Article By Sarah Bradley and John Butterfield
___
At Par Hawaii Refining, McKaig holds the title of Lead Process Engineer and works with Howard Lincoln who is Operations Superintendent. More specifically, he is responsible for overseeing the sulfur complex, the sulfur recovery units, the SCOT tail gas recovery unit (which reduces hydrogen sulfide emissions down to ppm levels), the ATU–the amine treatment unit, and the sour water stripper.
With experience in several departments, McKaig has gained significant expertise interacting with various industrial applications and pieces of equipment. In his day-to-day operation, he has had the opportunity to work with large heat transfer exchangers.
Heat exchangers are essential to the successful conversion process of refining crude oil and have an integral role at Par Hawaii. “As a company we have an excellent understanding of the conversion processes involved in refining crude oil to higher grade products. We understand what is needed to achieve optimum operational conditions for our heat exchangers, and how to size them accordingly,” said McKaig. “When it comes to designing heat exchangers, however, we do not do this ourselves.”
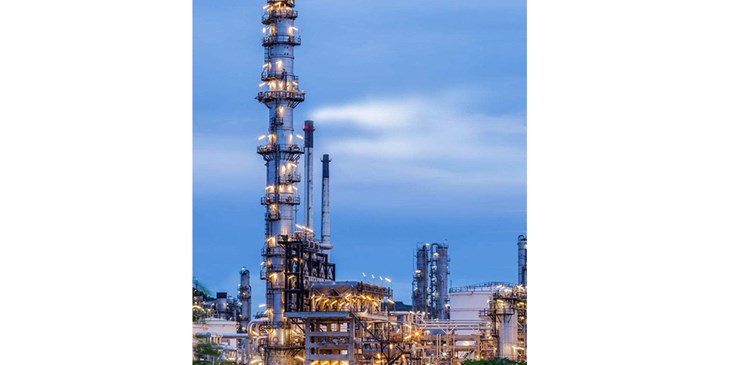
Each piece of equipment that the staff helps design has got to hold up to the duty for which it is needed, and so it is important that operators have a thorough understanding of all its processes. When a refinery requires an additional heat exchanger, the process engineers will assess and then estimate what the working conditions for the equipment will be and record this information on a process data sheet.
This is then stored for further consultation. Since accepting his role at the Par Hawaii refinery, McKaig believes he has been responsible for putting together as many as 100 of these sheets. Once drawn up, the sheets are passed on to the company’s in-house project leader.
“When we need replacement equipment, we draw on our data records and check that they correspond to the working situation. We then send our overview of requirements (specifications) to several vendors so that they can put in a tender for the construction. This can be anything from a single heat exchanger to a whole distillation tower,” explained McKaig. “Our procurement department will then analyze the bids that come back to us and see which plans make the most sense. Deciding which vender to proceed with can take a significant amount of time and discussion, as there are many ways to build an exchanger. Moreover, specs are always open to interpretation and susceptible to last minute modifications in order to fit a particular set of circumstances. It is therefore important that we understand why the manufacturer decides to build in a certain way and what the possible consequences are for the refinery. It is never a simple discussion because each project is a unique, custom-built order. With regards to the construction, we tend to rely on the input we get from the engineering companies since they have a great deal of experience and knowledge in building heat exchangers. They can ultimately guarantee the performance of the delivered equipment.”
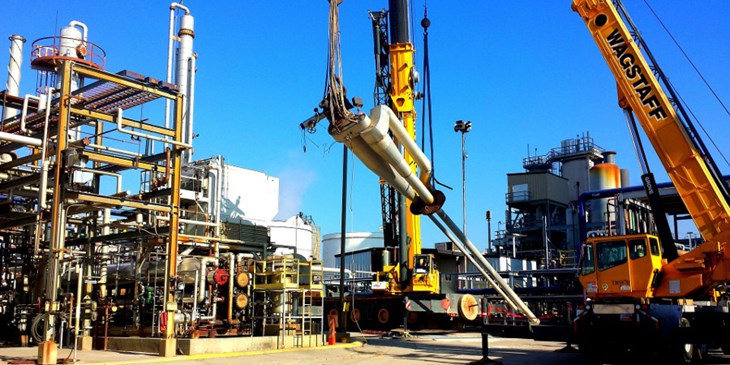
Troubleshooting
McKaig is not responsible for the design of the heat exchangers; he focuses most of his time on optimizing and troubleshooting. Heat exchangers become fouled and can corrode through use and wear. When this happens, they lose efficiency.
“I suppose you could compare a fouled heat exchanger to a car,” noted McKaig. “After it has been running for some time a car will need its air filter changed, its tires replaced, and its oil filter renewed. A heat exchanger is no different.
