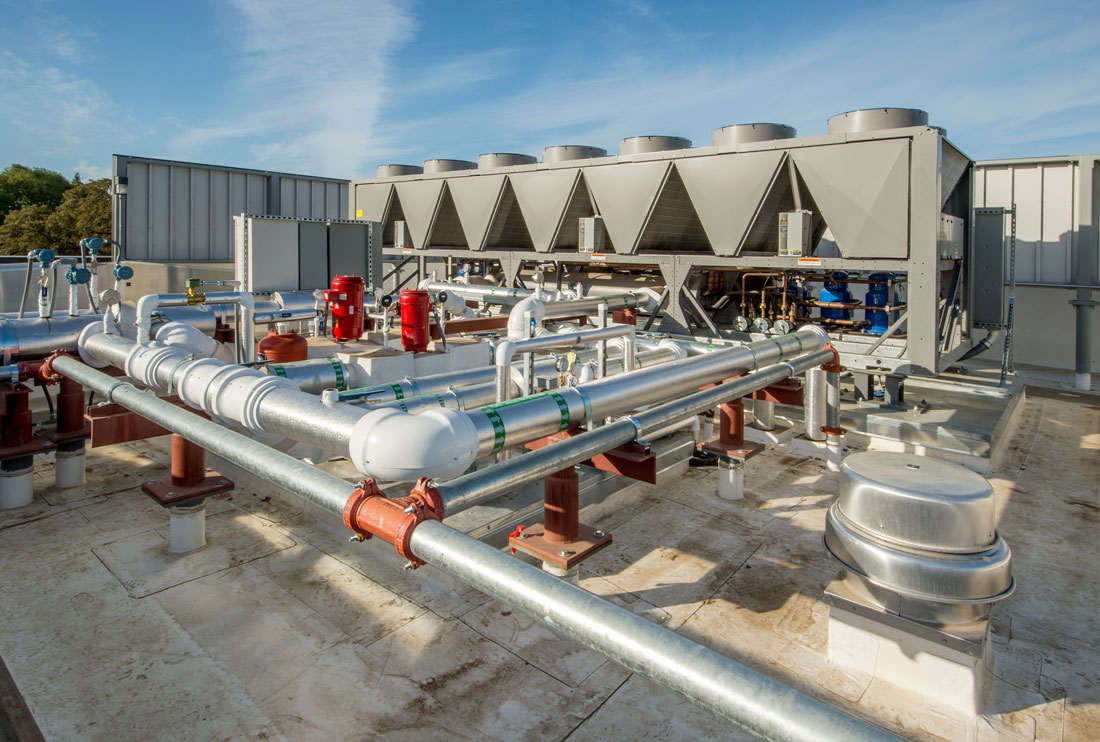
HVAC/R coatings are designed to protect the metal ‘tube & fin’ heat exchanger coil, which may be subjected to the stresses of an aggressive service environment, resulting in corrosion and the ultimate failure of the HVAC/R asset. Corrosion protection standards drive the development and determine the performance of coatings for this market estimated to be worth over USD 250 billion in 2022.
By Craig J R Thomas, HVAC/R Coating Specialist & Senior Managing Consultant – The Pipe-Sol Consultancy Ltd
A heat exchanger is a system used to transfer heat from one medium to another. Heat exchangers can be used in the process of both heating and cooling. One of the most widespread uses of heat exchangers is for air conditioning and refrigeration, which are commonly referred to as ‘coils’. Heating, ventilation, air conditioning and refrigeration (HVAC/R) systems employ various technologies to regulate temperature, humidity, and maintain air quality. HVAC/R systems provide heating and/or cooling for residential, commercial, industrial and institutional buildings. According to TechSci Research1, the global HVAC market was valued at USD 157.5 billion in 2018 and was projected to reach USD 253.8 billion in 2024. Using their CAGR of 8.39% during the forecast period, a market value of the worldwide impact of the Coronavirus Pandemic (2020-2021) has not been factored in. If the refrigeration market is included in the forecast, the HVAC/R market was valued at USD 181.1 billion in 2018, is estimated to be worth USD 254.2 billion in 2022 and is forecast to grow to USD 304.5 billion by 2024; the same caveat applies. These figures can be translated into an estimated 125+ million active HVAC/R units in 2022.
