This article highlights an additive manufacturing process that provides the same benefits as Laser Powder Bed Fusion (LPBF) when applied to 3D print cold plates, but also allows engineers to open up other creative possibilities when designing cold plates for their specific applications: Ultrasonic Additive Manufacturing.
By Dan King, Additive Manufacturing Project Engineer, Fabrisonic LLC
One of the articles published by Heat Exchanger World described the benefit of designing and manufacturing cold plates using additive manufacturing (see box). The authors helpfully describe what cold plates are, how they are usually manufactured, and the various benefits of designing and producing cold plates using Laser Powder Bed Fusion (LPBF) to 3D print cold plates, particularly for applications such as eVTOL aircrafts and other technologies that require small cold plate packaging. Let’s now explore another additive manufacturing process that takes designing of cold plates to the next level.
Fabrisonic and ultrasonic additive manufacturing
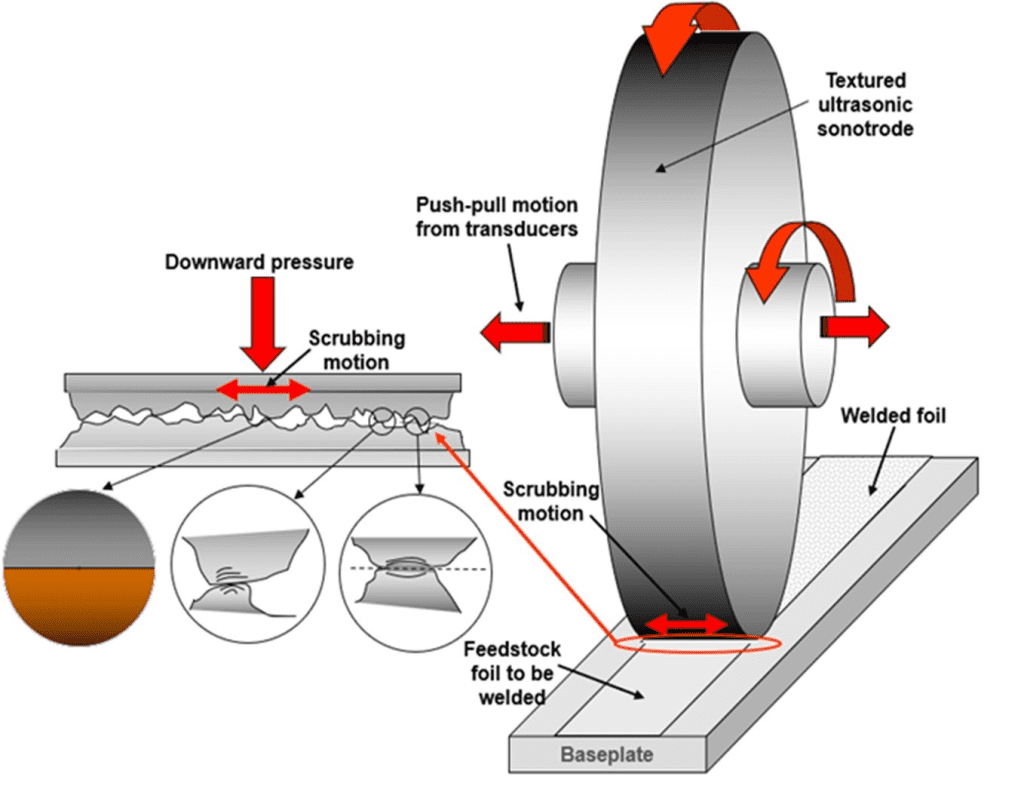
The world of additive manufacturing, also known as 3D printing, has opened the possibility for more complex and efficient heat exchanger devices. When people hear the term 3D printing, they generally think of processes involving the melting of a material, whether it be metal or polymer, through hot ends or lasers to gradually print a component layer by layer. However, Fabrisonic has developed a method of printing metals at very low temperatures called ultrasonic additive manufacturing (UAM).
Fabrisonic is an advanced manufacturing company located just north of Columbus, Ohio in the United States. Here, we have developed and refined a method of bonding metals together without any melting occurring during the printing process. Here’s a brief overview of how the process works: metals foils, ranging from <0.001” to 0.015” in thickness, are bonded together by a tool that scrubs back and forth between 20,000 and 30,000 times per second. The displacement of the tool side-to-side is on the order of 30-60 microns, a motion which breaks up the oxide layer between the metals. By applying a down force with the tool, combined with this scrubbing motion, a true metallurgical bond is formed between the two foils. The foundation for this process is ultrasonic welding. Fabrisonic has taken traditional ultrasonic welding and more than tripled the power to bond materials like aluminum, copper, steel, and even zirconium, to name a few. The UAM processes uses commercial metal foils rather than metal powders or wires, and does not require high safety processes or controls, as does metal powder 3d printing.
