Plate heat exchangers are essential components in fluid dynamics, efficiently transferring heat across diverse industries. And at the heart of these workhorses? Gaskets — the guardians of leak-free operation
By Lei Tao, HFM. Images by HFM.
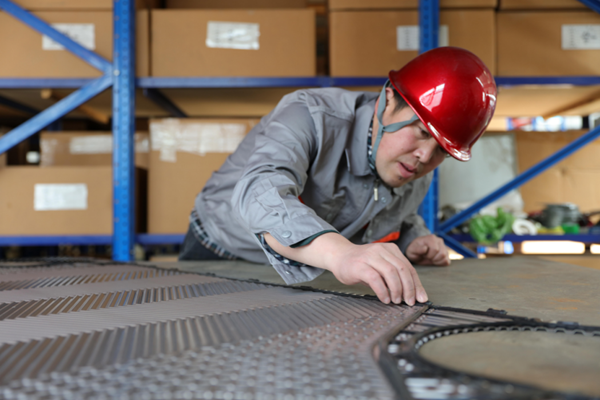
This article serves in understanding plate heat exchanger gaskets. We’re diving deep into material choices, sharing insider tips on installation, and exploring the secrets of a lasting gasket. From picking the perfect gasket material to understanding the subtleties of thickness and hardness, this guide is your key to optimizing performance and ensuring your plate heat exchanger stands the test of time.
Choosing the right gasket material
Plate heat exchanger gaskets are engineered from a diverse array of materials, each offering unique advantages. Let’s explore four common types: Nitrile Butadiene Rubber (NBR), Ethylene Propylene Diene Monomer (EPDM), Viton, and Chloroprene Rubber (CR). These materials are carefully selected based on their compatibility with specific operating conditions, including temperature. Understanding their distinct characteristics will enable you to make informed decisions for your plate heat exchanger’s optimal performance.
NBR (Nitrile Butadiene Rubber)
NBR gaskets are renowned for their exceptional compatibility with both water and oil-based fl uids. They are extensively utilized in plate heat exchangers across various industries, making them a reliable choice for ensuring leak-free seals. NBR is suitable for applications within a temperature range of 14°F to 230°F (-10°C to 110°C).
EPDM (Ethylene Propylene Diene Monomer)
Engineered to withstand the rigors of hot water, steam, and specifi c chemicals, EPDM gaskets stand out in high-temperature applications. They provide fl exibility and resilience, making them a preferred choice in environments with elevated temperatures. EPDM gaskets are capable of maintaining their integrity even when exposed to temperatures ranging from 14°F to 302°F (-10°C to 150°C), ensuring reliable sealing in demanding conditions.
Viton
In settings characterized by extreme temperatures and corrosive substances, Viton gaskets, a type of fluoroelastomer (FKM), stand out for their exceptional performance. Unlike standard elastomers, Viton gaskets offer heightened resistance to harsh elements, ensuring longevity and reliability even in the most demanding conditions. Notably, Viton gaskets encompass various formulations, including Viton A and Viton G, each tailored to specific temperature ranges and application requirements. For instance, Viton G is engineered to withstand temperatures ranging from 23°F to 338°F (-5°C to 170°C) and is particularly suitable for acidic environments, making it ideal for applications where both temperature fluctuations and corrosive substances are prevalent.
CR
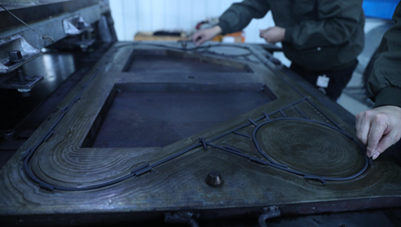
Primary vulcanization process at the HFM factory, molding raw rubber into durable gasketsChloroprene Rubber (CR) gaskets are prized for their remarkable resilience and durability, particularly in challenging environments. They boast excellent resistance to moderate chemicals and oils, making them ideal for various industrial applications. Additionally, CR gaskets typically operate within a temperature range of approximately 14°F to 212°F (-10°C to 100°C), ensuring reliable performance even in conditions with moderate temperature variations. With their exceptional resilience, durability, and temperature tolerance, CR gaskets provide reliable sealing solutions across diverse industries and applications. By comprehending the strengths and characteristics of each gasket material, including their temperature resistance, you’ll be empowered to select the most suitable option for your plate heat exchanger, ensuring its seamless operation.
Tailoring gaskets to operating conditions
Selecting the appropriate gaskets for your plate heat exchanger is crucial for ensuring optimal performance in varying operating conditions.
For applications with more moderate temperature requirements, materials like Nitrile (NBR) and EPDM can be suitable under normal circumstances, although their use should be based on their respective temperature ranges.
High-temperature applications: In environments with elevated temperatures, gaskets must maintain their integrity and seal to prevent leaks. Viton is a standout material known for its exceptional heat resistance. For example, in chemical processing plants where high temperatures are common, Viton gaskets reliably seal the system.