There are many types of HVAC/R unit such as air-cooled condenser units, air handling units, dry air liquid (air blast) cooler units, rooftop package units and split system units, and the vulnerable coil is what links them all. Coil types are extensive and include chilled and hot water coils, condenser coils, evaporator coils and steam coils. Coil designs are fewer in number and may encompass fin & tube, finned tube or microchannel specifications.
Acronyms
ACTS – Advances in Coatings Technology for Steel APEC – Advances in Performance Evaluation of Coatings
ASTM – American Society for Testing and Materials ISO – International Stand-ards Organisation
PACE – Performance of Alternate Coatings in the Environment
SPCC – Steel Structures Painting Council, known as The Society for Protective Coatings
HVAC/R asset protection
So, how can the investment made to design, build and install these HVAC/R assets be protected? Several tests have been developed and employed over the last 80 years to measure the effectiveness of coatings designed to protect the various metals utilised in the construction of these HVAC/R coil units from corrosion. These metals are typically aluminium, copper, (galvanised) iron and sometimes steel.
For the purpose of this article, primary consideration is given to aluminium-finned, copper-tubed HVAC/R coils, as these are most frequently specified on the grounds of heat transfer capability and cost. The casing is normally manufactured from galvanised iron. Aluminium and copper will require protection from corrosion, but arguably all three to maximise the life expectancy of the unit. Moreover, if not protected (or isolated) from each other, galvanic corrosion may occur. The salt spray (fog) test is arguably one of the most widespread and long-established corrosion tests used by industry professionals around the world. ASTM B117 was the first internationally recognised salt spray test standard and dates back to 1939. It became the “go-to” standard for many decades, as it was relatively inexpensive, provided a standardised (best) practice and, some postulated, was quick and quite repeatable.
As testing processes have evolved and more field data has been gained over the years, it has been statistically demonstrated that there is a weak correlation between the ASTM B117 salt spray test and a real-world environment. This article seeks to explore some of the reasons for this weak correlation to the real world, identify test standards in the process that provide a stronger correlation to the service environments in which HVAC/R units are expected to perform and highlight HVAC/R coating solutions that exist today, which will meet or exceed these standards.
ASTM B117
ASTM B117 specifies that scribed panels shall be placed in a salt spray cabinet at an angle of 15-30° from vertical and exposed to atomised salt spray solution comprising 5% sodium chloride (NaCl) with a pH 6.5 to 7.2 at 35°C ± 2°C (95°F ± 3°F) at 95-98% RH. For HVAC/R coating testing, aluminium panels are used, as this is one of the metals used to produce the coil fins, which if left untreated can corrode, although copper and steel can also be used. According to ASTM B117 each specimen shall be exposed to pH neutral salt fog at a fixed concentration at a fixed temperature for the uninterrupted duration of the test, which the standard does not prescribe. The test is continuous, static, and non-cyclic. For these reasons, it can be questioned whether such a test can actually mimic a real-world environment. At this point, the duration of static salt spray tests used by the HVAC/R industry should be mentioned. There has been a trend to let the tests run and run to demonstrate long-term / real-world coating performance. Test durations of 10,000 hours are not uncommon, with some reaching 17,500 hours+, although supporting test data are not always publicly available. 17,500 hours equates to almost 24 months of continuous exposure, and whilst this duration might seem like a reasonable and practical way to evaluate HVAC/R coating performance, there is nowhere on earth where the atmospheric conditions remain unchanged for months on end. Temperatures will rise and fall, humidity will change, UV intensity will vary, and freezing conditions will prevail, on top of which there will be the influence of chemical compounds such as sodium chloride (salt) and other man-made contaminants. Corrosion resistance is not chemical resistance, and chemical resistance is not tested unless otherwise specified.