The three main benefits of UAM
Because UAM is a very low temperature process, it has benefits over other additive manufacturing technologies. The first of these advantages is bonding dissimilar metals to one another. When melting occurs between two dissimilar metals, brittle intermetallics form between the two materials which can easily crack and form defects. With UAM, since the bonding mechanism is not melting but rather removal of oxides, dissimilar metals can be bonded to one another in the same part. The implication of this benefit is powerful. For example: an aluminum heat exchanger can be printed with copper to improve thermal performance while keeping weight low or printed with unique alloys such as tantalum to protect from radiation.
The second advantage of UAM is that it enables the embedding of sensors and other measurement devices into metal parts. Devices such as fiber optic cables, thermocouples, strain gauges, and other sensors can be fully embedded into the metal matrix for improved measurements, protection of sensors from the outside environment, and closer measurements to the area of interest. This allows for engineers to include various sensors into their heat exchanger, or cold plate, designs, enabling the collection of real-time, in-situ data for better understanding performance, refining digital twin models, and collecting health-monitoring information of their system.
The third main benefit of UAM is that it allows for complex internal channels for flow devices and heat exchangers. While most additive methods include this benefit, the advantage of UAM is that all of these complex channels feature a CNC machined surface finish. In fact, UAM produced parts do not require any post-printing surface finishing, heat treating, or HIPing. UAM machines are CNC machines retrofitted with the UAM technology which allows for seamless alternating between additive and subtractive manufacturing processes. In order to create complex internal channels in a part, the channels are simply machined with the subtractive portion of the machine and then capped with the additive portion of the system using UAM. Furthermore, this hybrid process allows for in-process inspection of parts, whereas additive processes such as LPBF do not.
NASA utilizes UAM for improved heat exchanger efficiency
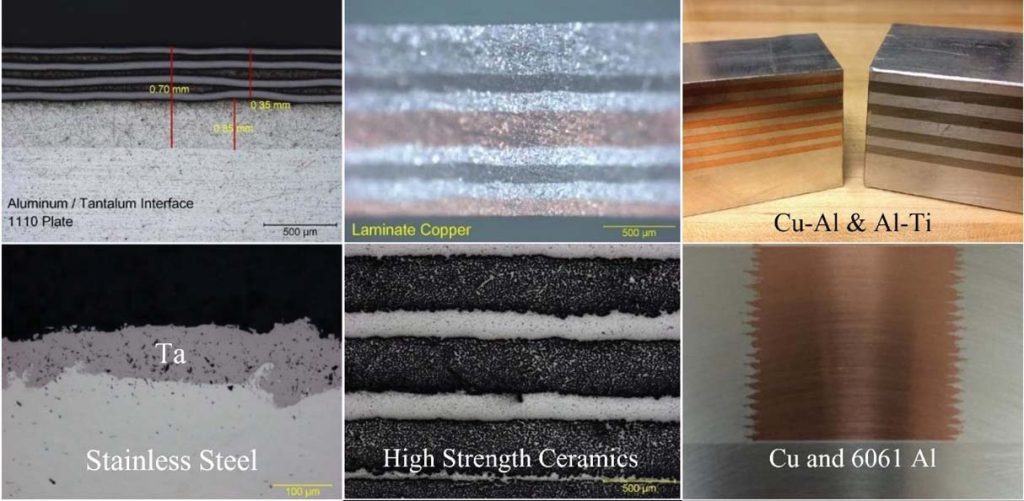
In many aerospace applications, heat piping is adhered to a surface using epoxy or brazing in order to heat or cool a particular area, device, or component. While epoxying and brazing are somewhat viable options for heat transferring devices, these techniques can lead to points of failure and loss of efficiency in the system. NASA came to Fabrisonic looking for a replacement for the aforementioned processes, and UAM was the perfect fit. Fabrisonic, in conjunction with Utah State University, manufactured a heat exchange panel that greatly improved the performance of the overall system. Instead of bending tubing and adhering it to a panel, UAM can seamlessly integrate the channels into the panel. By manufacturing the channels into the part as one, there is no joint between the fluid pathways and the outside panel face. This improves the overall efficiency of the device while removing a potential point of failure in the system.
Another critical aspect of aerospace parts is the weight of each component in the system. Even a pound of material can lead to a huge increase in cost and a decrease in flight efficiency. Knowing this, Fabrisonic was able to reduce the overall weight of the panels while increasing the efficiency of the heat exchanger by removing some of the panel thickness and replacing it with ~0.010” of copper material. Copper is more than twice as conductive as aluminum, resulting in a huge gain in overall thermal efficiency. Also, by adding copper onto the entire face of the panel, the heat was spread across the part evenly, resulting in improved heat radiation effects of the part. The last key requirement of this fully integrated heat exchanger that had to be met was hermeticity. These parts needed to be 100% leak free, as they would be flying on satellites. The final parts met all hermeticity and cleanliness specs from NASA, as they were measured to be hermetic beyond 1×10^-8 std cc/sec of helium.