Additionally, in industries such as power generation where steam at high temperatures is prevalent, EPDMHT (Ethylene Propylene Diene Monomer High Temperature) and Viton G (FKM) gaskets are commonly utilized due to their superior sealing performance and heat resistance. EPDMHT, a variant of EPDM rubber, is specifically formulated to endure higher temperatures, making it suitable for demanding applications. Similarly, Viton G is renowned for its heat resistance, establishing it as a preferred choice for high-temperature environments.
Design considerations
This section delves into the fundamental gasket designs prevalent in plate heat exchangers: Clip-on, Glue-on, Snap-on, and Loc-in. These designs vary in their attachment mechanisms and appearance.
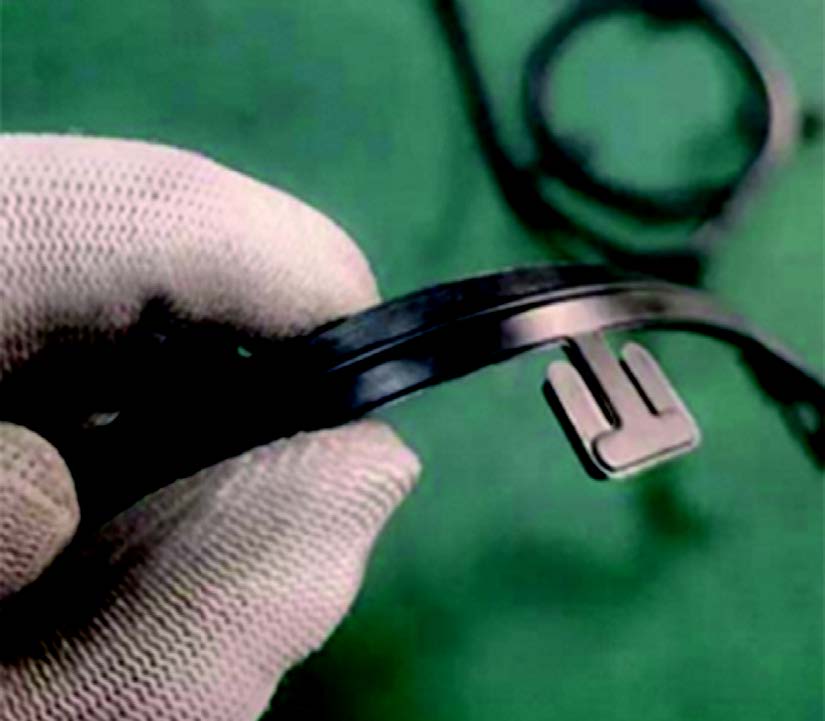
Types and Installations: Clip-on gaskets feature an attachment method where they clip onto the plate edges, providing convenience during installation. Glue-on gaskets are affixed using adhesive, while Snap-on gaskets securely snap into place upon installation. Loc-in gaskets are specifically engineered to be bonded into plate grooves for a secure fi t. It’s essential to note that while each type offers different installation methods, there are no inherent advantages or disadvantages in terms of factors like pressure or temperature resistance. However, Glue-on gaskets may not be preferred in the food industry due to concerns about potential contamination risks.
The role of raised inner bar (RIB): In gasket engineering, the presence of a Raised Inner Bar (RIB) serves as a strategic feature. This subtle ridge or bump along the inner perimeter of the gasket optimizes sealing performance. When compressed between mating surfaces, gaskets with RIBs benefit from enhanced stability and load distribution. The raised feature facilitates a more uniform distribution of compressive forces, mitigating the risk of localized stress concentrations and promoting a secure and reliable seal.
Gasket thickness and hardness
The effectiveness of a gasket in maintaining a reliable seal hinges on various factors, including its thickness and hardness. Striking the right balance between these elements is essential for preventing leakage and ensuring the longevity of the gasket.
Thickness: meeting pressure requirements: In high-pressure applications, thicker gaskets are often preferred as they provide enhanced resistance against the forces exerted, ensuring a secure seal. However, it’s crucial to strike a balance — excessively thick gaskets can lead to uneven distribution of pressure, potentially causing leaks.
Hardness: conformability for a secure seal: Softer gaskets exhibit greater conformability, allowing them to adapt to irregularities in the sealing surfaces. This characteristic is particularly advantageous when dealing with surfaces that may not be perfectly flat. However, it’s important to note that softer gaskets may be more susceptible to wear and compression over time.
Finding the optimal balance: Achieving the optimal balance between thickness and hardness is paramount. This balance ensures that the gasket maintains a consistent seal, even under challenging conditions. Consulting with experts or referring to manufacturer specifications can help in selecting a gasket with the appropriate characteristics for your specific application.
Installation and tightening: best practices
Proper installation and tightening of gaskets are critical steps in ensuring a reliable and leak-free seal. Following best practices during installation can significantly contribute to the overall effectiveness of the gasket.
