FACO headquarters & operations in Varallo Pombia (NO), Italy.
In the competitive landscape of industrial manufacturing, FACO stands out as a beacon of quality and innovation. A family-owned enterprise, FACO specializes in crafting custom-made finned block heat exchangers and drycoolers for a diverse range of industries, including HVAC, power generation, marine, oil & gas, chemical, food, heavy industry, and others. Heat Exchanger World sat down with Giorgio Lorenzoni, FACO’s Sales Director, to explore the core principles that have driven the company’s success. This article uncovers the unique strategies and product lines that make FACO a reliable partner in the field of heat exchangers, highlighting their dedication to sustainable practices and advanced engineering.
By Iryna Mukha, Heat Exchanger World
Company origins
Since its inception in 1963, FACO has stood at the forefront of innovation in the manufacturing of finned block heat exchangers and drycoolers for both industrial applications and HVAC/Refrigeration systems. Founded by Dante Dalla Rosa, soon joined by his brother Ivano, FACO quickly established itself as a specialist in HVAC heat exchangers, leveraging the complementary technical and organizational expertise of its founders.
Today, with more than 60 years of history, FACO is well-positioned to meet new technological challenges and sustain its leadership in the production of industrial, HVAC, and process heat exchangers. The company remains dedicated to its mission and core values, striving to create a lasting impact in the heat transfer industry while fostering a better future for generations to come.
The mission of FACO is to provide cutting-edge thermal solutions that enhance efficiency and sustainability across various industries. The company is dedicated to delivering high-quality products that not only meet but exceed industry standards and customer expectations. Their goal is to lead the way in innovation while maintaining a commitment to environmental stewardship.
According to Giorgio Lorenzoni “FACO values integrity, collaboration, and continuous improvement. We believe in fostering a culture where teamwork is paramount, ensuring that our skilled workforce of 170 employees feels empowered to contribute their best ideas and efforts.” FACO’s commitment to research and tailored solutions remains unwavering, reflecting their dedication to adapting to changing market demands and technological advancements.
Product line
FACO stands at the forefront of heat exchanger innovation, offering a comprehensive product line tailored to meet the diverse needs of various industrial applications. Their finned block customized heat exchangers are engineered for optimal performance, with variations that include air to liquid coils, refrigerant evaporators, condensers, steam coils, air preheaters, air dryers, superheated water/steam generators, heat recovery units, and economizers. These components are adaptable through a wide choice of tube patterns, materials, and thicknesses, catering to specific operational requirements.
FACO also provides specialized executions such as airtight, cover plate, water box headers, safety double-tube, bare tubes, and reinforced seismic-proof/antishock designs. Finned block heat exchangers typically consist of multiple rows and circuits with pipe headers and return bends coils. While water box cleanable heat exchangers are primarily used for cooling electric motors and generators. Special water box double-tube heat exchangers are designed to prevent contamination from tube leaks, providing enhanced safety.
FACO also excels in the design and production of finned block customized drycoolers, gas coolers, and air-condensers, with pipe headers & return bends or water box design. These are available in horizontal, vertical, V-shape, H-shape, and Smart-Box arrangements, providing flexibility to accommodate a variety of fluids, space requirements, noise emission, external load requirements, and operating scenarios. FACO genset radiators can be designed as double-circuit drycooler for cooling two separate circuits simultaneously, such as the engine’s jacket water and aftercooler.
Gas coolers are usually arranged as a multiple-stage compressor cooler, ensuring optimal cooling and efficiency for the gas compression system. The design incorporates multiple separate circuits within a single frame, enabling the simultaneous cooling of each compression stage at different pressures and temperatures within a single unit.
FACO equipment can be provided with protective treatments like tinning, hot dip galvanizing, cataphoresis, Heresite®, Rilsan® and Blygold®, which ensure longevity and reliability under demanding conditions, and additional accessories like drip trays, drop eliminators, turbulators, drain and vent valves, low-noise fans, louvers, expansion tanks, defrosting systems, etc.