To illustrate this point, HVAC/R coil manufacturers and their coating suppliers in the Middle East may have to contend with very high daytime temperatures of 40-50°C (104-138°F), low overnight temperatures falling below 0°C (32°F), varying levels of humidity depending on the season, a high UV Index of 10-12 and the hyper-saline conditions of the Persian Gulf. Its waters have an average salinity of 41g/kg2 with some areas exceeding 43 parts per thousand3. The concentration of salt in normal sea water is 35g/kg4. Although reliance on ASTM B117 has declined, it is still commonly used in the HVAC/R coatings industry forming part of many specifications and manufacturer testing protocols to demonstrate performance, even though ASTM stated itself: “Prediction of performance in natural environments has seldom been correlated with salt spray results when used as stand alone data”5.
Focus is given to ASTM B117 and ISO 12944-9, as these are the two test standards that are most actively used in the HVAC/R industry today, although other corrosion protection standards may be mentioned to provide context.
ISO 9227
ISO 9227 is almost identical to ASTM B117 and was first introduced in 1990. It is also a continuous, static Neutral Salt Spray (NSS) test and therefore also does not accurately simulate real world service environments. Perhaps the most significant difference between the two standards is a geographic one. ASTM B117 is published by ASTM and is therefore very widely used and accepted in the United States, although it does appear in international specifications and testing requirements, and ISO 9227 is published by the International Standards Organisation and is recognised globally.
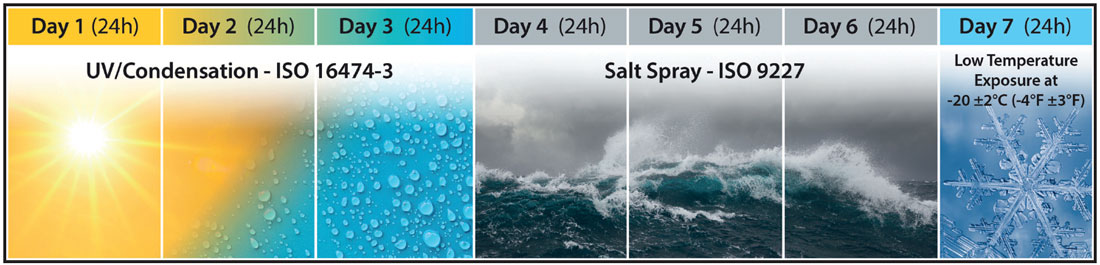
Standard references referred to in the article
ASTM B117-18 Standard Practice for Operating Salt Spray (Fog) Apparatus
ASTM D4587-11 Standard Practice for Fluorescent UV-Condensation Exposures of
Paint and Related Coatings
ASTM D5894-21 Standard Practice for Cyclic Salt Fog/UV Exposure of Painted Metal,
(Alternating Exposures in a Fog/Dry Cabinet and a UV/Condensation
Cabinet)
ASTM G85-19 Standard Practice for Modified Salt Spray (Fog) Testing
ISO 12944-2:2017 Paints and varnishes — Corrosion protection of steel structures by
protective paint systems.
Part 2: Classification of environments
ISO 12944-9:2018 Paints and varnishes — Corrosion protection of steel structures by
protective paint systems.
Part 9: Protective paint systems and laboratory performance test
methods for offshore and related structures
ISO 16474-3:2021 Paints and varnishes — Methods of exposure to laboratory light
sources. Part 3: Fluorescent UV lamps
ISO 20340:2009 Paints and varnishes – Performance requirements for protective paint
systems for offshore and related structures
ISO 9227:2017 Corrosion tests in artificial atmospheres – Salt spray tests
ISO 12944-9
ISO 12944 was first introduced in 1998 as an eight-part standard and was revised for a second time in 2018, which included the addition of Part 9. The required laboratory performance test methods are defined in Part 6 and form a series of cyclic tests depending on the specified corrosivity category up to C5 (as defined in ISO 12944-2). ISO 12944-9 specifies the performance requirements for protective coating systems for offshore structures, establishing a new ‘CX’ category. The duration of the exposure cycle is one week (168h) and is shown graphically in Figure 2. The standard specifies 25 full cycles or 4,200h.
