Fouling is the deposition of unwanted material on surfaces. In liquid-solid interfaces, fouling is of particular interest, as it can have several deleterious consequences. Predicting where and how fouling occurs is critical to designing heat exchangers.
By Isaac Appelquist Løge and Benaiah U. Anabaraonye
Fouling is present in private households and industries. In homes, it manifests as the accumulation of dust, limescale in kitchen appliances, or biofilm on unwashed surfaces. In industries, fouling is a challenge for oil and gas production shipping, heat exchangers, membrane technologies, and food production.
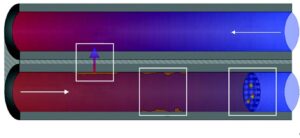
On ship hulls, the formation of crystals has been shown to severely increase the drag of a vessel, thereby increasing fuel consumption by up to 60 %. A layer as thin as 32 mm of fouling for heat exchangers can decrease the heat transfer efficiency by 25%.
Membranes used for freshwater production can be entirely put out of operation if the channels are blocked, and more than 25% of operating expenses are spent on pretreatment to reduce fouling. Some common examples of fouling and its consequences are illustrated in Figure 1.
A new approach
Until 1929, fouling was not dealt with in the academic community, and empirical and anecdotal references were the primary source of information. The Tubular Exchangers Manufacturing Association (TEMA) developed an empirical approach based on the heat resistance across the hot and cold sides of a heat exchanger.
The sum of these heat resistances could then be used to design the area of a heat exchanger. This method has been criticised widely due to its unphysical nature. Out of this criticism rose a new model developed by Kern and Seaton, which proposes a more mechanistic view of the underlying problem. They described mass accumulation over time as the difference between deposition and removal.
The Kern-Seaton model is the earliest approach in mechanistic fouling research and is still the basis of many models. In 1983, Epstein published a trendsetting paper summarising fouling in a 5×5 matrix.¹ Epstein classified fouling into five types (crystallite, particulate, chemical reaction, corrosion, and biological fouling) and five physical stages (initiation, transport, attachment, removal, and aging; see Figure 2).These stages have been used to expand the model of Kern and Seaton, where newer models consider initiation, transport, and attachment. We highlight key results from the main approaches in the literature.
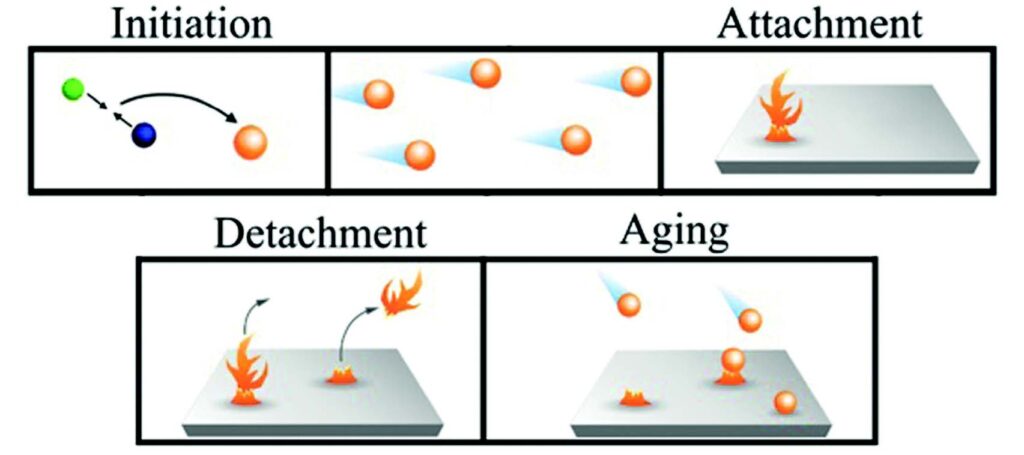
Artificial intelligence
Artificial intelligence is applicable in many scientific fields. Recent studies looked into the usefulness of neural networks in determining the fouling rate on heat exchangers. In a 2018 study, an artificial neural network was used as an alternative to complex and time-consuming experiments.² The researchers trained and validated their neural network against a databank of 11,626 datasets to estimate the fouling in a system, based on variables such as density, velocity, fluid and surface temperature, oxygen concentration, the hydraulic diameter of the passage, and time.
Through their model, they obtained results with a slight deviation from the datasets used for validation, which shows the practicalities of such a mathematical tool, and raises the questions of whether such tools could be implemented for design optimisation of heat exchangers. The limitations of this approach are that the physiochemical principles at play are not addressed and that it merely reproduces and extrapolates from already existing data.
Molecular dynamics
Molecular dynamics (MD) allows for a detailed investigated of the forces between particles and surfaces, and is well suited for fouling studies. In desalination, where thin-film reverse osmosis membranes play a crucial role, fouling is also a common problem, causing membranes to lose functionality over time. An MD study was performed on the antifouling performance of a polyamide-coated membrane.³
The researchers simulated the degree of crosslinking in the axial direction of the membrane to obtain a reactive, grafted surface through which the transport dynamics of water molecules could then be determined.
