This article details the guidelines to identify and establish spare criteria for critical assets (Shell and tube heat exchangers tube bundles categorized as “High Risk”) in order to allow increasing the asset availability and minimize the equipment downtime due to lengthy and costly repairs.
By Miguel Gutierrez, Field Consultant Engineer at GME – Reliability Solutions Department in Saudi Aramco
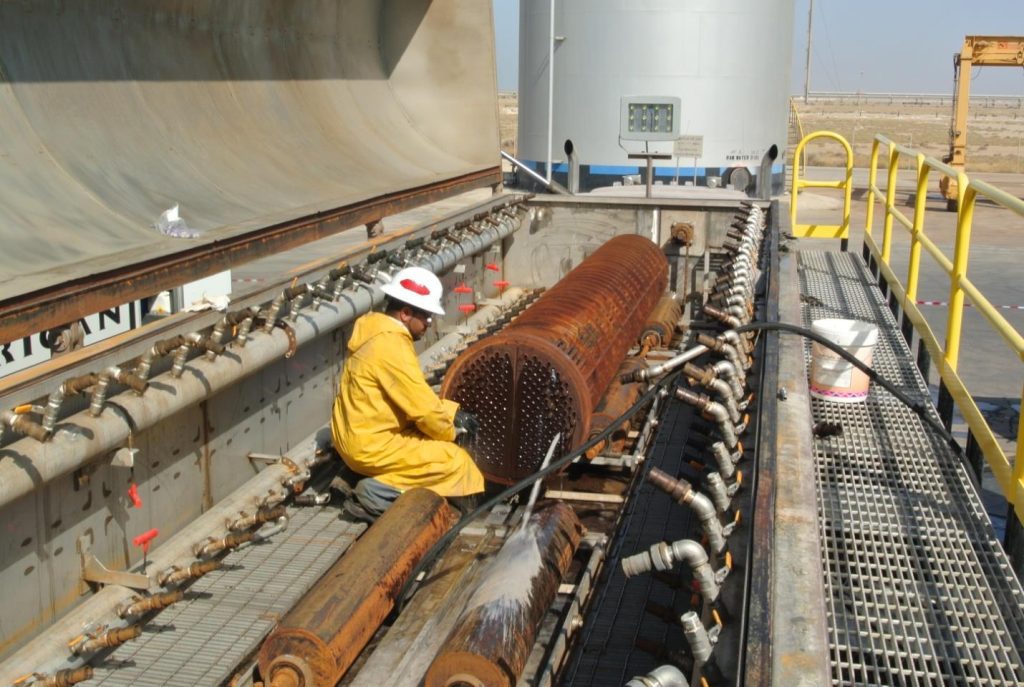
Objective
The main drivers to establish the required guidelines for maintaining a heat exchanger tube bundle spare (Offline asset sparing philosophy) are given by the asset criticality classification (Only applicable for “High Risk”), operational requirements, asset interchangeability, failure modes and frequency, lead time for tubes fabrication, logistics and space constraints, cost considerations (Cost of spare bundles and inventory holding costs) and repair vs replacement decision. The benefits of implementing an offline bundle sparing philosophy focus on ensuring a reliable plant operation and efficiency which will translate on enhancing plant performance, reduce overall maintenance costs and extend bundle service life.
Expected benefits
- Minimal operational downtime: Ensure critical process has minimal disruption by having spare tube bundles readily available for immediate replacement when failures occur.
- Improved maintenance efficiency: Streamline maintenance activities by cataloging tube materials and having spare bundles available. This allows for unplanned or planned maintenance to be carried out quickly and
efficiently without depending on tubes manufacturer delivery or bundle replacement. - Enhanced equipment reliability: Increase reliability by identifying common failure modes, avoiding prolonged operations under sub-optimal conditions that could lead to a large failure.
- Avoiding costly delays: Production losses and penalties due to long repair lead times (Extended MTTR) can be avoided by maintaining a spare parts inventory.
- Reduced unplanned shutdowns: Prevent unplanned shutdowns that can be costly in terms of production losses and associated penalties by ensuring spare tube bundles are readily available in case of unexpected failures.
- Optimized spare parts inventory: Develop an efficient offline asset sparing strategy by holding critical spare bundles without over-investing in components that are unlikely to fail. This balances operational risk and inventory costs.
- Supported predictive and preventive maintenance: Align the spare bundle philosophy with predictive maintenance programs. By monitoring the condition of the heat exchanger, spares can be ordered and replaced proactively avoiding failure before they happen.
- Compliance with safety and environmental standards: Ensure that critical equipment used in hazardous or environmentally sensitive processes is promptly repaired or replaced to meet safety and environmental regulations.
