High-pressure heat exchangers are crucial in industrial operations, especially in hydrocarbon processing plants, where they operate at over 100 bar and 400°C. This article examines the challenges and lessons from using special enclosure high-pressure heat exchangers, with a focus on Southeast Asia refineries. Unlike conventional shell-and-tube designs, these systems require advanced sealing to withstand extreme conditions, exceeding standard TEMA configurations. Innovative designs like screw-threaded closures, metallic diaphragm plates, and push-bolting systems provide cost-effective alternatives to bulky flanges and bolting, improving maintenance access and flexibility while introducing new complexities.
Muhammad Aizat Rasli Principal Engineer, Nurul Nadirah Staff Engineer, PETRONAS Group Technical Solution (PGTS), and Faqih Zaini
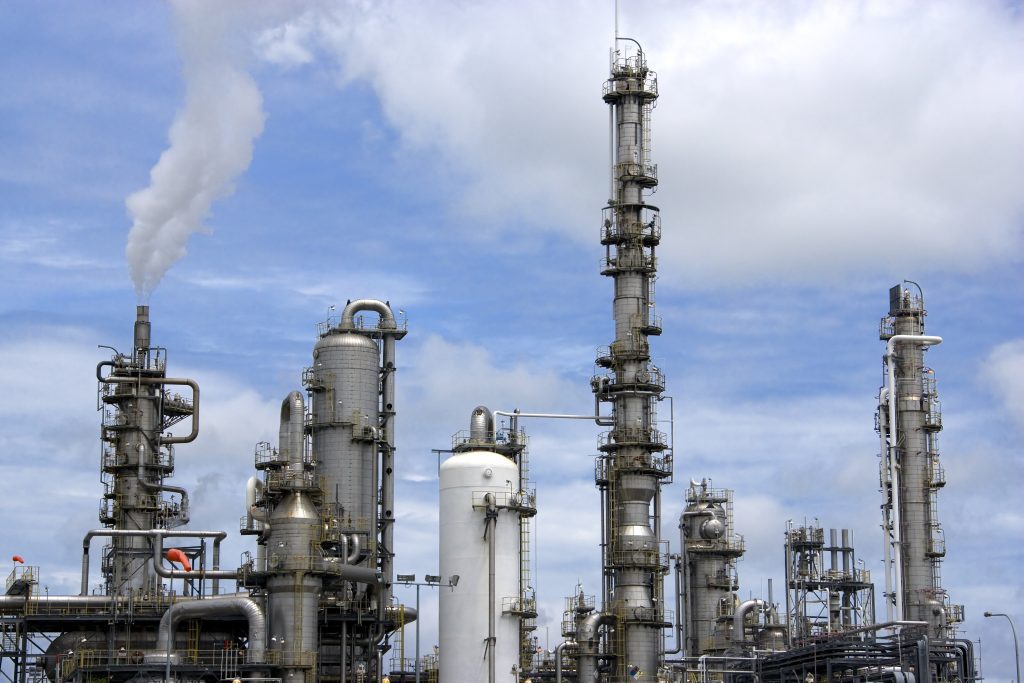
TEMA 11th Edition Stand
Prior to 2023, TEMA lacked detailed guidelines for specialized high-pressure heat exchangers, leading to inconsistencies and challenges due to the absence of a standardized reference. To address this, the 11th edition introduced the Type D classification, providing comprehensive guidelines tailored specifically to high-pressure applications. The following sub section provides a detailed summary of the newly added guidelines for Type D.
RCB-9.3.3 channel cover seal and closure mechanism The joint between the channel cylinder and flat cover should use a sealing element and closure mechanism that suits the service pressure and temperature. Seals can be gaskets, O-rings, metallic seals, or welds, and closure mechanisms may include bolts, key rings, or other locks. The design must meet Code requirements and consider ease of maintenance and assembly. Ring/face gaskets work with closure mechanisms that generate gasket-seating loads, but pressure limits must be seen. O-ring seals have no gasket-seating load and can be used with various closure systems. Metallic seals, either self-energizing or wedge-sealing, are suited for different closure mechanisms. In welded seals, the weld is for sealing only, with the closure mechanism handling the pressure load. When combined with bolts, the seal may be a weld-ring or diaphragm seal. For diaphragm seals, the diaphragm must be welded to the channel and have the right thickness to ensure a dependable seal while conforming to the flat cover. Joint assembly with bolts must follow the Diaphragm Installation Procedure as prescribe in TEMA Section E-4.6. Key rings and locking mechanisms don’t generate gasket-seating loads, so they should only be used with self-energizing or welded seals. These mechanisms include breechlocks, threaded hold-down rings, and other quick-actuating covers. These require a system to safely relieve pressure before opening.
