Over the centuries, the evolution of heat exchangers has witnessed remarkable advancements driven by scientific discoveries, technological breakthroughs, and the growing demand for enhanced energy efficiency. In this article, we delve into the fascinating journey of heat exchangers, tracing their evolution from ancient innovations to the cutting-edge technologies of the present day.
By Omari Hussein Sabuni, Mechanical Engineer – Kinyerezi Power Plant
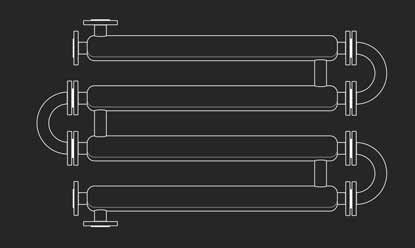
The roots of heat exchanger technology can be traced back to ancient civilizations. One notable example is the hypocaust system used in Roman baths and villas around 2000 years ago. This underfloor heating system employed a network of channels and pillars to circulate warm air produced by a furnace, effectively transferring heat to living spaces. Another ancient innovation is the “Alembic,” a precursor to the modern condenser. Used in alchemy and distillation processes, the alembic utilized the principle of heat exchange to convert vapors into liquid form. While these early developments lacked the scientific understanding we possess today, they laid the foundation for future breakthroughs in heat transfer.
The origins of heat transfer concepts
During the 17th and 18th centuries, early heat transfer concepts began to take shape through the efforts of pioneering scientists and engineers. Here are some key developments during this period:
Experimental studies: Scientists like Isaac Newton, Joseph Black, and Count Rumford conducted various experiments to investigate the nature of heat and its transfer. They made important observations and laid the foundation for the understanding of heat transfer processes.
Calorimetry: The measurement and quantification of heat were crucial in the development of heat transfer concepts. Scientists, including Joseph Black, devised calorimeters to measure heat quantities and study thermal phenomena. Black’s work on specific heat laid the groundwork for future advancements.
Conductive heat transfer: The concept of conduction, the transfer of heat through solids or stationary fluids, was explored during this period. Scientists recognized that heat could flow through objects and attempted to quantify the conductivity of different materials. The work of Fourier and others in the late 18th century further contributed to the understanding of conductive heat transfer.
Engineering applications: Early heat transfer concepts found practical applications in engineering. For example, Thomas Newcomen and James Watt developed steam engines in the 18th century. These engines utilized the principles of heat transfer to convert heat energy into mechanical work, paving the way for the Industrial Revolution.
Heat transfer coefficients: Engineers began to quantify the rate of heat transfer between objects or fluids with the development of heat transfer coefficients. These coefficients expressed the amount of heat transferred per unit area per unit time and helped in designing efficient heat transfer systems.
Mathematical models: Scientists and mathematicians, including Fourier and Laplace, developed mathematical models to describe heat conduction phenomena. Fourier’s work on heat conduction established the basis for Fourier’s Law, which relates heat transfer rate to temperature gradients and material properties.
Radiative heat transfer: The understanding of radiative heat transfer also emerged during this period. Scientists like Pierre Prevost and John Leslie made significant contributions to the study of radiation and its role in heat transfer. Their experiments helped establish the principles of radiation exchange between objects at different temperatures.
Heat exchanger concepts: Although not highly sophisticated at this stage, the concept of a heat exchanger started to take shape. Engineers and inventors explored the use of devices to transfer heat from one medium to another. Early examples included simple devices like fireplaces with metal grates to maximize heat transfer to a room.
Industrial revolution and the rise of shell and tube exchangers
The Industrial Revolution marked a turning point in the development of heat exchangers. As industrial processes became more complex, the need for efficient heat transfer systems became apparent. In the late 18th century, the first major leap came with the invention of the steam engine by James Watt. Watt’s engine required a condenser to convert steam back into water for reuse, giving rise to the concept of surface condensation and the shell and tube heat exchanger. The years between the late 18th to the early 19th century brought significant advancements in heat exchanger technology. During this period, the rise of shell and tube heat exchangers revolutionized heat transfer in industrial processes. Here’s an overview of their evolution during this era:
Demand for industrial heat transfer: The rapid industrialization during the Industrial Revolution created a need for efficient heat transfer systems to support various processes such as steam power generation, chemical manufacturing, and metal processing. This demand prompted engineers to develop more effective heat exchangers.
Invention of shell and tube heat exchangers: The early 19th century saw the emergence of the first practical heat exchangers known as shell and tube heat exchangers. The basic design consisted of a bundle of tubes contained within a larger shell. One fluid flowed through the tubes while the other circulated in the shell, allowing for efficient heat transfer between the two fluids.
