In the chemical process industries, some of the major issues faced in heat exchangers are fouling, vibration, leakages, and increased energy consumption. All these issues have a direct impact on the performance of the heat exchanger and effect the performance of downstream equipment.
By Mrinal Das – Senior Vice President Projects & Engineering Purchase, Dorf Ketal Chemical
Many of these issues are interlinked. For example, a lot of exchanger leakages occur from flow distribution issues. If the flow through the exchanger is not uniform, then high flow velocities can cause an additional problem, vibration. This vibration can increase the effect of erosion in exchangers which then leads to frequent leakage creating problematic maintenance and associated costs. Hence it becomes essential to use analytical tools to address flow distribution issues inside heat exchangers. Out of all the above issues, the most troublesome and common issue is fouling.
Fouling in heat exchangers
Fouling is a progressive process and can be defined as deposition of undesirable materials on the heat exchanger surface. Undesirable materials could be inorganic salts, polymers, sludge, sediments, crystals, coking products, biological deposits etc. Fouling in a heat exchanger directly impacts the heat transfer and flow. Fouling results from the synergistic consequence of transient mass momentum and heat transfer phenomenon between fluids and surfaces. The fouling process significantly depends on operating conditions like temperature, pressure, viscosity, density, thermal conductivity. Fouling in a process plant causes significant reduction in thermal performance, increase in pressure drop, promoting corrosion and eventually failures in heat exchangers.
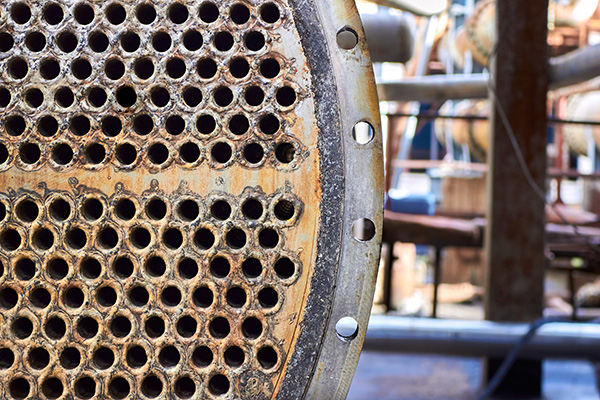
Common fouling types
Generally, about six types of liquid-side fouling mechanisms are observed in process plants viz. corrosion fouling, biological fouling, particulate fouling, chemical reaction fouling, precipitation or crystallisation fouling, freezing/solidification fouling. Common types of fouling are chemical, biological, deposition, and corrosion. Chemical fouling occurs from chemical reactions in the fluid stream resulting in the deposition of material on the heat exchanger surface. This type of fouling is common for chemically sensitive materials when the fluid is heated to temperatures near its decomposition (degradation) temperature. Coking of hydrocarbon materials on the heat transfer surface is also a common chemical fouling issue. Biological fouling occurs when biological organisms grow on heat transfer surface. It is common fouling mechanism where untreated or improperly treated water is used as coolant.
Corrosion fouling results from a chemical reaction which involves heat exchanger surface materials. Many metals such as copper and aluminum form adherent oxide coatings which serve to passivate the surface and prevent further corrosion. Many metal oxides which are corrosion products exhibit quite a low thermal conductivity and even relatively thin coatings of oxides may significantly affect heat exchanger performance.
Deposition fouling occurs when fluid particles settle onto the inorganic surfaces area. This is generally seen when the velocity of fluid falls below critical levels. This type of fouling can be helped with the proper management of the combined particles/fluid. In reality, more than one fouling mechanism is present in many processes and their combined effect is phenomenal and can be much severe than expected.
Various deposition and removal processes during fouling can be seen at glance in below diagram.
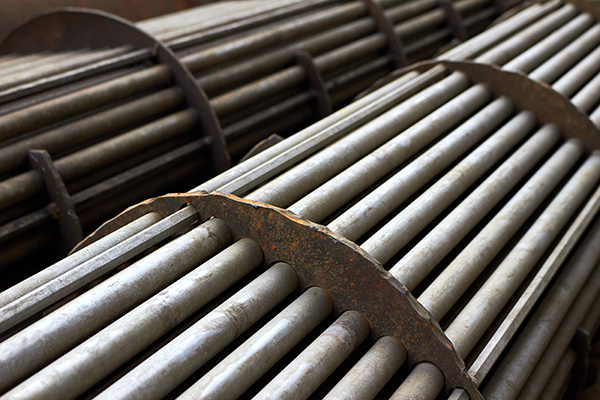
How to monitor your heat exchanger
Hence it becomes very important to have data points and information to precisely monitor a heat exchanger. The parameters which can be measured for monitoring are inlet and outlet temperature for cold fluid, inlet and outlet temperature of outlet fluid, mass flow rates for both cold and hot fluids, and hot and cold fluid pressure change across the heat exchanger.
To keep the heat exchange system running effectively it is advisable to consider some of these points: 1) understand all available data associated with pressure, flow, and temperature indication; 2) find out and assess what flows, pressures, and temperatures are recorded by operators in their daily routines; 3) continuously check the pressure – differential pressure tracking
on shell side or tube side of a heat exchanger can be extremely valuable information – if the differential pressure builds up over a period it means something is restricting the flow; and 4) to record temperature data information, it is best to utilise a handheld temperature gun, infrared temperature guns can help you monitor the temperature of the system effectively throughout its operation.