Improved measurements in in-situ applications
As previously mentioned, UAM enables the embedding of sensors for collecting real-time, in-situ data. This can be important to understand the performance of a cold plate in a heat exchanger system, particularly when cold plates are buried inside of a larger system and are hard to access, or when cold plates are installed in systems such as satellites, UAVs, electric vehicles, or eVTOLs. Having the sensors embedded into the cold plate allows for the collection of data much closer to the location of performance, and also protects the sensor(s) from environmental effects external to the cold plate.
For example, UAM has been utilized not only on parts flying in space but also on critical ground components of rocket systems. Fabrisonic teamed up with Luna Innovations and NASA to create a pipeline device called the Smart Pipe that measured stressed, strain, pressure, and temperature of the pipe. This device was to be used in rocket liquid hydrogen fuel lines to monitor the conditions of the fluid as it pumped into the rocket. Because the fuel was liquid hydrogen, the Smart Pipe had to be able to withstand cryogenic temperatures and pressures up to 6000 psi. To achieve the accuracy, sensitivity, and repeatability necessary to measure small changes in the fluid’s parameters, fiber optic sensors were fully embedded into the outside wall of a stainless steel 304 pipe. To embed a fiber using UAM, a channel that matches the fiber’s diameter is milled into the pipe. The sensor is placed in the channel, and a metal foil is vacuumed down over top of the device. Since metal flows under an ultrasonic field, the fiber optic sensor is completely surrounded in the metal matrix –see the cross section on the right as an example. As the pipe expands and contracts due to pressure and temperature changes, that fiber optic sensor reads a corresponding strain value. This strain value can then be mapped to read numerous different parameters depending on the user’s interests.
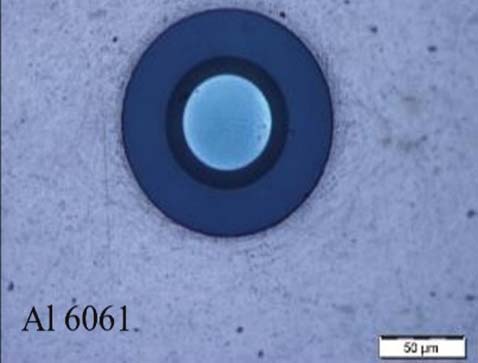
The pipe was successfully cycled at 6000 psi and was taken down to <-240 degrees Fahrenheit while maintaining repeatable and accurate measurements. Similar performance can be seen in cold plates embedded with sensors. For example, a popular measurement device used with heat exchangers is thermocouples. Traditionally, a thermocouple is adhered to the outside of the part or inserted into a drilled hole to take measurements at an area of interest inside the part. The problem with these approaches is that the measurements are limited to either the outside of the part or are restricted by the geometry of a drilled hole. With UAM, complex thermocouple routing can be designed to get measurements from as close to the area of interest as possible. The thermocouple is also bonded or coupled to the surrounding metal, resulting in faster and more accurate readings.
Based on the manufacturing advantages of UAM, engineers and designers can envision a cold plate that is made from different metals to take advantage of thermal properties of one metal and the light-weight properties of another. They can also incorporate embedded sensors to get real-time, in-situ data on the health and performance of the heat exchanger system at the point of cold plate integration. The benefits of UAM enable new ways of designing and making cold plates.
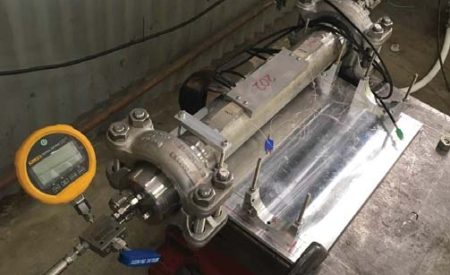
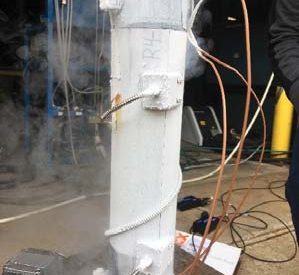
About the author
Dan King is a mechanical engineer who has been with Fabrisonic for around 5 years. Here, Dan has lead work in various areas including but not limited to machine design and build, machine training, fiber optic sensor embedding, heat exchanger manufacturing, and cylindrical printing development.
About this Technical Story
This Technical Story was first published in Heat Exchanger World Magazine in April 2024. To read more Technical Stories and many other articles, subscribe to our print magazine.
Technical Stories are regularly shared with our Heat Exchanger World community. Join us and share your own Technical Story on Heat Exchanger World online and in print.