The Ohio-class ballistic missile submarine USS Nebraska (SSBN 739). (Source: Dreamstime)
Submarines: deadly, hard to detect, and the setting of many a tense war film. They are also fantastic examples of human ingenuity, allowing for lengthy missions in an environment that humans are not designed for. Underwater, you need to have confidence in your vessel. There is pretty much nowhere worse for a piece of engineering to go wrong!
All text and images (unless stated otherwise) courtesy of Sterling Thermal Technology
The work Sterling TT does in the defence industry, cooling submarine parts, is designed to give submarine engineers control over their technology. It brings with it a unique set of challenges. Let’s talk about some of them.
What needs cooling on a submarine?
Submarines have a diesel engine or nuclear reactor that generates electricity to store in batteries. In this blog, we will talk primarily about diesel engines.
This electricity is used to power the propulsion motor, which turns the propellers. The same electricity is also used to power the onboard equipment.
Therefore, the cooling needed in a submarine is primarily for the following components:
• The diesel generator
• The propulsion motor
• The electrical cabinets connected to other equipment
Why is cooling important?
If components overheat, they may become damaged. A damaged generator won’t be able to generate electricity. Damaged motor? A damaged motor means the boat comes to a stop. These systems have a maximum temperature, and it is the job of the cooling to keep the temperature under control.
What if there is an issue with the cooling? The boat may be able to keep temperatures down by reducing the performance of the equipment (for example, slowing the vessel boat). However, submarines cannot operate optimally without high-performance cooling.
For electrical cabinets, the biggest risk is the water contacting the electrical components. To ensure this doesn’t happen, the cooling components are titanium and fully welded.
In a military setting, it is of course dangerous for submarine performance to be suboptimal. Therefore, a high-quality cooling system with appropriate redundancies in place is extremely important.
What sort of coolers are used?
The coolers themselves are standard fin-tube units that use water as a cooling medium, similar to a car radiator but on a larger scale. The water that runs through the tubes comes from the seawater outside the boat. The water is distilled onboard, taking out the salt and making it suitable for use as a coolant. The cooling units may be of a single tube or double tube design, but most of the time single tubes are used for one simple, but very important, reason: they are lighter.
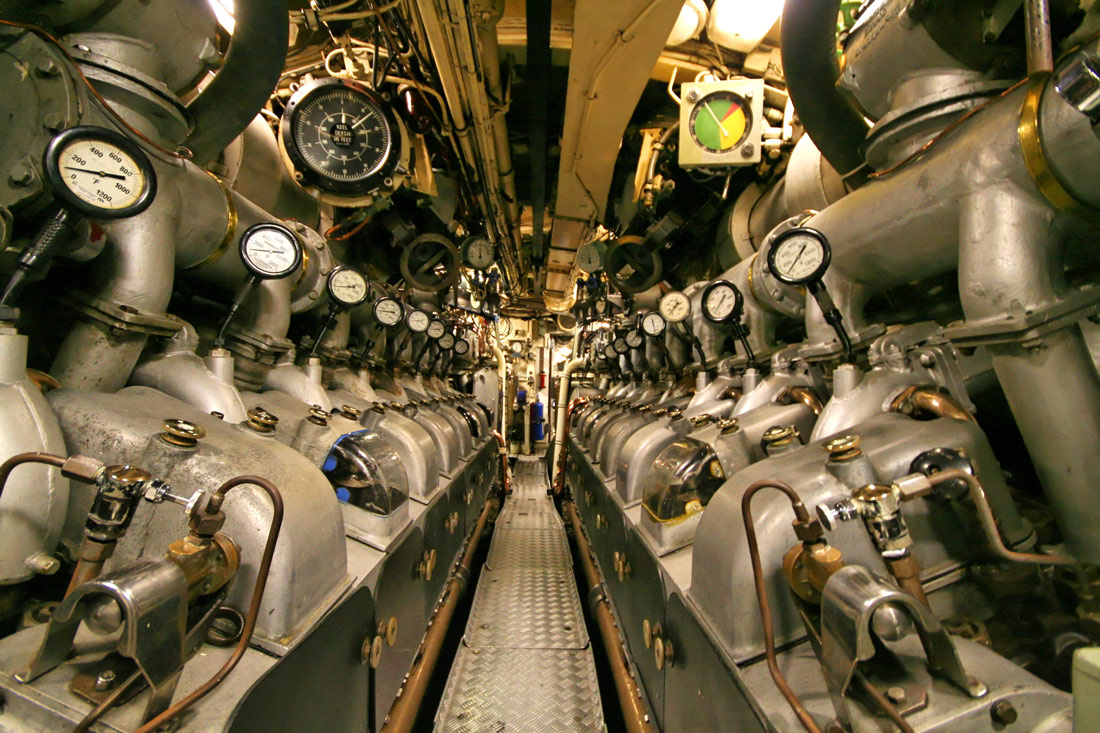
The size/weight challenge
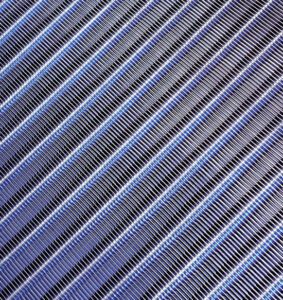
On a submarine, space and weight are at a premium. Everything that can be done to reduce the size and weight of the equipment is usually a priority. Every 1kg that the cooler is lighter means 1kg that can be used for other supplies.