The laboratory tests as specified in ISO 12944-9 did previously exist under ISO 20340, but this standard was withdrawn when ISO 12944-9 was created.
ISO 12944-9 is currently one of the most demanding corrosion protection standards that exists for highly aggressive offshore marine environments, and it is a cyclic test. If a coating passes CX testing, it will also meet C5/C4/C3 performance requirements. ISO 12944-9 is a more suitable test compared to and represents an improvement over ASTM B117, as it better replicates a real-world environment with varying exposure to UV (sunlight), condensation (moisture) and salt (water) spray as well as freeze-thaw weathering.
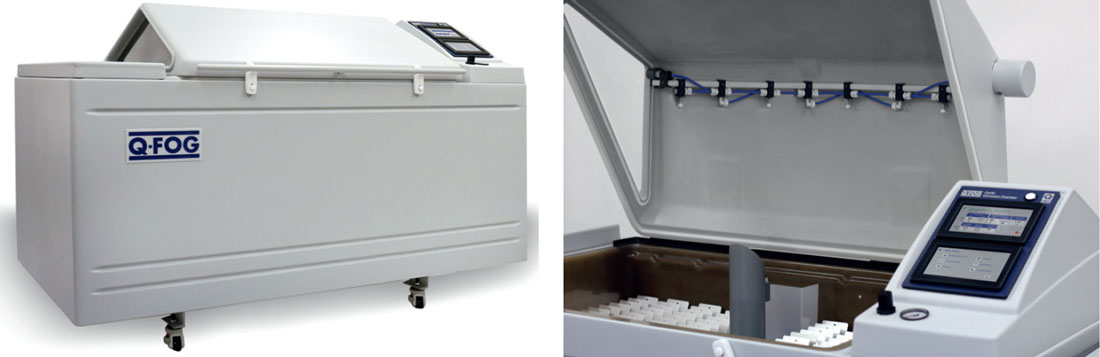
The need for real-world correlation
As previously mentioned, ‘rapid’ and ‘reproducible’ are both desirable attributes of a short-term coating performance test programme. ‘Relevant’ is another highly desirable attribute. Where short-term tests have been less than satisfactory in the past is the relevance of the data produced. Many accelerated tests, such as ASTM B117, do not replicate actual atmospheric conditions experienced in the real world of nature and therefore their value as a tool to determine the long-term effects of natural exposure to a coating in an ever-changing service environment is debatable. Boocock (SSPC) admits “with hindsight, it is obvious that ASTM B 117 salt spray (fog) testing, and similar methods offered a rapid but unreliable means for predicting coating behavior.”6
It is inherently difficult to mimic real atmospheric exposure conditions in a laboratory environment due to the random order in nature that the stresses of temperature, UV light, moisture (precipitation / condensation / humidity (time-of-wetness)), salt and corrosive agents can combine.
In 1994, SSPC began a joint programme with ASTM to evaluate accelerated testing methodologies to identify new and improved ways to better replicate actual service environments in which coatings had to perform. The SSPC/ASTM Round Robin had its research roots in three previous SSPC-sponsored programmes – PACE, ACTS and APEC. When conducting any such research into performance testing protocols, it is critical to evaluate the correlation of the results of the laboratory testing conducted versus the results of natural exposure experienced in the field. Analysis of PACE results first established that the correlation coefficient (R) of laboratory salt spray testing as per ASTM B117 versus severe exterior marine exposure was -0.116. To better understand what this means, consider that a perfect correlation would have an R value of +/-1.0, so a correlation coefficient of -0.11 would indicate an almost random relationship between the two variables (x – marine atmospheric exposure and y – salt spray exposure as per ASTM B117).
