Willy van Well has a friendly and open personality. Curious by nature, he is a man driven with passion when it comes to talking about heat exchangers and solutions for heat transfer systems. Heat Exchanger World caught up with him at his offices at ATHCO Engineering to provide you with this portrait of his enthusiasm for his working life.
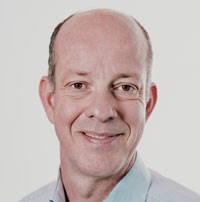
Though now living and working in Denmark, Willy van Well originally hails from The Netherlands where he trained at university to be a chemical engineer working on process equipment. He moved to Denmark to carry out research at university and to teach there. Later, he joined a Danish power plant company and worked on climate mitigation technology projects where the carbon dioxide produced from the exhaust gases in the plants was captured and stored underground. He has also worked as a process engineer with a Danish oil & gas technology company in the North Sea. All in all he has gained much experience in a number of environments in the twenty-one years since graduating with a Ph.D. thesis in 1998. Mr. van Well: “I enjoyed academic life – my Ph.D. looked into conversion processes in the refining of oil & gas products. However, an academic life largely revolves around research, and I began to get the feeling that I was actually doing research just for research’s sake. My product had become publications, so it was a wise decision for me to turn my back on academia and get down to the nitty-gritty of real life situations, which my work in industry has offered me ever since.”
“I now work at ATHCO Engineering, where I am a Senior Process and Sales Engineer. ATHCO Engineering is a supplier of heat recovery projects to the process industry. As its name suggests it has a competent engineering department with specialists in different working areas. These departments take on designing and planning of heat recovery solutions, with the engineering department manufacturing components for its clients in agreement with the specifications drawn up between the two parties. After a thorough quality control the solution is installed at the client’s location. ATHCO Engineering also helps with starting up projects and optimizing heat recovery within existing plants.”
Project tasks
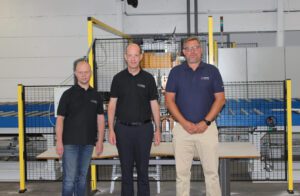
From the left to the right, Senior Engineer Ulrik Nielsen (responsible for building of the machine), Willy van Well and ATHCO’s new Sales Director Niels Bak.
“My work involves me being a single-source partner for clients, in which I am responsible for the complete heat recovery set-up. As such I have contact with customers over a wide range of subject areas, which may start up as early as their first enquiry into our organization. Often this involves a potential customer coming to us with a niggling heat exchanger problem for which he/she needs a solution. Because of my background I’m able to take care of anything involving initial design and dimensioning (my background incorporates thermal design) but, naturally, this is always done in close cooperation with our technical department. As a company we produce part components and projects for all types of process plants, including pressure equipment, and process tanks for heating and cooling, etc. Later on in the process, I also handle pricing and quotations and, in many cases, contract negotiations so it is a very varied package of responsibilities that fall into my lap. This combination makes my work both interesting and fulfilling. It is, further, not only the variety of tasks and projects that prove enjoyable but also the fact that I deal with heat exchanger solutions costing anything between a few thousand and a million euros.”
When it comes to looking at Willy van Well’s project list, around 80% of his time is devoted to new builds, the rest goes into maintenance or refurbishment work. More often than not, new projects will end with his team providing clients with tailor-made solutions. These result out of the conversations, specifications, and requirements that have been discussed from the start-up of negotiations with the client. Generally speaking these are big, specialized designs. Not surprisingly, therefore, the lifespan of projects also varies considerably; some of the quickest are produced in six weeks to two months, whilst some of the largest might take anything up to two years from initial discussions with the customer to actual delivery.
