How heat exchangers foul
In this series of articles we will look at how heat exchangers foul, how to understand the root causes of fouling, and how to mitigate the impact of fouling. The material presented is based entirely on the author’s experience and analysis of operating situations in the oil & gas industry. However, many theories and varied experiences exist across the industry and amongst researchers.
By Himanshu Joshi – Heat exchanger specialist
Fouling builds up on the surface of heat exchanger tubes by the process of deposition of solids, called the precursors. Some precursors are species which undergo a chemical reaction and become the final fouling deposit. The precursors can be carried in with the process stream, or they can form in the heat exchanger itself, usually by precipitation. The mechanism of deposition is different depending on the fluid phase – single phase, boiling, or condensing. It is essential to understand both the nature of the precursors and the mechanisms of fouling if one wants to take remedial actions such as mitigation and cost-effective cleaning.
Precursors
Two types of precursors are responsible for fouling – those not part of the fluid (contaminants or suspended solids, e.g., corrosion products, coke, salts), and precipitated solids which are initially dissolved in the fluid (e.g., asphaltenes, polymers, some salts). The precipitation of precursors can happen upstream or within the heat exchanger. The contaminants and precipitated salts will simply deposit but not undergo any chemical conversion at the heat exchanger conditions, while the organic precipitated precursors will thermally degrade to coke-like material with temperature and time.
For fouling specific terminology, we will define “coke” as organic material which has undergone thermal conversion at high temperatures (450+ C) and which is no longer soluble in aromatic solvents like toluene; for example, coke formed in the bottom of the vacuum column. “Coke-like” material is the state of partially converted organic precursors with the conversion happening in the heat exchanger due to the relatively high tube wall temperature (250-350 C).
A clear distinguishing parameter between the two is the atomic hydrogen-to-carbon ratio (H/C) which will typically be < 0.70 for coke and 0.80-0.90 for coke-like material formed in heat exchangers. The three following sections describe the fouling processes for the three fluid phases mentioned earlier. Note that carryover of inorganic material, especially corrosion products like iron sulfide, can make heat exchangers foul that otherwise wouldn’t foul from any other mechanism.
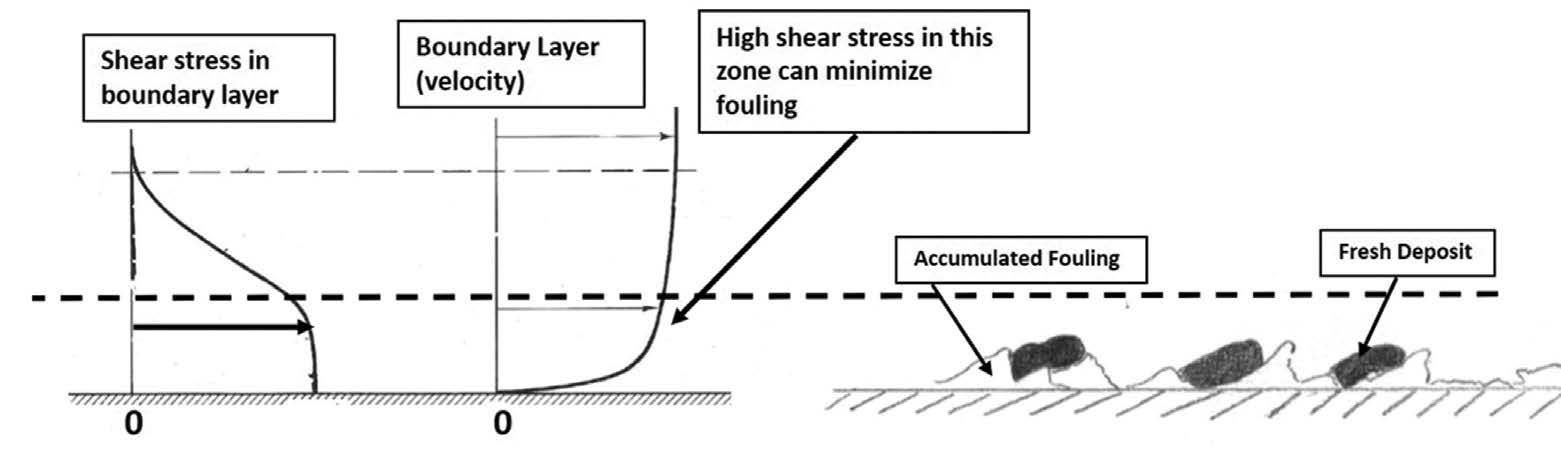
Single phase liquid or gas
Fouling of single-phase heat exchangers occurs due to deposition of the two types of precursors. of precursors. Over time, the deposit layer compacts and hardens, and provides both a resistance to heat transfer and blockage of the flow path. If the tube wall is hotter than the fluid (the fluid is being heated) the organic precursors will convert to coke-like material.
The rate of precursor deposition is highly dependent on the fluid shear stress at the tube wall (higher the shear, lower the rate) and the attraction between the surface and the precursors – some surfaces are more “sticky” for the precursors. For most situations, a wall shear stress of > 10 Pa will minimize fouling. Fig. 1 depicts this process.
Boiling/Reboilers
When a liquid containing an insoluble precursor vaporizes at the tube wall, it leaves that (solid) precursor behind. That is, the solid isn’t carried away from the wall with the vapor but sticks to the wall. If the precursors are organic, they will convert to coke-like material over time (such as in reboilers); if inorganic, they will form a hard layer over time (such as salts in a steam generator).
The phenomenon of nucleate vs film boiling is shown in Fig.2, which shows a typical pool boiling curve of heat flux vs temperature difference and what boiling flow regimes look like in a vertical tube. Under condition A, vapor bubbles escape through the liquid film on the surface while under condition B some part of the surface has vapor in contact with it. Condition B is where fouling is more likely to occur and will happen at a faster rate compared to condition A.