By using these simple statistical methods, SSPC realised that ASTM B117 was a “poor predictor of coating performance”.6 New cyclic tests were employed as part of APEC to improve predictive capability. Theory suggested that a coating’s ability to protect a metal substrate against corrosion is reduced, as it degrades from UV exposure and that different atmospheric processes can and do combine in nature, so the most noteworthy of the new tests was cyclic salt spray (modified ASTM B117) combined with UV/condensation exposure (ASTM D4587). It was already known that the R value for conventional salt spray was -0.10997,8 (-0.116). Interestingly and perhaps surprisingly, cyclic salt spray delivered an R value of 0.0657,8 so only a marginally better correlation. The R value for cyclic salt spray combined with UV/condensa-tion exposure was 0.69937,8 This correlation coefficient is dramatically stronger and shows that there is “an impressive improvement in correlation between artificial and natural performance”8 according to Boocock. This Cyclic Salt Spray/UV/Condensation exposure test also shows a highly significant correlation at the 95% confidence limit7,8 (P Value). The excellent research work undertaken by SSPC created a test method that delivered results with an R Value of 0.70 and a P Value of 95. The R2 value is 0.49, meaning that the correlation accounts for 49% of the data.
What is evident, and was even acknowledged by SSPC at the time, is that this test programme is still not ideal, but it lead to a revision to ASTM G85 in 1994 and the creation of ASTM D5894 in 1996, both of which are still used today. After 4 years of use, it was generally recognised that “ASTM D5894 is a substantial improvement to the traditional salt spray test (B117) in terms of reproducing atmospheric corrosion in an accelerated fashion.”9 Moving on 20 years, ISO 12944 is now also globally recognised and widely used; corrosion testing research/evaluation work continues.
HVAC/R coil coatings
HVAC/R assets can be protected from the most corrosive and perhaps chemically aggressive service environments through the application of a high performance HVAC/R coating to the coil unit.
It is not the purpose of this article to critique the products currently available in the market, however it is the author’s opinion that the HVAC/R coating that offers the highest level of corrosion protection (CX / Offshore) combined with superior resistance to the widest range of chemicals is a modified baked phenolic coating applied in a thin film to ensure the heat transfer of the coil is not unduly affected. The baked phenolic epoxy is applied by dipping (full immersion) to ensure the maximum coil penetration, although flooding (flow coating) and spray application methods can also be used. The coil is then baked in an industrial oven to effect full cure. This cure process, also called crosslinking, requires an elevated (metal) temperature for a specific length of time in order to establish the full film properties.
A baked phenolic epoxy HVAC/R coating will fully meet the requirements of ASTM B117 and now most critically ISO 12944-9, provide chemical resistance to a wide range of acids, solvents and inorganic salts as well as meet other end-user performance criteria.
Conclusion
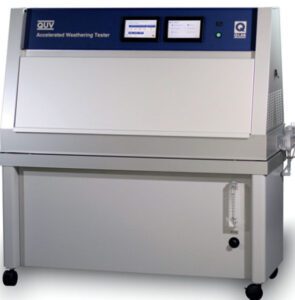
What is important in using or designing a specific laboratory test to determine coating performance and therefore predict the effectiveness of the coating to protect a HVAC/R asset in the real world is that the test should factor in all of the principal stresses of the service environment on the coating under consideration. Industry experts and coating specialists continue to agree that a combined cyclic corrosion and weathering test remains the best approach, as this correlates most closely and therefore most accurately mimics actual atmospheric conditions, in this case, in which the HVAC/R unit will operate. Additional tests can be added or conducted in parallel, such as chemical, freeze-thaw and UV-C resistance.
When I set out to write this article from a standpoint of information and data, both quoted and misquoted that already existed in some form, my aim as the author was to educate, and in some areas re-educate the HVAC/R industry in relation to corrosion testing and to provide commentary, what is relevant, what is not, what correlates, what does not, and why. In 2022, ISO 12944-9 exists as the corrosion protection standard against which all HVAC/R coatings for heat exchanger coils should be tested.
