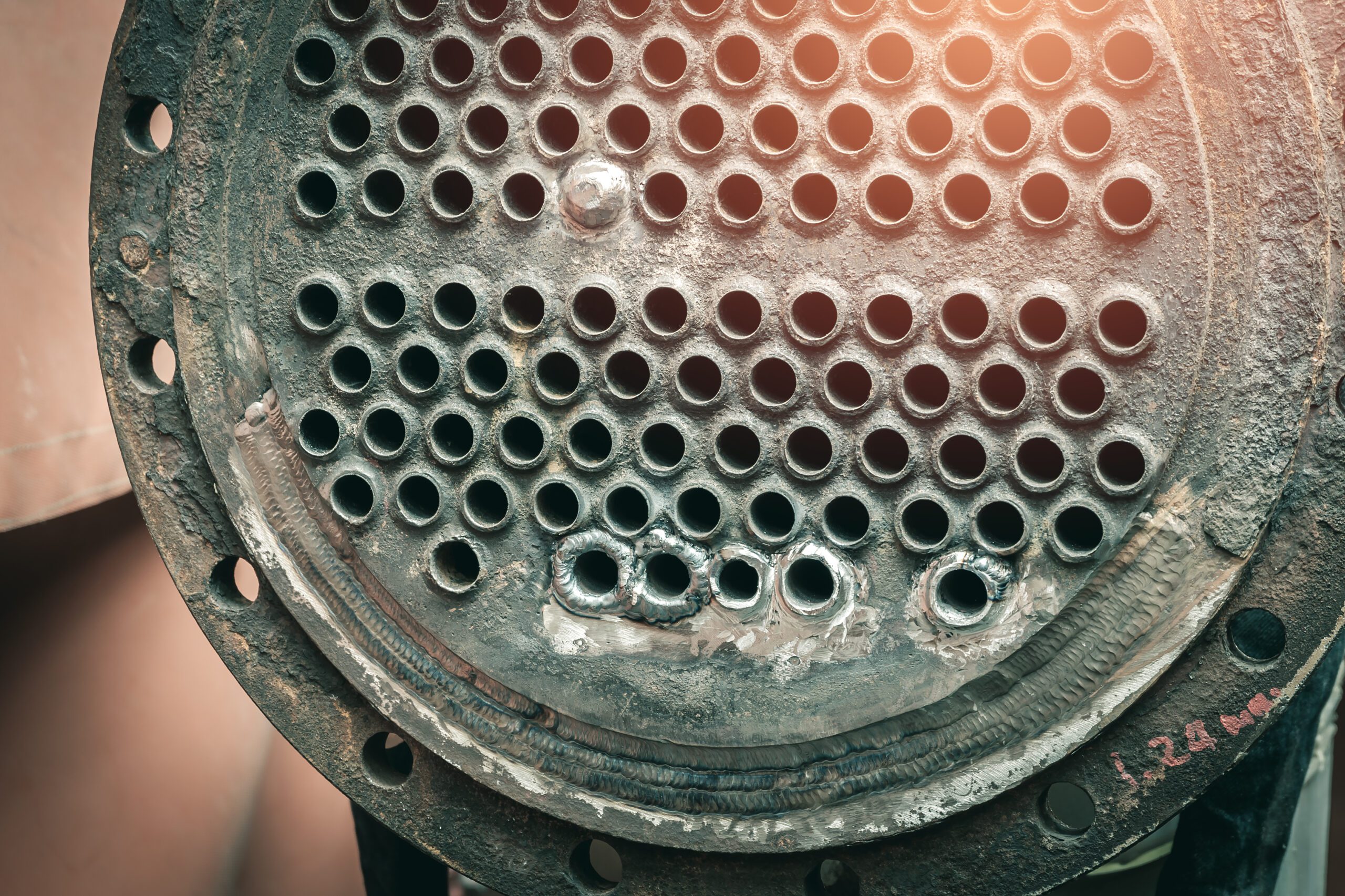
Vibration issues and their causes
Vibration is a prevalent problem in heat exchangers that can lead to severe damage if left unaddressed. It may result from various factors such as misalignment, unbalanced impellers, loose components, or excessive fluid velocity. Vibrations can cause tube fatigue, tube-to-tube sheet leaks, or even complete equipment failure.
