In the world of stainless steel tubes, the name Mannesmann resonates with a legacy of innovation, quality, and excellence. Heat Exchanger World sat down with Denise Caspar, Business Development Manager for CPI & Energy, Vitali Zeis, Sales Director, and Tim Wallbaum, R&D and Sustainability Manager, to learn the recipe for success behind the company’s remarkable contribution to heat exchanger technology and its ambitious stride towards sustainability.
By Iryna Mukha, Heat Exchanger World
The Mannesmann legacy
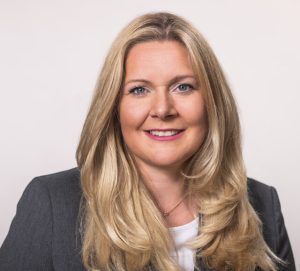
Denise Caspar begins our story with a nod to history, “Mannesmann Stainless Tubes stands on the shoulders of giants, Reinhard and Max Mannesmann, the inventors of the world’s first rolling process for seamless tubes in 1885.” This invention marked the dawn of a new era, and in the ensuing years, Mannesmann not just flourished but expanded through strategic mergers, notably forming DMV alongside the Dalmine-Group (now known as Tenaris) and the Vallourec-Group. “This merger,” Denise emphasizes, “was a testament to our diverse and profound expertise in this old yet dynamic industry.”
As Mannesmann continued to evolve, they acquired the DMV shares of both Dalmine and Vallourec and, in 2008, the company took its final form as Salzgitter Mannesmann Stainless Tubes. Everyone within MST cherishes their history as it reflects everything the company stands for today. According to Denise “Our evolution highlights the diversity and the know-how of the MST company today. At that time, the three main big European seamless stainless tube producers combined their expertise and experience in this industry, upon which we continue to build to this day.”
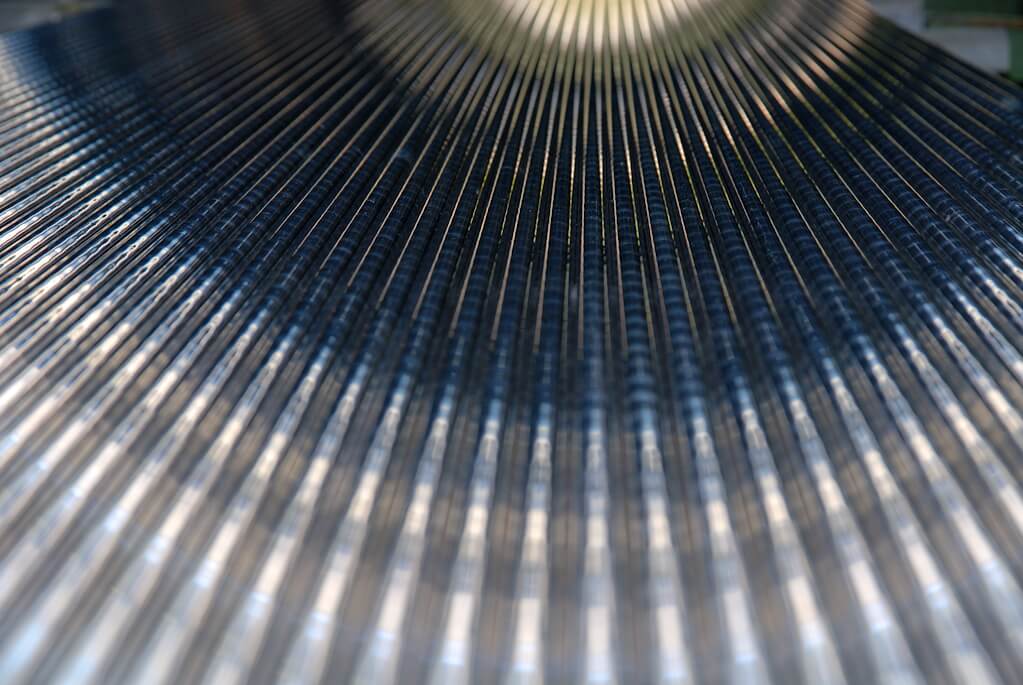
Serving diverse industry needs
In a landscape where precision and quality are paramount, MST stands as a beacon of excellence. The company’s product offerings are powered by a dual approach to production processes, as Denise explains. “At the core of our operations, we have two primary processes: the hot finishing process and the cold finishing production process.”
