When a fault was discovered in one of four large feedwater heaters installed at the newly built Shuqaiq Steam Power Plant in Saudi Arabia, it raised the specter of a nightmare scenario.
Text and images courtesy of AeroGo
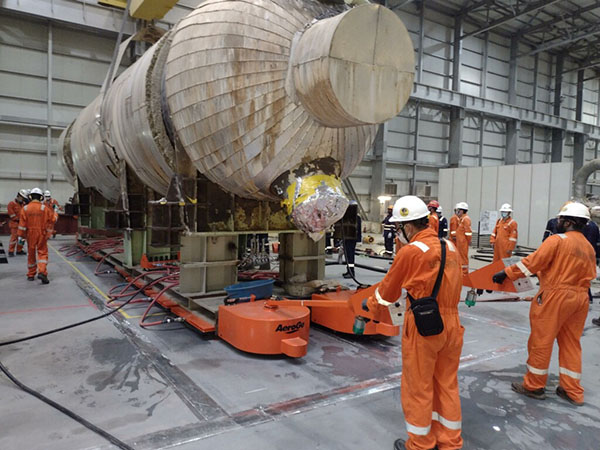
Owned by the Saudi Electric Corporation, Shuqaiq is an oil-fired 2,640MW steam turbine power plant consisting of four steam turbines, a 380kV substation, seawater intake, and more. Located 140 km north of the port city of Jazan and only commissioned in 2019, the plant quickly realized that one of the feedwater heaters had started to crack due to an irreparable fault. Suddenly, these behemoths – 65 feet long, 20 feet tall, weighing 215 metric tons (almost 450,000 pounds) – needed to be removed and replaced from a plant that was designed around the assumption each feedwater heater would spend its entire lifecycle being refurbished or reconditioned in place.
Tricky maneuvers
With scant space to maneuver the giant objects – and floors whose maximum tolerance might allow 50 tons, at a stretch – the right material handling option initially eluded them. Fork trucks wouldn’t have been able to lift the object. Cranes couldn’t fit where they needed to go and then move the objects through the circuitous route they needed to follow. Even rollers would have just crushed the floor. The task seemed impossible. But then air casters made the whole problem virtually disappear into thin air.
what are air casters?
Air casters are donut-shaped airbags that, once filled with compressed air, form a seal with the floor into which excess air continuously seeps. That excess air results in a nearly frictionless film of air less than .005” thick upon which the load literally floats. They essentially turn any object, including giant feedwater heaters, into hovercraft that can be moved with only around a tenth of the force needed to move the same weight on wheels.
To successfully position the air casters under the feedwater heaters, operators used a steel skid with
18 air casters attached. They jacked the heaters up into position, slid the skid underneath, and lowered the heaters back down. Since each caster covers around 1,500 in2, the combination spread the entire weight of the load over about 27,000 in2 and reduced total operating pressure to around 14 psi, so that the otherwise delicate surrounding floor surface would be able to bear the weight.
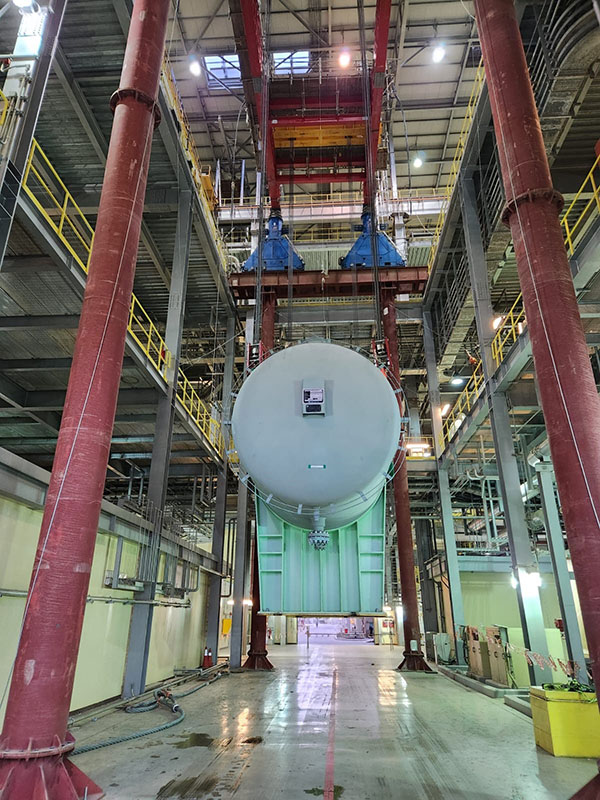
Even then, plant operators remained somewhat nervous about cracking the concrete floor because the feedwater heaters were just so heavy. So, to further protect the floor against damage, AeroGo (manufacturer and supplier of air casters) also worked with plant operators to design a grid where they could span the floor area with I-beams and lay steel plate over the top. That way, they could carry all the load on the columns of the building rather than on the floor. It wasn’t strictly necessary, since the air casters reduced floor loading so much and the film of air worked as an interface to protect the floor surface, but it did absolutely eliminate the possibility of damaging the turbine floor in any way.
quick work
Once operators had the feedwater heaters floating and the floors prepared, they had a new realm of material handling possibilities open to them. “Once they’re ready, air casters allow completely omnidirectional movement,” says Randy Manus, a Senior Field Application Specialist with AeroGo, who spent a month at the Shuqaiq site assisting with move preparations.
In this case, that meant operators would be able to transport the feedwater heaters through a narrow (relative to the size of the heaters) and circuitous path. Manus describes the incredibly difficult route the equipment had to take through the facility to reach the exit bay: “They needed to slide the heater back, rotate it 45 degrees, take it out, rotate it another 45 degrees, move down 200 meters of runway, make a 90-degree turn, and finally park it in an area with a big strand jack crane. There, they could pick it up, slide it over and lower it down to basement level for removal.”
