By Michael Radicone, Lead Specialty Products – Heat Transfer Research Inc.
What is vapor infusion?
Vapor infusion is an environmentally friendly method that reduces fouling and corrosion in heat exchangers and process equipment that use water as a cooling stream. Vapor infusion safely generates scrubbing, transitory bubbles that reduce the formation of foulants on heat exchanger surfaces and sedimentation while imparting targeted, reduced chemical treatments. Vapor infusion is intended to reduce or eliminate foul formation and progression, maintaining optimum heat exchanger functionality.
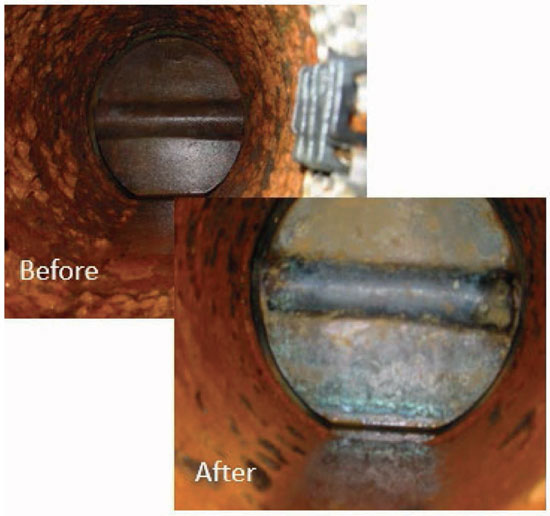
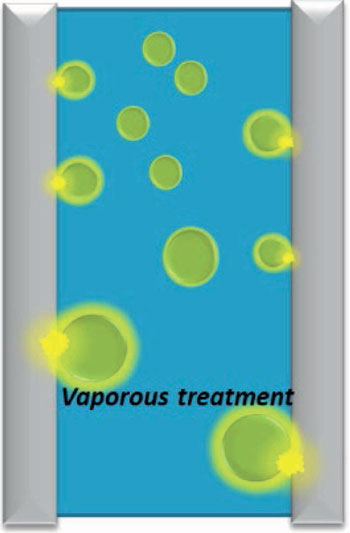
How vapor infusion works
The vapor infusion system injects (infuses) low-dose vaporous chemical treatment periodically into the cooling water flow stream of heat exchangers and process equipment, creating a profusion of vapor bubbles in the flow stream. The vapor bubbles mechanically prevent adherence and solidification of fouling agents while disrupting sedimentary action (Figure 1). The vapor bubble surface chemically treats the internal surfaces of heat exchangers and process equipment to reduce fouling and corrosion (Figure 2). The bubble-to-surface interaction provides targeted chemical treatment while minimizing chemical residue to the water fluid stream. The unique properties of turbulent bubbles provide environmental benefits and disruptive capabilities for removing the initiation of fouling sites and sedimentation. The vapor bubbles have a lower oxygen content which decreases dissolved oxygen and inhibits oxidation corrosion.
The effectiveness of vapor infusion has been demonstrated in studies conducted at various universities, with the United States Navy, and with commercial applications. Vapor infusion is effective for any application that uses fresh water, sea water, or water with high levels of organic matter or scaling salt for cooling. Vapor infusion has been successfully implemented on plate-and-frame and shell-and-tube heat exchangers. Processing plants, ships, offshore rigs, aquaculture farms, and geothermal systems applications have all benefited from using vapor infusion. Clients have experienced a decreasing need for manual tear down and chemical cleaning of heat exchangers, as well as a reduction or elimination of the use of chlorine. For heat exchangers that still require manual cleaning, clients have seen a greatly increased time between cleanings. Often, they never need to open their exchangers because the heat exchangers are operating close to design conditions and, when opened to perform inspection after years of use, the exchangers show little fouling of any type (Figures 3 and 4).
