This case study highlights the design choice of Cipriani PHE heat exchangers to ensure energy efficiency and heat recovery within a data centre.
Text & images by Cipriani PHE
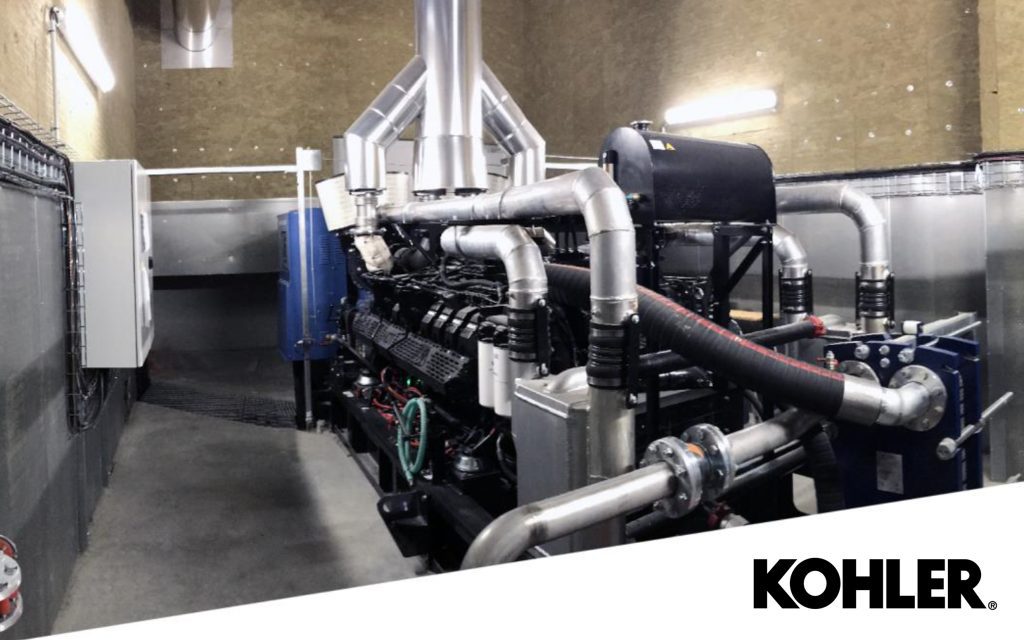
Industrial technologies based on IoT (internet of things), artificial intelligence, data collection and analysis phases, online security, digital communication, and social networks are now topics of public domain.
However, they do not concern only the activities of international companies and global markets, but more and more often involve people in everyday life. All these activities have one thing in common, the need to have a digital space in which to save data. The exponential growth of all these areas inevitably leads to the growth of data centres. Firstly, what is a data centre? It consists of a physical space connected to the network that allows users and companies to store and share data worldwide. These servers must always be active, imagine what a blackout of even just five or ten minutes would entail, people would no longer have the possibility to exchange content or browse the internet, companies could no longer store documents with the risk of losing some of them.
To ensure continuous operation, these machines need constant power supply and a cooling system that maintains the spaces at a preset temperature, avoiding overheating and consequent damage to the system.
The heat exchanger in a data centre
The plate heat exchanger plays a key role and can be inserted in different applications within a data centre. The main and most well-known function is certainly that of liquid cooling, but it is not the only one; in fact, it can be used both in power generation to avoid power interruptions and in heat recovery from servers. As for the cooling part, initially data centres were cooled by air. However, the growing demand and the development of increasingly complex and powerful technologies have led to a change of direction, preferring the greater efficiency of water cooling or in combination with other special fluids. In some unique data centres, components are even immersed in the cooling fluid, precisely to increase its effectiveness. In a data centre, compliance with temperatures is very important, the temperature values must have a precision of about half a degree, and that is why plate heat exchanger technology is optimal, thanks to its high efficiency combined with a reduced footprint. In this article, we will go into more detail on two lesser-known applications, thanks to customers like Kohler and Artek VVS, who have been using the heat exchanger to ensure continuity of electricity in the former case and recover heat from the server in the latter.