Surface preparation: cleanliness is key: Before installing a gasket, it’s imperative to ensure that the sealing surfaces are clean and free from any debris, old gasket material, or contaminants. Any imperfections on the surface can lead to uneven pressure distribution and potential leakage.
Applying uniform pressure: During the installation process, apply uniform pressure across the gasket. This ensures that the gasket compresses evenly, creating a consistent seal. Avoid applying excessive force, as this can lead to gasket deformation and, ultimately, leaks.
Avoiding over-tightening: In the assembly process of plate heat exchangers (PHE), manufacturers typically provide specific tightening guidelines for securing the components. These guidelines include both maximum and minimum values for the tightening dimensions. It’s crucial to adhere to these guidelines diligently to ensure optimal performance and longevity of the PHE. Over-tightening, exceeding the specified tightening limits, can have detrimental effects on the performance of critical components such as gaskets. It may cause the gasket to deform, compromise its integrity, and potentially lead to leaks. Following the manufacturer’s recommended tightening guidelines and using calibrated tools for tightening are crucial steps in preventing over-tightening and maintaining the reliability of the PHE.
Regular Inspection post-installation: After installation, it’s advisable to conduct a thorough visual inspection to confirm that the gasket is seated properly and that there are no visible signs of misalignment or deformation.
Periodic retightening (if applicable): In certain applications, especially those involving thermal cycling or significant pressure fluctuations, periodic retightening may be necessary to maintain the integrity of the seal. This practice helps compensate for any relaxation of the gasket material over time.
Inspection and replacement: ensuring longevity
Regular inspection of gaskets is a crucial maintenance practice that ensures the continued effectiveness of the seal. Identifying signs of wear, damage, or degradation early on allows for timely replacement, preventing potential leaks and maintaining the efficiency of the plate heat exchanger system.
Visual inspection: A visual inspection is the first line of defence in assessing the condition of a gasket. Look for any visible indicators of wear, such as cracks, tears, or compression set. Pay close attention to areas where the gasket is in direct contact with the sealing surfaces.
Functional testing: In addition to visual inspection, functional testing can be performed to assess the integrity of the gasket. This may involve conducting pressure tests or leak tests to verify that the gasket is effectively sealing.
Gasket lifespan considerations: It’s important to note that gaskets typically have a lifespan of 1–2 years, depending on various factors including operating conditions and material quality. Therefore, it’s crucial to include gasket replacement as part of routine maintenance procedures.
Meeting industry standards
Compliance with industry-specific regulations is crucial to ensure the safety, quality, and environmental responsibility of your plate heat exchanger system. Gasket selection plays a pivotal role in meeting these stringent requirements.
Food processing industry: prioritizing hygiene and safety
In the food processing industry, gaskets must strictly adhere to rigorous hygiene and safety standards to safeguard the integrity of the final product. It’s imperative to note that gaskets applied with adhesive, commonly referred to as glue-on gaskets, are not suitable for food-related applications due to potential contamination risks. Instead, gaskets crafted from FDA-approved, food-grade Nitrile (NBR) and EPDM are the preferred choice. These materials are specifi cally formulated for food-grade applications and are certifi ed safe for direct contact with consumable products. For instance, in a dairy processing plant, Nitrile and EPDM gaskets, being Food Grade, FDA approved materials, play a crucial role in maintaining a hygienic and secure seal, ensuring the purity and safety of food products.
Petrochemical industry: managing hazardous materials
The petrochemical industry often handles hazardous materials, demanding gaskets that can withstand aggressive chemicals. Gaskets made from chemical-resistant materials like Viton are the preferred option. These gaskets provide an extra layer of assurance, ensuring the safety and integrity of the system, even in the presence of corrosive substances. For instance, in a petrochemical refinery, Viton gaskets are indispensable for maintaining a secure seal in pipelines carrying volatile compounds.
Conclusion
In today’s dynamic industries, efficiency and dependability are paramount, and the choice of gasket is foundational to achieving optimal performance. Gaskets are the backbone of plate heat exchangers, ensuring seamless operations. Selecting the right gasket involves a delicate dance of material compatibility, design finesse, and industry adherence, guaranteeing your system performs at its best.
About the author
Lei Tao (Steven Lei), in his role as HFM’s CTO, boasts over 8 years of expertise in plate heat exchanger design and technical support, including his ability providing large-scale thermal engineering solution. Lei’s dedication to practical innovation has led to significant advancements, particularly in optimizing gasket performance within heat exchangers. Notable for his contributions to engineering solutions, Lei holds utility and invention patents, reflecting his focus on pioneering technologies. As a leader, Lei maintains a steadfast focus on technical precision and industry-leading standards, driving advancements in heat transfer technology. He can be reached via email at leitao@hfm-phe.com.
About this Technical Story
This Technical Story was first published in Heat Exchanger World Magazine in July 2024. To read more Technical Stories and many other articles, subscribe to our print magazine.
Technical Stories are regularly shared with our Heat Exchanger World community. Join us and share your own Technical Story on Heat Exchanger World online and in print.