Engineering expertise
Thanks to its wide in-house engineering skills, supported by some design software, FACO is able to supply customized solutions according to the most stringent requirements.
Thermo-fluid dynamics design process is usually driven by the proprietary FACO selection software that utilizes performance data acquired from in-house testing laboratory and from CFD simulations according to ASHRAE standards. FACO holds the AHRI Std. 410 certification for the performance of the water heat exchangers used in HVAC and refrigeration applications. The company has recently acquired a license for HTRI® Xace software and has become a member of HTRI. By supplementing and enhancing the proprietary selection software, Xace may calculate, simulate and design air coolers and heat exchangers even under non-standard process conditions, to manage even more complex issues and meet all market’s demands. FACO employs Siemens AMESIM 0D-1D for an exceptionally detailed analysis of heat exchanger performance. This advanced tool – which considers the finned block as a set of discrete elements – allows to delve deeply into the intricacies of heat exchange processes, ensuring a meticulous assessment that aligns with the highest standards of accuracy. FACO leverages its in-house expertise to conduct comprehensive Computational Fluid Dynamics (CFD) thermo-fluid dynamics analyses. This proficiency enables to assess energy and flow distribution intricacies within heat exchangers and drycoolers, offering valuable insights for optimizing performance. Utilizing cutting-edge tools such as Siemens Simcenter STAR-CCM+, both the equipment itself and the surrounding installation site can be meticulously evaluated, ensuring a thorough understanding of thermal and fluid dynamics for enhanced engineering precision.
Comprehensive assessments, including seismic evaluations, shock, vibration strength and fatigue analysis, are conducted using advanced 3D modelling and Finite Elements Analysis (FEM), solidifying FACO’s reputation for excellence in engineering services. FEM software as Siemens Femap NX Nastran and Dassault Systèmes SolidWorks Simulation is used to conduct comprehensive assessments of structural integrity under extreme loading conditions.
With its robust portfolio and commitment to innovation, FACO continues to lead the industry, setting benchmarks for quality, performance, and sustainability in heat exchange solutions.
Enhanced quality
FACO operates under an ISO 9001:2015 certified quality management system. ISO 19443 QMS for products and services to the civil nuclear sector is in progress.
Tailored to customer requirements, FACO’s industrial heat exchanger and drycooler design complies with globally recognized standards, including ASME VIII DIV.1 & DIV.2 (including “U-Stamp”), EN 13445 Unfired Pressure Vessels, AFCEN’s RCC-M for nuclear power industry and other codes upon request.
FACO’s team includes internal international welding technologists and engineers who are experts in welding and brazing of austenitic stainless steel, carbon steel, copper-nickel, copper, brass and aluminium.
The manufacturing process is closely monitored according to standard or project-specific Inspection and Test Plan (ITP). A wide range of Non-Destructive Testing (NDT) options are available to meet standard or specific requirements.
Tailored approach
At the forefront of FACO’s engineering solutions is their commitment to crafting bespoke heat exchange solutions. Unlike traditional manufacturers that churn out standardized product lines, FACO thrives on customization, delivering tailor-made solutions that precisely fit the unique heating and cooling requirements of each client. “All of our production is tailor-made,” starts Giorgio, “We don’t produce any equipment series, only customized.”
This customer-centric approach ensures that each product not only meets but exceeds efficiency expectations across varied applications and environments. “We aim to provide the best value for customers in developing their products, services and businesses where heat exchange is the key factor,” points out Giorgio.
This focus on customization extends beyond product development to include predictive analysis and rigorous testing, ensuring each solution is both reliable and efficient.
“Thanks to our wide in-house design experience, supported by our engineering tools, we are sometimes able to even improve the requirements provided to us by the customers. As a result, we’re able to find a solution they didn’t know they needed,” explains Giorgio. With such a robust foundation in innovation and a commitment to quality, FACO continues to lead the industry in delivering high-performance, custom-engineered thermal solutions.
