An example of a geothermal power plant. Source: Dreamstime
Heat exchangers are critical components for geothermal applications but prone to damage from scaling and corrosion. The GeoHex consortium has been working to develop materials for heat exchangers that offer improvements in anti-scaling and anti-corrosion properties as well as heat transfer performance. These materials will afford improved efficiencies and reduced costs.
Text and images provided in collaboration with GeoHex
The proposed way to realise the needed improvements is to use amorphous coatings. The initial challenge therefore lay in finding/developing coating materials which provide anti-corrosion and anti-scaling properties. This has led to the investigation of materials capable of not only providing the required anti-corrosion properties but also able to withstand the high temperatures associated with geothermal applications.
GeoHex plans to achieve reduced scale formation in geothermal heat exchangers by using a variety of different coating types, including amorphous coatings. The project aims to take development from lab scale to full equipment scale; from working on small coupons, to heat exchanger test rigs, to relatively small but still representative heat exchangers, composing of proper geometry, corrugated plates, and pipes.
Project focus
The GeoHex project has centred its focus on Organic Rankine Cycle (ORC) powerplants due to their usability for low to medium thermal resources. In these applications, heat exchangers are used with a geothermal fluid on one side and a working fluid on the other. The working fluid is boiled and the vapour transfers energy to turbines to then generate electricity. The working fluid is then condensed to repeat a continuous cycle. The outcome of GeoHex’s coating research intends to increase the heat exchanger performance for such applications, as well as to enhance anti-scaling and anti-corrosion properties.
The project relies on work carried out by a consortium (see box text). Tæknisetur undertook single-phase testing analysis for multiple types of coatings manufactured using different processes, including:
- Thermal sprayed aluminium coating (TSA)
- Physical vapour deposition (Amorphous 1 & 2)
- Electroless nickel plated coatings (ENP)
- Chemical vapour deposition (MWCNT)
- High velocity oxygen fuel coatings (nanoporous)
The Tæknisetur team assessed heat transfer performance and durability of each coating with an in-situ heat exchanger rig, installed at ON Power’s Hellisheiði geothermal power plant, fitted with temperature and flow sensors, and performed microstructural analysis of tested samples using SEM/EDX and XRD, and pull-off adhesion tests.
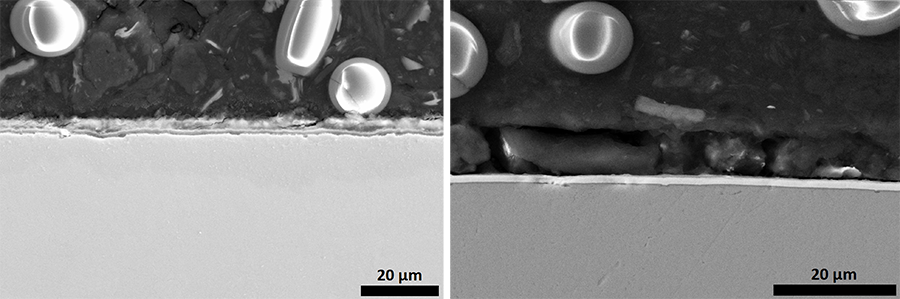
Based on the heat transfer, microstructural analysis, and mechanical results, the following conclusions can be summarised for the single phase GeoHex coatings:
- Amorphous 1 shows great potential in silica removal where 80% of silica scaling was removed at 15.86 MPa but only 40-50% was removed on 245SMO and 316L at 27.03 MPa and 18.1 MPa respectively.
- TSA and ENP show a 45% and 35% increase in heat transfer coefficient respectively with low scaling accumulation compared to reference materials.
- 316L-Amorphous 2 sample had 4.9% lower heat transfer coefficient compared to the nanoporous-Amorphous 2 sample indicating better heat transfer performance, indicating better heat transfer performance by using the nanoporous coating.
Advantages of amorphous over crystalline structures
Amorphous materials do not have a well-defined crystalline structure, giving coatings based on them unique physical and chemical properties making them ideal for protective coatings. The lack of a crystalline structure means they can be deposited in a variety of ways (sputtering, ARC-deposition,), at mild and very scalable conditions giving precise control of thickness and properties.
Other advantages:
- Hardness and wear resistance
- Corrosion resistance
- Smoothness
- Can be designed to have enhanced properties, such as high or low reflectivity
- Electrical properties – can be designed to have high conductivity or insulation
This project has received funding from the European Union’s Horizon 2020 research and innovation programme. Grant agreement: 851917
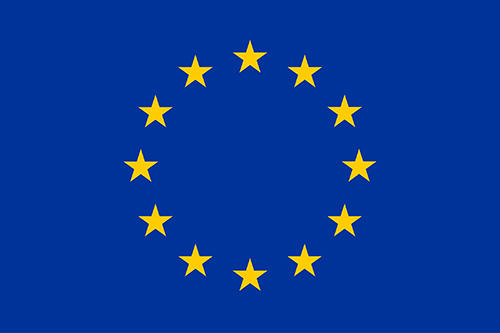
David Ingvi Snorrason (R&D Engineer and Project Manager from GREIN research, another member of the GeoHex consortium) explains further: “Corrosion tends to occur on grain boundaries and amorphous materials lack such boundaries meaning that the oxide scale which inherently forms on the material is uniform which hopefully makes the coatings more corrosion resistant. Also, with regards to the polymeric reaction of silica scaling, the smoothness of metallic glass could potentially hinder formation of scaling and/or make it easier to get rid of silica scaling. The focus of this project is on heat exchangers, but we also see possible application in different parts of geothermal systems.”