The hot finishing process, according to Denise, is notable for its productivity and capability to yield products with diameters ranging from 33.4mm to an impressive 280mm, and wall thicknesses spanning from 2.7mm to 50mm. “This size range combined with our possibilities to comply with norms and customer specifications is unparalleled largely thanks to the availability of many additional processes such as stabilized heat treatment,” Denise notes.
Essential to achieving outstanding mechanical and corrosion-resistant properties, these treatments ensure a product line that is as durable as it is diverse. “Our dedication to maintaining a stable and homogenous microstructure across our tubes enhances the overall product quality significantly.”
Beyond the impressive scope of their hot finishing capabilities, Mannesmann’s cold finishing process brings another layer of technical mastery into the fold. “Through cold pilgering or cold drawing techniques, we’re able to offer outer diameters from 1.6mm up to 245mm and wall thicknesses starting from .05mm up to 40mm.” The sheer range of dimensions available speaks volumes of the flexibility and adaptability at Mannesmann’s disposal, enabling the company to service a multitude of industries with highly specific needs.
“By understanding the full chain of our tube DNA combined with industrial needs, MST is the right technology-driven partner to develop tubes with beneficial features,” says Denise. “It is important to understand that the supply chain for a seamless tube manufacturer does not end with the delivery of the tube itself. To develop tube solutions beyond the industry challenges, the MST materials must be able to stay in critical temperature zones even longer. Especially with the focus on assembling by welding without building critical precipitations in the microstructure which would leads to massive degradation of the tubes during operation.”
Highlighting their commitment to quality, Denise further asserts, “In addition to hydrostatic testing, we perform any kind of non-destructive examination on the tube you can imagine ensuring our customers receive excellent quality tubes at the end.” This meticulous approach to quality assurance cements Mannesmann’s reputation as a trusted provider in the steel tube market.
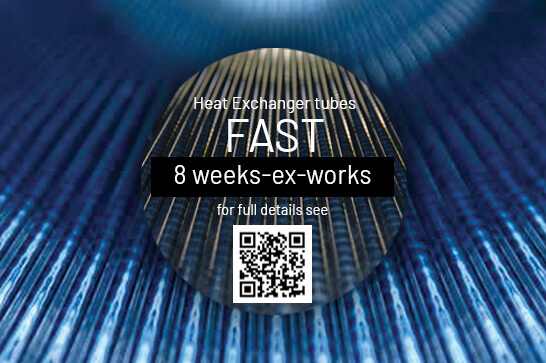
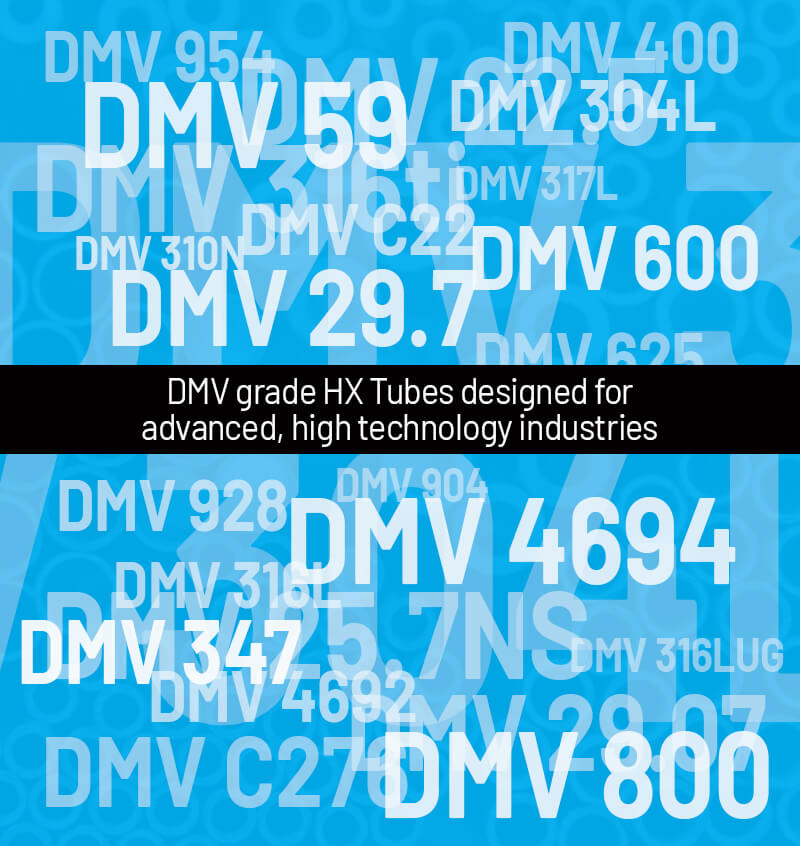
Global presence, local impact
One of the key focuses of MST that makes it stand out in the world of manufacturing is not just its comprehensive range of products but also its dedicated effort to ensure that local markets benefit from its global reach. According to Vitali Zeis, the company’s strategic setup allows it to cater to a diverse clientele with remarkable efficiency. “We have five mills in total located in key markets around the world including Germany, Italy, France, the United States, and India,” Vitali begins, laying down the foundation of their expansive operations.