Vibration issues in heat exchangers can arise from various causes. Some of the common factors contributing to vibration problems include:
- Misalignment: Improper alignment of the heat exchanger components, such as tubes, tube sheets, baffles, or support structures, can lead to vibrations. Misalignment can result from inadequate installation or structural changes due to thermal expansion and contraction.
- Unbalanced Rotating Parts: If the rotating components, such as impellers, fans, or motors, are not properly balanced, it can cause vibrations. Unbalanced forces can create excessive vibrations and put stress on the equipment, leading to potential failures.
- Fluid Flow Issues: High fluid velocities or turbulent flow can induce vibrations in heat exchangers. This can occur when the fluid flow exceeds the recommended design limits or when there are flow restrictions or blockages within the exchanger.
- Mechanical Looseness: Loose components, such as bolts, fasteners, or supports, can generate vibrations in heat exchangers. Mechanical looseness can result from inadequate tightening during installation, wear and tear over time, or vibrations from adjacent equipment.
- Resonance: Resonance can occur when the natural frequency of the heat exchanger matches the frequency of the external forces acting on it. This can lead to amplification of vibrations and structural damage if not addressed promptly.
- Tube-to-Tubesheet Clearance: Insufficient clearance between the tubes and tube sheets can cause vibrations. When the tubes expand or contract due to temperature changes, inadequate clearance can result in frictional forces and induce vibrations.
- Flow-Induced Vibrations: Fluid flow can induce vibrations in heat exchangers, especially in shell-and-tube designs. Flow-induced vibrations can be caused by phenomena such as vortex shedding, fluid-induced oscillations, or flow-induced turbulence.
Cost of vibration issues in heat exchangers
The cost of vibration issues in heat exchangers can vary depending on several factors, including the severity of the problem, the extent of damage caused, and the type of industry or process in which the heat exchanger is involved. Here are some potential costs associated with vibration issues:
- Equipment Repair or Replacement: Vibration problems can lead to damage or failure of various components in the heat exchanger, such as tubes, tube sheets, baffles, or supports. Repairing or replacing these components can incur significant costs, including the cost of materials, labor, and downtime for equipment shutdown.
- Production Loss: When vibration issues cause equipment failures or the need for unplanned maintenance, it can result in production downtime. The loss of production output during this period can have a direct financial impact on the plant’s profitability.
- Energy Consumption: Vibration can reduce the efficiency of heat exchangers, leading to increased energy consumption. If the heat exchanger is not operating at its optimal performance, more energy is required to achieve the desired heat transfer, resulting in higher utility costs.
- Safety Hazards: Severe vibration issues can compromise the structural integrity of the heat exchanger, potentially leading to safety hazards. If a catastrophic failure occurs, it can result in personnel injury, damage to surrounding equipment or infrastructure, and the associated costs of addressing the safety incident.
- Maintenance and Inspection Costs: Implementing a proactive maintenance and inspection program to monitor and address vibration issues requires resources and investment. Regular inspections, condition monitoring systems, and the employment of vibration experts or engineers can add to the operational costs of the heat exchanger.
How to mitigate vibration issues in heat exchangers
Here are some strategies to mitigate vibration issues:
- Proper Design and Installation: Ensure that the heat exchanger is designed and installed correctly, taking into consideration factors such as structural stability, adequate clearance for thermal expansion, and appropriate support systems. Follow industry standards and guidelines during the design and installation phases.
- Alignment and Balancing: Perform regular alignment checks to ensure that the components of the heat exchanger, such as tubes, tube sheets, baffles, and supports, are properly aligned. Balancing rotating parts, such as impellers or fans, is essential to minimize vibrations caused by unbalanced forces.
- Fluid Flow Considerations: Pay attention to fluid flow rates and velocities within the heat exchanger. Ensure that the flow rates are within the design limits and avoid excessive fluid velocities that can induce vibrations. Consider the use of flow straighteners or other flow control devices to mitigate turbulence and flow-related vibrations.
- Regular Inspections and Maintenance: Implement a comprehensive inspection and maintenance program to detect and address vibration issues early on. Regularly check for loose components, worn-out parts, or signs of damage. Schedule periodic inspections, including vibration analysis, to monitor the condition of the heat exchanger and identify potential vibration sources
- Vibration Monitoring Systems: Install vibration monitoring systems that can detect and alert any abnormal vibrations in real-time. These systems can help identify the root cause of vibration issues and enable timely intervention before severe damage occurs. Implement predictive maintenance strategies based on vibration data analysis.
