This article outlines the common causes associated to air cooled heat exchangers (ACHE) header plug leaks and the required repairs, maintenance scope and inspection guidelines for its resolution.
By Miguel Gutierrez, Field Consultant Engineer at GME – Asset Technical Solutions in Saudi Aramco
ACHE header plug leaks in the oil and gas industry are considered one of the main unsafe events associated to a loss of process containment with immediate impact in the safety of the facility, leading in most cases to unplanned equipment shutdown with the subsequent production losses. The main objective of this document is to list the most common causes of header plug leaks and how to resolve them by following best industry practices utilizing dedicated repair methods that cover all aspects such as workmanship/assembly supported by stringent QA/QC requirements, all this in order to ensure a leak free plugsheet – header plug joint enhancing the equipment reliability, integrity and plant safety.
Types of header plugs
Header plugs are mechanical components of an ACHE equipped with plug-type header boxes and their main function is to allow access for cleaning, individual tube examination, welding, rolling or re-rolling of the tubeto-tubesheet joint and plugging in case of tube leaks.
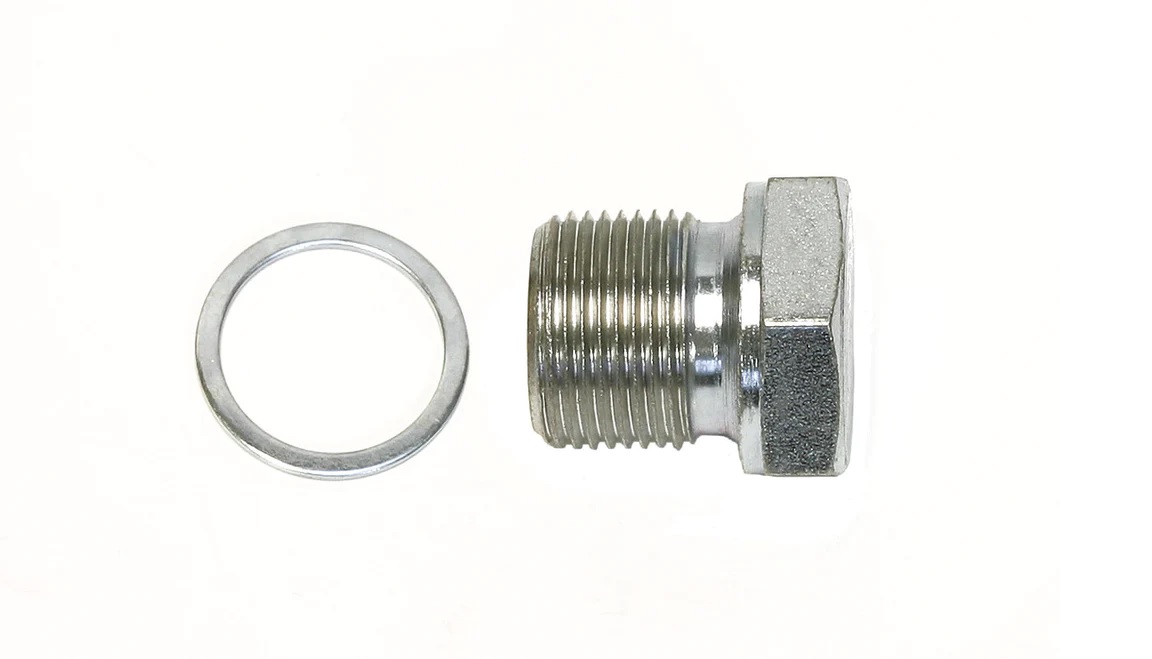
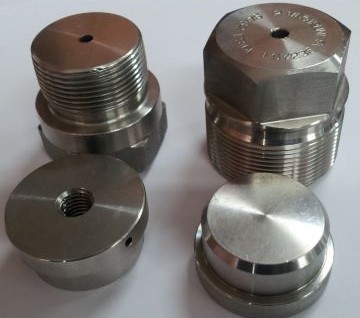
There are mainly two types of header plugs, selfcentering shoulder plugs (Fig.1) and two-part plugs with gasket compressor (Fig.2). The sealing between the header plugs and the plugsheet is achieved by utilizing solid metal gaskets (Or washers) which are normally softer than the plugsheet spot face.