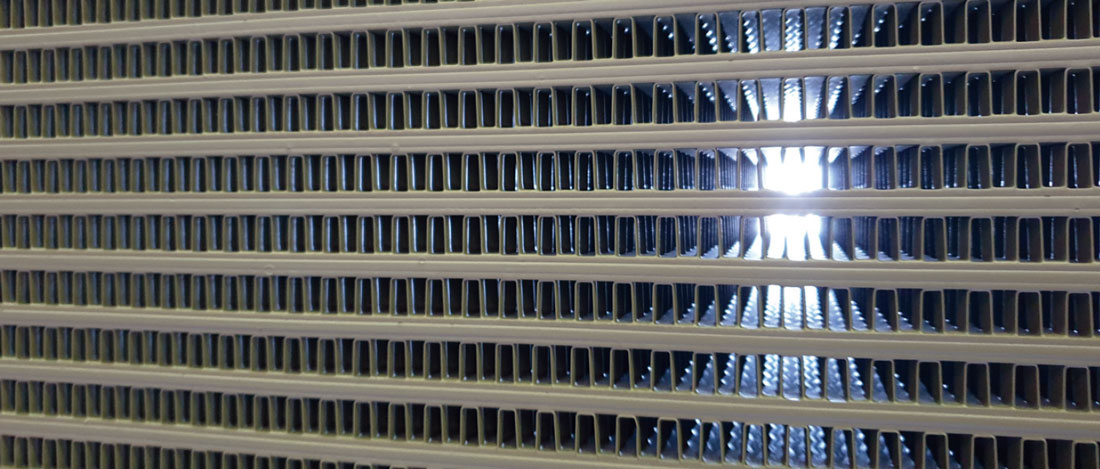
About the Author
Craig has over 20 years’ experience in the field of protective coatings and has worked with/for multiple world-leading coating manufacturers, including 3M, Copon/E Wood, Jotun and Kansai Paint. He is a certified NACE Coating Inspector (Level 1). He set up his own international consultancy business in 2016 and has focused most recently on HVAC/R coatings, undertaking a 2-year project for Heresite.
References
1 “Heating, Ventilation, Air Conditioning & Refrigeration (HVAC R) Market in Saudi Arabia”, HVAC R Expo Saudi 2020, TechSci Research, February 2020.
2 IBRAHIM, H. D., XUE, P. and ELTAHIR, E. A. B., “Multiple Salinity Equilibria and Resilience of Persian/Arabian Gulf Basin Salinity to Brine Discharge”, Frontiers in Marine Science, July 2020.
3 ALASWAD, S. O., DAWOUD, M. A., DAWOUD, R. M. and EWEA, H. A., “Towards sustainable desalination industry in Arab region: challenges and opportunities”, 4th International Water Desalination Conference: Future of Water Desalination in Egypt and the Middle East, 24–27 February 2020.
4 “How Much Salt is in the Ocean?”, www.americanoceans.org/facts/how-much-salt-in-ocean, Accessed: 29 March 2022.
5 American Society for Testing and Materials [ASTM] (2018), ASTM B117-18 Standard Practice for Operating Salt Spray (Fog) Apparatus, ASTM (Online), Available at https://www. astm.org
6 BOOCOCK, S. K., “Meeting Industry Needs for Improved Tests”, Journal of Protective Coatings & Linings, September 1995.
7 BOOCOCK, S. K., “A Report on SSPC Programs to Research Performance Evaluation Methods”, Proceedings from SSPC Conference on Evaluating Coatings for Environmental Compliance
(SSPC 94-14), June 1994.
8 BOOCOCK, S. K., “A Report on SSPC Programs to Research Performance Evaluation Methods”, Journal of Protective Coatings & Linings, October 1994.
9 WELDON, D. G., “Problem Solving Forum: Which Accelerated Test Is Best?”, Journal of Protective Coatings & Linings, August 2000.