- Proper Material Selection: Select materials that have suitable mechanical properties, corrosion resistance, and temperature tolerance to withstand the operating conditions of the heat exchanger. Consider materials that are less prone to vibration-induced fatigue or corrosion.
- Training and Expertise: Ensure that personnel involved in the operation, maintenance, and inspection of heat exchangers receive adequate training on vibration-related issues. Consider involving vibration experts or consulting engineers to analyze and provide recommendations for mitigating vibration issues.
- Address Resonance: If resonance is identified as a vibration source, consider implementing design modifications or adding dampers to shift the natural frequencies away from the excitation frequencies. Analytical techniques such as finite element analysis (FEA) can help identify resonant frequencies and optimize the heat exchanger design accordingly.
Thermal leakage and its causes
Thermal leakage occurs when there is improper sealing or insulation around the heat exchanger, leading to heat losses. It can be caused by deteriorated seals, damaged insulation, or inadequate installation.
Thermal leakage in heat exchangers can occur due to several reasons. Here are some common causes of thermal leakage:
- Improper Sealing: Inadequate or improper sealing between the components of the heat exchanger, such as tube-to-tube sheet joints, header connections, or flange connections, can result in thermal leakage. Gasket failure, insufficient compression, or misalignment during installation can compromise the integrity of the seal, allowing heat to escape.
- Deteriorated Seals or Gaskets: Over time, seals and gaskets used in heat exchangers can degrade, harden, or shrink due to aging, exposure to high temperatures, or chemical interactions with the process fluid. This can lead to gaps or cracks in the seals, enabling thermal leakage.
- Tube-to-Tube Sheet Clearance: In shell-and-tube heat exchangers, improper clearance between the tubes and the tube sheet can contribute to thermal leakage. Inadequate clearance can result in bypassing of the process fluid, causing heat transfer inefficiencies and leakage.
- Tube Fouling: Fouling deposits on the inner surface of the tubes, such as scale, sediment, or biological growth, can act as insulation and reduce heat transfer efficiency. This can lead to temperature differences across the heat exchanger, causing thermal leakage.
- Erosion or Corrosion: Erosion or corrosion of the heat exchanger components, particularly the tube walls or tube sheet, can result in thinning or perforation, leading to thermal leakage. Corrosive fluids or high-velocity flows can accelerate erosion or corrosion processes.
- Insufficient Insulation: Inadequate or deteriorated insulation around the heat exchanger can allow heat to escape into the surroundings. This can result in reduced thermal efficiency and wasted energy.
