Following a customer’s request, the Ekin Endustriyel Team was tasked with providing a specific heat exchanger design that would be suitable for flue gas within an electrical machinery facility. This case study highlights how the team successfully met the heat requirements of a 132 kW capacity ORC system by implementing an innovative energy recovery solution using a shell and tube heat exchanger.
By Enes Kuzey Er – R & D Specialist, Ekin Endustriyel
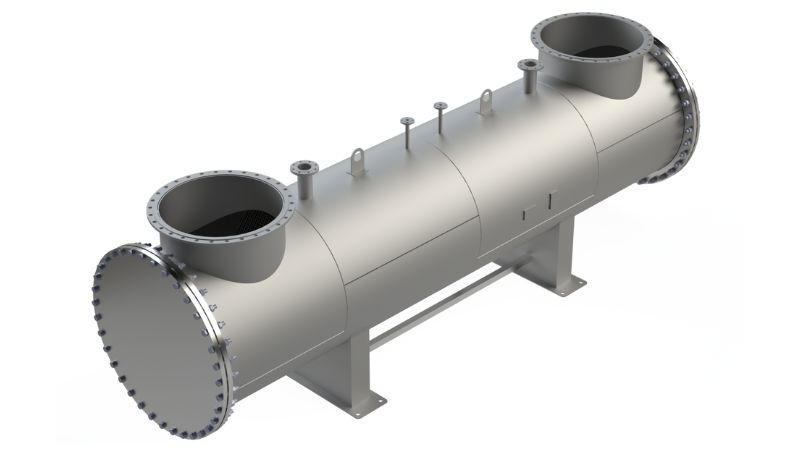
Initial task
The customer generates power through the Organic Rankine Cycle (ORC) and converts it into electricity with turbines. Thermal oil, at a temperature of 160°C, serves as the secondary fluid in the ORC process. Due to heat transfer in the process, the thermal oil loses enthalpy, resulting in a temperature decrease to 125°C. At this stage, an external heat source is required, leading to the implementation of a shell and tube heat exchanger, chosen for its compatibility with high temperatures and process fluids.
The solution
Within another section of the facility, there is a steam production line utilizing natural gas. After processing, the natural gas becomes waste flue gas at 260°C. This waste flue gas serves as the external heat source, enabling thermal energy recovery for heating the thermal oil in the ORC process. The flue gas enters the heat exchanger at 260°C and exits at 155°C after cooling. Meanwhile, the thermal oil enters at 125°C and exits at 160°C after heating. The shell and tube heat exchanger facilitates a total work of 950 kW.
Custom heat exchanger
The heat exchanger is designed according to TEMA standards as the NEN type. It features a shell diameter of 1300 mm and a total length of approximately 5500 mm. Flue gas flows through the inner tubes while thermal oil circulates within the shell. To withstand the potentially corrosive nature of the waste natural gas, all components in contact with the inner fluid are manufactured from stainless steel, while other parts of the heat exchanger are made from carbon steel. The material standards adhere to EN-10025 for the shell and EN-10216 for the inner tubes, ensuring both economic efficiency and reliability.
Results
Following heat recovery with the shell and tube heat exchanger, the heated thermal oil is sent to the ORC section, maintaining a closed continuous cycle within a combined structure. Through the utilization of this 950 kW heat recovery system, the thermal requirement of 132 kW for the ORC system is fully met.
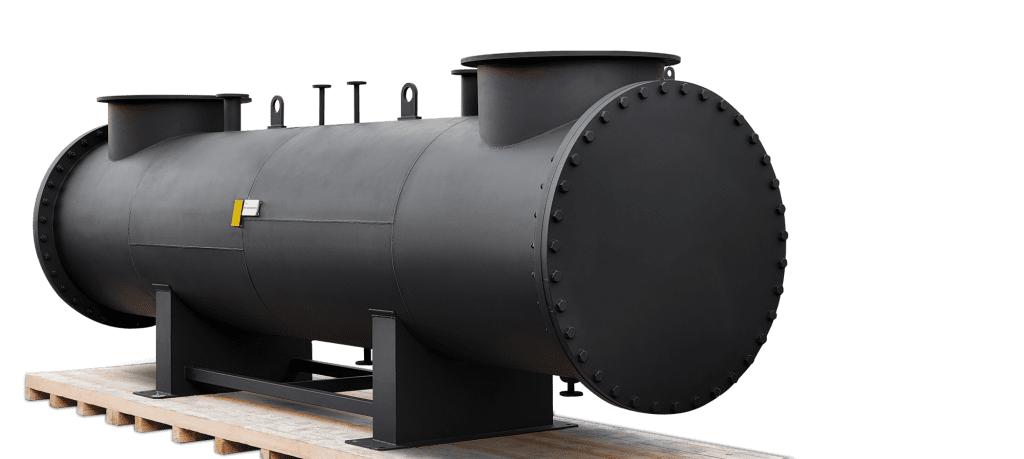
About the author
Enes Kuzey Er is the Heat Transfer Product Sales – R&D Specialist for Ekin Endustriyel, responsible for sales of heat transfer products such as plate type heat exchangers (gasketed or brazed) and shell and tube heat exchangers. He is also researching solutions for industry needs through customer feedback, and provides support for related research and development processes.
About this Technical Story
This Technical Story was first published in Heat Exchanger World Magazine in June 2024. To read more Technical Stories and many other articles, subscribe to our print magazine.
Technical Stories are regularly shared with our Heat Exchanger World community. Join us and share your own Technical Story on Heat Exchanger World online and in print.