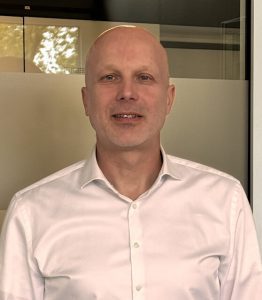
The footprint of Mannesmann spans across three continents, each location serving a unique purpose yet all interlinked to form a robust network. The German mill boasts a hot extrusion press and cold finishing facilities, while their Italian mill focuses on specialties like heat exchanger tubes and boiler tubes, tailored for cold finished products up to 89mm in external diameter. France hosts two of their mills; one equipped with a significant hot extrusion press, and Mannesmann SOTEP, acclaimed for its specialty in aerospace and industries like gas and nuclear, thanks to its advanced cold finishing capabilities. The US mill in Houston mirrors the Italian facility’s products but caters exclusively to the American market. “Our presence in these strategic locations allows us to ensure that we’re not just a global entity but a locally impactful partner,” Vitali explains. The emphasis on local impact is further illustrated by their innovative fast heat exchanger program launched a couple of years ago, primed to address urgent needs for tube replacements during unplanned outages. “This program, leveraging our mill in Italy, offers heat exchanger products across a variety of sizes in austenitic stainless, duplex, and super duplex materials with delivery times as quick as 8 weeks,” he adds. What further strengthens Mannesmann’s commitment to local markets is their adaptive approach towards material stocks. “We continuously adapt our raw material and hollow stocks to enable ourselves to offer very competitive lead times, for materials not covered by the fast heat exchanger program as well,” states Vitali. This adaptability ensures that needs beyond the fast 8-weeks-ex-works program are also met promptly, leveraging the comprehensive stocks of raw materials and hollows.
Elevating sustainability to new heights
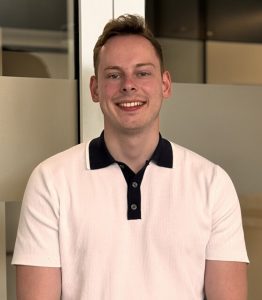
Mannesmann Stainless Tubes has recently been awarded the prestigious ECOVADIS silver medal, a recognition that underscores the company’s commitment to sustainability, ethics, and human rights. Tim Wallbaum, the company’s R&D and Sustainability Manager shared key insights into the company’s sustainability efforts, highlighting the strides MST is making toward a greener future.
“We are proud of this achievement,” Tim begins, “It’s a testament to our ongoing efforts across all our plants and various departments in Europe and the United States.” This acknowledgment by ECOVADIS positions MST as one of the leading figures in sustainability within their sector, an accolade the company doesn’t take lightly.
