This article elaborates on the opportunity of using less ductile duplex stainless steel alloys as a cost-effective alternative to high-alloy austenitic grades in welded plate heat exchangers. This is because the highest possible corrosion resistance is often required to meet the severe conditions encountered in the refining, chemical, and petrochemical industries.
By Claes Tigerstrand and Jan Li, Outokumpu
Shell-and-tube heat exchangers are typically selected for air coolers in the refining and petrochemical industries. However, plate heat exchangers (PHE) can provide more efficient heat transfer, result in a more compact design, and are less prone to fouling.
The challenge of designing a PHE exists because of the complex shape of the plates, which require that the material from which they are made has a high formability both in its use as well as during its fabrication processes. The sealing properties of the stack of plates are critical to ensure optimal performance. The operating pressure cannot reach the same level as for a shell-and-tube tube heat exchanger. A consequence of the stacked-plate design is that it is also more vulnerable to crevice corrosion when the environment becomes more severe.
Moreover, a PHE is per definition, in most cases, characterized as a piece of pressure equipment (due to having internal pressures over 0.5 bar), which implies that a high mechanical strength is an important mate-rial property to consider, ensuring the best possible structural performance.
Thus, the critical design criteria and associated material properties typically requested for a PHE are listed below:
• High pressure – High mechanical strength
• Complex shape – High formability
• Corrosive media – High corrosion resistance
• Efficient heat transfer – High thermal conductivity
What about using duplex stainless steels for PHE?
The most commonly used materials for PHE are – not surprisingly – the highly ductile and corrosion-resistant austenitic stainless steel alloys, e.g., 304L, 316L, and higher alloyed versions such as super-austenitic 6% Mo grades for harsher environments. Other materials such as nickel and titanium alloys are also alternatives able to address extremely corrosive media, as well as copper alloys which provide very good heat transfer properties.
Thus, if a corrosion resistant alloy, such as a stainless steel, is specified to resist corrosion in a severe environment, one start point could be: is duplex stainless steel a potential alternative for PHE because of its higher strength?
The acceptable design stresses given for different duplex alloys, in accordance with the applicable design standards for pressure equipment (e.g., ASME VIII, EN 13445), are up to two times higher than those provided by austenitic grades with no nitrogen addition. If this strength advantage can be exploited, then thinner gauges can be realized, or will allow higher working pressures depending on the prevailing design condition for the heat exchanger in question. The use of thinner plates in the heat exchanger also improves the heat transfer capacity. Additionally, duplex alloys provide somewhat higher heat conductivity than austenitic al-loys with the same plate thickness.
To further evaluate the potential of using a duplex alloy in PHE, the key parameter to focus on is its forming properties. Duplex stainless steels provide a fracture elongation of about 25% vs. 40% for most austenitic grades, which clearly indicates the lower formability of the former. More ductile duplex al-loys such as Forta FDX 27 (1.4637, S82031) utilize the so-called TRIP effect, induced by its metastable microstructure, to further improve their formability to a level which approaches that of austenitic alloys. However, the corrosion resistance of this grade is com-parable to that of type 316 and therefore is not always resistant enough for the harsh conditions encountered in the refining and petrochemical industries. The most critical process parameters to consider are the higher content of impurities (e.g., chlorides and sulfur compounds), reduction of pH, or higher temperatures. Therefore, when harsher environments encountered, the question boils down to asking if conventional DX 2205, or even super-duplex SDX 2507, can serve as an alternative to the more expensive high-alloy austenitic grades? The typical chemical compositions of the selected duplex and austenitic stainless steels are depicted in Table 1, with a comparison of their critical material properties in Fig. 1 and 2.