- Poor Design or Construction: In some cases, thermal leakage can be attributed to poor design or construction practices. This includes improper sizing of the heat exchanger, inadequate consideration of thermal expansion and contraction, or insufficient attention to sealing details during fabrication.
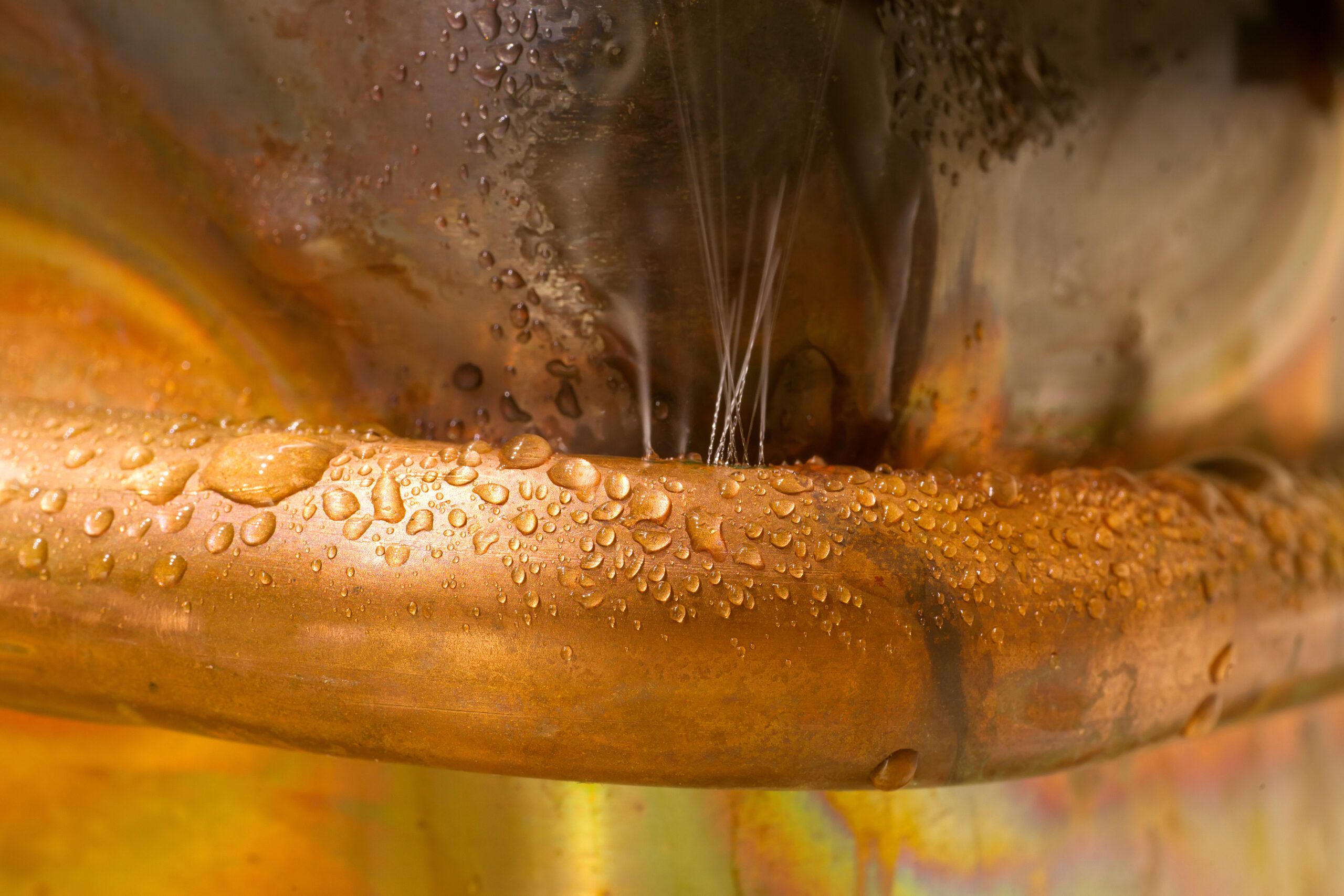
Cost of thermal leakage
The cost of thermal leakage in a heat exchanger can vary depending on several factors, including the severity of the leakage, the size and type of the heat exchanger, the operating conditions, and the specific industry in which it is used. Here are some potential costs associated with thermal leakage:
- Energy Loss: Thermal leakage results in reduced heat transfer efficiency, leading to wasted energy. The increased energy consumption can result in higher utility costs and operational expenses.
- Reduced Performance: Thermal leakage can compromise the overall performance of the heat exchanger. This can result in decreased process efficiency, reduced productivity, or lower product quality, depending on the specific application.
- Downtime and Production Loss: If the thermal leakage becomes severe and requires repairs or replacement, it may lead to downtime and production loss. The heat exchanger may need to be taken offline for repairs, impacting the plant’s productivity and potentially causing delays in production schedules.
- Maintenance and Repair Expenses: Addressing thermal leakage issues may involve maintenance or repair activities, such as sealing replacement, gasket replacement, tube repairs, or tube sheet repairs. These activities can incur costs related to labour, materials, and any necessary equipment.
- Contamination and Product Loss: Depending on the application, thermal leakage can result in contamination of the process fluid or loss of product. Contaminated or compromised products may need to be discarded, resulting in financial losses.
- Safety Concerns: Thermal leakage can pose safety hazards, particularly if the leaked fluid is hazardous or flammable. The costs associated with addressing safety incidents, conducting investigations, and implementing safety measures can be significant.
- Environmental Impact: Thermal leakage can lead to environmental concerns if the leaked fluid is harmful to the environment. The costs may include cleanup, remediation, and compliance with environmental regulations.
How to mitigate thermal leakage
Here are some strategies to mitigate thermal leakage:
- Sealing and Gasket Maintenance: Ensure that the seals and gaskets used in the heat exchanger are of high quality and compatible with the operating conditions. Regularly inspect and replace seals or gaskets as needed to maintain an effective seal and prevent thermal leakage.