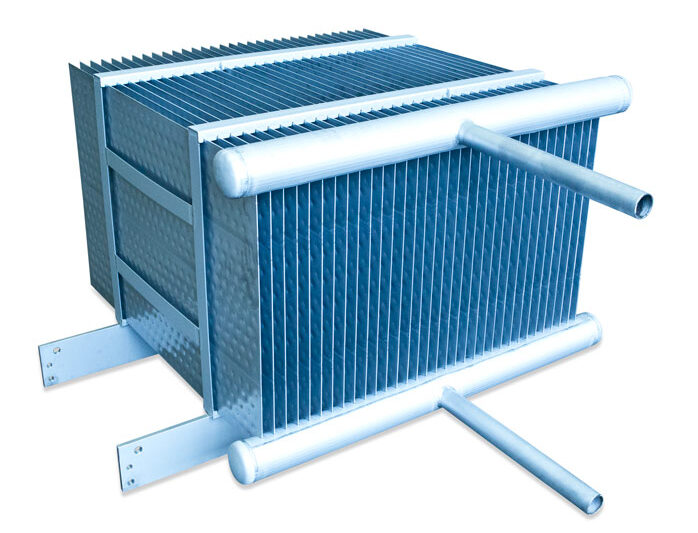
Thermo plate/pillow plate technology
Certainly, what ATHCO Engineering produces in terms of heat exchangers is far from being, run-of-the mill designs and product series, particularly when it comes to pillow plate technology, which is their core specialty competence enabling them to combine their thermo plate (pillow plate) technology with their customers’ requests for heat exchange. A unique feature of the thermo plates is that they are very efficient in heat recovery applications from exhaust gas, waste water, or other ‘dirty’ fluids/gases.
“Heat recovery is not only important for the business economy,” says Mr. van Well “but also for the environment around us. Because of the efficiency of our thermo plate products they provide a remarkable reduction in energy consumption for our clients, which means that they are not only able to achieve production cost reductions and but additionally attain a ‘greener’ profile due to their lower consumption of fossil fuels.”
The thermo plates produced by ATHCO Engineering consist of two plates spot-welded together and they are sealed with welding along their contours. The plates are then expanded until the desired expansion height is achieved.
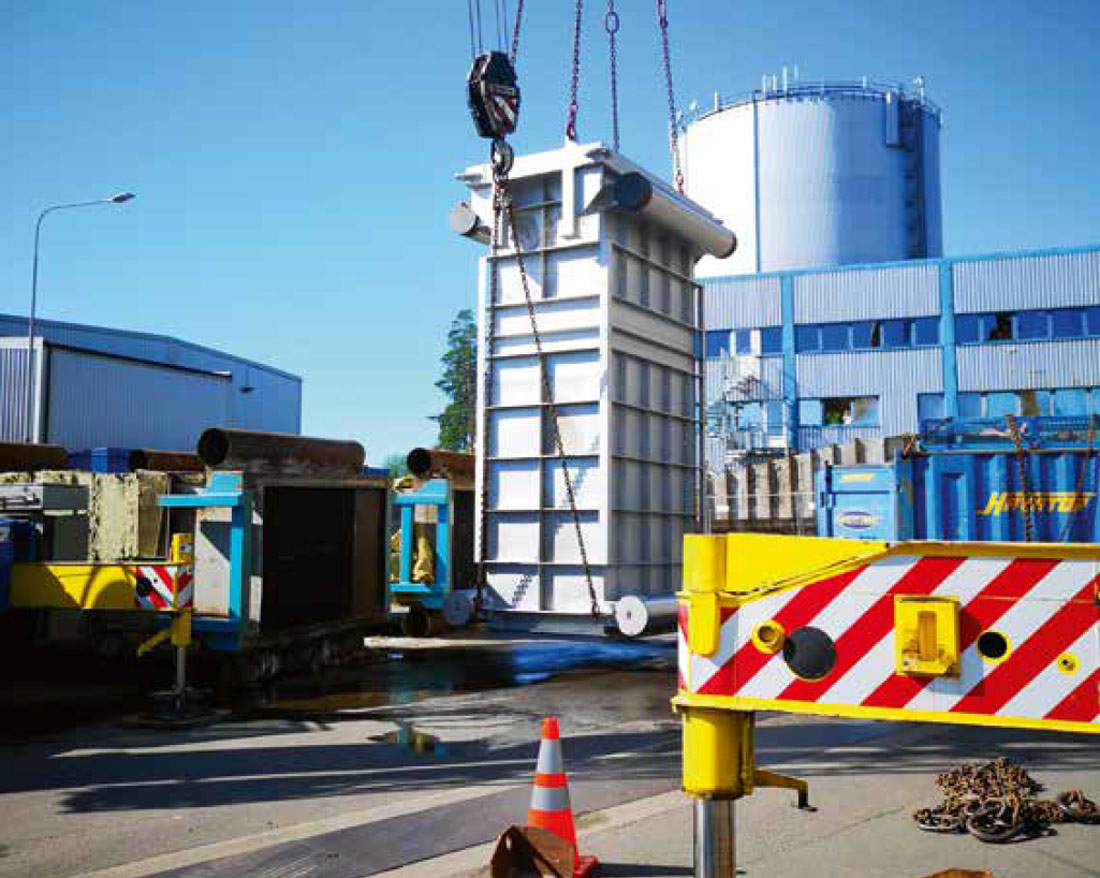
While the thickness and the spot pattern is determined by design pressure, the channel height and the space between the thermo plates in a heat exchanger is determined by flow and allowed pressure drop.