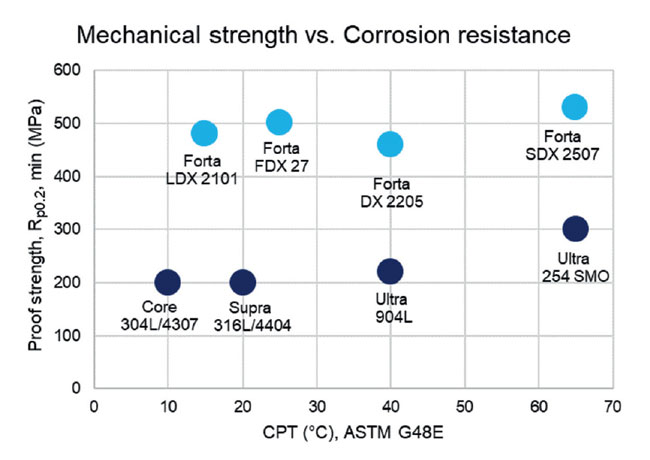
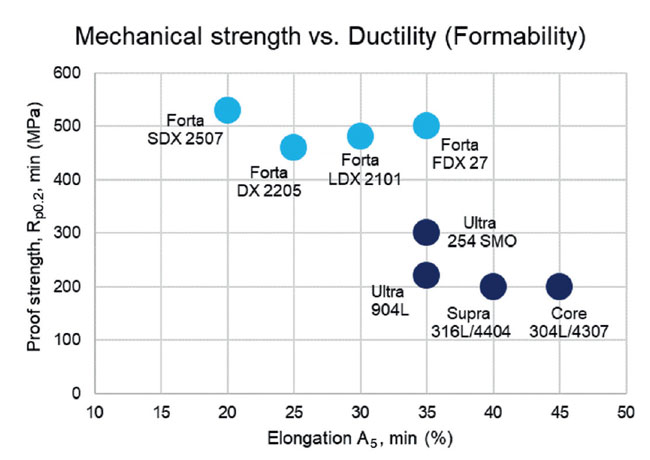
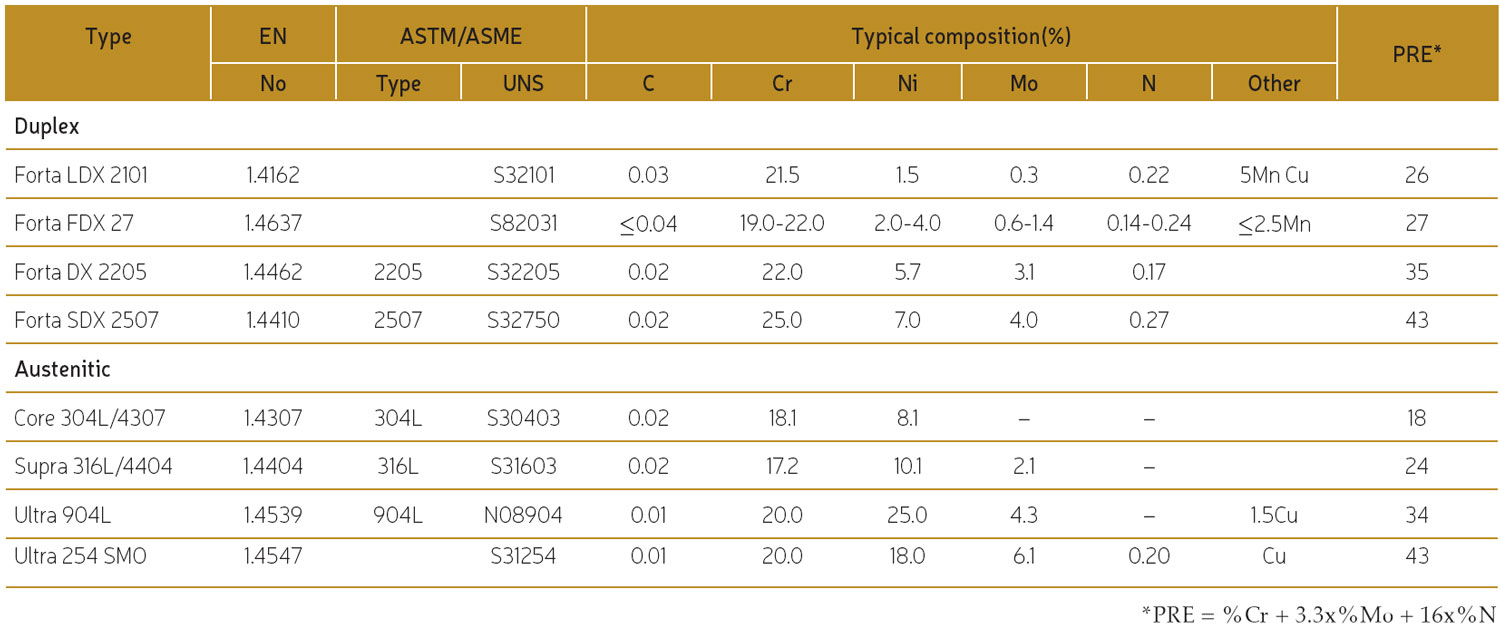
Formability and Forming Limit Diagram (FLD)
A better tool to assess the formability the complex metal sheet rather than just looking at elongation values is to consider a forming limit diagram (FLD). In this type of diagram, different bi-axial strain conditions can be evaluated. The three major forming conditions are: plane strain, stretch forming, and deep drawing, depicted in Fig. 3.
