As a plant operator, you are likely always chasing new opportunities to improve operations. Perhaps it’s to reduce costs or increase production? Reduce energy usage? Cut emissions? Produce a better-quality finished product? Often overlooked, however, is how such changes can impact the performance of existing technology such as plate-based moving bed heat exchangers (MBHEs).
By Jamie Zachary, Solex Thermal Science
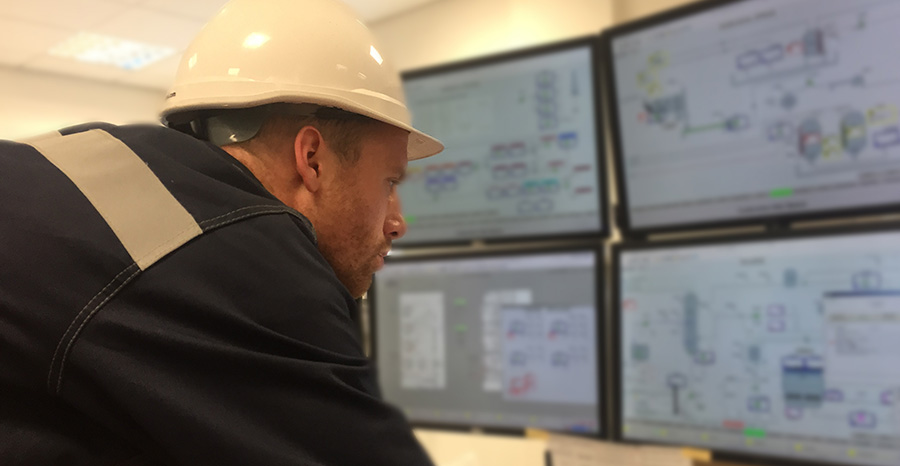
Process evaluations provide plant managers with opportunities to ensure their installed technology is still operating optimally and as it was originally intended. “It’s a tune-up for your tech,” says Barry Milln, Director, Customer Solutions and Service at Solex Thermal Science, a Canadian-headquartered heat transfer technology company that specializes in developing high-efficiency, indirect heat exchange technology for the heating, cooling, and drying of free-flowing granular materials.
Of the many different variables that can impact the performance of your heat exchange technology, Milln categorizes a few that he’s seen most often:
• Product: The product’s characteristics have changed, whether they be variations in the upstream processes, chemistry, quality, or the downstream/market needs.
• Heat transfer fluid: The temperature, type, and/or flow rate of the heat transfer fluid has changed.
• Equipment: This potentially includes anything ancillary to your heat exchange technology – for example, water circulation pumps. It could also include components of the heat exchanger itself such as instrumentation, feeders and discharge devices using vibratory motors or actuators.
• Processes: The product throughput is different, most often to handle demand for increased production. Also, the temperature at the outlet has changed due to downstream requirements.
• Maintenance: Inadequate preventative maintenance has led to issues such as fouling on both the product and liquid sides, excessive wear and resulting degraded performance.
What are the impacts?
Roman Milman, Service & Support Engineer at Solex, notes different process conditions can affect the performance of plate-based MBHE technology in different ways. For example, if the throughput increases but heat transfer fluid temperature remains the same, then the output temperature of the finished product will be deficient.
In some cases, it can lead to condensation occurring during cooling and, subsequently, caking. “For example, we worked with a fertilizer customer who wanted to increase the capacity of the production line from 100 to 120 tph,” says Milman. “They didn’t account that the water temperature and purge air requirements would also need to change. So, it led to caking between a few of the plates. Over time, the entire heat exchange system started underperforming. After consulting our engineering team, we made a few small adjustments, and it ran trouble free afterward.”
In other cases, the product might change – and so too its specific heat capacity (cp). This could lead to overheating or overcooling. The product could also contain additional moisture, which is a catalyst to condensation forming and, again, caking within the MBHE.
Or, if the product is organic, it might also not be as clean as desired. This could lead to clogging between the plates and negatively impact mass flow. In some more extreme cases, the clogging or buildup of this organic material can lead to smolders starting within the MBHE.
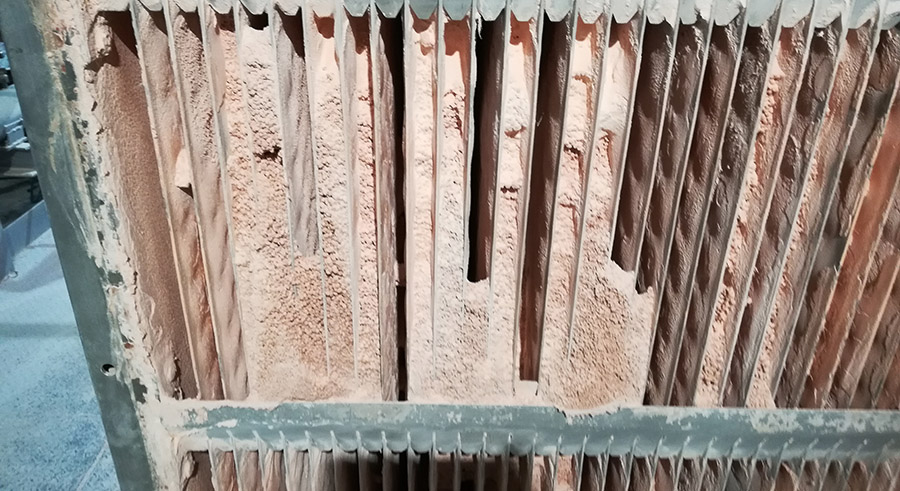
What are the solutions?