Two fouling agents were introduced in the flow, namely 1-ethyl-2-methyl benzene and n-decane, and through the membrane’s mean force, the surface’s inertness could be characterised.
Furthermore, through trajectory analysis of the fouling agents, they could relate the membrane’s inertness to the pollutant’s size, hydrophobicity, and polyamide coverage ratio of the membrane. This study highlights the opportunities to gain mechanistic information on the surface-adsorbent interaction through molecular dynamic simulations.
Computational flow dynamics
Computational flow dynamics (CFD) is a versatile tool, which have been widely used in fouling studies. CFD provides opportunities to study the physical interplay of surface stresses, flow velocity, and rheological properties. Figure 3 illustrates how mixing and transport processes could be understood through CFD in combination with results from experiments. CFD algorithm for heat exchanger systems must solve equations for mass transport, heat transfer, and chemical reactions in both the solution and on the surface, all while having a system that is evolving in time. Depending on the model’s complexity, multiple stages of the fouling process can be incorporated, ranging from complex nucleation schemes to temporal evolution of the properties of the fouling layers. Johansen and coworkers developed a model that aims to change how surface fouling is usually modelled.⁴ They challenge the popular two-step model, which calculates the transport to the surface and then the surface adsorption.
Instead, they proposed a wall function where the deposition is simulated as a mass sink at the walls. This model has been validated and showed good agreement compared to the traditional models. Due to the coarse mesh used in this model, it shows good promise for usage in industrial-scale applications where the system is of high complexity. One critical assumption in this model is that the wall acts as a mass sink, and therefore the inner diameter of the tube is unchanged with deposition. When reactions would occur over a long period, it is unlikely that the model would accurately describe reality. As more and more deposition would occur, the hydraulic diameter would shrink, effectively increasing the shear forces and thereby the contribution and importance of detachment.
Conclusion
AI, MD, and CFD can give insights into the mechanisms governing the rate of fouling. However, none of the published models have a detailed, unified description of all the five steps described in Epsteins 5×5 matrtix, and there exists experimental evidence suggesting that fouling is even more complex than previously anticipated.
We have shown that surface properties, saturation state, and flow velocity can influence detachment and aging in previously unreported ways.⁵⁻⁸ We have also shown that the interplay between all five stages of fouling for processes occurring over a longer time is not entirely understood. In the coming issues, we will present novel research on detachment and aging, and in the last issue, we will discuss the critical areas of opportunity for the modeling of fouling processes.
References
- Epstein. Thinking About Heat Transfer Fouling-A 5 x 5 Matrix. Heat Transfer Engineering, 4(1):43–56, 1983.
- Ke Li, Shanlong Li, Lifen Liu, Wei Huang, Yuling Wang, Chunyang Yu, and Yongfeng Zhou. Molecular dynamics simulation studies of the structure and antifouling performance of a gradient polyamide membrane. Physical Chemistry Chemical Physics, 21(36):19995–20002, 2019
- Sverre G Johnsen, Tiina M Pääkkönen, Stein Tore Johansen, Riitta L Keiski, and Bernd Wittgens. Implementation, demonstration and validation of a user-defined wall-function for direct precipitation foulingin ANSYS Fluent. Technical report, 2017.
- Ehsan Davoudi and Behzad Vaferi. Applying artificial neural networks for systematic estimation of degree of fouling in heat exchangers. Chemical Engineering Research and Design, 130:138–153, 2018.
- Løge, I.A., Anabaraonye, B.U. and Fosbøl, P.L. (2022) ‘Growth mechanisms of composite fouling: The impact of substrates on detachment processes’, Chemical Engineering Journal, 446, p. 137008. doi:10.1016/j.cej.2022.137008.
- Løge, I.A. et al. (2023) ‘Crystal nucleation and growth: Supersaturation and Crystal Resilience Determine stickability’, Crystal Growth & Design, 23(4), pp. 2619–2627. doi:10.1021/acs.cgd.2c01459.
- Løge, I.A. et al. (2022) ‘Scale attachment and detachment: The role of Hydrodynamics and surface morphology’, Chemical Engineering Journal, 430, p. 132583. doi:10.1016/j.cej.2021.132583.
- Anabaraonye, B.U. et al. (2021) ‘The influence of turbulent transport in reactive processes: A combined numerical and experimental investigation in a Taylor-Couette reactor’, Chemical Engineering Journal, 421, p. 129591. doi:10.1016/j.cej.2021.129591.
About the authors
Benaiah U. Anabaraonye is a research scientist and Program Manager at the Danish Offshore Technology Centre. He has a PhD in Chemical Engineering from Imperial College London.
Isaac Appelquist Løge completed a Ph.D. on crystallisation fouling, using novel methods to visualise fouling formation. He is currently researching what makes fouling detach and what makes it stick.
Isaac Appelquist Løge and Benaiah U. Anabaraonye will be publishing regular articles as part of a Research Series across multiple issues of Heat Exchanger World. All articles will be available in our online archive: https://heat-exchanger-world.com/category/technical-articles/