- Planned maintenance flexibility: Maintenance Team can schedule tube bundle replacements during planned shutdowns when spares are readily available, improving turnaround times and allowing for better planning of maintenance windows.
- Reduced emergency situations: A well-defined spares bundle philosophy reduces
the likelihood of costly emergency repairs, where expedited shipping and labour costs can increase expenses. - Timely replacements: Having spare bundles on hand allows for the timely replacement of severely corroded bundles and facilitate the utilization of interchangeable bundles for similar equipment, thus extending the bundle service life.
A structured approach that will facilitate an operating facility to establish an offline sparing philosophy for shell and tube heat exchanger bundles is shown in the flowchart.
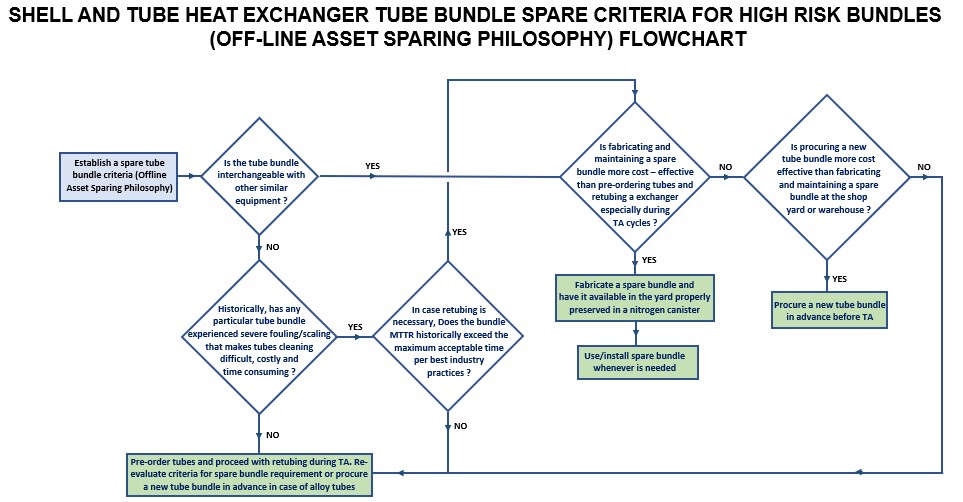
Shell and tube bundle storage procedures
A) Using rust inhibitor
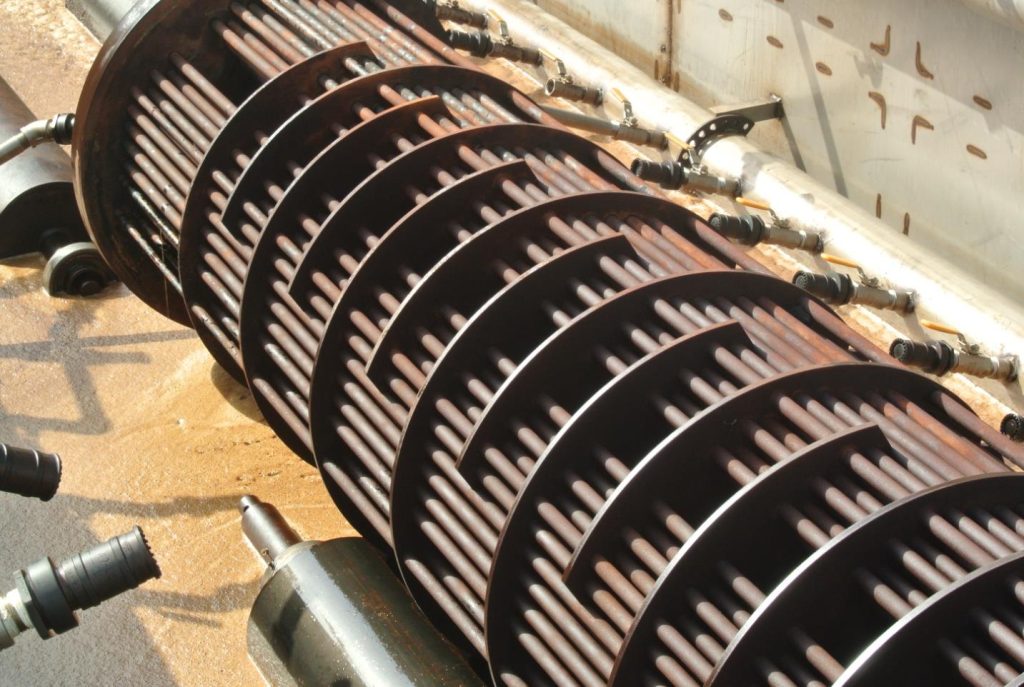
- Shop Supervisor to develop and inventory sheet of all tube bundles at the facility shop yard.