Unfortunately, there is not a one-size-fits-all solution to maximizing the performance of your heat exchange technology. However, there are some best practices that include regular preventative maintenance, as well as consulting with providers such as Solex when processing and/or operating changes are needed.
“I’ve seen, first-hand, what can be done,” says Milln. “Our 30-plus years of experience and in-house expertise, in combination with our proprietary thermal modelling software, allows us to uniquely identify any issues with your technology and work with your team to optimize production.”
He shares an example where a customer purchased MBHE technology from Solex originally designed to handle municipal water. Later, that customer started using a colder water source. In doing so, however, the decreased water temperature caused condensation and, eventually, caking within the heat exchanger.
“We worked with them on optimizing the fluid control system so that the water inside the MBHE was at the correct temperature range, both in and out, for the application,” says Milln. In another example, Milman says a customer was seeing unexplained variations in the outlet product temperature compared to the original design specifications.
“We had designed the heat exchanger for 100 tph of product throughput, but the customer was only operating at 60-70 tph. This led to plates being over-cooled. Instead of receiving the product at 40 °C at the outlet of the MBHE, it was closer to 30 °C,” he says. “Our advice was to increase the water temperature at the inlet fluid manifold until they could run the system at design throughput.”
Other benefits
Customers can also tap into ongoing innovation and improvements to the technology. “We recently had a customer who was having some challenges with a vibrating feeder installed on their heat exchanger more than two decades ago,” says Milln. “The shackles that were holding the feeder tray have since been upgraded with a more effective suspension design. That offered them not just an easy fix, but the ability to extend the life of the existing system.”
Additionally, volatile and increasing energy prices have led many companies to look for alternative and lower cost energy sources, including recovering process heat from the heating, cooling and drying stages. Milln notes Solex is currently working with companies across virtually every industry to find and re-use sources of energy that customers were not thinking of before – for example, using hot flue gases to heat water that can then be used in a MBHE to heat the product.
“Our technology is quite customizable with the ability to upgrade and retrofit with relative ease, giving operators the opportunity to realize the potential of previously untapped energy sources,” says Milln.
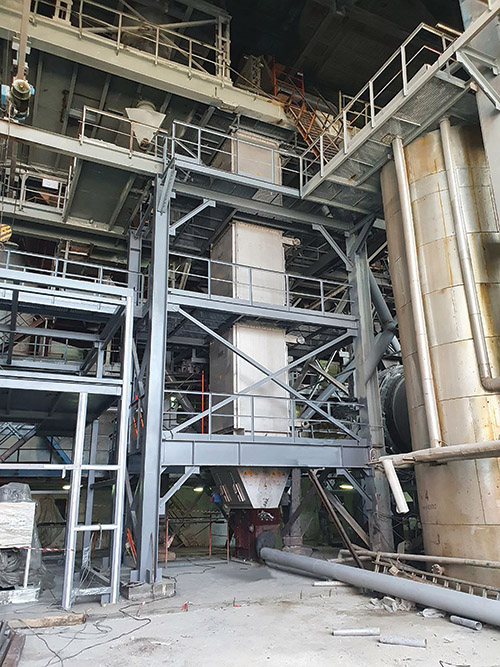
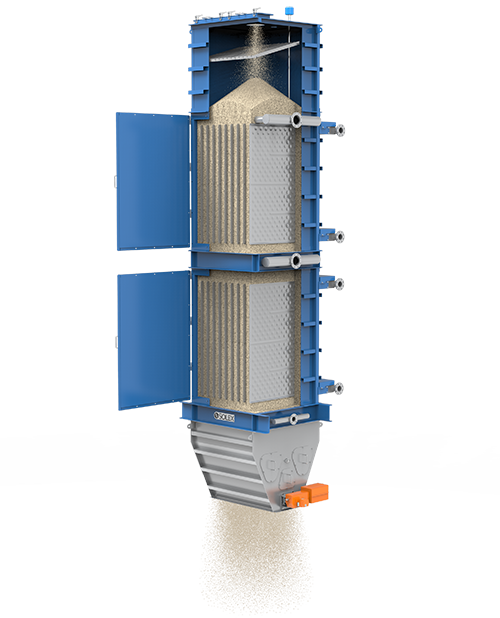
By regularly evaluating the performance of MBHE technology, plant operators can often improve production,
as well as extend the life of the existing system.