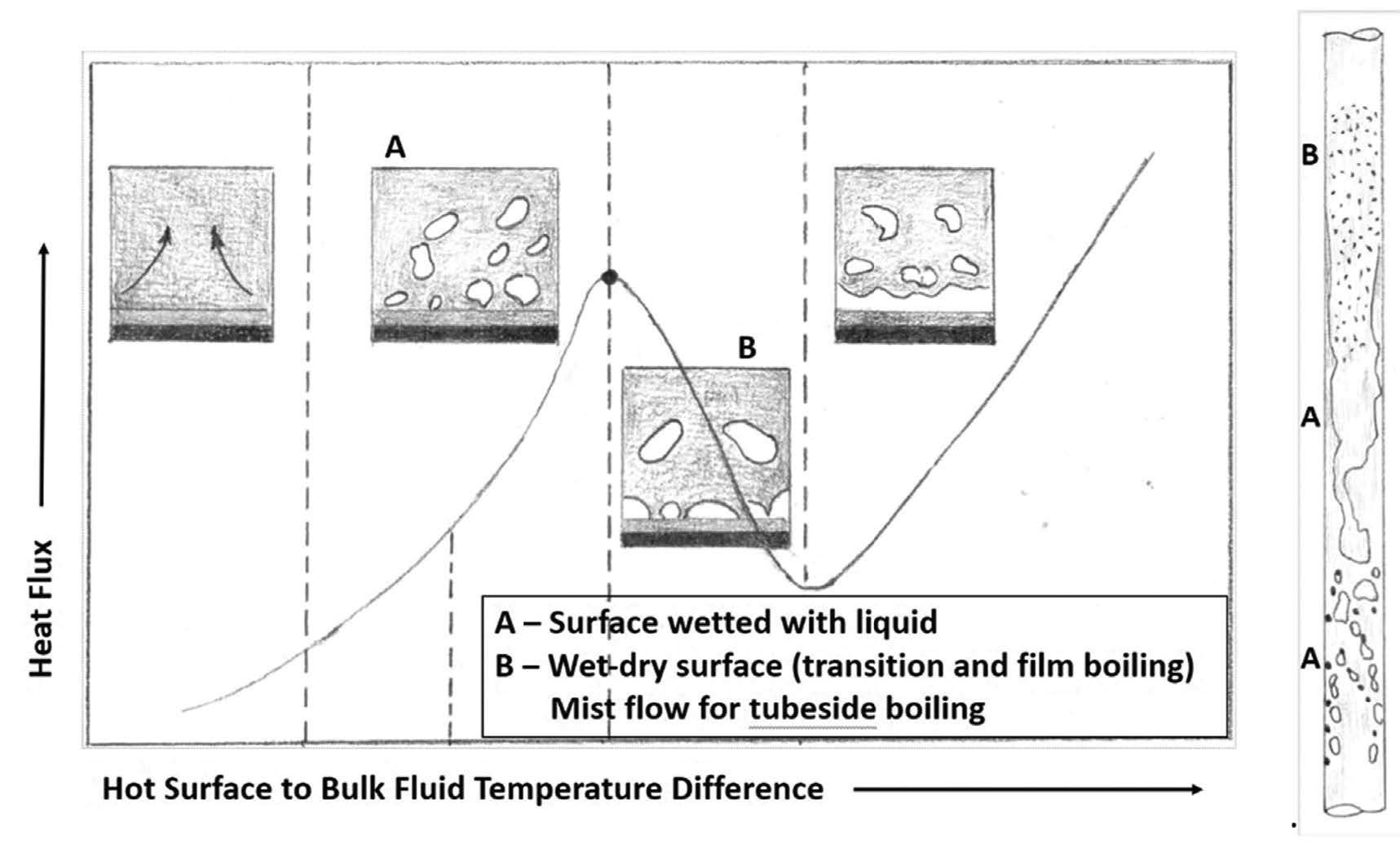
Overhead condensers
Overhead material might contain salts which are dissolved, but which precipitate when in contact with a cold tube surface. Examples are chlorides in atmospheric overhead or in hydrotreating reactor effluent. The salts may not deposit on the tube wall as they can be washed away with liquid flow, but will tend to accumulate and harden in areas where sufficient liquid is not available due to low-flow zones such as in a dead-space beyond an outlet nozzle. Water injected into the overhead or effluent can help dissolve the salts and prevent accumulation, but only if a sufficient quantity of water is available and it can reach the surfaces where deposition is likely to occur.
Catching up on Fouling Focus!
Have you missed the earlier installments of this multi-part series? All articles are available in our online archive:
Part 2 – https://heat-exchanger-world.com/heat-exchanger-fouling-in-practice-understand-and-mitigate-part-2/
Part 3 – https://heat-exchanger-world.com/heat-exchanger-fouling-in-practice-understand-and-mitigate-part-3/
Part 4 – https://heat-exchanger-world.com/heat-exchanger-fouling-in-practice-understand-and-mitigate-part-4/
Part 5 – https://heat-exchanger-world.com/heat-exchanger-fouling-in-practice-understand-mitigate-part-5
About the author
Himanshu Joshi retired from Shell in 2021 after 34 combined years with ExxonMobil and Shell, during which he specialized in heat exchangers and fouling. He was part of a team that was granted a patent related to fouling deposit analysis at ExxonMobil, and led applied fouling R&D projects at both companies. He has made several presentations about the field aspects of fouling and fouling mitigation, and deployed many mitigation technologies in the field. He can be reached by email at alph.hmj@gmail.com.