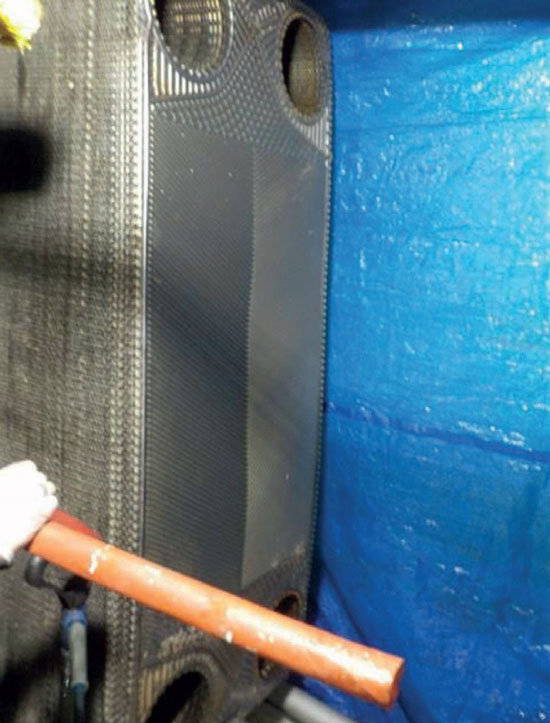
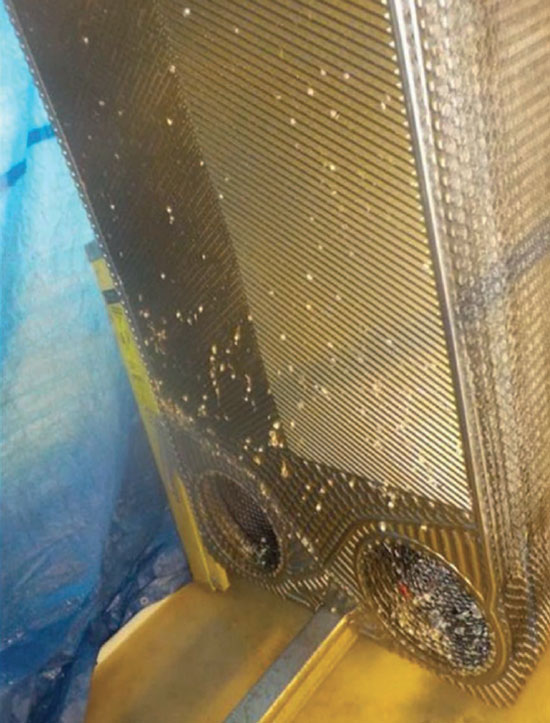
Vapor infusion reduces carbon expression
It is known that efficient operation of a heat exchangers has a direct correlation to carbon expression through increased energy draw and effects of diminished heat transfer on engine systems. Numerous studies have concluded the direct results of fouling on carbon emissions.
In one such study, Casanueva-Robles and Bott [1] determined that “the presence of unwanted deposits on heat transfer surfaces in power station steam condensers can increase the discharge of ‘greenhouse’ gases.
The extent of the increase is of course dependent upon the thickness of the deposit.” The authors continue:
“The loss of heat recovery and the additional energy for pumping represent a loss of thermal efficiency. When fuel combustion supplies energy, additional greenhouse gas emission will result.” The use of vapor infusion maintains optimum heat exchanger functionality and cooling water flow by operating the heat exchanger at close to design conditions. As a result, the energy requirement of the cooling water pump is both continuous and lower.
Recent study
During the 2022 Horizons Symposium on Heat Transfer in Environmental Technologies, McElrath presented a study [2] that tested the effectiveness of the I2 vapor infusion technology compared with traditional chlorine treatment in a cooling water flow loop. He concluded that I2 vapor infusion is a promising alternative to chlorine treatment for mitigating biofouling in condenser tubes. This technology also demonstrated the potential to mitigate buildup of sediment in condenser tubes.