Tales from the field
Over the years, Southeast Asia refineries has commissioned various types of high-pressure heat exchangers across its hydrocarbon processing facilities. Each deployment has provided valuable insights into operability and maintainability, underscoring the need for tailored designs that align with specific operational demands. One notable case involved a Feed and Reactor Effluent heat exchanger, which experienced recurring leaks shortly after its commissioning in 2021. Despite rigorous testing and initial assurances of reliability, the system faced performance challenges worsened by unit upsets. The leaks were traced to the internal assembly responsible for sealing the tubesheet gasket—a critical component meant to withstand all operating conditions.
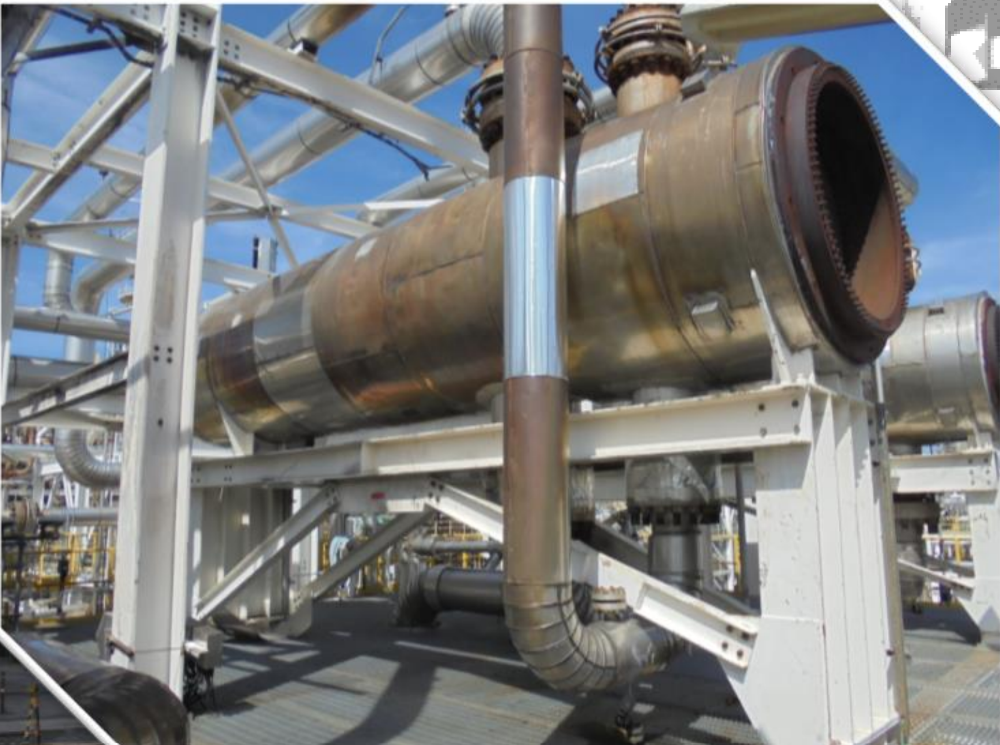
Complexities in high-pressure heat exchanger handling
High-pressure heat exchangers are crucial yet highly complex components, particularly in the energy and chemical industries. Their design, operation, and maintenance pose significant challenges essential for ensuring reliability, safety, and efficiency in demanding conditions. In this article, we aim to highlight two critical challenges encountered with high-pressure heat exchangers, drawing from past operational experience which are:
1. Loss of Bolt Load
2. Difficulties in Disassembling
which underscore significant hurdles that impact system performance, reliability, and maintenance efficiency.
Loss of bolt load due to stacked components and gasket relaxation
One of the critical challenges identified with high-pressure heat exchangers is the loss of bolt load, which is intricately linked to the interplay of stacked components and gasket relaxation.