Header plug leaks common causes and resolution
The most common causes for ACHE header plug leaks are the following:
1. Wrong gaskets material:
The use of inadequate materials not compatible with the service will initiate corrosion/degradation of the gasket leading to premature leaks. It is also well known that a dissimilar metallurgy (Plugsheet – Gaskets) can initiate galvanic corrosion on the spot face affecting the joint integrity. Moreover, the selection of inadequate materials will impact in the gasket sealing ability, this is because the required plug torquing might be either insufficient (Lower than the minimum required gasket seating stress) or excessive (Higher than the maximum gasket seating stress) which will crush the gasket. In addition to the above, there are some other important aspects related to the gasket manufacturing process that must be considered such as:
- Gaskets shall be made of annealed solid metal preferable of the same material as the header plug.
- For flat gaskets which are machined, the top and bottom contact surfaces roughness must be between 1.6 to 3.2 μm (Smooth finish).
- Gaskets ID and OD shall be laser cut to provide a clean and smooth flat surface.
- If punched gaskets are used, care shall be taken to remove shear lips and burrs. The gasket shall be free of burrs to eliminate any high spots that might affect the sealing ability.
2. Inadequate plugs specification:
Header plugs design and material selection is critical to achieve a seal tight plugsheet – header plug joint. Among the most common deficiencies that significantly contribute to leaks are the installation of header plugs that are not provided with self-centering shoulder which avoids to properly center the gasket limiting an equal gasket compression during plug assembly/torquing. Another critical aspect is the inadequate selection of header plugs in services that can initiate crevice corrosion. Ideally, shoulder plugs are designed with hexagon heads and parallel shank that is long enough to completely fill the plugsheet hole threads. In cases where crevice corrosion is likely to occur in the plug threads that are in contact with the process fluid, then two-part plugs with gasket compressor shall be specified (See Fig.2).
One important common cause of leaks is associated to plug threads galling, which results in damaged threads, weakened joints and seized plugs. This phenomenon normally occurs in austenitic stainless steel and nickel alloy plugsheets – header plugs assembly and the contributing factors are related to threaded connection interference fit as per ASME B1.1 and the use of materials with the same hardness. A solution to this problem is to specify the materials in order to maintain a minimum difference in hardness between the plug and plugsheet of around 30 to 50 BHN (Header plugs are the hardest material) and upgrade the threaded connection to standard fit maintaining the tolerances specified on ASME B1.1.
3. Plugsheet spot faces imperfections:
Minor spot face dents or scratches are mechanical damages attributed to poor workmanship during the removal/disassembly of the gaskets when using inadequate mechanical tools. Another possible cause of spot face damage is due to gasket excessive rotation during assembly/torquing when using gaskets with high hardness not meeting the minimum requirements during the manufacturing process as discussed above. Spot face corrosion damage in the form of pitting corrosion is another factor that is commonly observed, and it is influenced by the corrosivity of the process fluid and material compatibility. In order to guarantee a leak free joint and to ensure a reliable equipment operation, during the execution of routine maintenance activities and repairs is recommendable to machine those identified damaged spot faces (See Fig.5) to a surface finish (Average roughness) between 0.8 μm and 3.2 μm as per API 661. In case the minimum spot face surface finish requirements after machining is not achieved and mechanical damage is still visible, a potential solution that will avoid weld repairs is to implement the use Kammprofile gaskets which can be easily accommodated on the spot face filling the cavities and ultimately achieving a tight seal. The use of these gaskets also helps to prevent galling, thread sheer and thread stripping while requiring less than half the torque of traditional gaskets.