For PHE sheets there are different types of strain condi-tions depending on the specific shape of the pattern, the radii, and height of the corrugations, which infl uence the flow and heat transfer capacity. The shape complexity has a strong impact on how the tool and the forming operation can be performed using a certain type of alloy.
The graph in Fig. 4. displays the typical forming limit curves (FLCs) for three different types of stainless steels: ferritic, austenitic, and ferritic-austenitic (duplex). As expected, the austenitic type provides the best formability considering all strain conditions, and the ferritic type the worst even though the latter, in relative terms, performs better in deep drawing. The duplex type with its dual microstructure sits in-between [1].
A heat-exchanger plate with its complex shape really challenges the material performance. The formability would be typically highest when biaxially strained, and lowest in the plane strain condition and therefore complex parts such as a heat-exchanger plate often fail under this condition. The sheet thickness also influences the formability – a thinner gauge depresses the FLC, which brings further challenges when a duplex alloy is opted for, when considering that its higher strength enables plate thicknesses to be reduced.
To evaluate if a duplex alloy is feasible or not for use, one approach could be to perform a forming trail using the existing tooling designed for the austenitic stainless steel. A grid pattern is then typically applied to the blank, This makes it possible to measure the strains after forming with a camera and compare them with the FLC for the same alloy and thickness.
Let us illustrate the situation using an experiment with 0.6 mm thick DX 2205. This was carried out as the initial development work for a case study presented below in which the goal was to replace 316L for a welded PHE. A cut piece of the heat-exchanger plate is displayed in Fig. 5.
The result of the strain measurements are depicted in Fig. 6, where the measured data points indicate the most prone area to cracking is in the bottom radius of the protrusion in the rolling direction of the sheet, where plane strain conditions prevail. The margin of failure is about 5% strain. However, the most strained area is located at the end point of the ridge where thinning has occurred due to stretch forming conditions. Yet, the margin of failure is about a 15%-strain. A common rule of thumb is to include a safety margin of about 10–15% strain below the FLC to avoid failure.
The insight gained from this test was that it is possible to use the existing tooling for DX 2205 without causing any failure. Nevertheless, to ensure a robust and predictable solution minor changes in the pattern were recommended, such as smoothing out the critical radii to reduce both the critical plain strain conditions and to reduce the degree of thinning.
Important to mention here is that a finite element simu-lation is a very effective tool to use prior to conducting further prototype testing in order to optimize the shape of the corrugation pattern.