In systems where multiple components—up to seven—are stacked on a single joint, the complexity of thermal behaviour becomes a significant concern. During thermal upsets, each component expands and contracts at different rates due to varying thermal coefficients. This mismatch creates a non-uniform response across the joint, introducing uneven stresses that gradually compromise the clamping force needed to sustain sealing integrity. The issue is further worsened when using a three-gasket system, which adds layers of variability to the joint’s behaviour under operational conditions. The three-gasket system, by itself is a system that is rarely being implemented in high-pressure heat exchangers even at the global scale. Nevertheless, one refinery in Malaysia integrated this system into a high-pressure heat exchanger as shown in Figure 2, setting it apart from standard practices.
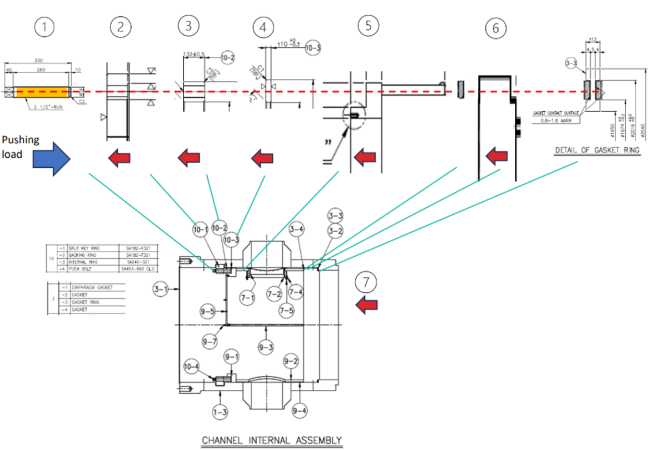
This aggravates the bolt load issue as when thermal cycling occurs, gaskets will undergo relaxation—a reduction in their ability to sustain compression over time. Combined with the non-uniform thermal expansion of stacked components, this relaxation amplifies the likelihood of bolt load loss. The diminished clamping force heightens the risk of leaks at critical points or even complete joint failure, particularly during thermal upsets where rapid temperature fluctuations intensify stresses on the joint.
Difficulties in disassembling high-pressure heat exchangers
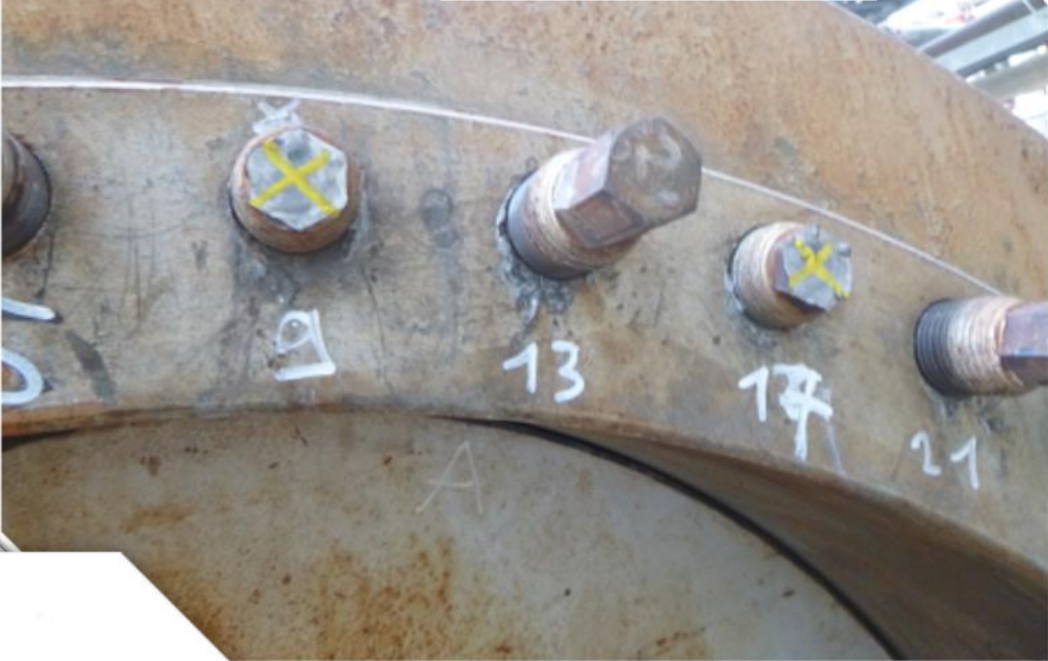
Disassembling high-pressure heat exchangers for maintenance or inspection presents significant operational challenges, often resulting in time-consuming delays. Based on previous experiences at plants, a recurring issue is the inadequate tooling available for the removal and reassembly of key components, particularly the push bolts. The absence of properly calibrated tools to manage these bolts leads to frequent tool breakage when attempting to loosen them, further complicating the disassembly process. In many instances, push bolts often become seized due to the harsh operating conditions inherent to high-pressure heat exchangers as shown in Figure 3.