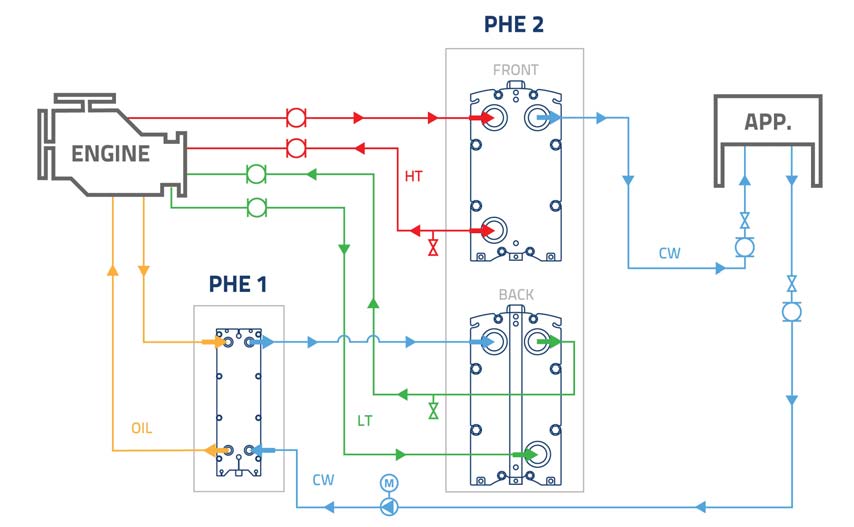
Expansion of a data centre in France using a Kohler KD SERIES generator
The demand for “digital space” has been growing exponentially in recent years. To meet this demand, there are two possibilities: create new data centres or expand existing ones. In this case study in France, the client needed to ensure increased electrical continuity to meet the needs of additional servers. Data centres are categorized based on their effi ciency, one of the evaluation parameters is the TIER: TIER I (guaranteed availability at 99.671%), TIER II (at 99.741%), TIER III (at 99.982%) and finally TIER IV, with a guaranteed availability of 99.995%, which translates to a maximum of 0.4 hours of interruption per year. The 1800 kVA reserve power plant from Kohler thus becomes a fundamental element to ensure electrical continuity to the French data centre. To ensure maximum performance of data centres while reducing the risks of inactivity, it is necessary to ensure a constant supply of electricity as well as adequate and precise cooling temperature. To ensure a “no-break” in the electricity supply, independent generators are installed to act as backup in cases of interruption or decrease in normal electricity supply. Kohler has been able to combine the electrical need of the data centre with the opportunity to recover the heat dissipated by the engine for electricity production, thus achieving the practical resolution of the electrical need without further dispersing energy that can be recovered for various uses.
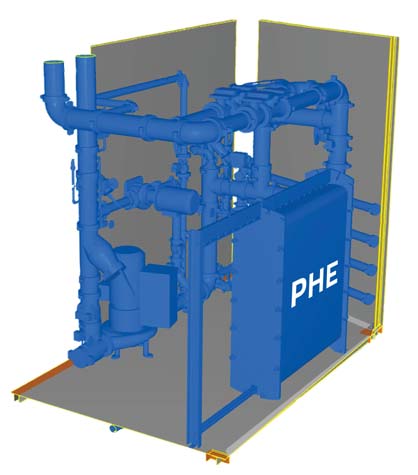
In this specific case, the know-how related to energy generation comes from the French company SDMO, founded in Brest in 1966. Since 2005, SDMO has joined the Kohler group, definitively taking its name from 2021. The unification under this brand reflects the ability to provide customers worldwide with quality, adaptability, and innovation, making Kohler the third largest generator manufacturer in the world. From gasoline or diesel or HVO generators to continuous or reserve power production systems, passing through domestic generators, soundproof and robust for the electric rental market and standard industrial generators, Kohler develops its solutions for all sectors where energy is needed.
Heat exchanger in cogeneration
Cipriani PHE, as a long-standing supplier of plate heat exchangers for the Kohler group, always creates tailor-made solutions for this type of application, trying to meet the different needs that arise in each project. Thanks to the knowledge gained over the years, internal technicians have planned for this solution the installation of a plate heat exchanger with gasketed plates, with the aim of optimizing the cooling needs of the engines and optimizing the spaces within the skid (an important element for the client and the contractor).
