This article demonstrates the Helixchanger option in reducing the velocity-dependent fouling in heat exchangers.
By Bert Boxma, Heat Transfer ABC, The Netherlands
Introduction
Heat exchanger fouling causes a major economic drain on industries today. In most industrialized countries these losses amount to 0.25 to 0.30 percent of the gross national product (GNP). Costs associated with exchanger fouling are refl ected in over-sizing of the heat exchangers leading to not only the incremental capital and installation costs but also the operation, maintenance and downtime costs adding up to a staggering 2.5 to 3.0 times the initial purchase price of heat exchangers. High performance heat exchangers are particularly susceptible due to greater loss of performance under fouling conditions.
More than 35-40% of heat exchangers employed in global heat transfer processes are of the shell and tube type of heat exchangers. This is primarily due to the robust construction geometry as well as ease of maintenance and upgrades pos-sible with the shell and tube heat exchangers.
In a shell and tube heat exchanger, the conventional seg-ment baffl e geometry is largely responsible for higher foul-ing rates. Uneven velocity profi les, back-fl ows and eddies generated on the shellside of a segmentally-baffl ed heat exchanger results in higher fouling and shorter run lengths between periodic cleaning and maintenance of tube bundles. In a Helixchanger heat exchanger, the conventional segmen-tal baffl e plates are replaced by quadrant shaped baffles positioned at an angle to the tube axis creating a uniform veloc-ity helical fl ow through the tube bundle. Near plug fl ow conditions are achieved in a Helixchanger heat exchanger with little back-fl ow and eddies, often responsible for foul-ing and corrosion. Exchanger run lengths are increased by 2 to 3 times those achieved using the conventionally baffl ed shell and tube heat exchangers. Heat exchanger performance is maintained at a higher level for longer periods of time with consequent savings in total life cycle costs (TLCC) of owning and operating Helixchanger heat exchanger banks.
Feedback on operating units as well as case studies are presented to illustrate the improved performance and economics achieved by employing the Helixchanger heat exchangers.
Fouling characteristics
The principal mechanisms of fouling are reported to be as follows:
• Particulate matter in flows
• Crystallization
• Chemical reaction
• Corrosion processes
• Biological mass accumulation
This paper covers the impact of shellside fouling on the thermal performance and economics of shell and tube heat exchangers employed in the refinery and petrochem-ical plant processes.
Refinery applications
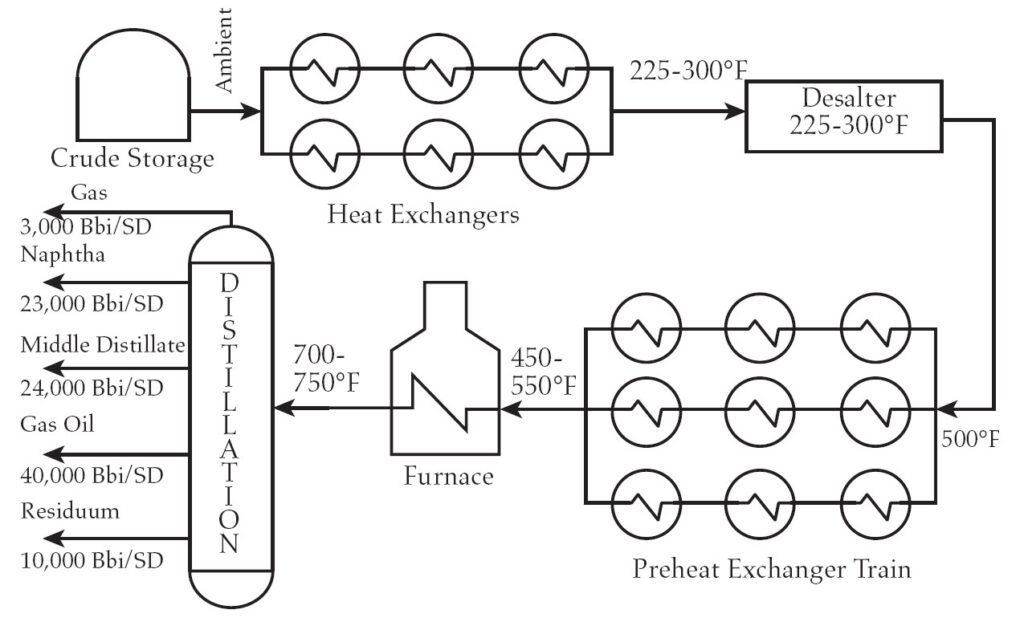
Generally, the fouling deposits occur as high molecular weight polymers are formed in the crude preheat systems. Products of corrosion and inorganic salts mix with the polymers and increase the volume of the fouling deposits. Most of the heat input in a refinery takes place in the Crude Unit where the crude oil is preheated in heat ex-changer trains prior to further heating to elevated tem-perature in a fired heater (furnace). See Fig. 1. The total refinery output is relying on the uniform operation of the crude unit with consistent outlet temperatures at desired flow rates. Preheat exchanger performance is, therefore, vital in reducing the fuel consumption in the downstream furnace and supplying the uniform crude flow to the furnace over a desired run cycle.