“It’s not just a title; it’s a reflection of our consistent sustainability strategy that we’ve meticulously developed and implemented over the years,” Tim adds.
A significant focus for MST in their sustainability crusade has been decarbonization. “In light of the pressing overproduction of greenhouse gases, it’s imperative for organizations to take charge in reducing their carbon footprint,” Tim states firmly. This resolve led to the establishment of a dedicated decarbonization team at MST, integrating efforts across various departments and plants to spearhead initiatives aimed at reducing their environmental impact.
Tim shared the meticulous approach MST undertakes to quantify and address its carbon emissions. “We’ve conducted a comprehensive calculation of our corporate carbon footprint, adhering to the renowned greenhouse gas protocol, covering Scope 1, Scope 2, and importantly, Scope 3 emissions,” he explains. This thorough evaluation forms the foundation of their decarbonization strategy, ensuring transparency and accuracy in their pursuit to align economic and ecological interests harmoniously.
Concluding, Tim reflects on the broader implications of their ECOVADIS silver medal. “This recognition is more than an accolade; it’s a clear signal to our customers and partners that we’re deeply committed to not just delivering high-quality products but also driving sustainable development within our industry.” Through their continued efforts in sustainability, MST is not just forging a path for themselves but setting a benchmark for the entire industry to follow.
Tradition of excellence and innovation
Touching on what shaped MST’s success the most over the years, Denise Caspar delves into company’s multiple pillars of success. “Key drivers for industries relying on heat exchanger tubes include efficiency and longevity of materials, with safety and reliability taking precedence to ensure stable process units, especially in the chemical process and petroleum refinery sectors.”
This insight points to the intricate balance MST strikes between offering high-grade products and supply chain costs, without compromising on the critical selection and availability of materials. Denise emphasizes, “Our company’s approach is clear. We do not compromise with lean chemistries, understanding the necessity of a meticulously engineered material grades to maintain the essential self-healing effect of stainless steels.”
Furthermore, Vitali Zeis asserts MST’s diverse array of materials and customized solutions which bolster its stronghold in the business. “We pride ourselves on offering a vast range of materials, including over 50 different alloys, and the ability to produce very long tubes with U-bending facilities in-house,” Vitali states, showcasing the company’s comprehensive suite of offerings.
He further underscores the importance of meticulous quality control—from steel quality and alloying concepts to heat treatment and non-destructive examination—ensuring that MST’s products can withstand the most hostile conditions of high pressure, temperature, and corrosion found in industries like nitrogen and phosphorus-based fertilizer production.
An attractive feature that speaks to MST’s clients is its commitment beyond just manufacturing. “It’s important to drill down into the quality of our products… It’s not solely about our production process, but about specializing our applications for CPI or Energy sectors to truly underscore the value proposition of Mannesmann Stainless Tubes beyond being a seamless stainless tube producer,” Denise adds, inviting deeper discussion on the applications of MST’s products in specialized areas.
This comprehensive approach, supported by a wide variety of sophisticated materials and an ability to cater to complex, demanding projects, positions MST as a leader in its field. The company’s dedication to not just meeting but exceeding the exacting standards of various demanding industries underscores its commitment to quality and excellence. The company’s strategic positioning at the intersection of technology, material science, and customer-centric solutions in the competitive landscape of heat exchanger manufacturing is the testament to their reputation as a reliable partner within the industry.
Conclusion
The Mannesmann Stainless Tubes narrative is one marked by a relentless pursuit of excellence and innovation. From their historical invention that revolutionized the industry to their current strides in sustainability and technology, they’ve consistently set the benchmark for quality and reliability. It’s evident that Mannesmann’s contribution to the heat exchanger world goes beyond mere product offerings. It’s about creating a legacy of unparalleled service, enduring quality, and sustainable practices that not only withstand the test of time but also lead the charge towards a greener and more efficient future.
About this Featured Story
This Featured Story was first published in Heat Exchanger World Magazine in July 2024. To read more Featured Stories and many other articles, subscribe to our print magazine.
Featured Stories are regularly shared with our Heat Exchanger World community. Join us and share your own Featured Story on Heat Exchanger World online and in print.