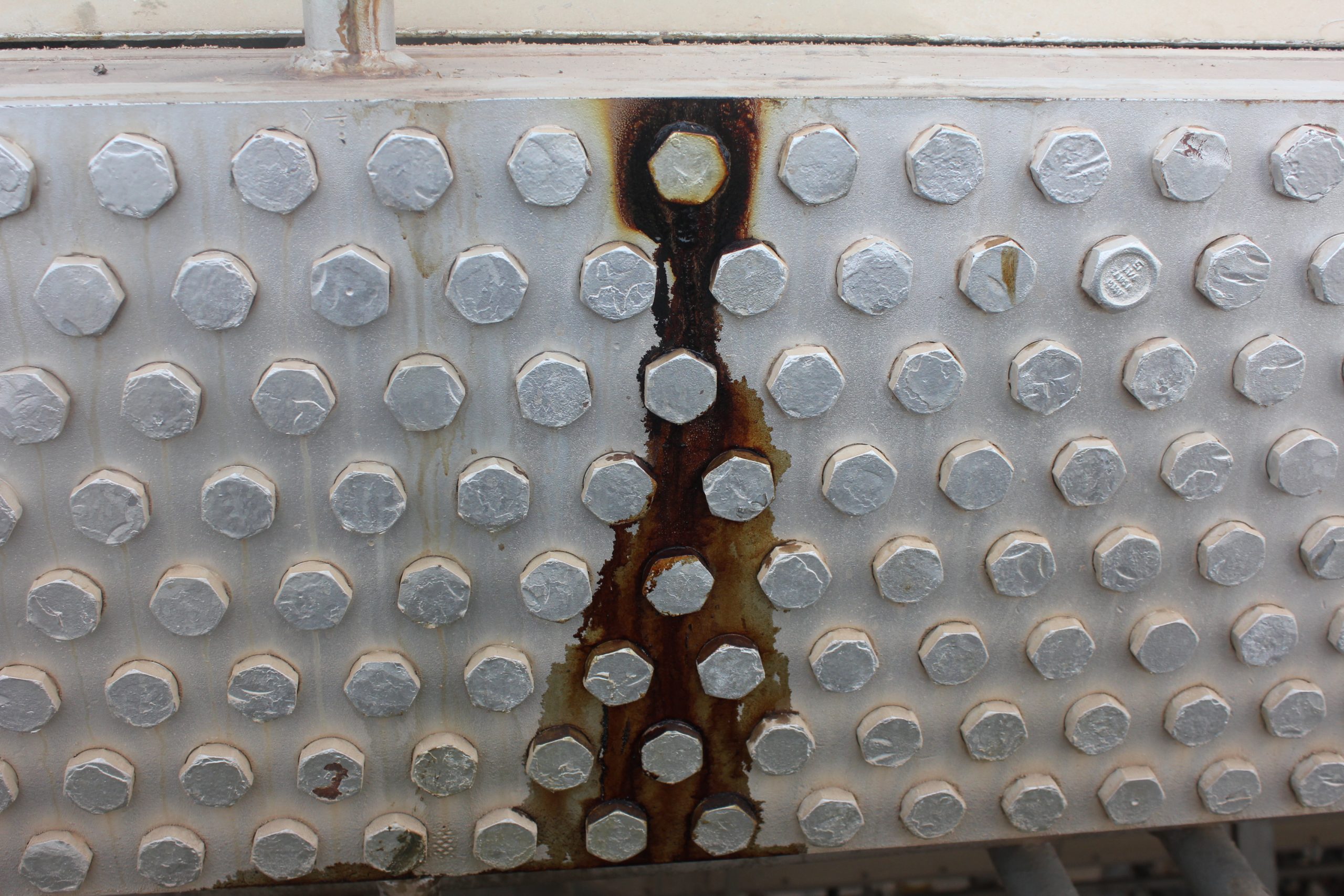
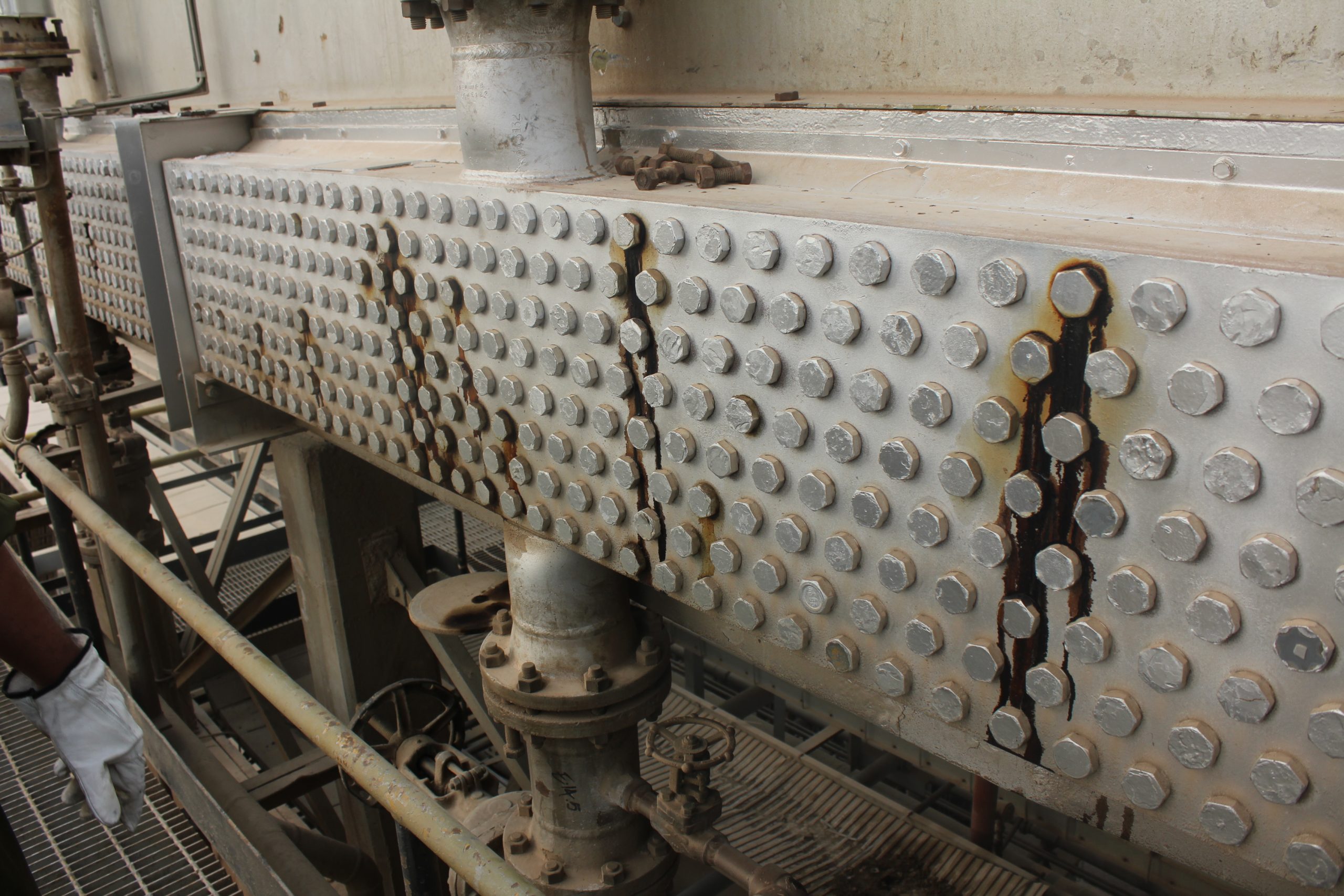
4. Plugsheet thread damage:
Similar to inadequate plugs specification as mentioned above, plugsheet threads damage are also associated to crevice corrosion and thread galling (Fig.4). An important factor to consider is that during the equipment manufacturing when drilling the plugsheet holes, the machining method utilized to drill and make the threads plays a vital role to mitigate the galling effect after the equipment is placed in service. That is why it is imperative to specify the use of the thread rolling method in lieu of thread cutting method to prevent thread galling and maintain an adequate mechanical fit with the required tolerances as per ASME B1.1.
In order to repair plugsheet threads damage during equipment routine maintenance activities, it is recommendable to proceed in the following sequence:
Re-tapping the threads with the same size tap “chase the thread” and verify the tolerances as specified on ASME B1.1.
- In case re-tapping is not sufficient to rectify the threads damage, proceed by enlarging the plugsheet hole to the next available size provided ligament efficiency calculations as per ASME VIII Div 1 Appendix 13 are conducted (Verify membrane and bending stresses at the plugsheet are below the maximum allowable stresses).
- In case enlarging the plugsheet hole size is not possible for any other reason in addition to not meeting ASME code verification (Ligament efficiency calculations), proceed to weld build up, drill and machine the plugsheet hole to the original size maintaining required tolerances as per ASME B1.1. Despite this is an acceptable solution, it is not desirable and will be considered as the last choice since excessive heat input during the welding process might compromise the ligaments of adjacent plugsheet holes. Another reason is that header box heat treatment (Stress relief) is necessary after major weld repairs are done and there is a potential for header box distortions affecting the tube to tube sheet joint in case the tube bundle is still in place. It is important to highlight that during the rectification of the plugsheet holes including the spot face machining; verification of the perpendicularity, thread slop and flatness are carefully measured to ensure they are within the required tolerances (Part of QA/QC).