- Proper Installation and Alignment: During the installation of the heat exchanger, ensure proper alignment of components and tightness of connections. Follow manufacturer guidelines and specifications to achieve effective sealing and prevent gaps that can lead to thermal leakage.
- Tube Clearances and Support: Properly maintain tube-to-tube sheet clearances to prevent bypassing of the process fluid and ensure efficient heat transfer. Inadequate clearances can lead to temperature differences and thermal leakage. Additionally, provide adequate support for the tubes to minimize stress and prevent movement that could compromise the seals.
- Regular Inspection and Maintenance: Establish a comprehensive inspection and maintenance program to detect and address thermal leakage issues promptly. Regularly inspect the heat exchanger for signs of degradation, erosion, corrosion, or damage. Clean tubes regularly to prevent fouling that can hinder heat transfer and contribute to thermal leakage.
- Insulation: Ensure that the heat exchanger is properly insulated to minimize heat loss. Inspect the insulation regularly for damage or deterioration and repair or replace as necessary. Effective insulation reduces thermal gradients and helps maintain optimal heat transfer efficiency.
- Thermal Expansion Considerations: Account for thermal expansion and contraction during the design and installation of the heat exchanger. Use appropriate expansion joints, flexible connections, or clearance gaps to accommodate thermal movements and prevent stress on seals and connections.
- Regular Performance Monitoring: Implement a monitoring system to track the performance of the heat exchanger. Monitor key parameters such as temperature differentials, pressure drops, and energy consumption to identify any deviations or signs of thermal leakage. This allows for timely corrective actions before the issue becomes severe.
By implementing these mitigation strategies, thermal leakage in heat exchangers can be minimized, leading to improved energy efficiency, enhanced performance, and reduced operational risks.
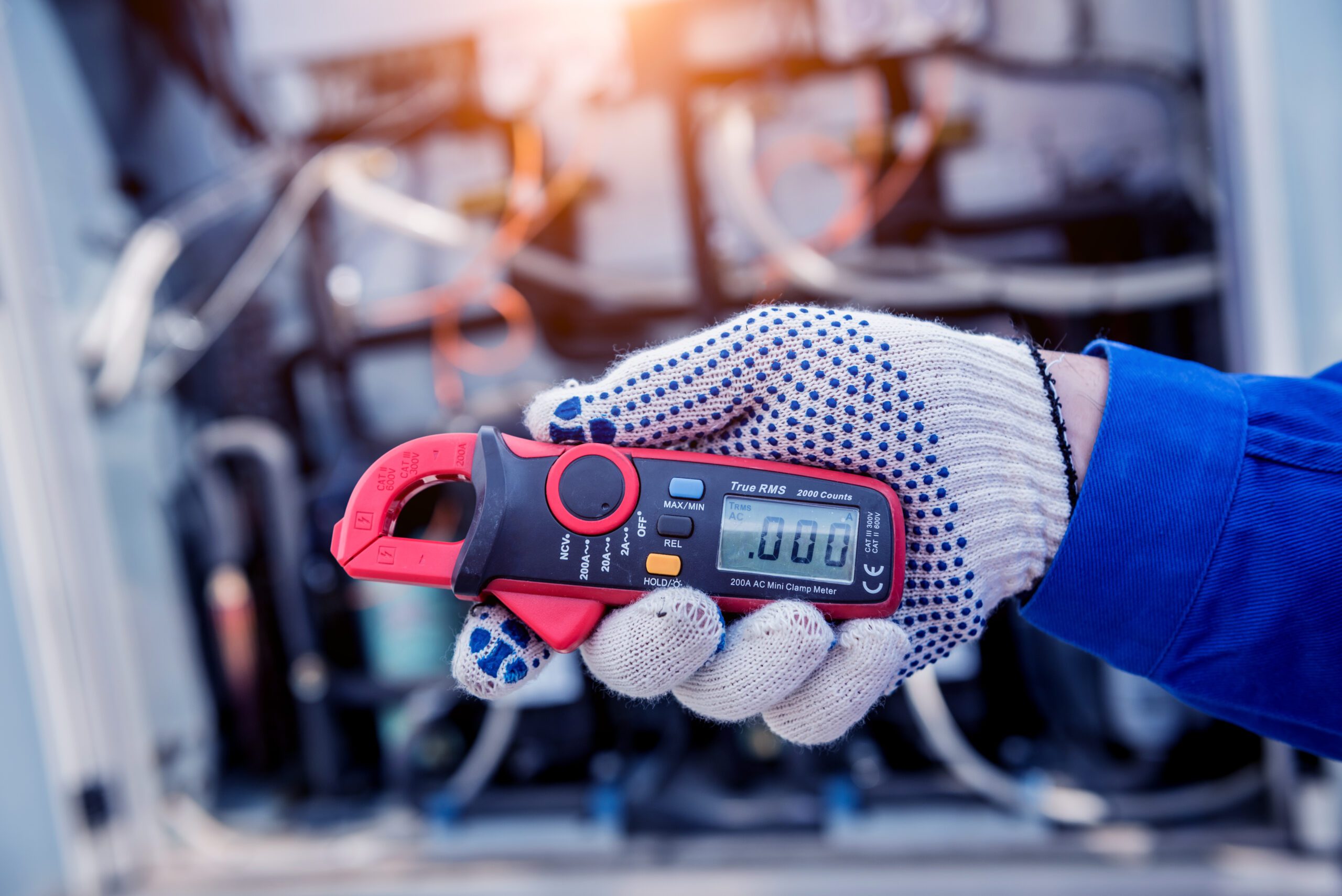
Premature metal failure and its causes
Heat exchangers are exposed to extreme temperature differentials and corrosive environments, making them susceptible to premature metal failure. This can result in cracks, fractures, or complete equipment breakdown. Premature metal failure in heat exchangers can occur due to several factors, including:
- Corrosion: Corrosion is one of the primary causes of metal failure in heat exchangers. It can be caused by chemical reactions between the metal surfaces and the process fluid, leading to the degradation of the metal over time. Corrosion can be accelerated by factors such as high temperatures, aggressive fluids, improper material selection, or inadequate corrosion protection measures.
- Erosion: Erosion occurs when the flow of fluid within the heat exchanger causes the metal surfaces to wear away over time. This can be particularly problematic when the fluid contains abrasive particles or experiences high-velocity flow. Erosion can weaken the metal, leading to premature failure.
