FluidForming is a high-pressure, bladder-free sheet metal hydroforming process. The process has been used by product developers and manufacturers for rapid prototyping and low- to medium-volume production runs. Working closely with product developers at Evicient, the team at FluidForming Americas helped optimize part design using Autoform finite element analysis, and created production-ready prototypes of a counterflow, flat-plate, microchannel heat exchanger for testing, analysis, and product development.
By Jurgen Pannock, Ph.D., Chief Technical Officer, FluidForming Americas LLC, and Jesse Killion, Co-Founder, Evicient LLC
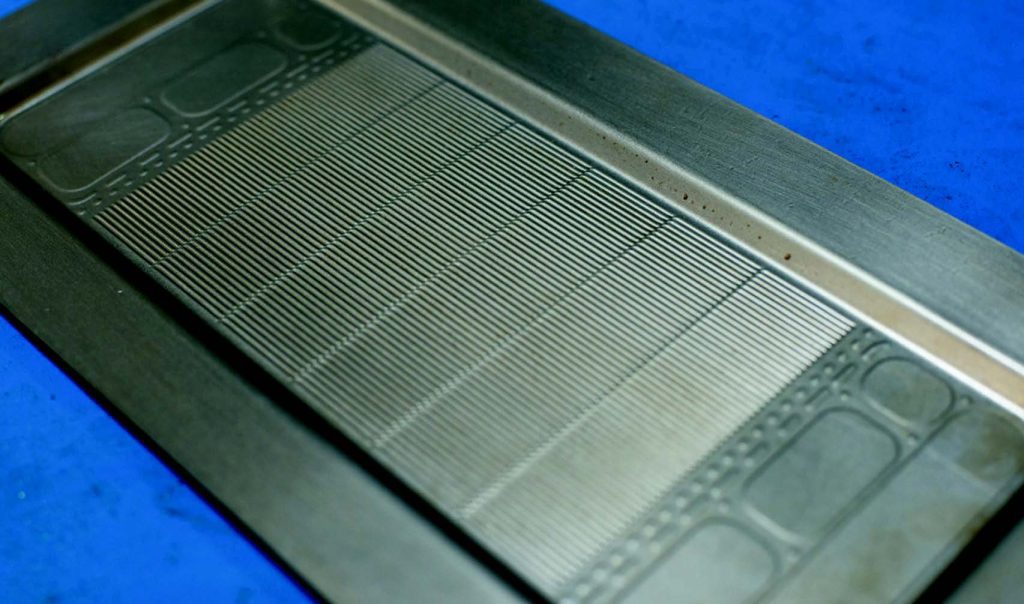
The FluidForming metal forming process was selected to form prototypes of microchannel heat exchangers from 28 gauge nickel plated 1006 steel. The dimensions of the prototype panels were 280 mm x 115 mm. The plates included headers to distribute the working fluids and 55 channels 1.7 mm wide x 0.2 mm deep. A forming pressure of 30,000 psi was employed, though the process can achieve pressures up to 60,000 psi. The fundamental benefit of this prototype — and all microchannel heat exchangers — lies in the fact that, as the cross-sectional area decreases, the surface area to cross sectional area of the media increases and the heat transfer coefficient increases. In addition, smaller channels can withstand higher pressures with thinner walls than larger channels. Microchannel heat exchangers therefore provide better efficiency with less material and more space efficient designs. Thus, the benefits of microchannel heat exchanger include:
- Efficiency: pound for pound significantly more efficient than traditional heat exchangers.
- Size: Typically significantly smaller than conventional heat exchangers.
- Fluid savings: Depending on the use, the amount of operating fluid on the inside the tubing can result in cost savings.
Creating microchannel geometries in flat-plate heat exchangers requires precise dimensional control. Creating prototypes is typically a capital-intensive process. The process in question only requires tooling on one side of the material and inherently has high dimensional accuracy and repeatability.
Problem: rapid prototyping and part functionality
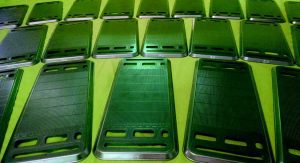
High tooling costs, elaborate machine set-up, prohibitively complex part design, and forming inconsistencies associated with conventional metal forming methods previously rendered prototyping the microchannel heat exchanger with that technology impossible. In this instance, Evicient needed a functional prototype of a microchannel heat exchanger to ascertain the feasibility of a product the company was developing. Other processes — such as bladder-based hydroforming or stamping — were unable to achieve the level of detail required for our functional analysis. The FluidForming process was not only able to achieve the challenging targeted geometry, but the tooling and low-volume costs were significantly lower than the investments required for other stamping processes”.
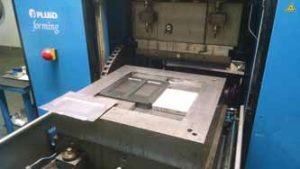
FluidForming is a sheet metal hydroforming process that achieves a 99.996% first-pass yield rate, providing the accuracy and repeatability that highly complex parts require. As a reinvention of conventional hydroforming, it uses extremely high forming pressures — up to 60,000 psi — to form geometrically complex parts, like microchannel heat exchangers. The smaller the radii or details in the part that need to be formed, the higher the pressure has to be. To form a feature with half the radius — a more detailed part, in other words — the forming pressure must increase significantly. The forming process’s ability to triple or quadruple the pressures compared to conventional, bladder-based hydroforming technology enabled the forming of these small details required for the prototypes.
Solution: higher forming pressures
With FluidForming, the part repeatability is much better, and the spring-back and warping are minimized because parts are formed more evenly as the forming force — applied by water — acts directly on the material and stretches it more evenly. The process only uses one surface onto which the material is pressed, which allows the contour to be repeated every time. Its bladder-free design and high forming pressures contribute greatly to part accuracy and repeatability. Because the completed microchannel heat exchangers experienced virtually no warping or springback, expensive and time-consuming post-forming fixturing and clamping is minimized or eliminated. The process enabled the creation of microchannel geometry in a flatplate heat exchanger design with hydraulic diameters of 600 microns. The geometric repeatability was excellent. No other vendor was able to commit to such aggressive profiles.
About the author
Jurgen Pannock is the co-founder and CTO at FluidForming Americas, LLC. He received his Ph.D. in Engineering from the University of Maryland, College Park. He went on to work for the Whirlpool Corporation, where he was employed as the Technology Manager, Global Technology Manager in Air Treatment, Director of Design for Safety, and Director of Advanced Development Refrigeration.
About the author
Jesse Killion is a co-founder of Evicient and has expertise in microchannels and two phase flow. He has over a decade of experience designing, developing and testing liquid cooling solutions for a variety of electronics applications including consumer electronics, industrial test equipment and various energy systems.
About this Technical Story
This Technical Story was first published in Heat Exchanger World Magazine in September 2024. To read more Technical Stories and many other articles, subscribe to our print magazine.
Technical Stories are regularly shared with our Heat Exchanger World community. Join us and share your own Technical Story on Heat Exchanger World online and in print.