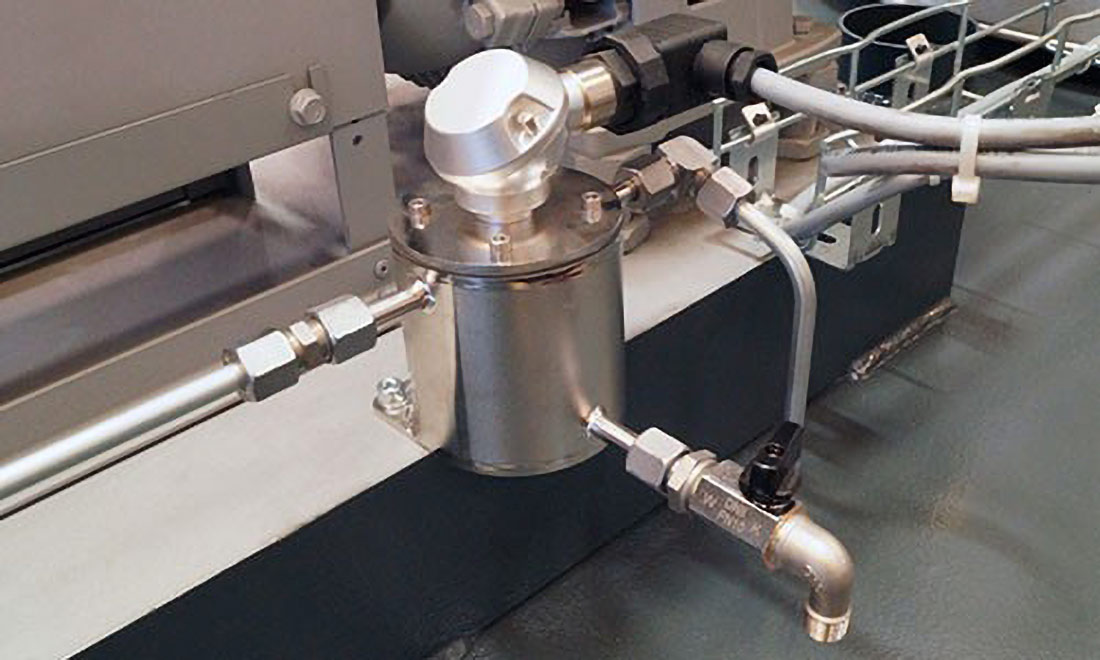
By Dominik Weidler, Chief Information and Technology Officer at NESS Wärmetechnik GmbH
Large-scale heating plants, although complex and exposed to high loads, can operate over long periods without interruption and with low maintenance. To achieve this goal two aspects are important.
The first aspect is a professional commissioning and maintenance of the pumps, which includes precise alignment of the pumps and venting the pumps before the commissioning and before each start-up.
In order to avoid and detect possible problems in the system at an early stage, one – and that is the second aspect – has to take monitoring into account during the planning phase. An important element here is pump monitoring, as the pumps are central to the function of the system. In heat transfer systems with liquid heat transfer media, the highest demands occur on the pumps of the system. Depending on the system pressure and the heat transfer medium used, the specifications of the optimal pump differ. In general, canned motor or magnetic drive pumps are technically the most suitable. At the same time, however, these pumps are significantly more expensive to purchase than classic pumps with mechanical seals. From a purely economic point of view, in many cases it even makes sense to use pumps with mechanical seals and – through additional monitoring – to compensate for the somehow higher risks.
Key factors
Three indispensable factors should be included in a pump-monitoring concept: Bearing temperature, pump vibration, and leakage quantity. These help to detect problems and wear on pumps at an early stage and to optimally integrate maintenance and repair into the production cycle. Due to the temperature and viscosity of the fluid used, pumps in such systems have to deliver high performance continuously over long periods. Leakage, vibration and rising bearing temperature are the most common disturbance factors in pump operation and therefore it is useful to monitor them. The monitoring modules described here should have three levels: Normal operation, alarm when approaching the limit values, and shutdown when exceeding the specified limit values. This not only serves for occupational safety and environmental protection, it also protects the pump unit and its immediate surroundings from damage and contamination.