In our previous article, published in Heat Exchanger World’s July issue, we discussed recent advancements in modeling and prediction of fouling. In this article, we will emphasize the significance of surfaces in fouling processes and delve into the shortcomings of existing prediction models.
By Isaac Appelquist Løge and Benaiah U. Anabaraonye
Surfaces are ubiquitous, and play a critical role in the operation of heat exchangers. Since, the efficiency of heat transfer is determined by the surface area between fluids, fouling poses a major challenge, as deposited materials on surfaces will decrease efficiency. In this article, we will discuss how surfaces influence fouling rates and explore innovative surface-based mitigation approaches. Further, we will review why predicting fouling remains a challenge.
How surfaces affect fouling build-up
The morphology of a surface influences the rate of fouling. The presence of surface features, whether intentionally designed patterns or unintentional roughness, can give rise to unforeseen effects on fluid transport and reaction rates. Research indicates that surface roughness plays a significant role in determining the amount of deposition on a surface and the bonding strength of the foulant.
For instance, it has been demonstrated that removing fouling from a rough surface requires a force approximately 30 times greater than that needed for a smooth surface[¹]. The increased deposition on rough surfaces can be attributed to a higher number of sites for fouling formation, more ‘hooking’ sites, and improved advection resulting from interactions between the surface and the fluid.
In a recent study, we discovered that patterned surfaces have the potential to enhance overall deposition while concurrently increasing the frequency of detachment events. Local protrusions within a flow field can result in deposits that exhibit weak attachment to the surface, making them susceptible to easy detachment in the presence of fluid forces (see Figure 1)[²].
The complexity of fouling
Fouling is a complex process involving multiple mechanisms, including crystallization, particle sedimentation, and biofilm formation. The adhesive properties of these foulants can vary widely, from being tightly bound to the surface to being more elastic. This diversity in adhesion strength is crucial in determining how well the foulant layer withstands external forces. Unfortunately, current fouling models often overlook the intricate interplay of these multiple fouling modes. This oversight can lead to inaccuracies in predicting fouling rates and assessing the effectiveness of mitigation strategies.
In a recent study, we demonstrated how predictions of fouling rates are affected by crystal resilience. We investigated the impact of deposition order on the overall deposition rate in a system containing BaSO₄ and CaCO₃[³]. We found that when BaSO₄ was deposited first, it led to a twofold increase in the deposition rate of CaCO₃. Conversely, when CaCO₃ was deposited first, the subsequent introduction of BaSO4 actually displaced CaCO₃, resulting in an overall reduction in deposition (see Figure 2).
This observation is attributed to the relatively lower resilience of CaCO₃ to detachment forces compared to BaSO₄, highlighting that when the softer salt acted as a substrate, it facilitated detachment. Particulate fouling, characterized by the sedimentation of solid particles, exhibits weaker adherence to surfaces compared to crystallization fouling. Foreign solid particles can act as nucleation seeds by accelerating the rate of crystallization fouling. Consequently, fouling could be mitigated by filtering out these particles from the solution. However, the influence of particles on fouling is also dependent on their size, shape, and composition. In certain cases, particles can even exacerbate the erosion of already deposited fouling layer.
Biological fouling introduces an additional layer of complexity. Biofilms consist of colonies of microorganisms embedded in a polymeric matrix. They can amplify crystal formation, resulting in more build-up, and can even influence the properties of these crystals. Furthermore, biofilms can facilitate the adhesion of crystal nuclei to surfaces. When crystallization fouling grows beyond the biofilm layer, the crystals can protect the flexible biofilm, and a synergy is created between biological and crystallization fouling.
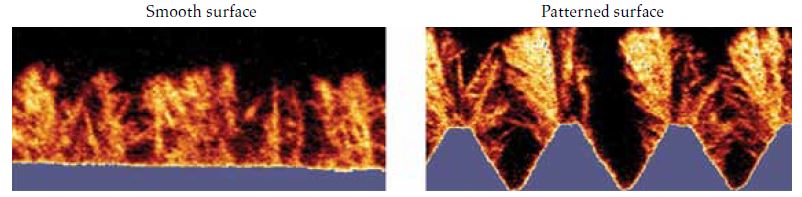
Surface modifications can be used to mitigate fouling
Surface engineering is a valuable strategy in the fight against fouling. This proactive approach involves designing surfaces to reduce attachment while concurrently enhancing detachment rates, offering promising solutions. Notable techniques within surface engineering include magnetic coatings, hydrophobic coatings, and patterned surfaces.