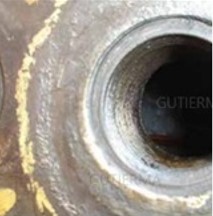
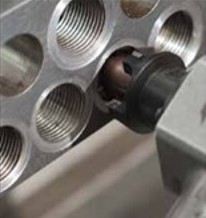
5. Improper torquing:
Inadequate torquing leads to plug leaks due to either insufficient gasket stress (Lower than the minimum required gasket seating stress) or excessive (Higher than the maximum gasket seating stress) which will crush the gasket. Therefore, it is important to carefully review the design parameters especially the lubrication factor when performing torquing calculations by using any of the available methods such as ISO 16047, K factor approach or ASME PCC-1 gasket stress.
6. Lack of QA/QC:
It is important to establish a stringent QA/QC procedure that incorporates important steps during routine maintenance activities and major repairs of ACHE plugsheet such as material traceability (gasket and header plugs manufacturing records), dimensional verification (perpendicularity, flatness, thread slop, surface finish, projection of spot face, thread tolerances, etc.), installation sequence, use of proper lubrication, torquing and pressure tests.
7. Poor or inadequate maintenance repair procedure:
In most of the cases, the lack of a qualified procedure and skilled labor for ACHE routine maintenance activities and major repairs is one of the factors attributed to header plugs premature leaks when the equipment is put back in service. One of the most important steps to consider in the repair procedure are the special precautions to take during header plugs and gaskets removal to avoid plugsheet threads and spot face damages. Also, in case rectifying (Repairing) a damaged plugsheet is part of the maintenance scope, the utilization of adequate tools for drilling, tapping and machining by specialized personnel is paramount and it must be complemented by a dedicated QA/QC as mentioned above. Additionally, in case of a major scope of work such as weld repairs, it is important to ensure a qualified welding procedure and skilled welders are utilized. On regards to the manufacturing and procurement of header plugs and gaskets to be utilized for ACHE routine maintenance activities, it is important to ensure these items are fabricated by qualified vendors following the more stringent QA/QC requirements and meeting client and standard specs without deviations. A good practice is to develop specific ITPs for header plugs and gaskets including steps starting from the pre-fabrication, in process inspection up to final inspection and testing requirements that must be witnessed and signed by the buyer representative or 3rd party inspector and supported by mill certificates provided by the vendor supplier.
Conclusion
With the implementation of a dedicated routine maintenance scope of work supported by stringent QA/QC requirements for the reconditioning of ACHE plugsheet or major repair of leaking header plugs, it is expected to improve the reliability, maintainability and safety of ACHE, which will eventually translate in reducing maintenance costs and avoid plant downtime due to
unexpected failures (leaks) during normal operation.
References:
1. API 661 – Air Cooled Heat Exchangers
2. ASME PCC-2 – Repair of Pressure Equipment and Piping
3. NB23 – National Board Inspection Code
4. ASME B1.1 – Unified Inch Screw Threads
5. IOGP S-710 – Supplementary Specification to API 661 Air-Cooled Heat Exchangers
6. AJER – 2320-0847 p-ISSN: 2320-0936 – Torque Tightening of ACHE Header Box Plugs
7. NACE Paper C2020-15197 – Air Cooler Plug Gaskets Leakage During Startup
About the author
Miguel Gutierrez is a Senior Mechanical Engineer with over 30 years of experience in the oil and gas industry, particularly in the Downstream Business showcasing his expertise in stationary equipment. His focus on piping/pipelines, pressure vessels, heat exchangers and storage tanks, along with handson trouble Miguel Gutierrez shooting during plant operations and turnarounds, reflects a comprehensive skill set. His international experience in Venezuela, the Caribbean Basin and the last 18 years in the Middle East adds a global dimension to his professional profile.
About this Technical Story
This Technical Story was first published in Heat Exchanger World Magazine in March 2024. To read more Technical Stories and many other articles, subscribe to our print magazine.
Technical Stories are regularly shared with our Heat Exchanger World community. Join us and share your own Technical Story on Heat Exchanger World online and in print.