The offshore wind industry is booming and will continue to grow.
GE, one of the leaders in the industry, has made a prominent mark in offshore wind power technologies and offshore wind farm development with the Haliade-X, the most powerful offshore wind turbine to date.
Text & images by HEATEX
The case
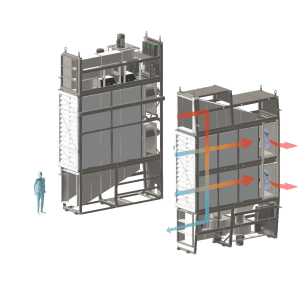
Industry: Wind power systems continue to grow throughout the world. According to the Global Wind Energy Council (GWEC), there was over 60 GW of new wind power installed capacity and production across the globe in 2019. Rapidly expanding government commitments and technological progress are contributing to the positive outlook.
Company: GE Renewable Energy is one of the world’s leading wind turbine suppliers, with over 49,000 units of onshore and offshore turbines across the globe. Mostly ranging between 2 MW to 14 MW.
Application: The heat generated needs to dissipate to ensure the life expectancy of the components inside the nacelle. Heatex develops customized cooling systems for both onshore and offshore Wind Turbines.
The turbines are placed out in the ocean, and as it rotates, the generator creates heat that needs to dissipate. Also, the salty ocean air risks causing corrosion. So after evaluating different cooling technologies, GE decided to go for an airto-air closed-loop cooling system to keep the internal air contaminant-free while cooling the generator.
With every degree that the cooling system can lower the generator temperature, it effectively extends the generator’s life and improves GE’s offered financial return. The more efficient the heat exchangers are, the more efficient the turbines are.
GE was looking for a partner capable of supplying larger modules that meet demanding requirements regarding heat dissipation, quality, production, and cost.
Heatex leveraged its air-to-air heat exchangers to develop a customized system solution to fulfill GE’s specific needs.
Challenges
When converting kinetic energy to electrical energy a large amount of heat is produced in the windings of the generator. That heat needs to be efficiently removed to ensure a long lifetime and high AEP of the wind turbine. With the size of Haliade-X there were several challenges to be addressed:
- Maintaining a sufficient flow of cooled air to the generator
- Designing the heat exchanger with an optimal balance between heat transfer and pressure drop to minimize the total power consumption
- Keeping the size of the system within specified limits while reducing the total weight
- Selecting materials to last a minimum of 25 years in offshore environment
Solution

Many months were spent on full-scale performance testing in Heatex’s test laboratory, proving that the system would provide adequate cooling power. In addition, more than ten different materials and coatings were tested to ensure sufficient corrosion resistance and durability (25+ years).
The cooling system consists of two units on each side of the nacelle. The outside air is pulled into the system via inlets and runs in a closed loop, ensuring the out-and inside air never mixes.
The system was designed around Heatex’s modular cross flow heat exchangers for high heat transfer efficiency and low pressure drop. Fans were optimized accordingly to reduce total power consumption and weight.
The framework was designed as an integrated part of the structure inside the nacelle, equipped with interfaces for transport, lifting, and service.
Results
Verified Performance: 100% verified cooling performance in full scale tests at Heatex’s own lab facilities. 700kW Cooling Capacity Cooling capacity in such a narrow space required highly efficient plate heat exchangers.
Low Maintenance Costs: self-cleaning heat exchangers require minimal maintenance.
High Cooling Capacity: heat exchangers, fans, and ducts were designed and tested as a complete system to avoid losses and secure high capacity.
Moderate Power Consumption: fully adjustable power consumption was based on actual operating conditions and cooling needs.
Solid Cooling Efficiency: plate heat exchanger technology contributes to increased heat transfer and overall efficiency.
About this Featured Story
This Featured Story was first published in Heat Exchanger World Magazine in April 2024. To read more Featured Stories and many other articles, subscribe to our print magazine.
Featured Stories are regularly shared with our Heat Exchanger World community. Join us and share your own Featured Story on Heat Exchanger World online and in print.