When equipment is continually in operation it requires servicing; parts begin to wear thinner, tubes become worn and need to be replaced, and leaks need plugging. That is why choosing the correct metallurgical composition for building the heat exchangers is so important. If we can successfully determine what material to use in construction, there will be less corrosion. Unfortunately, corrosion can never be completely eliminated.”
As corrosion is unavoidable, it is better to assess the condition of a heat exchanger in terms of its longevity and rate of decay. “Essentially, you need to think along the lines of, ‘Is the corrosion taking place at an acceptable rate—so at a very gradual rate of mils per year?’” explained McKaig. “If the corrosion progresses at a rate that exceeds reasonable expectations, then the situation has to be monitored very carefully, so that you have time to troubleshoot before a failure occurs.”
An example of one of the corrosion issues McKaig is faced with is their caustic and acid systems in the wastewater treatment plant. This is where caustic and/or acid is used to control pH levels. “We monitor the systems to check that we are controlling the corrosion rate. Over time, some issues are bound to occur, as this is part of normal wear and tear. Fouling takes place and the efficiency of the system decreases. These situations are normal. Nonetheless, if there are real issues with the acids or the wrong composition of metal alloys have been used for construction, then the heat exchangers will obviously wear and corrode more quickly. So parts will have to be replaced more frequently.”
Monitoring wear and tear
Par Hawaii can processes up to 145,000 barrels of crude oil a day based on production at Par West and Par East. This process involves heating the material in the distillation towers to up to 650ºF, where the crude oil is separated into different components, known as fractions. The type of product that is created when the crude oil is boiled depends on the temperature at which it is collected. In other words, each fraction represents a boiling range of crude oil when boiled to a specific temperature. Once the crude oil is boiled and separated into the different petroleum fraction, each fraction is captured individually and further processed to meet final product specifications or upgraded into additional products. Some heavy oils are further processed in a ‘cracking process’ which involves breaking apart the molecules of the heavier fractions to produce lighter higher-value products like jet and diesel fuel. ‘Reforming’ is another process used to upgrade the octane rating of lower-value naphtha to produce higher-value gasoline blend components. The reforming process involves chemical reactions under pressure to change the composition of the hydrocarbon chain. Once the products have been separated out, they need to be cooled down again before they can be stored.
“Such processes naturally put wear and tear on the heat exchangers. So we have exchangers that are often interchangeable, meaning we can keep some running while we take others out of service for cleaning and maintenance.”
In an effort to be as efficient as possible, many refineries now use real time tools to help monitor the performance of their heat exchangers. Data on the exchangers is produced by collecting temperatures and pressures across the heat exchangers. The engineer collects data about temperatures and pressures from various probes and inputs this data into the computer monitoring system. This information is then analyzed and used to predict corrosion for the foreseeable future. If, for example, corrosion is only occurring at around two mils per year in a plate, then it might not need to be inspected again for two to four years. On the other hand, if rates of corrosion are predicted to be considerably higher than this, then a further inspection might be needed within a shorter period of time.
Lifecycle span
“If heat exchangers are regularly cleaned and maintained, then they can work well throughout a period of 25 to 30 years,” McKaig said. However, if these criteria are not respected then it will likely need servicing much quicker.
Moreover, fluid flowing through the system does not mean that it is not getting fouled, and fouling will ultimately lead to a less-than-perfect performance. When serious corrosion issues are not attended to, McKaig estimates the lifespan of the heat exchanger can be significantly reduced. Each exchanger design has optimum configurations to minimize cost yet maintain efficiency.
Changing technology
McKaig notes that the industry continues to innovate around improving heat exchanger design and efficiency. However, the basic shell and tube heat exchanger remains an effective and efficient work horse for the industry. High efficiency heat exchangers are capable of replacing several old style exchangers, but each change must be reviewed carefully for operating conditions and lesser recognized potential concerns with fouling and corrosion.
Par Pacific Holdings, Inc. (NYSE: PARR), headquartered in Houston, Texas, owns and operates market-leading energy and infrastructure businesses. Par Pacific’s strategy is to acquire and develop energy and infrastructure businesses in logistically-complex markets. Par Pacific owns and operates one of the largest energy networks in Hawaii with 148,000-bpd of combined refining capacity, a logistics system supplying the major islands of the state and 91 retail locations. In the Pacific Northwest and the Rockies, Par Pacific owns and operates 60,000-bpd of combined refining capacity, related multimodal logistics systems, and 33 retail locations. Par Pacific also owns 46% of Laramie Energy, LLC, a natural gas production company with operations and assets concentrated in Western Colorado. More information is available at www.parpacific.com