Any other material handling system that could even come close to handling such a route would take hours or days of painstaking starts-and-stops. Not so with air casters. “From the time we started to move til the time we finished, the move was about 35 minutes,” says Manus. Replacing the heaters with replacement units simply followed the exact same procedure in reverse – and was just as fast.
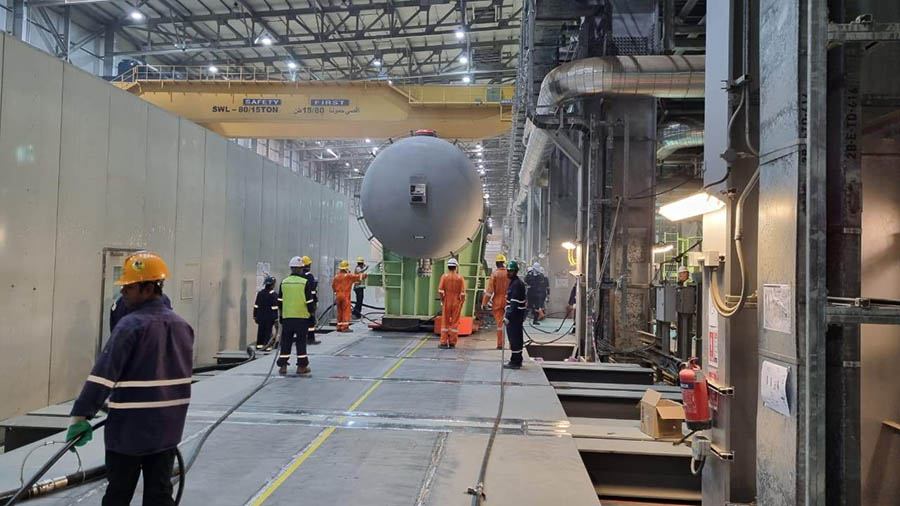
Precise positioning
One critical factor during the move: being able to maintain precise positioning of the equipment. Along portions of the route, the heaters came within inches of wall on either side; even the smallest misalignment could have resulted in a collision. To help with navigation and positioning, operators used power drives attached to the air casters.
Then, the replacement unit had to fit in exactly the right spot. Often, it’s easier removing objects than getting them back in position in exactly the right way. Air casters can do both with equal finesse, allowing operators to move the equipment easily out of position and then relocate it perfectly in line with necessary hookups, attachments, and pipes.
Simple operation
On top of the speed and precision of the air casters, the move required only three operators, two on one end and one on the other, with three powered drives. Though joined by a handful of spotters and a pair of air hose wranglers, those three operators were the sole source of movement. Obviously, there was a crew there for disassembling the heater, but as far as the move crew, it was only about five or six people.
“To me, probably one of the coolest things about all this is how little training was needed for the operators to be successful,” says Manus. He explains that there are no 450,000-pound test weights sitting around to teach people how to run the equipment, how it was going to feel, and what they needed to do, especially when there’s a language barrier. “The move team consisted of one Indonesian, one Korean, and one Sri Lankan operating the drives. That tells you how intuitive the system is. You can take three people who have never seen a system like this, none of whom speak the same native language, and within a few hours they’re able to move over 400,000 pounds in 35 minutes 200 meters through a facility.”
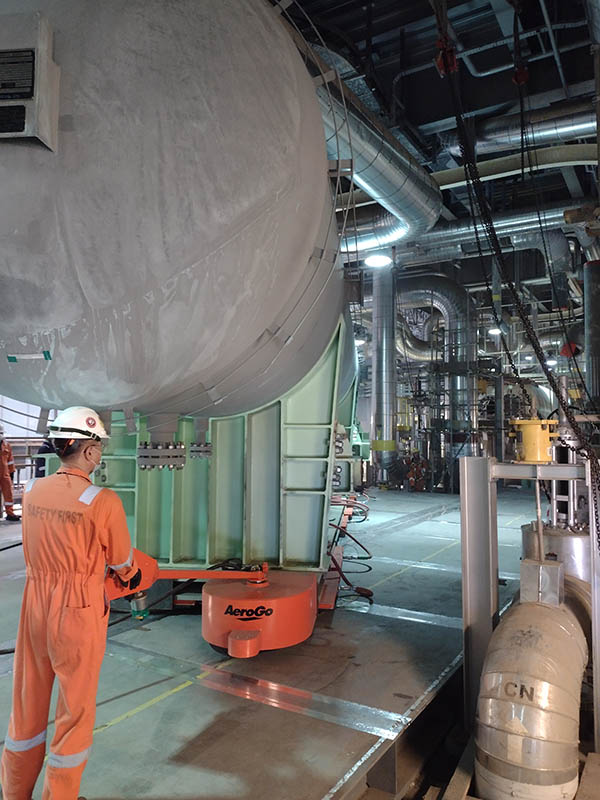
Manus notes that some preliminary training was necessary and that the first move required about two or three hours teaching the operators how to run the power drives. The next move, they completed in 35 minutes. “To me, that speaks volumes to the capability of the equipment that they can safely do something like that with a minimal amount of training,” says Manus.
Under ordinary circumstances, a move like this – enormously heavy equipment moving across delicate flooring through a difficult route it was never intended to traverse – presents an incredibly daunting task. Yet air casters made short work of the project, nimbly maneuvering the feedwater heaters with only minimal operators faster than any other material handling system could have managed. “There’s just nothing else out there that could do what the air casters did,” says Manus. “I’ve been doing this for 30 years and I am still amazed how this equipment can make what seems an impossible task, relatively simple.”