Thermo plates are used for heat recovery in many industries such as food processing, chemical industry, and wood and paper processing, for example, and can be further used for making condensers, exhaust gas coolers, oil coolers, and heat/cooling shells for tanks. Some of the most obvious advantages are that they are very easy to clean, have a high sanitary standard, are thermally efficient having a large surface-to-volume ratio, and have a low pressure drop.
“Some of ATHCO’s largest plate have a length of six-to-seven meters and are one and half meters wide,” Mr. van Well tells us “so in some cases we produce plates of more than 20 square meters. And in the near future we will be able to make even significant larger plates when our new spot welding machine has come into operation.” They are always tailor-made. Moreover, the types of heat exchangers that we produce are manifold. For example, we have the ProcessTherm, which is used for heat recovery heat from dust loaded air (fx from a spray dryer). We also produce a flue gas condenser for recovering heat from biomass power and waste incarnation plants; a top condenser for handling the condensation of organic vapours in distillation columns; the Therm-X, a self-cleaning heat exchanger for heavily contaminated water; the TP-HEX, which is a compact pressurized heat exchanger; and the ThermFlex, a large pressurized heat exchanger for the (petro) chemical industry, fx. as a feed and effluent exchanger.
Work enjoyment
When it comes to work enjoyment, Willy is keen to point out that he is not involved with standard products. Sitting behind a desk and managing standard heat exchanger projects by just typing numbers into a computer program and building what is calculated would not provide him with the challenges he needs. “To come up with complete best solutions for clients you really have to be knowledgeable about what you are doing, ask the right questions, and be able to evaluate and understand the answers you get from them. I am quite often involved with a client from the first stage of a query, through order finalization, to delivery, build-up, and even testing. A challenge that I continually face is introducing companies to thermo plate technology. Even though it has been around for about fifty years, it is not all that well known as it is only used in a handful of applications. Obviously, however, it is not a crusade. The technology we provide has to fit the application and we will only provide thermo plate technology to a customer if it is the most appropriate and best solution for his/her heat transfer challenges,” says Mr. van Well.
FROM ACO TO ATHCO
Before becoming ATHCO Engineering, ACO Engineering Denmark and THP Engineering (Germany/China) worked closely together for several years introducing thermo plate exchangers to the Chinese market. The companies joined forces in 2016 under the name ATHCO Engineering and this European–Asian cooperation has focused on the development and sales of large-scale heat exchangers (up to 2500 m2) and reactor technology based on thermos plate technology for the chemical and petrochemical industry. In China, they are used in a lot of plants where glycol is made based on the gasification of coal.
ATHCO Engineering sees a great potential in the supply of the large heat exchangers based on pillow plate technology. The company is therefore making significant investments to increase and improve its capacity. It has recently a.o. invested in heavy duty cranes in the workshop and it is a the moment building a new spot-welding machine. As part of this strategy, Niels Bak with 30 years of experience within international sales of heat exchangers has joined ATHCO Engineering as Sales Director per 1 September 2019.
About this Featured Story
This Featured Story was first published in Heat Exchanger World Magazine in September 2019. To read more Featured Stories and many other articles, subscribe to our print magazine.
Featured Stories are regularly shared with our Heat Exchanger World community. Join us and share your own Featured Story on Heat Exchanger World online and in print.