Rarely do heat exchangers cause catastrophic events in operating plants. For that reason, they tend to get ignored; little or no proactive maintenance is done and improvements are typically not made unless they become a critical problem. But, if you look at which equipment is responsible for the most economic losses over a period of 5-10 years – process interruptions, maintenance, replacement parts – heat exchangers are always near the top of the list, especially in refining!
By Himanshu Joshi, heat exchanger specialist – Becht
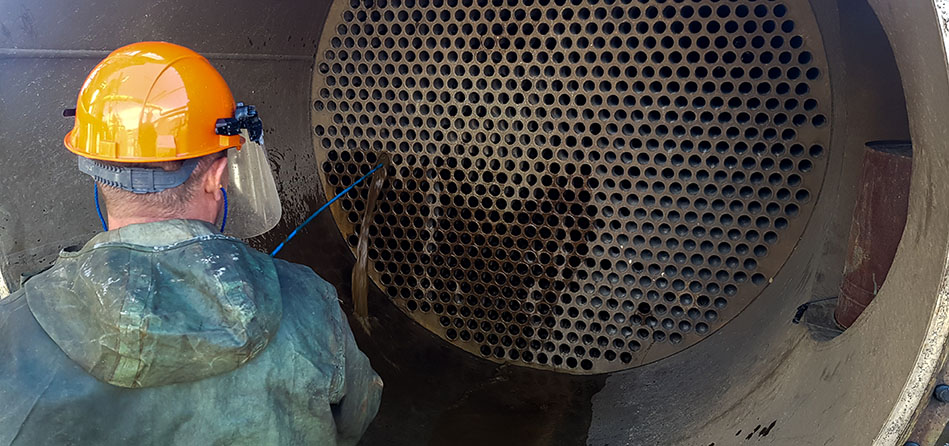
However, problems such as heat duty loss and its impact on operations, increased energy consumption, small leaks, and replacement of tube bundles go somewhat unnoticed because individually these events are not high cost, nor are they high profile safety issues.
Proactively addressing the worst actors (the ones which cause the highest losses) can have a significant impact in reducing maintenance costs and minimizing throughput related losses. Two strategies have proven to be successful.
Address heat exchangers from a reliability perspective
Keep an updated list of heat exchangers with the highest cost impact and have a plan to address the root cause of failures. Data should be available to show all maintenance costs for any heat exchanger and for process stoppages/slowdowns caused by heat exchanger failures. Using this data and adding all costs will produce a list which can be prioritized for action. In a typical operating plant about 5% of heat exchangers will fall into the category of very high impact. That list can be further shortened based on whether it is practical to take action.
Service | Shell side | Tube side | Hydroblasting Qa/Qc | Ultrasonic Qa/Qc |
CPHT | Vac Resid | Crude | 86% | 97% |
FCC Slurry | BFW | FCC Slurry | 78% | 91% |
CPHT | HGO | Crude | 62% | 100% |
CPHT | Vac Resid | Crude | 75% | 100% |
CPHT | HGO | Crude | 91% | 100% |
CPHT | HGO | Crude | 78% | 93% |
CPHT | Vac Resid | Crude | 80% | 100% |
CPHT | Vac Resid | Crude | 80% | 93% |
L/R DEA | Lean Amine | Rich Amine | 90% | 100% |
CPHT | ABPA | Crude | 92% | 98% |
CPHT | Flashed Crude | Vac Resid | 86% | 100% |
Average | 82% | 97% |
Data courtesy of Clean As New, www.cleanasnew.com
Monitor the operating performance of the most process-critical heat exchangers and those which affect energy consumption
Usually, heat exchanger performance deteriorates because of fouling, and a good monitoring method can achieve several objectives:
• Quantify the loss in heat duty and its impact,
• Identify which heat exchangers should be cleaned to get the maximum benefit,
• Evaluate the cost vs benefit of different cleaning methods,
• Identify if certain process conditions or feed compositions lead to increased fouling.
Together, these factors can be used to minimize the losses due to fouling and understand and eliminate the root causes of fouling. If root cause elimination is an objective, an additional very helpful tool is a proper deposit analysis.
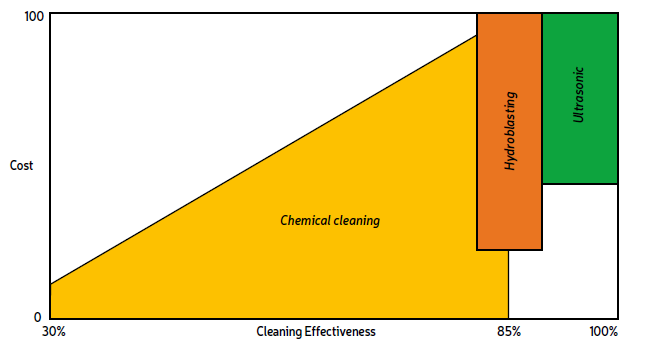
Comparison of heat exchanger cleaning methods
When a heat exchanger is cleaned, the expectation should be that it will now deliver the maximum possible heat duty. But an evaluation of most post-clean operations will show that the cleaned heat exchanger is delivering only about 85% of what should be the clean heat duty.