The second most important process unit in the refi nery is the Hydrotreater. The process stream in a Hydrotreater reacts with hydrogen in presence of a catalyst at elevated tempera-ture and pressure to remove sulfur and nitrogen. The major fouling in this unit occurs in the feed/effl uent heat exchang-ers. In these exchangers, the cold Naphtha feed is preheated using the hot product effl uent. See Fig. 2. Fouling in the Feed/Effl uent heat exchangers can decrease the outlet preheat temperature of Naphtha causing more fuel consumption in the furnace and/or reduce the Naphtha flow rate.
The last refi nery process where heat exchangers are em-ployed as Feed/Effl uent heat exchangers is the Reformer Unit. See Fig. 3 for a schematic of this unit. Reforming is a catalytic process designed to increase the antiknock quality of the naphtha streams. The dehydrogenation in this unit converts the naphthenes to aromatics. Fouling in the preheat exchangers play a vital role in reducing the heat transfer coeffi cient, often by 25-30% in three(3) months and as low as 50% in six(6) months after startup. Added fuel costs in the downstream furnace as well as maintenance and cleaning costs of heat exchangers could signifi cantly affect the plant operating costs. Anti-fouling agents are often added to the process streams to reduce the fouling tendencies and improve the plant economics.
The total fouling related expenses in the major refi ning units in the USA alone is estimated to be approximately US$ 1.4 billion a year. The total fouling related costs for major industrialized nations is estimated to exceed US$4.4 billion annually. Considering that the Refi nery fouling related costs rep-resent a minor portion of the fouling related costs in all industries, the fouling mitigation technology deserves a greater attention.
Fouling mitigation technology
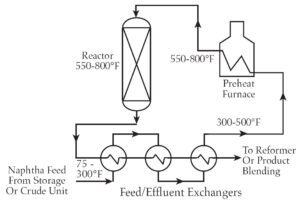
The Tubular Heat Exchanger Manufacturers Association (TEMA) standards suggest fouling factors for several fluids based upon the asymptotic fouling model as described by Kern and Seaton (1959). In this model the competing fouling mechanisms lead to an asymptotic fouling resistance beyond which no further increase in fouling occurs. The asymptotic values are, therefore, recommended as the design fouling factors in the TEMA standards. This approach does not particularly address the fouling phenomenon such as that at the “hot” end of a crude preheat train, since fouling there does not exhibit the asymptotic behavior.
Ebert and Panchal (1997) have presented a fouling model that is expressed as the average (linear) fouling rate un-der given conditions as a result of two competing terms, namely, a deposition term and a mitigation term.
Fouling Rate = (deposition term) – (anti-deposition term) where α, β, γ, and δ are parameters determined by regres-sion, τw in the shear stress at the tube wall and Tfi lm is the crude fi lm temperature ( average of the local bulk crude and local wall temperatures).
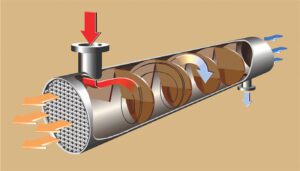
The relationship in Eq. (1) points to the possibility of identifying combinations of temperature and velocity below which the fouling rates will be negligible.
Ebert and Panchal (1997) present this as the “threshold condition”.
The model in Eq. (1) suggests that the heat exchanger ge-ometry which affects the surface and fi lm temperatures, velocities and shear stresses can be effectively applied to maintain the conditions below the “threshold conditions” in a given heat exchanger.