Shell and tube advantages: The design allowed for a large heat transfer surface area due to the numerous tubes within the shell. This increased surface area facilitated efficient heat exchange and improved overall performance. The tube bundle could also be easily removed for cleaning or maintenance.
Application in steam power plants: Shell and tube heat exchangers were ideal for use in steam power plants. They were used to transfer heat between the hot flue gases from the combustion process and the water or steam flowing in the tubes. This facilitated the generation of steam for powering engines and machines.
Refinements and enhancements: As the industrial demand for heat exchangers grew, engineers made several refinements to the shell and tube design. These included improvements in tube materials, such as the introduction of brass and later steel tubes that were more resistant
to corrosion and pressure. The development of tube supports and baffles inside the shell improved heat transfer efficiency by enhancing fluid mixing and reducing fouling.
Increased efficiency and capacity: Over time, engineers developed techniques to enhance the performance of shell and tube heat exchangers. By increasing the number of tubes, optimizing the tube diameter, and improving the shell design, the heat transfer capacity and efficiency of the exchangers improved significantly. This allowed industries to achieve better energy utilization and Process efficiency.
Broader applications: Shell and tube heat exchangers expanded beyond steam power plants and were applied in various industries. They were used in chemical processing, oil refineries, food and beverage production, HVAC systems, and more. The versatility and reliability of shell and tube exchangers made them a popular choice for a wide range of industrial applications.
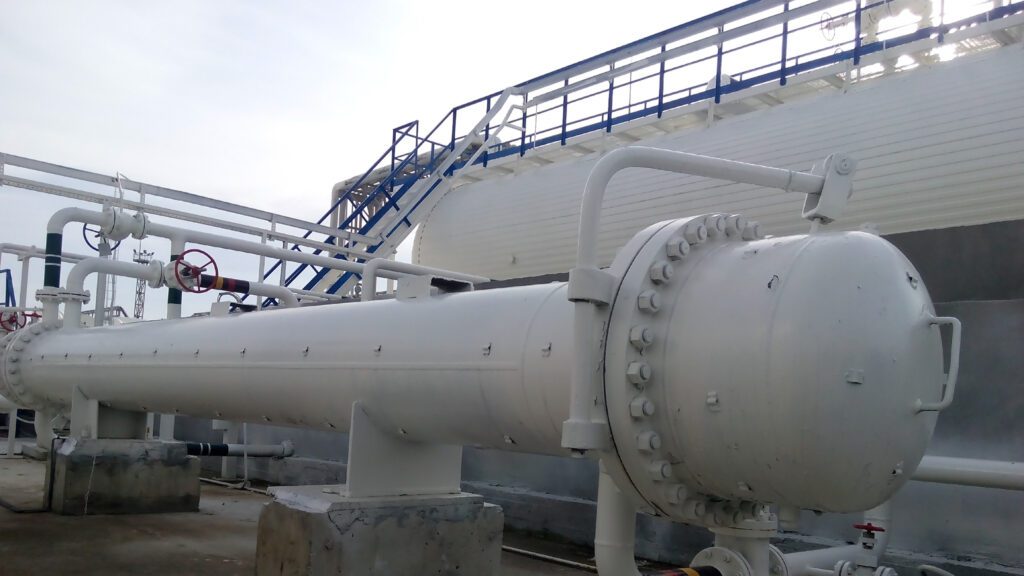
Advancements in compactness and efficiency
As industrial processes advanced, the demand for more compact and efficient heat exchangers grew. In the early 20th century, engineers introduced new designs and materials to meet these requirements. One notable development was the introduction of finned tube heat exchangers. By adding fins to the exterior surface of the tubes, the heat transfer area was significantly increased, improving efficiency.
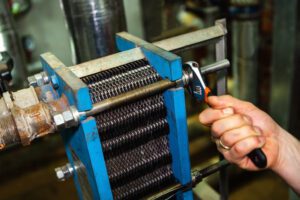
Plate heat exchangers: In the 1920s, plate heat exchangers emerged as a compact alternative to traditional shell and tube exchangers. They incorporated a series of corrugated metal plates, which increased the surface area available for heat transfer. This design led to improved heat transfer efficiency and reduced overall size and weight of the exchangers.
Compact heat exchangers: The concept of compact heat exchangers gained prominence in the 1960s. These exchangers featured intricate designs that maximized the heat transfer surface area while minimizing the size and weight of the unit. Compact heat exchangers encompass various types, including plate-fin, printed circuit, and microchannel heat exchangers.