By utilising today’s technology tracking the system manually, any process industry can keep track of a heat exchanger. Chemical cleaning methods by acid and alkali with combination of rinsing can be used to clear the fouling in heat exchangers. Chemical cleaning can clean fouling effectively without the need to dismantle the heat exchanger. This process enables the heat exchanger to be operational in reduced time without taking it offline.
Designing against fouling
In the designing stage, fouling factor is taken into consideration. Different methods of heat exchanger construction are carried out by manufacturers to help provide an increased heat transfer area that may be affected by fouling. During manufacturing, many important factors are taken into consideration to minimise the occurrence and buildup of fouling: a) allocate more fouling fluid to tube side; b) design the heat exchanger for a fouling fluid velocity of 3 ft/s on the shell side and 5 ft/s on the tube side; c) allow easier cleaning access to the heat exchanger; d) when servicing, make sure the wall temperature of the tube isn’t kept too hot, as it could create unwanted deposit of salts or render any chemicals ineffective.
The effect of fouling causes deposition on the walls of passages either in tubes or/and in shell sides of heat exchangers. This reduction is passage area causes increase in pressure drop and reduced heat transfer. Heat transfer and pressure drop are inversely proportional to the diameter of the passage. Pressure drop will increase to cube root of diameter. Pressure drop of a fouled heat exchanger passage is very high compared to the clean passage of the heat exchanger.
Fouling causes immense production loss associated with efficiency deterioration. This production loss can be associated with unplanned and planned operation shutdown due to fouling,
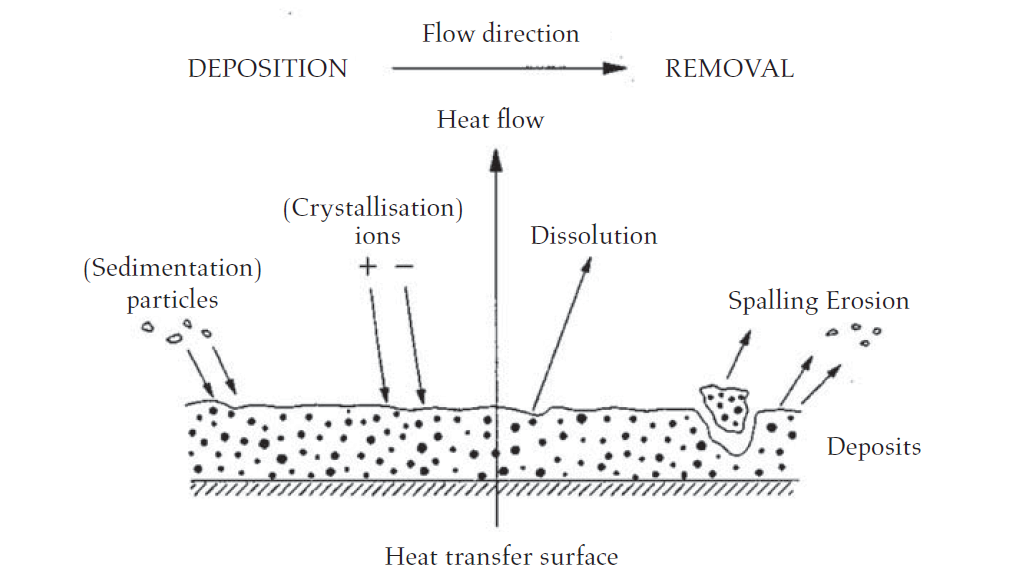
maintenance costs from removal of heavy fouling deposits with the use of chemicals/anti-fouling devices, maintenance cost associated with replacement of plugged or corroded equipment, cleaning cost for industries range between EUR 46 to 55,000 per heat exchanger. Fouling can be determined by either the nature of the fouling process fluid, the heat transfer process or combination of both. Heat transfer mechanism is the main cause for most of the fouling. High temperatures increase the rate of fouling. By decreasing the temperatures, the rate of fouling can be lowered which in turn will reduce the cleaning cycle. Hence it is important to mitigate fouling through large increases in heat transfer efficiency and changing flow conditions inside exchanger tubes.
Conclusion
We can conclude that fouling effects can be immensely reduced in heat exchangers by proper design, controlling the materials which cause fouling, good selection of construction material, proper protective coatings for the heat exchanger surfaces, and periodic regular cleanings. Detailed and effective analysis of operating parameters of fouled heat exchangers must be conducted and analysed as it is essential to calculating the correct fouling factor for both the product and service fluids. Process and mechanical design of a heat exchanger should ensure the right fluid velocities, temperatures, and other operating parameters.
Preventive maintenance, especially by systematic inspection, and cleaning should be carried out to prevent fouling and to maintain the heat exchanger effective running. Though fouling in heat exchangers cannot be eliminated, it can definitely be controlled and reduced to maintain the heat exchanger’s performance without adversely affecting the process performance. It is advised to read and refer to case studies articles from publications like Heat Exchanger World as well to get more knowledge and awareness.
About the authors
Mrinal Das has over 30+ years of experience in petrochemicals, refineries, fertilisers and specialty chemical industry in India and abroad. Mr Das is currently working in Dorf Ketal Chemical (Mumbai, India) as Senior Vice President Projects & Engineering Purchase. Prior to this, he had worked in senior management positions in Laxmi Organic Industries, Jacobs Engineering India Pvt. Ltd (Now Worley), Larsen and Toubro Limited, Deepak Fertilisers and Petrochemicals Pvt. Ltd, OilServ. He has worked from end-user, detailed engineering consultant, EPC and EPCm sides.