For critical heat exchangers which impact process performance or energy consumption, that remaining 15% could translate to large losses. To get to clean performance the foremost thing to consider is the cleaning method – is it the best, optimum, most cost-effective for a given heat exchanger? Heat exchanger specialists at Becht are able to identify the most effective cleaning method for a specific service and quantify the associated benefits.
Hydroblasting
– the use of high-pressure water jets to force fouling off both the inside and outside surfaces of tubes – this has been used as the default method for many decades. This process is labor intensive and an HSE risk unless robotic cleaning is used. Because it depends on labor, it can be low cost in some parts of the world but very high in others. The effectiveness of this method is around 85%. The low effectiveness is mostly a result of the pressure of the water jets not being able to reach deep into the shell-side, all around the tubes, and around U-bends on the inside of the tubes.
Chemical cleaning
– the circulation of water or an oil-based chemical – this is practiced throughout the industry with varying procedures and degrees of success. This method is equivalent to hydroblasting for cleaning effectiveness, but usually less effective because adequate procedures are not followed. You can expect a cleaning effectiveness anywhere between 30-85% based on the cleaning procedure. One benefit of this method is that the circulation is carried out in-situ, that is, it doesn’t require opening up the heat exchanger. Another is that multiple heat exchangers can be hooked-up to the circulation simultaneously, so the overall time and labor is reduced. With multiple heat exchangers, the cost is equivalent to hydroblasting on a per heat exchanger basis.
Thermal cleaning
– thermally decomposing organic material releasing pyrolysis gasses and leaving behind a coke-like residue – this method can be up to 100% effective, if the foulant is mostly organic. This method requires the insertion of the tube bundle into a high temperature oven. The reference below highlights the high effectiveness, safety, and low water consumption of the thermal cleaning method.
Ultrasonic cleaning
– immersion of the tube bundle in a water bath where ultrasonic waves form cavitation bubbles and impact the surface to remove deposits – this has proven to be near 100% effective in cleaning both organic and inorganic fouling. The bath can have a tailored chemistry to dissolve the deposits or hold them in suspension and make them easy to remove. The high effectiveness, safety, low water consumption, and overall low cost of this method is highlighted in the two references below. The table, based on analysis of actual operating data, shows the roughly 15% average improvement in cleanliness compared to hydroblasting. It shows the ratio of the actual heat duty right after cleaning (Qa) to what should be expected from a clean heat exchanger (Qc), for eleven actual cases from oil refining.
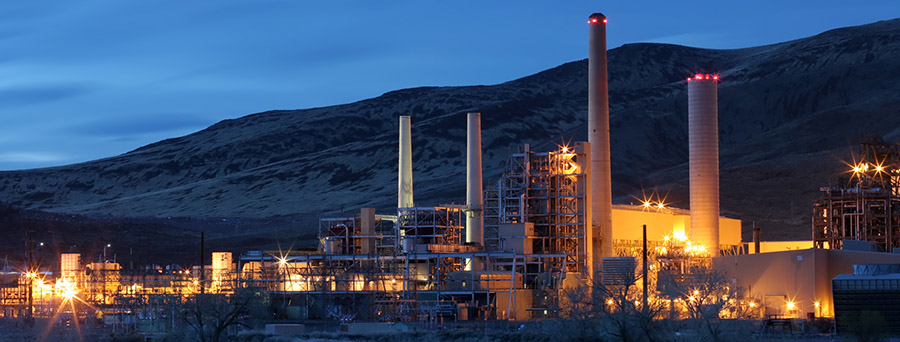
Conclusion
Shown above is a qualitative representation of the cost and effectiveness of three cleaning methods I have experienced. In summary, chemical cleaning has a wide range of cost and effectiveness; hydroblasting is about 85% effective with costs varying mainly based on location; and ultrasonic cleaning gives the best cleaning at costs similar to hydroblasting or cheaper.
About the author
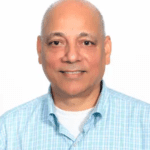
Himanshu Joshi is an industry veteran with 34 years’ experience as a Heat Exchanger specialist at ExxonMobil and shell. in his career, he has dealt with all aspects of heat exchangers from selection and design to operational troubleshooting and improvements. He served as the subject Matter Expert (SME) for fouling and heat transfer enhancement with both employers and conducted a fouling r&d program which has resulted in unique predictive methods.
References
- Thermal cleaning of heat exchangers, no alternative but a better way to clean – R. A. Mol
- Taking safety to the max: Eliminating hydroblasting risk through innovative design, automation and process – B. Kieser and D. Stang
- Understanding the value of cleaning – gains from the use of ultrasonic cleaning of large industrial equipment – C. H. Schulz and B. Kieser