Over time, exposure to high temperatures and process fluids accelerates corrosion, weakening the bolt threads and causing them to bind. This issue is further compounded by thermal cycling, where repeated expansion and contraction of components during operation create uneven stress across the bolts. Such stress intensifies when bolts are improperly torqued during assembly, either through overtightening or uneven load distribution, which can distort the threads and make future disassembly even more difficult. The cumulative effect of these challenges, stemming from insufficient tooling, corrosion, and improperly maintained fastenings, creates a domino effect that significantly prolongs disassembly procedures, increasing operational costs but also results in unnecessary delays, impacting overall plant productivity and operational efficiency.
Operational insights and lessons learned
The experience with high-pressure heat exchangers has provided valuable insights into key aspects of future system development. Lessons from real-world challenges have deepened understanding of the complexities in designing, implementing, and maintaining these systems. This knowledge forms the foundation for improving future designs and performance in demanding conditions. We will now explore two significant lessons learned, their implications, and how they have shaped our problem-solving approach.
Inadequate push bolt design
One of the refineries experienced an issue with push bolt load loss. Based on a comprehensive root cause analysis, it was revealed that an inadequate design methodology had been applied. Originally, there are three standards that we used as reference which are ASME VIII-1, EN1591-1, and EN13555. These standards are used to ensure all internal components, including the partition assembly, internal flange, and internal ring, could withstand the forces exerted by push bolts without experiencing buckling or distortion—even when tightened to their yield strength. The detailed design philosophy prioritized robust engineering practices, ensuring resilience under extreme operating conditions and accommodating potential variances during maintenance and assembly. However, a critical gap was identified in the ASME VIII-1 code, as highlighted in ASME STP-PT-036: Bolted Flanged Connections in Elevated Temperature Service. The study revealed that component relaxation was not fully considered in the ASME VIII-1 calculations, indicating the limitations of this standard in high-temperature applications. This gap underscores the importance of integrating supplemental design codes, such as EN1591-1 and EN13555, which address material creep and joint behaviour under elevated temperatures more comprehensively. By aligning the design with the provisions and strengths of these international standards—ASME VIII-1, EN1591-1, and EN13555—user can significantly enhance the reliability and resilience of its high-pressure heat exchanger systems. These standards provided a robust framework to address critical design requirements, ensuring the components could withstand operational stresses and prevent failures, thereby establishing a solid foundation for long-term operational excellence.