- Thermal Stress: Heat exchangers are exposed to significant temperature variations during operation, resulting in thermal stress. Rapid and repeated changes in temperature can cause expansion and contraction of the metal, leading to stress concentrations and potential failure points. If the metal is not designed or supported adequately to withstand thermal stress, it can result in premature metal failure.
- Fatigue: Fatigue failure occurs when the metal undergoes repeated cyclic loading or stress over an extended period. The cyclic stress can lead to microcracks or fissures in the metal, which gradually propagate and eventually cause failure. Factors contributing to fatigue include vibration, thermal cycling, pressure fluctuations, or inadequate design considerations.
- Creep: Creep is the gradual deformation of metal under constant stress at high temperatures. Heat exchangers operating at elevated temperatures for extended periods can experience creep, causing the metal to elongate or deform. Creep can lead to changes in dimensional stability and structural integrity, resulting in premature metal failure.
- Material Incompatibility: The selection of incompatible materials for construction or for contact with specific process fluids can lead to metal failure. Incompatibility can result in chemical reactions, galvanic corrosion, or other forms of degradation, weakening the metal and reducing its lifespan.
- Mechanical Damage: Mechanical damage, such as impacts, excessive vibration, or improper handling during installation or maintenance, can introduce localized stress concentrations or structural defects in the metal. These defects can act as initiation points for failure and reduce the overall strength of the heat exchanger.
Cost of premature metal failure in heat exchangers
The cost of premature metal failure in a heat exchanger can vary depending on several factors, including the severity of the failure, the size and type of the heat exchanger, the operating conditions, and the specific industry in which it is used. Here are some potential costs associated with premature metal failure:
- Replacement or Repair Costs: If the metal failure is severe, it may require the replacement of the entire heat exchanger or significant repair work. This can involve substantial costs related to purchasing a new heat exchanger, installing it, or repairing the damaged components.
- Downtime and Production Loss: Metal failure often leads to the need for unplanned maintenance or repairs, resulting in downtime. The heat exchanger may need to be taken offline, disrupting the production process and causing delays. Downtime can result in lost productivity, missed production targets, and potential financial penalties for contract non-compliance.
- Equipment Inspection and Assessment: Following a metal failure, it may be necessary to conduct thorough inspections and assessments to determine the root cause, extent of the damage, and required corrective actions. This can involve hiring specialized technicians, conducting non-destructive testing, or engaging engineering consultants, which can incur additional costs.