Liquid-infused surfaces (LISs) are biomimetic coatings known for their remarkable antifouling properties[⁴]. Nevertheless, the primary challenge lies in ensuring durability, as the coatings tend to degrade over time during operation. In response to this challenge, researchers have created resilient ferromagnetic coatings with a liquid-liquid interface. These coatings drastically reduced deposition rates and promoted easy detachment with increased shear stress. To further enhance longevity, these coatings have been seamlessly integrated into a gel structure[⁵].
Another innovative nature-inspired surface modification is referred to as the lotus flower effect. The lotus flower has a fractal-like surface structure, wherein each protrusion on the surface is replicated on a progressively smaller scale. This intricate arrangement results in a superhydrophobic surface. This hydrophobic nature gives rise to a self-cleaning effect, rendering it more challenging for weakly adhering crystals to persist on the surface.
Researchers have demonstrated that surfaces featuring numerous small curvy features outperformed those with protruded or inverted squared patterns in mitigating scaling issues[⁶]. This pattern was found to enhance detachment events, primarily attributed to the presence of heightened local shear stress. While surface engineering provides many benefits, challenges such as cost, durability, and potential environmental impact remain. Current ongoing research is dedicated to the pursuit of environmentally friendly, enduring, and cost-effective antifouling strategies.
![Figure 2. The order in which foulants grow is crucial. The figure shows an example where BaSO4 promotes CaCO3 growth, while CaCO3 promotes detachment of BaSO4. See more in[3]](https://heat-exchanger-world.com/wp-content/uploads/sites/19/2023/10/Predicting-fouling-Surface-effects.jpg)
The way forward
Surfaces play a pivotal role in fouling processes. However, many existing models fall short in capturing the complexities arising from the dynamic behavior of surfaces. Prediction errors can lead to expensive design errors. For instance, an overestimation of the surface area in a heat exchanger can significantly inflate the price of the unit. Therefore, models that can illuminate how fouling modes and surfaces intersect and influence each other are needed.
To advance our understanding and enhance model development, further experimental research is imperative. Research studies should focus on unraveling the adhesive interactions that arise from the interplay of diverse surfaces and fouling modes. With a deeper understanding of fouling, we can develop more effective strategies to combat it. Surface modifications through coatings and surface patterning present promising opportunities. As scientific exploration continues, we can expect to develop even more innovative solutions to fouling.
About the authors
Benaiah u. Anabaraonye is a research scientist and program manager at the danish offshore technology Centre. He has a phd in Chemical Engineering from imperial College london.
Isaac Appelquist Løge completed a Ph.D. on crystallisation fouling, using novel methods to visualise fouling formation. He is currently researching what makes fouling detach and what makes it stick.
Isaac Appelquist løge and Benaiah U. Anabaraonye will be publishing regular articles as part of their Research Series across multiple issues of Heat Exchanger World. All articles will be available in our online archive: https://heat-exchanger-world.com/category/technical-articles/.
References
- Keysar, S. et al. (1994) ‘Effect of surface roughness on the morphology of calcite crystallizing on mild steel’, Journal of Colloid and Interface Science, 162(2), pp. 311–319. doi:10.1006/jcis.1994.1044.
- Løge, I.A. et al. (2022) ‘Scale attachment and detachment: The role of Hydrodynamics and surface morphology’, Chemical Engineering Journal, 430, p. 132583. doi:10.1016/j. cej.2021.132583.
- Løge, I.A., Anabaraonye, B.U. and Fosbøl, p.l. (2022) ‘Growth mechanisms of composite fouling: The impact of substrates on detachment processes’, Chemical Engineering Journal, 446, p. 137008. doi:10.1016/j.cej.2022.137008.
- Villegas, M. et al. (2019) ‘Liquid-infused surfaces: A review of theory, design, and applications’, ACS Nano, 13(8), pp. 8517–8536. doi:10.1021/acsnano.9b04129.
- Masoudi, A. et al. (2017) ‘Antiscaling magnetic slippery surfaces’, ACS Applied Materials & Interfaces, 9(24), pp. 21025–21033. doi:10.1021/acsami.7b05564.
- Pääkkönen, T.M. et al. (2013) ‘Surface patterning of stainless steel in prevention of fouling in heat transfer equipment’, Materials Science Forum, 762, pp. 493–500. doi:10.4028/www.scientific.net/msf.762.493.