The plate heat exchanger plays a fundamental role in cogeneration plants, where an engine powered by gas or fuel (natural gas or biofuel in the most recent plants) generates electricity and thermal energy through an alternator mechanically driven. Through the heat exchanger, the thermal energy produced by the engine is recovered. The heat transferred to the engine cooling fluid is subsequently transferred to a secondary circuit that can be used for various purposes such as heating the environment. In this case, as reported by the exemplary diagram in the figure, the three-circuit high-efficiency plate heat exchanger was sized and realized to cool with a single cooling circuit (usually water or glycol water) a first low-temperature engine circuit and a second high-temperature one.
The thermal energy recovered from engine cooling could then be used for subsequent needs in the plant itself or transferred to other uses. The efficiency and customization of the plate heat exchanger therefore allow finding adequate solutions to situations where the engine circuit must be maintained at the correct temperature for constant and optimal performance and where physical installation space is necessarily limited. The recognized reliability of these generators is therefore also guaranteed by the quality of the exchangers, whose design and sizing are the result of careful and continuous discussions between customer and supplier.
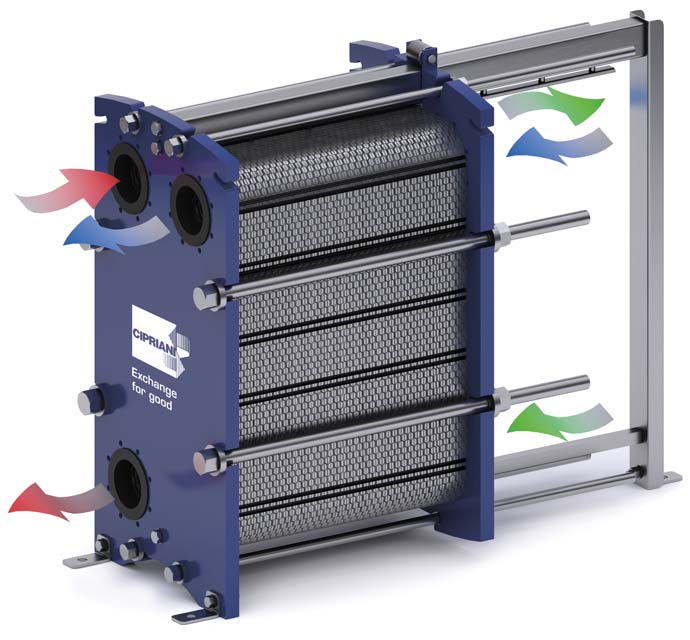
Heat recovery from a data centre in Norway to melt snow in the surrounding areas of the plant
Arktek VVS is a Norwegian company that deals with the design and construction of industrial plants throughout Northern Europe. It was founded in 1976 as Rørlegger`n i Son and over the years it develops more and more competences in the industrial field until it was acquired recently by Arktek VVS. For this last partnership, it collaborated with Cipriani PHE to insert a gasketed plate heat exchanger in a project for a 10MW data centre in Oslo. In this specific case, the heat exchanger uses hot water from the racks for a specific purpose: to melt snow on the roads surrounding the plant, which often causes inconvenience to the personnel working at the plant. For his function, two Cipriani PHE heat exchangers were installed, one of 300KW and one of 3000KW, with DN150 connections for flow rates from 80 l/s and temperatures between 11°C and 23°C. This solution falls into the category of “green” applications that recover energies that would otherwise be lost.
Innovative solutions like this allow to protect the environment twice: first because they recover waste energy from a process without having to resort to the production of new energy, and second because they do not disperse fluids or vapours causing possible changes in the surrounding environment. The plate heat exchanger thus proves in practice to be a key component for the efficiency of even new generation plants and is classified as a green machine that supports the performance needs of the plant by correctly exchanging energy and saving it as one of the necessary ways to safeguard the environment.
About Cipriani PHE
Cipriani PHE is the first Italian manufacturer of gasketed plate heat exchangers, tailor designed for every need and optimised for the most diverse industrial sectors. Since 1987, they have been producing their heat exchangers at their Verona site, controlling every stage-from conception to realisation to export.
About this Technical Story
This Technical Story was first published in Heat Exchanger World Magazine in March 2024. To read more Technical Stories and many other articles, subscribe to our print magazine.
Technical Stories are regularly shared with our Heat Exchanger World community. Join us and share your own Technical Story on Heat Exchanger World online and in print.