Finned tube heat exchangers: Fins were introduced on the heat transfer surfaces of tubes, enhancing heat exchanger performance. Fins increase the surface area available for heat transfer and facilitate better heat exchange between the fluids. Finned tube heat exchangers are widely used in applications such as air conditioning, refrigeration, and oil and gas processing.
Plate fin heat exchangers: Plate fin heat exchangers, also known as fin and tube heat exchangers, became popular in the latter half of the 20th century. They consist of alternating layers of flat plates and fins, which create a highly efficient heat transfer mechanism. Plate-fin exchangers find applications in industries such as aerospace, automotive, and cryogenics.
Enhanced surface geometries: Researchers have explored advanced surface geometries to enhance heat transfer performance. These include microstructured surfaces, such as microchannels, micro-ribs, and micro-corrugations, which promote better fluid mixing and heat transfer characteristics. Textured surfaces, with patterns or coatings, can also enhance heat transfer by reducing fouling and improving fluid flow.
Advanced materials: The use of advanced materials has significantly contributed to improved efficiency and compactness of heat exchangers. Materials like stainless steel, titanium, and various alloys offer excellent heat transfer properties, corrosion resistance, and mechanical strength. These materials allow for higher operating temperatures and pressures, leading to more compact and efficient heat exchanger designs.
Computational modeling and optimization: With the advent of computational modeling and optimization techniques, engineers can now design heat exchangers with improved efficiency and compactness. Computational Fluid Dynamics (CFD) simulations and other numerical methods enable detailed analysis of fluid flow, heat transfer, and pressure drop characteristics, leading to optimized designs.
Heat exchanger network design: Heat exchanger network design techniques focus on optimizing the arrangement and integration of multiple heat exchangers within a system. By considering the process conditions, heat transfer requirements, and fluid properties, engineers can identify opportunities for compactness and efficiency improvement, leading to energy savings and reduced costs.
Additive manufacturing: The emergence of additive manufacturing, or 3D printing, has opened up new possibilities in heat exchanger design. It allows for complex geometries, customization, and integration of features that improve heat transfer performance. Additive manufacturing enables the creation of intricate internal flow paths, optimized surface textures, and novel heat exchanger designs not easily achievable with traditional manufacturing methods.
Advancements in computational fluid dynamics and optimization
In recent decades, the combination of computational fluid dynamics (CFD) and optimization techniques has significantly contributed to the evolution of heat exchangers. CFD simulations allow engineers to visualize and analyze complex flow patterns, temperature distributions, and pressure drops within heat exchangers. This enables them to fine-tune designs for optimal performance and energy efficiency.
Furthermore, advanced optimization algorithms have been employed to improve heat exchanger performance by maximizing heat transfer rates, minimizing pressure drops, and optimizing geometry. This multidisciplinary approach has led to the development of innovative heat exchanger designs, such as printed circuit heat exchangers and additive manufacturing techniques.
Emerging trends and future prospects
The evolution of heat exchangers continues to unfold with the emergence of new trends and technologies. One such trend is the integration of renewable energy systems with heat exchangers, enabling efficient utilization of waste heat and the integration of thermal energy storage. The application of heat exchangers in sustainable processes, such as geothermal energy, solar thermal systems, and waste heat recovery, holds great promise for a greener future.
Another area of ongoing research is the exploration of advanced materials with enhanced thermal conductivity, corrosion resistance, and durability. Graphene, carbon nanotubes, and other nanomaterials are being investigated for their potential to revolutionize heat transfer technology by providing superior performance at the nanoscale. Furthermore, the development of smart heat exchangers equipped with sensors and control systems enables real-time monitoring and optimization, leading to increased efficiency and reduced energy consumption.
The evolution of heat exchangers spans centuries, from the ancient hypocaust systems to the modern advancements in micro and nano heat exchangers. As we move forward, the integration of renewable energy, advanced materials, and smart systems promises to reshape the landscape of heat exchangers, leading to a more energy efficient and sustainable future.