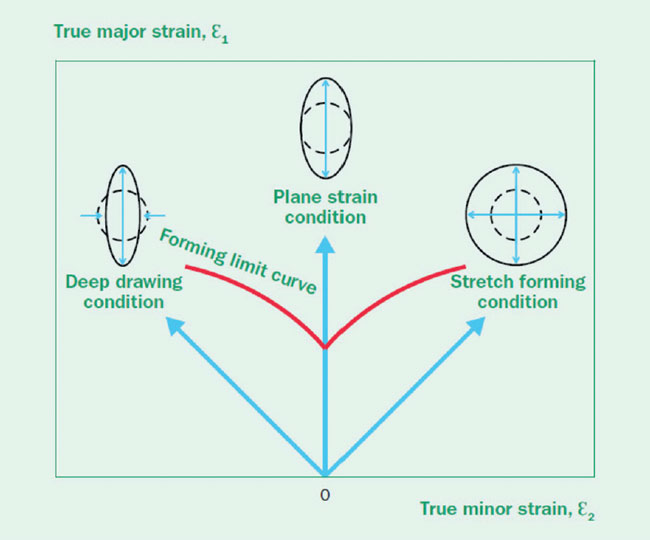
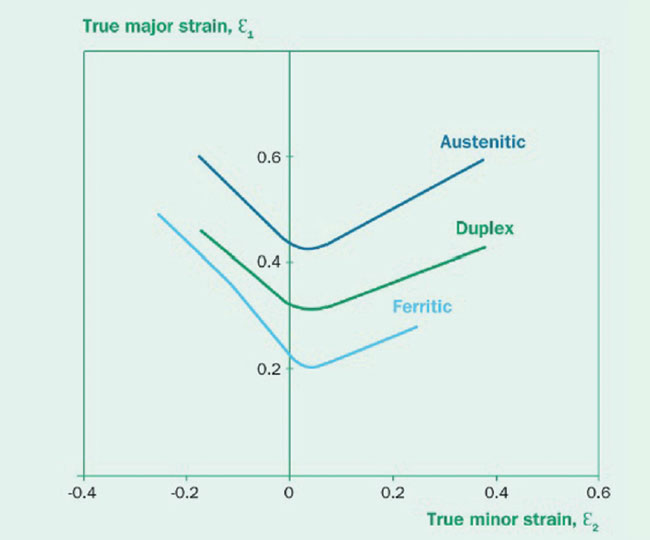
Case study: Plate heat-exchanger solutions using duplex for refining and petrochemical industries
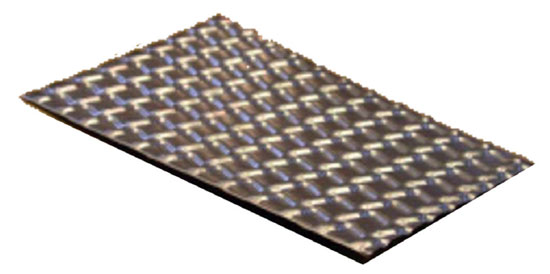
Heat-exchanger plates made of duplex stainless steel were developed by the Chinese heat exchanger manufacturer Gansu Lanke Petrochemical Equipment Co., Ltd. (here-inafter referred to as LANPEC) under the lead of Prof. Chunmei Chang.
The plate design, which was considered previously impossible to produce, was made using duplex grades. This result came about due to intensive technical cooperation between Outokumpu and LANPEC. Only minor modifi cations to the pressing die were implemented for the fi nal solution (as explained in the previous section).
The first solution in 2006 was an all-welded PHE using 0.6 mm thick DX 2205 plates, and replaced underspecifi ed 316L for an overhead condenser of an atmospheric distil-lation column in an oil refi nery. The solution provided a considerably longer service life when compared to that of 316L, which lowered the OPEX (e.g. shutdown, repair and replacement costs) for the plant. This experiment was a great success and has been followed by numerous others since then (another case depicted in Fig. 7).
In recent years, refining and petrochemical plants have encountered even more corrosive sour crudes, which also reach the limit of DX 2205 for some PHE applications. Therefore, our joint development team has continued to work on the development of more resistant – but less ductile – super-duplex grade SDX 2507 to serve as an alternative to more expensive super-austenitic and titanium alloys. The aim of this work was to achieve a more cost-effective solution with less intensively formed heat-exchanger plate designs, which benefi tted because of its leaner alloying composition, higher strength, and comparable corrosion resistance.
