The renewable energy sector is pushing the boundaries of technology to deliver cleaner, more efficient solutions. One of the most significant challenges that project teams face is striking the right balance between thermal efficiency and pressure drop when selecting heat exchangers, all while meeting the growing demand for compact equipment. As many projects move toward modularisation, the importance of compact and highly efficient heat exchangers becomes paramount. This challenge is particularly evident in the development of supercritical CO2 (sCO2) power cycles for concentrated solar power (CSP) plants.
Text & images by Kelvion
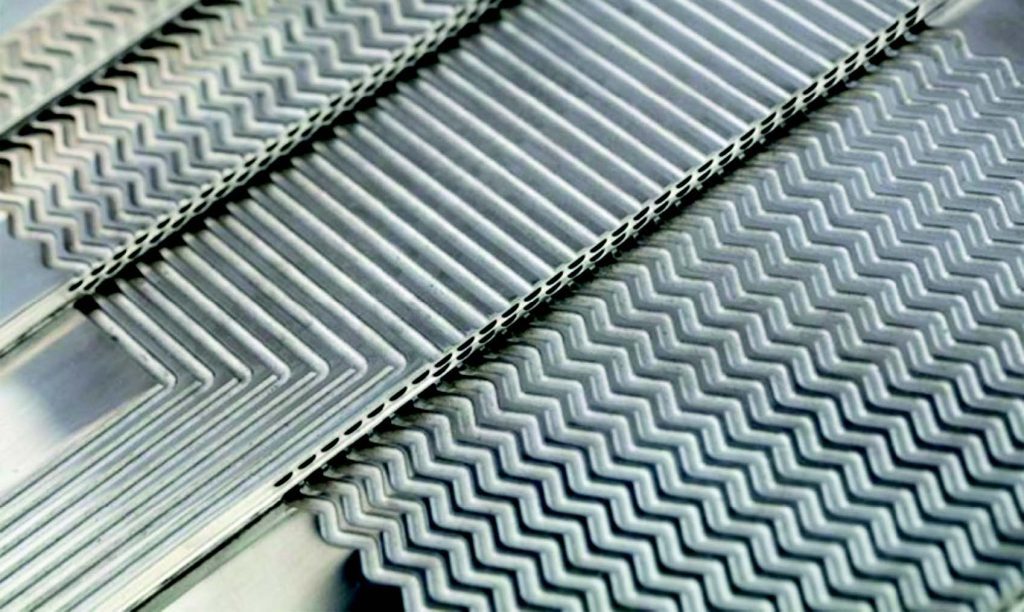
Kelvion, a global provider of heat exchanger technology, is pioneering solutions for the challenges faced by the renewables sector through innovative channel designs for printed circuit heat exchangers (PCHEs). By introducing a new PCHE channel pattern, Kelvion is transforming the performance of sCO2 power cycles, marking a significant milestone in the evolution of green technologies.
SCARABEUS project: the genesis of innovation
Kelvion’s journey towards redefi ning heat exchanger design began in 2019 with the SCARABEUS project, an initiative aimed at optimising sCO2 cycles for concentrated solar power plants (CSP). As part of this groundbreaking European research project, involving nine renowned industry and academic partners, the company committed itself to developing advanced solutions for blended CO2 cycles in CSP applications. The SCARABEUS project provided Kelvion with a platform to innovate and refi ne its K°BOND heat exchangers, specifically optimising the flow dynamics within PCHEs. “We improved the fl ow dynamic by innovating new internal shapes, departing from the conventional straight and zig-zag channels,” says Roy Niekerk, business developer at Kelvion. “The new pattern significantly reduces pressure drop while maintaining superior heat transfer coefficients.”
Supercritical CO2 power cycles: an emerging technology
Supercritical CO2 power cycles use carbon dioxide in a supercritical state, where it is above its critical temperature and pressure, making it neither a distinct liquid nor gas. This unique state offers several advantages for power generation. Unlike traditional steam cycles, which use water or steam as a working fl uid, sCO2 cycles use CO2, which operates at lower critical pressures and with a higher fl uid density. These properties allow for more compact systems with smaller components, offering potential reductions in capital costs and plant footprint. [2] One of the major benefi ts of sCO2 cycles is their effi ciency. The near-incompressibility of supercritical CO2 at critical points signifi cantly reduces compression work compared to steam cycles, while the fl uid’s high critical temperature allows for effective heat rejection even at ambient temperatures. As a result, sCO2 cycles achieve higher thermal efficiency across various applications, from fossil fuels to renewable sources like solar and geothermal energy.