- All tube bundles stored at the facility shop yard will be protected using a rust inhibitor that will be applied by spraying.
- Blow dries the surface to be sprayed using compressed air.
- Apply a liberal spray coating of the inhibitor to all surfaces that will rust.
- Apply a coating of grease to all gasket surfaces
- On carbon steel tube bundles that have been tube side tested, the ID of the tubes require to be blown dry and have rust inhibitor sprayed in each tube from both ends. (The actual application of the rust inhibitor shall be done outside the shop preferably in the hydrojetting area (Open yard)
- After the bundle is sprayed and approved for storage by the Shop Supervisor and Inspection QA/QC Team, an inventory and inspection tag will be added. It is advisable to store the tube bundle in close area warehouse and/or use heat shrink wrapping when stored in open yards.
- It will be the responsibility of proponent Engineer/Inspection QA/QC to inspect the stored bundles.
- Inspection QA/QC will check and verify each bundle against the inventory and mark the tag on the bundle that has been inspected including signing the inventory sheet.
B) Using pressurized nitrogen (N2) canister
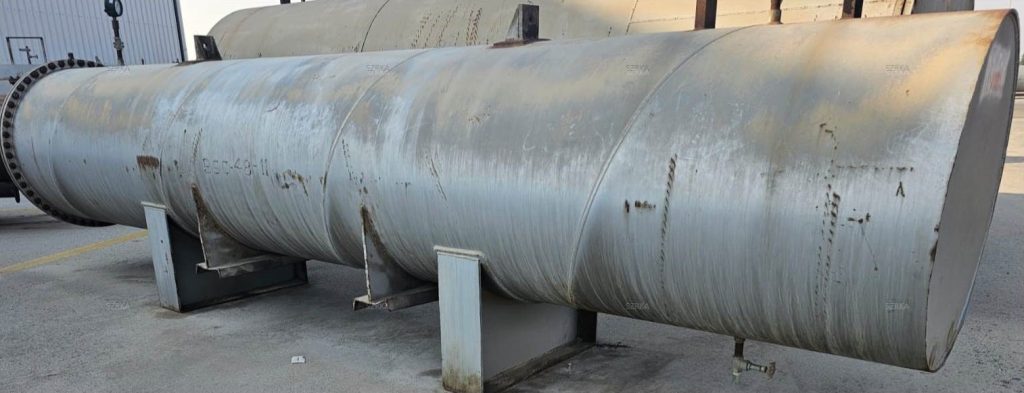
- Shop Supervisor to develop and inventory sheet of all tube bundles at the facility shop yard.
- Determine the required canister dimensions that will fi t the stored bundle.
- The canister shall be visually inspected for any defects (Corrosion, coating failure, lifting lugs damage, weld seams imperfection, sliding bar damaged, etc.)
- Flanged connections and all other machined surfaces area will be protected using an appropriate lubricant with rust preventive compound such as Cortec VpCI-369 or equivalent.
- Place the bundle inside the canister and close it using flanges and seal compound.
- Shop personnel should ensure a proper pressure gauge is installed on top of the canister including it has calibration sticker.
- Depressurize the canister and then re-pressurize with nitrogen (N2) until pressure gauge reaches 2 to 5 Psig.
- It will be the responsibility of Proponent Engineer/Inspector QA/QC to inspect the stored bundles
- Inspection QA/QC will frequently check and verify each canister pressure reading and log it and sign on the inventory sheet.
Sample of an N2 canister fabrication drawing.
For the full resolution, please contact editor at i.mukha@kci-world.com.
About the Author
Miguel Gutierrez is a Senior Mechanical Engineer with over 30 years of experience in the oil and gas industry, particularly in the Downstream Business showcasing his expertise in stationary equipment. His focus on piping/pipelines, pressure vessels, heat exchangers and storage tanks, along with hands-on troubleshooting during plant operations and turnarounds, reflects a comprehensive skill set. His international experience in Venezuela, the Caribbean Basin and the last 18 years in the Middle East adds a global dimension to his professional profile.
References:
- A MSSD Shop Department – Shop Heat Exchanger Bundle Storage Procedure
- PI 660 – Shell and Tube Heat Exchangers for General Refinery Services
- ASME PCC-2 – Repair of Pressure Equipment and Piping
- B23 – National Board Inspection Code
About this Technical Story
This Technical Story was first published in Heat Exchanger World Magazine in March 2025. To read more Technical Stories and many other articles, subscribe to our print magazine.
Technical Stories are regularly shared with our Heat Exchanger World community. Join us and share your own Technical Story on Heat Exchanger World online and in print.