- Safety and Environmental Impact: Depending on the nature of the metal failure, safety incidents or environmental concerns may arise. The associated costs may include investigation expenses, implementation of safety measures, cleanup and remediation efforts, and potential fines or penalties for non-compliance with safety or environmental regulations.
- Loss of Productivity and Efficiency: Metal failure can impact the overall performance and efficiency of the heat exchanger, leading to reduced heat transfer efficiency, lower process yields, or increased energy consumption. These factors can result in decreased productivity, higher operating costs, and reduced profitability.
- Secondary Equipment Damage: Metal failure in a heat exchanger can potentially cause damage to other interconnected equipment or components, such as pipes, valves, or pumps. Repairing or replacing these additional components can add to the overall cost of the failure.
- Reputation and Customer Impact: Premature metal failure incidents can negatively impact a company’s reputation and customer perception. Customers may lose confidence in the reliability of the products or services provided, leading to potential customer dissatisfaction, contract cancellations, or difficulties in attracting new customers.
How to mitigate premature metal failure in heat exchangers
Here are some strategies to mitigate the risk of premature metal failure:
- Material Selection: Choose materials that are appropriate for the specific operating conditions, including temperature, pressure, and fluid composition. Consider factors such as corrosion resistance, erosion resistance, and compatibility with process fluids to ensure the longevity of the heat exchanger.
- Corrosion Protection: Implement corrosion protection measures such as coatings, inhibitors, or cathodic protection to prevent or minimize corrosion damage to the metal surfaces. Regularly inspect and maintain the corrosion protection system to ensure its effectiveness.
- Proper Design and Engineering: Ensure that the heat exchanger is properly designed and engineered, considering factors such as thermal stress, fluid dynamics, mechanical loadings, and anticipated operating conditions. Account for factors like expansion and contraction, stress concentrations, and fluid flow velocities during the design phase.
- Adequate Support and Anchoring: Provide proper support and anchoring mechanisms to minimize stress concentrations and prevent excessive movement of the heat exchanger components. This helps to reduce the risk of fatigue failure and structural damage.
- Regular Inspection and Maintenance: Establish a comprehensive inspection and maintenance program to detect early signs of metal degradation or failure. Regularly inspect the heat exchanger for corrosion, erosion, fatigue cracks, or other forms of damage. Implement preventive maintenance practices, such as cleaning, repair, and replacement of damaged components, to address issues before they escalate.
- Monitoring and Condition Assessment: Implement monitoring systems to track key parameters such as temperature, pressure, flow rates, and vibration levels. Regularly analyze the data to identify any deviations or trends that may indicate potential metal failure. Conduct condition assessments periodically to evaluate the overall health of the heat exchanger and identify potential risks.
- Training and Expertise: Ensure that personnel involved in the operation, maintenance, and inspection of heat exchangers receive proper training on metal failure prevention and detection. Consider involving experts or consultants with specialized knowledge in heat exchanger design, materials, and maintenance to provide guidance and support.
- Corrective Actions and Repairs: Promptly address any identified issues or signs of metal degradation through appropriate corrective actions. This may include repairing or replacing damaged components, applying protective coatings, implementing corrosion control measures, or adjusting operating parameters to reduce stress on the metal surfaces.
- Performance Evaluation and Improvement: Continuously evaluate the performance of the heat exchanger and identify areas for improvement. Monitor and analyze operational data to optimize heat transfer efficiency, reduce stress on the metal, and extend the lifespan of the equipment. Implement necessary modifications or upgrades based on operational experience and industry best practices.
Conclusion
Heat exchangers are integral components of process plants, but they are susceptible to several problems that can impact their performance and efficiency. By implementing regular inspection, preventive maintenance, and proper design considerations heat exchanger performance can be optimised and the need for costly downtime and repairs reduced.
About the author
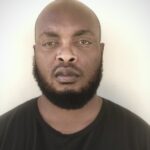
Omari Hussein Sabuni is an experienced mechanical engineer at Kinyerezi Gas Power Plant, specializing in heat exchanger design, optimization, troubleshooting and providing practical solutions for various heat exchanger problems. He is skilled in analyzing thermal systems and developing innovative solutions to enhance heat transfer efficiency and adept at conducting feasibility studies, performing risk assessments, and ensuring compliance with industry standards.