Innovating PCHEs
PCHEs are critical to the efficiency of supercritical CO2 power cycles. These compact, high-efficiency heat exchangers are produced using a combination of chemical etching and diffusion bonding technologies. Metal plates, etched with intricate fl ow channels, are stacked and bonded to form a solid block capable of withstanding high pressures and temperatures. This construction method allows for sophisticated channel designs that enhance heat transfer within a minimal footprint, making PCHEs an ideal choice for sCO2 power cycle recuperators. [1]
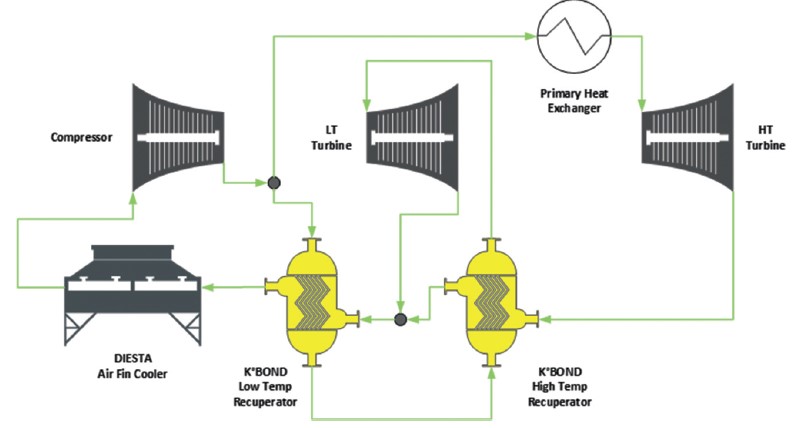
New channel patterns for enhanced efficiency
Traditionally, PCHEs feature either straight or zig-zag fl ow channels, depending on the specific characteristics of the working fluid. Straight channels are typically used for phase-change processes like evaporation or condensation, while zig-zag channels are preferred for single-phase fluids. However, research has suggested that alternative shapes, such as airfoil or S-shaped channels, could offer superior performance. But none comprehensively addressed all manufacturing and mechanical constraints. Indeed, the dimensions and arrangement of the shapes must align with the requirements of the chemical etching process and ensure sufficient contact surface to prevent any excessive deformation during the diffusion bonding of plates. Obviously, the design pressure (>200 bar) and temperature (>600°C) have also a significant impact on spacing and height of these shapes.
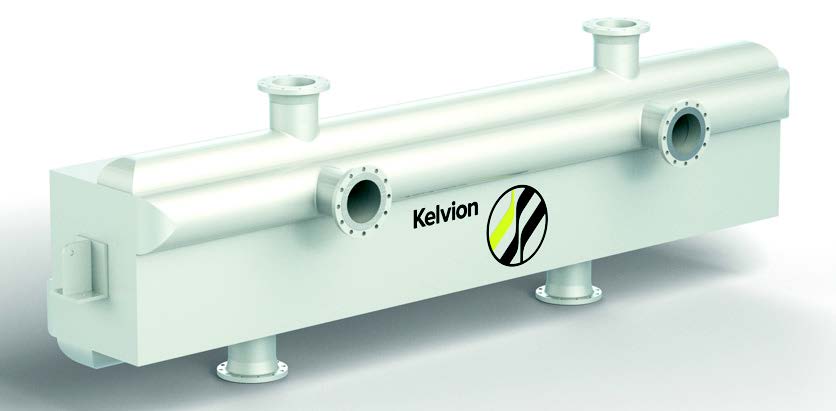
Kelvion took this insight further by developing an optimised channel pattern that balances manufacturing constraints with performance goals. Using advanced mechanical fi nite element analysis (FEA) and computational fluid dynamics (CFD), Kelvion’s engineers developed a new shape that reduces pressure losses while maintaining high heat transfer efficiency. The optimised pattern has been validated through testing at the Technische Universität Wien, where two prototypes—one with conventional zig-zag channels and one with Kelvion’s new design — were compared. “The results showed that the new pattern achieved up to 20% lower pressure drop while delivering equivalent heat transfer performance,” says Xavier Guerif, PCHE Product Line Manager at Kelvion. Alternatively, the new design could reduce the number of plates required by 10% without compromising efficiency.
Broader applications beyond sCO2 cycles
Kelvion’s advances in channel pattern design have the potential to benefit a wide range of applications beyond sCO2 power cycles. The improved effi ciency and reduced pressure drop of the new PCHE design can also be applied to:
• Natural gas compression
• Hydrogen compression
• CO2 compression
• Nuclear power plants
• Geothermal energy systems
These advancements demonstrate Kelvion’s commitment to delivering cutting-edge solutions that meet the evolving needs of the energy industry.
Conclusion
Printed Circuit Heat Exchangers (PCHEs) have emerged as the preferred technology for the recuperator section of supercritical CO2 power cycles, offering significant efficiency advantages over conventional steam cycles. With this newly introduced advanced channel pattern, these benefits are taken even further. By reducing pressure drop while maintaining superior heat transfer, Kelvion’s innovations promise to make sCO2 power cycles — and a wide range of other applications — more efficient, compact, and cost-effective.
References
- Edgar-Lane, Chris. Understanding printed circuit heat exchangers & the role of chemical etching. Precision Micro. [Online] [Cited: May 1, 2024.] https://www. precisionmicro.com/understanding-printed-circuit-heat-exchangers-the-role-of-chemical-etching/.
- Patel, Sonal. What are superctitical CO2 power cycles? Power Magazine. [Online] April 1, 2019.
https://www. powermag.com/what-are-supercritical-co2-power-cycles/.
About this Technical Story
This Technical Story was first published in Heat Exchanger World Magazine in October 2024. To read more Technical Stories and many other articles, subscribe to our print magazine.
Technical Stories are regularly shared with our Heat Exchanger World community. Join us and share your own Technical Story on Heat Exchanger World online and in print.