This work has resulted in the consistent production of welded PHE using SDX 2507. Until now, both DX 2205 and SDX 2507 were widely used for PHEs in industries, such as in oil refi ning, the chemical and pharmaceutical industries, for environmental protection, in nonferrous metal industries, and in wastewater treatment. This is an impressive achievement by LANPEC and Prof. Chang, which clearly moves the boundaries forwards as to what type of applications duplex stainless steel can be used for. In Table 2 a few different cases and their critical environments are highlighted in which either DX 2205 or SDX 2507 were selected.
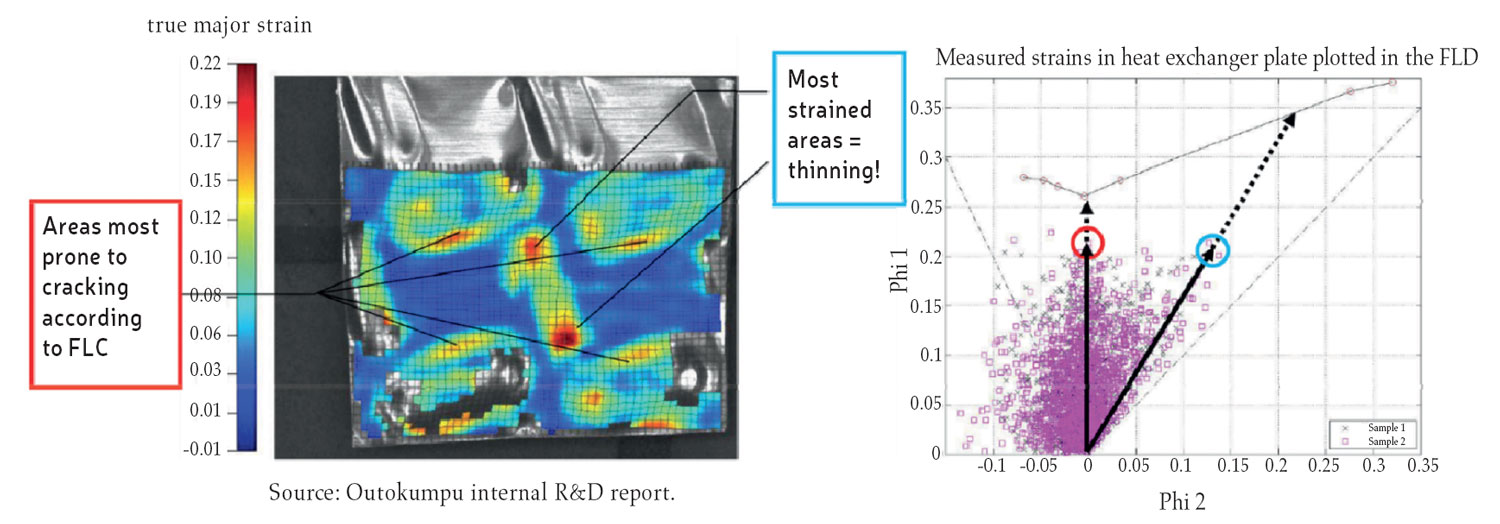
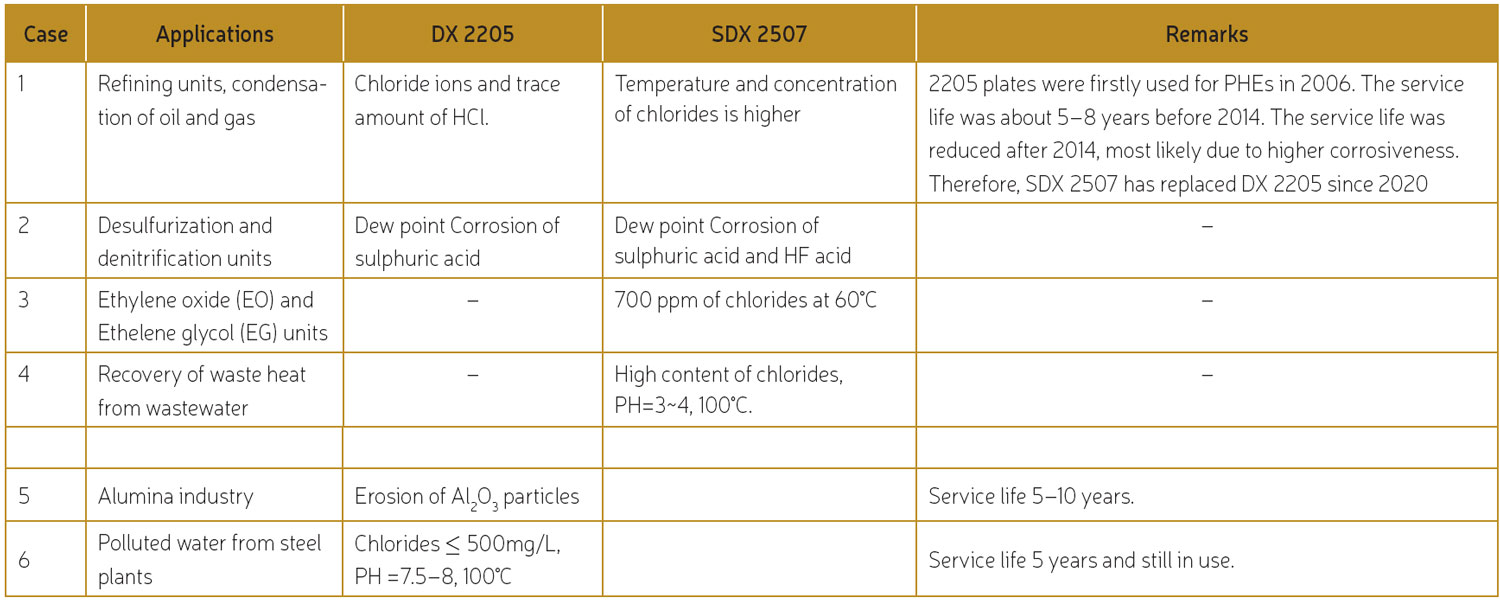
Conclusions on the suitability of using duplex stainless steels for PHE
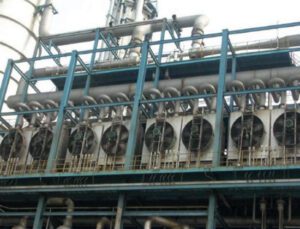
1) Higher design stresses can be tolerated than for austenitics – allowing for higher working pressure or thinner plates.
2) Relatively complex flow patterns can be pressed using similar forming tools as for austenitics supported by material supplier expertise.
3) Cost-effective solutions can be realized utilizing their superior properties to improve the performance of the heat exchanger. The leaner alloying composition provides a higher relative corrosion resistance, which delivers reliable operations and potentially longer service life, hence a lower total LCC.
Reference
[1] Sheet Metal Forming Handbook, Outokumpu 2017.
About Outokumpu
Outokumpu is the global leader in sustainable stainless steel. Our stainless steel has the highest recycled content and the smallest environmental footprint in the industry. The company is organized into four business areas – Europe, Americas, Ferrochrome and Long Products. We employ some 10,000 professionals in more than 30 countries, with the headquarters in Helsinki, Finland. The history goes back to the invention of stainless steel and we continue to drive stainless steel innovation. Outokumpu offers today the widest portfolio of high performance stainless steels products in the market.
About the author
Claes Tigerstrand – Head of Heavy Industry, Technical Value Creation, BA Europe, based in Sweden with more than 20 years’ experience of global technical marketing related to stainless steel for Outokumpu.
About the author
Jan Li is Lead Technical Manager – Heavy Industry, Technical Value Creation, BA Europe based in China with a strong focus on developing the use of stainless steel for applications in the chemical process industry in East Asia. Joined Outokumpu in 2002.
About this Featured Story
This Featured Story was first published in Heat Exchanger World Magazine in November 2021. To read more Featured Stories and many other articles, subscribe to our print magazine.
Featured Stories are regularly shared with our Heat Exchanger World community. Join us and share your own Featured Story on Heat Exchanger World online and in print.