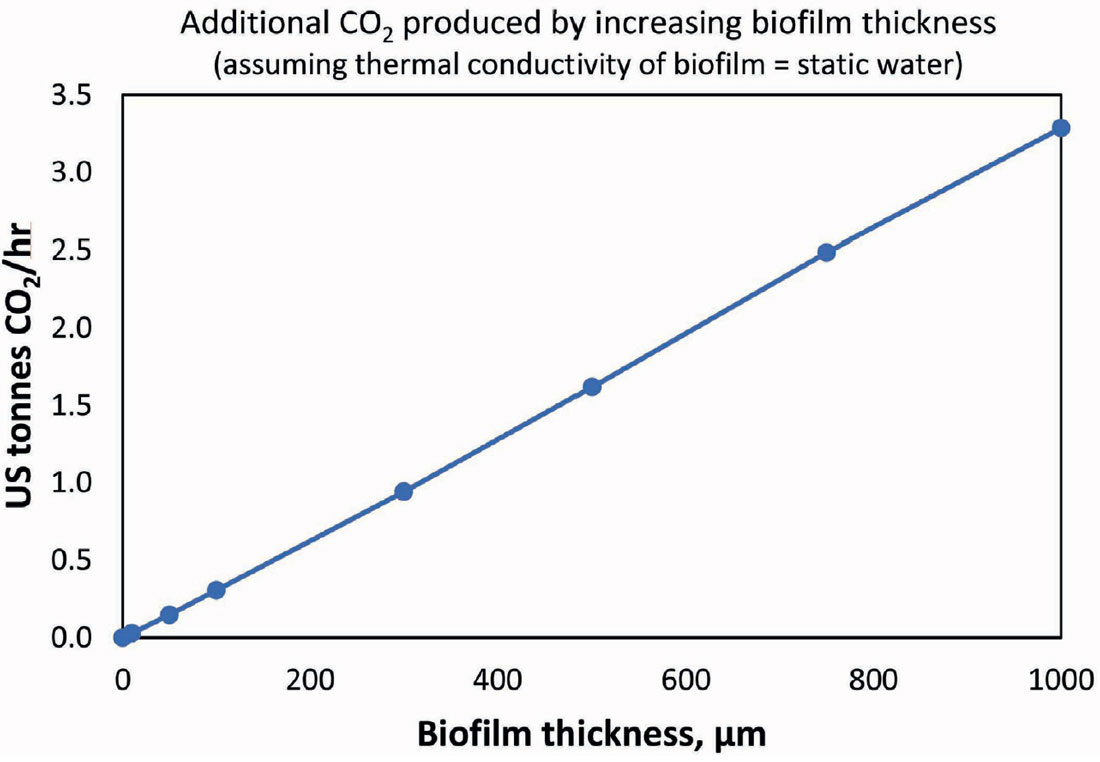
Vapor infusion implementation
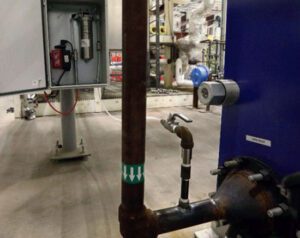
The vapor infusion system is relatively compact and easily installed on most heat exchangers (Figure 6). The system requires a compressed air and electric source, as well as a simple connection to the treated water flow stream. The vapor infusion system operating conditions are based on the heat exchanger operating conditions, including water flow rate, temperature, and pressure. The system functions automatically, infusing periodically depending on heat exchanger application and cooling system operation. The only labor required after installation is a periodic cartridge change and simple maintenance of air filters for excessive moisture and/or oil from the compressed air source. Heat Transfer Research, Inc. (HTRI) is the exclusive worldwide provider for vapor infusion technology for heat exchanger and water processing applications using fluid flow. For more detailed information or to request a presentation about the vapor infusion technology to you or your company, visit https://www.htri.net/vapor-infusion.
References
1. T. Casanueva-Robles and T. R. Bott, The environmental effect of heat exchanger fouling: A case study, Proc. 6th Intl. Conf. Heat Exchanger Fouling and Cleaning – Challenges and Opportunities, Eds. H. Müller-Steinhagen, M. R. Malayeri, and A. P. Watkinson, ECI Symposium Series, Vol. RP2, 278 – 282 (2005).
2. J. McElrath, A study of iodine vapor infusion to mitigate fouling of cooling tower water, Proc. 2022 Horizons Symposium, 59 – 72 (2022). [Online] https://www.htri.net/
About the author
Michael Radicone is Specialty Products Lead for Heat Transfer Research, Inc. the global leader in process heat transfer technology and design. Michael is also the President and Chief Science Officer of I2 Air Fluid Innovation, Inc, developers of the vapor infusion protocol for heat exchangers and gas scrubbers and mercuric transformational additives for wastewater.