In the past, cooling units used to be made of copper-nickel. These days titanium is used instead, partly due to the weight advantage.
As well as weight, we also have to contend with the limited space and the typical shape. Any coolers have to be designed and built to fit the submarine’s tube-like hull. This might mean making curved parts to maximise the use of space. An additional factor is getting replacement parts into the sub — those parts have to fit down the hatch! Coolers need to be designed so that they can be dismantled into parts no larger than the diameter of the hatch (perhaps 1m across).
What redundancies are needed for a submarine cooler?
When designing for a submarine, our clients in the defence industry will specify the “failure modes” that a cooler design needs to meet.
For instance, what if a certain part of the boat was to go into emergency shutdown? Would the cooler still be able to perform? What if the fans on the cooler fail? What if, due to a pump failure on the submarine, the cooler only receives half of the water?
The designs take into account a range of situations to ensure the equipment can withstand a range of eventualities – no matter how unlikely.
Submarines tend to have tandem motors. Two coolers per motor is a common design. Each of these coolers is a “100% cooler”. It means that, individually, they are theoretically capable of providing all of the cooling that the motor needs. Another way to put it is that we oversupply cooling so that if there is a problem, there is plenty of backup cooling to keep the motors at an optimal temperature.
Another contingency on the cooler is the doors that can be opened to let in air, helping to keep temperatures within necessary limits.
Our job is to design a system that can withstand suboptimal conditions and failure states to keep on running. It is sometimes described as meeting “part duties”, “reduced duties” or “70% duty”.
Sometimes the client introduces a new failure mode that we have to cover during the process, which prompts a review of the design. We always work in conversation with clients to ensure we provide equipment fully fit for purpose.
The challenges of designing equipment for the defence industry
As you might expect for products manufactured for the defence industry, there is the issue of confi dential information that needs to be kept secret. That usually involved NDAs that prevent the disclosure of technical information about the submarine design. Usually, we wouldn’t see the whole submarine design. The work is compartmentalised, and we only see aspects of the design related to the coolers’ placement and cooling systems.
Even after the cooling unit is finished, information about pressure ratings and G-Loadings for the equipment may be carefully controlled.
As submarines are defence vessels, we must consider that the equipment may suffer damage while on duty. Submarines are warships, after all. That’s why our coolers go through extensive shock testing before installation.
A final consideration is the risk of hacking. Almost anything on a computer connected to the internet can be hacked in some way. It’s never a more serious concern than when it comes to military computers. If our coolers could be hacked, an entire submarine could be brought to a very dangerous halt. We work with our defence clients to design equipment that hostile actors cannot shut down remotely.
What is the design process of a submarine?
A submarine may take 10 years or more to design and build. Sterling TT is brought on fairly early in the process, and our part may involve multiple years of prototyping coolers before they are finally manufactured and installed.
Part of the reason for the length of this process is that the submarine design will develop over that period, and our cooler designers will need to evolve to take this into account. We may also be given new specifications for the coolers, such as an additional failure mode.
Repairing coolers on a submarine
Though we consider our excellent aftersales service and repairs to be something that sets our organisation apart, we don’t actually do many repairs for submarine equipment.
That is because a submarine and its crew must be a self-sustaining system. The crew technicians address issues with equipment, including coolers, while onboard.
It’s a different story for surface ships where we sometimes perform cooler repairs. Because of some of the locations surface ships travel to, less than ideal coolants are pushed through the unit pipes, such as sandy water. This causes erosion and requires servicing. This is less of a risk on subs.
About the Company
With decades of experience providing heat exchangers for the defence industry, Sterling TT has the expertise required to work on submarines as well as surface ships. A submarine is an advanced and complex piece of military equipment. Being involved in making one is a unique challenge, one that requires decades of experience and engineering expertise. But it is a challenge that the company is proud to be a part of.
About this Featured Story
This Featured Story was first published in Heat Exchanger World Magazine in May 2022. To read more Featured Stories and many other articles, subscribe to our print magazine.
Featured Stories are regularly shared with our Heat Exchanger World community. Join us and share your own Featured Story on Heat Exchanger World online and in print.