^ Two operators move a new 100-ton boiler from bay-to-bay in a manufacturing facility.
By Randy Manus, Senior Application Engineer at AeroGo, Inc., Seattle, WA, USA
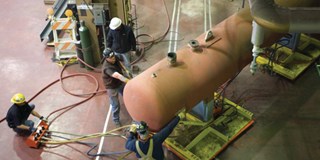
Transporting heat exchangers, boilers and pressure vessels poses a significant challenge. Their sheer size and weight turn manufacturing, repositioning, or replacing the components into a major production. Worse, traditional load moving options like forklifts, cranes, wheels, and riggers fail to answer the central challenges of dealing with heat exchangers specifically. The constraints of each – such as the space required for forklifts or the need to ensure the machines fit within a crane’s capacity and reach envelope – limit how easily those tools can manage the move.
So, Cleaver-Brooks, an industrial boiler manufacturer, was genuinely excited to find a material handling solution that made it possible to easily move 100-ton boilers with just two operators, even along twisty pathways and through doorways, all without hindering operations.
The technology that made it possible: air casters.
What are air casters?
Developed in the 1950s by the aerospace industry, air casters are donut-shaped bags that inflate with compressed air. As excess air escapes, it seeps under the bag to create lift, thereby floating the load on an ultrathin film of compressed air.
Air casters operate similar to an air hockey puck or hovercraft but with much better operator control. Once floating and nearly frictionless, air casters require relatively little force to move even very heavy loads. On most floor surfaces, operators need to exert only 5-25 pounds of force to move loads of up to 5,000 pounds when using air casters, compared to 300 pounds of force to move a load of the same weight when using wheeled casters. As a result, even just a few operators can glide machinery across a floor. Even better, air caster systems are easy to operate, requiring no certifications and thus eliminating the need to ever wait for an operator, such as is required for forklifts or cranes.
As a result, air casters can also more easily move heat exchangers that weigh tens of thousands of pounds. This is how Cleaver-Brooks found its solution. By using quickattach power drives with air casters under their 100-ton boilers, they could transport even genuinely super-sized objects that would ordinarily obstruct or shut down a production process. As an added bonus, by dispersing the load over a large surface area, air casters offer a typical maximum surface load of less than 50 psi, dramatically reducing floor point loading and the risk of floor damage.
Floating on air versus using traditional methods
While forklifts, cranes, wheels, and riggers are more common choices for replacing or repositioning components and equipment like heat exchangers, they only introduce new challenges to solve.
For example, in tightly constrained work environments, such as replacing a heat exchanger in a 40+ year old nuclear facility, there is no room to spare for forklift counterweights or crane installation. By contrast, air casters fit within the footprint of the heat exchanger, boiler or vessel and require no additional space in which to maneuver.
Reducing the work envelope is a vital benefit when attempting to move giant components in tight spaces.Similarly, increasing movement flexibility and maneuverability is critical in constrained environments. Air casters shine in this respect: since the load being moved is literally floating on air, air casters glide in all directions with equal efficiency and can rotate in place. This makes it possible for organizations to navigate even huge, 100-ton heat exchangers through maze-like corridors with sharp, narrow turns. Operators can glide large components from one area to another with precision and then accurately position the heat exchanger in a new location. Once it reaches its destination, operators simply deflate the air casters, and the machine gently settles into its new position.
When moving on air, production efficiencies can go sky high
In terms of productivity and efficiency, this flexible movement results in reduced labor and downtime and faster load movement than any other material handling equipment.
As one operator stated, “It took minutes instead of hours to move that heat exchanger.” This means, depending on the facility, it’s possible for even major moves to be completed without shutting down.
Safety is also inherent to the air caster method of heavy load movement. Loads are floated on a film of air as thin as a business card, keeping the weight low to the ground and disbursed across the floor surface. With air casters, heavy and awkward loads stay low to the ground and maneuver smoothly, reducing risks to operators, equipment.
Air casters offer a viable and proven transport tool
Moving heavy, awkward multi-ton components such as heat exchangers, vessels and boilers can be accomplished numerous ways, but air casters unambiguously conquer environmental constraints and enable operators to move components with the greatest degree of precision, ease, and speed. Air casters have proven that the process of moving a typical heat exchanger can be completed in significantly less time than cranes or forklifts can accomplish, especially when the job is performed in a constrained environment. Air casters greatly reduce cost and complexity and provide a low risk, low downtime method to accomplish the move, with minimal manpower and without causing slowdowns. As a result, air casters can make all the biggest problems with moving heat exchangers and related equipment disappear into thin air.