In a Helixchanger heat exchanger, the quadrant shaped baffl e plates are arranged at an angle to the tube axis in a sequential pattern, creating a helical fl ow path through the tube bundle See Fig. 4. Baffle plates act as guide vanes rather than forming a fl ow channel as in conventionally baffl ed heat exchanger. Uniformly higher fl ow velocities achieved in a Helixchanger heat exchanger offers enhanced convective heat transfer coeffi cients. See Fig. 5.
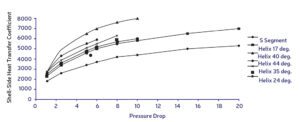
Helical baffles address the thermodynamics of shellside flow by reducing the flow dispersion primarily respon-sible for reducing heat exchanger effectiveness. Least dispersion (high Peclet Numbers) achieved with the helical baffle arrangements approach that of a plug flow condition resulting in high thermal effectiveness of the heat exchanger. See Fig. 6.
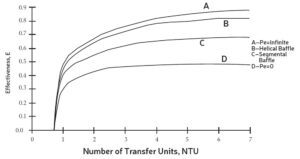
Optimum design of a Helixchanger heat exchanger offers the following characteristics:
• Uniform flow velocities through the tube bundle offering uniform film and metal temperatures.
• Elimination of backflow and eddies
• Shellside flow approaches plug flow conditions improving the temperature driving force.
• Higher flow velocities are achieved with corre-spondingly lower pressure drops, thereby improving sheer stress at the heat transfer surface.
• Reduced shell size achieved with the Helixchanger option, offers higher tubeside velocities as a secondary benefi t in reducing the tubeside fouling rates as well.
All of the above characteristics achieved in a He-lixchanger heat exchanger contribute significantly in lowering the fouling rates and maintain higher performance during longer run cycles as compared to conventional heat exchangers.
Helixchanger feedback
Case 1: Crude Preheat Train, Refinery in USA
This application consists of two parallel trains of two exchangers in series. Desalted crude is preheated from about 450°F to 500°F in this exchanger with 680°F tar, before being sent to the crude furnace for further heating.
It is a highly fouling application. The existing segmental baffl e exchangers required cleaning once per year. Fig 7 (a) shows the performance of these exchangers in the last operation cycle. After cleaning in mid-1998, the heat duty achieved in these exchangers varied from about 24 MMBtu/hr to 17 MMBtu/hr in mid-1999. The fi rst set of HELIX bundles were installed in mid-1999. Fig 7 (b) shows the performance of these bundles after more than 6 months in operation. Between Mar-2000 and Sep-2000, the heat duty achieved in these bundles varied from 37 MMBtu/hr. to 33 MMBtu/hr. In mid-2001, the average heat duty achieved in the HELIX bundles was 29MMBtu/hr. As evident, the HELIX bundles achieved, on average, more than 50% higher duty than the earlier segmental bundles. This was a result of the signifi cantly reduced fouling accumulation on the heat transfer surface and the enhanced heat transfer performance achieved in the HELIX design. Evaluation of typical mid-2001 data on the HELIX bundles showed the total fouling resistance to be around 0.022 hr ft2 °F/Btu, which was less than 50% of the fouling resistance observed in the segmen-tal bundles. The higher average heat transfer performance of the HELIX bundles resulted in valuable savings in fuel cost in the downstream fi red heater. Inspection of these bundles in early 2002 showed little fouling on the heat transfer surface. In summary, the HELIX bundles achieved 2-3 times longer operation runlengths between cleaning than the earlier segmental bundles while achieving enhanced heat transfer performance. The feedback on the application has led to the specifi cation of HELIX bundles in many crude preheat trains at different facilities of this processor.
Case 2: Crude Unit, Refinery in Canada
Twenty-two(22) HELIX units are in service at this refinery – fourteen(14) in crude preheat service and eight(8) in crude overhead condenser service. Replacement HELIX bundles were offered targeting the origi-nal heat duty in the fourteen(14) crude preheat exchangers. The earlier segmental bundles required cleaning once every year. As of Mar-2003, the HELIX bundles have demonstrated more than 2 years of continuous enhanced heat transfer performance. Fig 8 (a) & (b) shows sample data as variation of overall heat transfer coeffi cient with time between the segmental and the HELIX bundles, in the hottest four of the crude preheat exchangers. In this set of exchang-ers, crude is preheated from 370°F to about 475°F using 540°F heavy vacuum gas oil (HVGO). It is limited by temperature cross. The helical data in Fig 8 (b) after Dec 1 is to be excluded as it corresponds to a sudden 25% drop in crude fl ow rates combined with a 25°F drop in HVGO inlet temperature.