Global presence
FACO has established itself as a formidable presence in the global market, with a strategic focus on expanding its influence beyond its home base. Currently, 25% of the company’s sales originate from Italy, while a significant 75% derive from international markets, mainly in Europe. This global distribution is supported by FACO’s well-organized international network, which comprises an internal sales team adept at managing both distributors and direct customer accounts. Each sales engineer is tasked with nurturing relationships with key clients, ensuring that FACO’s innovative solutions are consistently delivered with precision and reliability.
In addition to its internal team, FACO benefits from a cadre of skilled sales agents. The company has forged strong partnerships with some distributors in Sweden, the Netherlands, France, Denmark, Iceland, Poland, Ukraine, cementing FACO’s robust European footprint. According to Giorgio “This strategic network is critical to maintaining our competitive edge and fulfilling our commitment to sustainability and impactful innovation, ensuring that FACO not only meets but exceeds the expectations of its international clientele.”
Sustainability efforts
FACO is committed to being at the forefront of sustainability, proudly operating as a zero-emission company according to ISO 14064-1. By sourcing natural gas and electricity exclusively from renewable resources, FACO integrates environmental responsibility into its core operational framework. The company is actively addressing Environmental, Social, and Governance (ESG) topics, reflecting an earnest commitment to sustainability. Internally, FACO upholds a robust code of ethics, while also engaging in thorough discussions to evaluate and minimize its environmental impact. Giorgio notes that customer assessments often highlight FACO’s positive strides in ESG matters, while also suggesting areas for improvement, which the company intends to address in the coming years. This dedication to sustainable practices underscores FACO’s leadership in the industry and its unwavering pursuit of a greener future.
Nuclear expansion
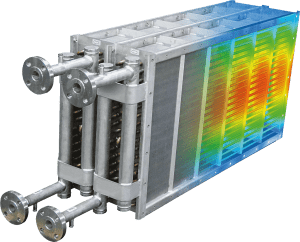
One of the most exciting developments for FACO is their head-on expansion into the nuclear industry, a sector characterized by its intricate technologies and stringent quality requirements. This move solidifies FACO’s commitment to innovation and leadership in engineering, as the company positions itself to meet the specialized demands of nuclear power. At the core of this expansion is a new production unit set to launch mid-2025 dedicated to nuclear applications, featuring offices tailored for inspection activities. This facility aims to segregate the final assembly of heat exchangers specific to nuclear projects, adhering to the unique standards necessary for such applications.
With extensive expertise in heat exchangers and drycoolers across various industrial domains, FACO is poised to deliver safety-related items that satisfy the needs of the nuclear sector. The company’s engineering capabilities are robust, allowing for the customization of products according to site-specific requirements and conditions. FACO is equipped to design and manufacture heat exchangers in compliance with AFCEN’s RCC-M code, focusing on mechanical components for pressurized water reactors (PWR) where temperature control is critical. Giorgio highlights the strategic emphasis on the nuclear market as a key area for future growth, noting, “Our engineering allowed us to enter the nuclear power market, one of the most demanding sectors. We are investing heavily in this area, as it represents a significant focus for our future endeavours.” The company’s commitment is further exemplified by its pursuit of ISO 19443 certification for the quality management system, specifically for products and services in the civil nuclear sector.
In addition, FACO is investigating about developing a digital twin for the heat exchangers specifically tailored for the nuclear industry. This groundbreaking initiative is made possible through the integration of advanced software already in-house. By creating a digital replica of the heat exchanger, clients will gain the unparalleled ability to incorporate this model within their comprehensive digital twin systems of entire plants. This integration offers the capability to simulate every conceivable operational condition, thus optimizing performance management and enhancing safety protocols. This ambitious project epitomizes the next level of advanced engineering at FACO, positioning both the company and its clients at the vanguard of technological innovation within the nuclear sector.
About this Featured Story
Why Subscribe?
Featured Stories are regularly shared with our Heat Exchanger World community. Join us and share your own Featured Story on Heat Exchanger World online and in print.