Future applications and overcoming issues
When asked about the future of such coatings, and prospects of their real-life application to geothermal heat exchangers, Baldur Gunnarsson of Tæknisetur explains that the “results for the amorphous coating show great potential for silica scaling removal and by using the nanoporous coating on the working fluid side shows an increase in heat transfer coefficient.”
David of GREIN Research expands further:
“The heat exchanger plates are where you need coatings with high thermal stability which our chrome coating can provide
(up to 750 degrees C, which is beyond the requirement in geothermal power plants). But, we also considered other components of the geothermal system, such as the turbine blades or sensitive parts which might come into contact with more corrosive environments.” The researchers believe that the coatings will be just as useful in these applications as for the heat exchangers.
Application of the coatings will require further testing, as this will involve hard to reach areas such as interior surfaces of pipework – physical vapour deposition techniques, for example, are difficult but not impossible to perform. Further analysis is also needed for cost predictions, although the team expects overall cost will be reduced as the coatings will provide superior protection, meaning lower cost materials can be used rather than austenitic stainless steels. As with all research projects, the team did encounter some issues, such as delamination.
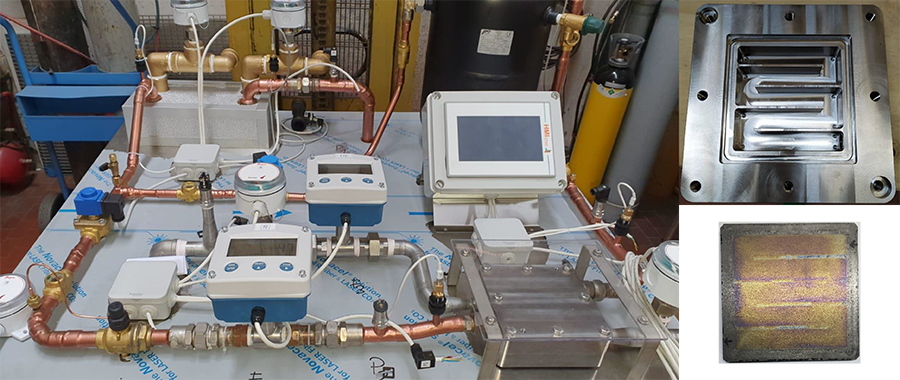
“We saw delamination especially because the samples we produced initially for our first screening were mirror-finished,” David explained. “So we saw some peeling in certain cases, but that’s a problem that can be solved by using a better adhesion layer. In this case, we used a chromium adhesion layer, but there are other elements that can be used, titanium for example. So, if you do run into that problem where you’re getting too much tension in the coating, the tension becomes too much for the adhesion and becomes an engineering problem generally which can be solved by using proper adhesion layers beneath the coating. We’ve not used fracture mechanics, but we do standard scratch tests and adhesion tests to assess the coatings. We are working to improve on this.” Regardless of how early these test results are, the GeoHex team is confident about the durability of its coatings.
“The testing was only 200 hours for the long term testing, which is not a lot of time. So it would be good to test further for longer periods,” said Baldur. “We saw some indication of corrosion in some of the coatings, thermal sprayed aluminium and nickel phosperous, but most did not show any signs of corrosion. So I can’t yet commit to an exact number for lifetime assessment. But I assume that at one point for the heat exchanger, you would want to take disassemble the heat exchanger and clean it so we would have to assess the forces you can apply to the coating without damaging it. In general, we believe these coatings will have a long lifetime.”
Current status
By way of a conclusion, GeoHex is confident that amorphous metal coatings show a great potential for corrosion protection, but it can be challenging to find alloy compositions that form a stable amorphous structure. Combinatorial magnetron sputtering and X-ray analysis can be used to map out the phase space of TaSiM (M = Al, Cr, Fe, Ti) alloys and identify amorphous compositions.
In a paper published in the ‘Journal of Non-crystalline Solids’, representatives from GREIN Research and the University of Iceland demonstrate how amorphous coatings are obtained at atomic percentages above 10-15% of each constituent; TaSiAl coatings are stable when annealed in air up to and including 550°C whereas TaSiFe, TaSiCr and TaSiTi remain amorphous up to and including 750°C. The research also shows that Ta35Si15Cr50 is almost unchanged at that temperature, and has a stable surface oxide shell less than 20 nm in thickness at 650 °C. The stability of these materials at high temperatures means that they could be suitable for use as anti-corrosion coatings in high temperature applications, such as in geothermal.
GeoHex global consortium
Iceland – ON; University of Iceland; ICETEC; Grein Research
Norway – Flowphys AS
UK – TWI Ltd; Technovative Solutions; University of Leicester
France – CEA; ENOGIA
Italy – Spike Renewables
Romania – Polytechnic University of Bucharest
Philippines – Quantum Leap
Find out more
You can find out more about the GeoHex project through an interview with project leaders in Heat Exchanger World March 2022 issue: https://heat-exchanger-world.com/featured-story-the-geohex-project-anticorrosive-coatings-for-geothermal-heat-exchangers/
Learn more from the project’s website: https://www.geohexproject.eu/
Recent paper produced by representatives from Grein Research and the University of Iceland, ‘Structural stability and oxidation resistance of amorphous TaSi-based ternary alloy coatings’: https://www.sciencedirect.com/science/article/pii/S2590159123000353?via%3Dihub
About this Featured Story
This Featured Story was first published in Heat Exchanger World Magazine in May 2023. To read more Featured Stories and many other articles, subscribe to our print magazine.
Featured Stories are regularly shared with our Heat Exchanger World community. Join us and share your own Featured Story on Heat Exchanger World online and in print.