Although it may be observed from the graphs that the HELIX bundles show marginal improvement in the drop in overall heat transfer coeffi cient with time in the initial stages, it has since achieved and sustained an asymptotic level of perfor-mance much higher than the performance level achieved in the earlier segmental bundles. The HELIX bundles are report-edly expected to achieve more than 3 years of continuous operation, thus increasing the run-length by 3 times.
The crude overhead condenser application consists of four parallel trains of two shells in series. 50% capacity upgrade was offered for this service using helical baffl es in low-fi nned tube bundles within limited shellside pres-sure drop. The plant has confi rmed achieving the capacity upgrade and has reported, as of Mar-2003, more than two(2) years of successful continuous operation with these HELIX bundles. Earlier segmental bundles required 2-3 times cleaning in this time period. The HELIX bun-dles have achieved signifi cantly enhanced heat transfer performance and have sustained this performance for a long period of time. 3-4 times longer run-length has already been achieved with these bundles.
Case 3: Feed/Effluent Exchangers, Hydrotreater Unit, Refinery in the Netherlands
This application consists of four ‘BEU’ shells in series. The reactor effl uent condenses in the tube while the feed vaporizes on the shellside. The existing segmental bundles experienced severe shellside fouling requiring cleaning twice per year. Replacement HELIX bundles were supplied for this application. They were installed in 1998. Fig 9 (a) and (b) show photographs of the hottest and coldest HELIX bundles after one year in operation. Insignifi cant fouling was observed in the COLD bundle while uniform scale type of fouling was observed on the heat transfer surface in the HOT bundle. The processor has reported extending the runlength of this unit by 3-4 times with the application of the HELIX bundles. These bundles have achieved 25% larger throughput within limiting hydraulic constraints. It was also reported that the signifi cantly enhanced heat transfer performance of the HELIX bundles have provided substantial additional savings by not requiring downstream heater modifi cations.
Case 4: Feed/Effluent Exchanger, Unifining-Platforming Unit, Refinery.in Italy
This Feed/Effl uent exchanger is a four shells-in-series unit with feed vaporizing on the shellside and effl uent condens-ing in the tubes. The existing segmental-baffl ed bundles experienced severe uneven fouling, requiring cutting of the shell for access to the bundle. Fig 10 (a) shows the heavily fouled segmental bundle inside the halfcut shell. A replacement HELIX bundle was installed in the second hottest shell of this unit in year 2000. Fig 10 (b) shows the photograph of the U-bend end of this HELIX bundle, with uniformly distributed fouling over the heat transfer surface. Signifi cant cost savings have been achieved by the application of the HELIX bundle in this unit, by its reli-able operation, its reduced fouling characteristics and its consistent enhanced heat transfer performance.
Conclusions
Heat exchanger fouling has been very costly for the industry both in terms of capital costs of heat exchanger banks as well as the operation and maintenance costs associated with it.
The helixchanger heat exchanger when applied in typically fouling services, has proven to be very effective in reducing the fouling rates signifi cantly. Three to four times longer run lengths are achieved between bundle cleaning operations. Proper attention is required in designing the heat exchangers placed at the hot end of crude oil pre-heat operations where temperatures and velocity thresholds are highly dependent on heat exchanger geometry. The helical baffle design offers greater flexibility in selecting the optimum helix angles to maintain the desired flow velocities and temperature profiles to keep the conditions below the “fouling thresholds”.
Nomenclature
E activation energy, J/mol K
Pr Prandtl number
R gas constant, J/mol K
Re Reynolds number
Rf fouling resistance, m2 K/kW
t time, s
T temperature, K
α, β, γ, δ constants in Eq. (1)
τw Wall shear stress, Pa
ABOUT BERT BOXMA
Mr Bert Boxma is CEO of Heat Transfer ABC B.V. and has more than thirty-five years of experience, specialised in heat exchangers. His company is member of Heat Transfer Research Inc. (HTRI) USA and he has been familiar with HTRI’s software products since 1982.
For references used in this article, please contact the Editor.
About this Featured Story
This Featured Story was first published in the November 2021 issue of Heat Echanger World Magazine. To read more Featured Stories and many other articles, subscribe to our print magazine.
Featured Stories are regularly shared with our Heat Exchanger World community. Join us and share your own Featured Story on Heat Exchanger World online and in print.
Featured Story by Bert Boxma