Improved disassembly procedures
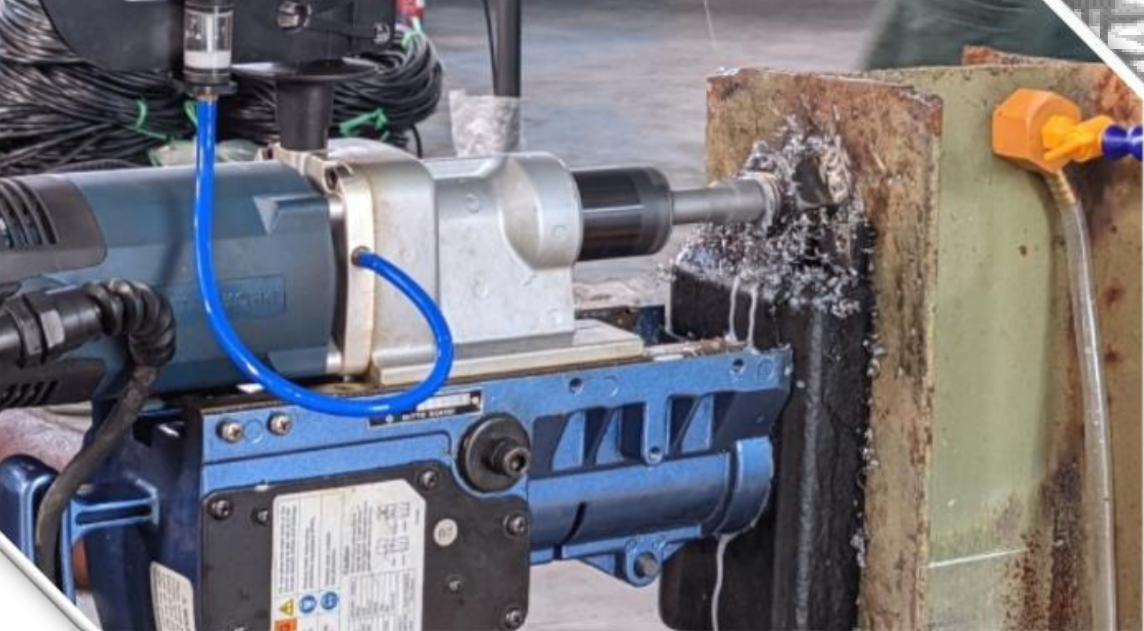
Based on operational experience, effective maintenance strategies have emphasized the importance of thorough preparation and specialized tooling. Two key improvements are mock-up systems for push bolt removal (see Figure 4) and specialized impact sockets. Mock-up systems allow operators to practice disassembly on a smaller scale, identify challenges, and ensure all tools are ready, reducing delays and minimizing damage risks. Specialized impact sockets, designed for push bolts, make it easier to loosen seized bolts without harming nearby components. These advancements improve disassembly efficiency and equipment reliability, raising the standard for maintenance.
Looking ahead
Proprietary sealing designs provide innovative solutions for managing extreme pressures but require careful attention during design, manufacturing, and installation. Lessons learned from challenges with high-pressure heat exchangers offer a strong foundation for improving future designs and operations, paving the way for more robust and reliable systems.
For companies embarking on new projects involving high-pressure heat exchangers, it is essential to ensure that the selected fabricator or designer owns extensive experience and a deep understanding of this type of equipment. This expertise is vital because even minor design flaws can lead to significant safety risks, operational failures, or costly downtime thus impact negatively to the plants.
By embedding these lessons into future practices, the industry can ensure not only safer and more efficient equipment but also a commitment to continuous improvement, setting a benchmark for high-pressure heat exchanger technology worldwide.
Conclusion
High-pressure heat exchangers represent a pinnacle of engineering complexity, demanding innovative solutions and relentless attention to detail. Overcoming the unique challenges they present requires more than adherence to standard practices. It demands a commitment to continuous learning and improvement, driven by real-world experience and advanced methodologies.
The journey with this high-pressure heat exchanger has not only expanded the boundaries of technical expertise but also reinforced the importance of collaboration, innovation, and adaptability in engineering. These insights provide a solid foundation for addressing future challenges and ensuring the continued evolution of reliable and efficient systems. With every challenge overcome and every solution implemented, the benchmark for excellence in high-pressure heat exchanger design and maintenance is raised, securing their place as a cornerstone of modern industrial operations.
References
- Tubular Exchanger Manufacturers Association (TEMA) (2023). TEMA standards for tubular heat exchangers (11th Edition)
- Reeves, D., & Clover, D. (2014). “Breech lock exchangers: Obtaining leak-free performance”. Proceedings of the ASME 2014 Pressure Vessels & Piping Conference.
- American Society of Mechanical Engineers (ASME). (2010). STP-PT-036: Bolted flanged connections in elevated temperature service
About this Technical Story
This Technical Story was first published in Heat Exchanger World Magazine in February 2025. To read more Technical Stories and many other articles, subscribe to our print magazine.
Technical Stories are regularly shared with our Heat Exchanger World community. Join us and share your own Technical Story on Heat Exchanger World online and in print.