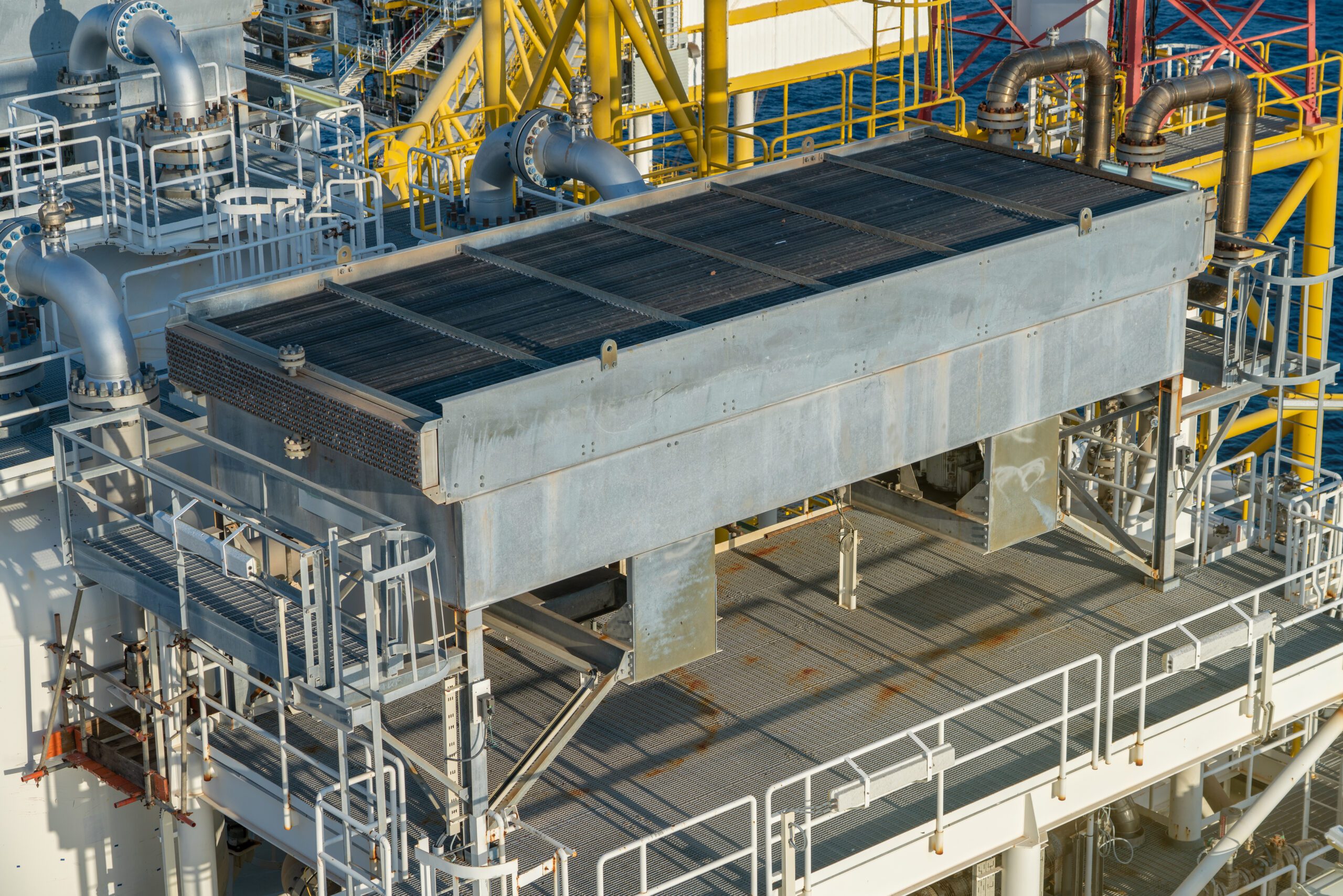
Micro and nano heat exchangers
As technology continued to advance, the need for even smaller heat exchangers arose. this led to the development of micro and nano heat exchangers, leveraging the unique properties of micro and nanostructures. micro heat exchangers employ microchannels and microfins to achieve high heat transfer rates in compact devices. they find applications in electronics cooling, fuel cells, and microreactors.
Nano heat exchangers push the boundaries of miniaturization even further. By utilizing nanoscale materials and structures, such as carbon nanotubes and nanoparticles, these heat exchangers exhibit exceptional thermal conductivity and efficiency. the emergence of nanotechnology has opened up new possibilities in fields like electronics, medicine, and renewable energy. Micro and nano heat exchangers represent the latest advancements in heat exchanger technology, offering unprecedented compactness, high heat transfer rates, and potential applications in various fields.
About the author
Omari Hussein Sabuni is an experienced mechanical engineer at kinyerezi gas power plant, specializing in heat exchanger design, optimization, troubleshooting and providing practical solutions for various heat exchanger problems. He is skilled in analyzing thermal systems and developing innovative solutions to enhance heat transfer efficiency and adept at conducting feasibility studies, performing risk assessments, and ensuring compliance with industry standards.
About this Featured Story
This Featured Story was first published in Heat Exchanger World Magazine in September 2023. To read more Featured Stories and many other articles, subscribe to our print magazine.
Featured Stories are regularly shared with our Heat Exchanger World community. Join us and share your own Featured Story on Heat Exchanger World online and in print.