Inspection of heavily fouled water inlets and condenser tubes at a power plant.
Termanox is a Dutch start-up founded on years of experience in water treatment. With funding from the NOM and FOM Regional Investment Funds from the North of the Netherlands, its team is looking for partners to run a pilot project to prove the effectiveness of a unique compound that prevents biological fouling in (open) cooling water systems. As a new player in an industry dominated by giant chemical companies, the Termanox team are rising to this ‘David vs Goliath’ challenge to bring their environmentally and economically friendlier product to the global market.
By Joanne McIntyre, Heat Exchanger World
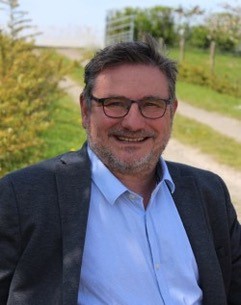
Stefan Spaas was a co-researcher with the Dutch KEMA Research Institute when he first encountered an amine-based antifouling product that would eventually change his career. At the time, he was part of a research team carrying out projects for the power generation industry, focusing on environmental issues such as emissions and CO2 reduction. A French chemical manufacturer had developed a product to treat cooling water in heat transfer systems based on amines to mitigate biological organisms.
“This was a radically new approach to prevent biofouling, and we were asked to research its effectiveness,” explains Stefan. “Traditionally, biological load in water is treated by adding toxic chemicals at a high enough concentration to kill organisms, thereby preventing fouling of heat exchangers, pumps, piping systems, etc. This new product had a totally different approach, based on the premise of: why treat all the water when fouling only occurs where the water touches a surface, such as the inside of a pipe or heat exchanger? The product migrated to the pipe wall, creating a film that prevented fouling. The idea intrigued me because while a power plant operates with huge volumes of water flow, very few organisms actually come into contact with these surfaces…so why fill it with chemicals?”
Eventually, the French company pursued other areas of interest and agreed to sell the newest developed patent. Stefan and a group of colleagues formed Termanox and started their journey to perfect the product, defend the patent and then launch the product onto the market under the name Blueterm®. The Termanox team’s research and intensive testing resulted in an updated recipe that was equally effective, cheaper, and easier to produce and handle. In the new-and-improved version, some of the film-forming compounds were replaced with an exopolysaccharide. Termanox is now seeking industry partners to undertake pilot projects to prove the unique product concept.
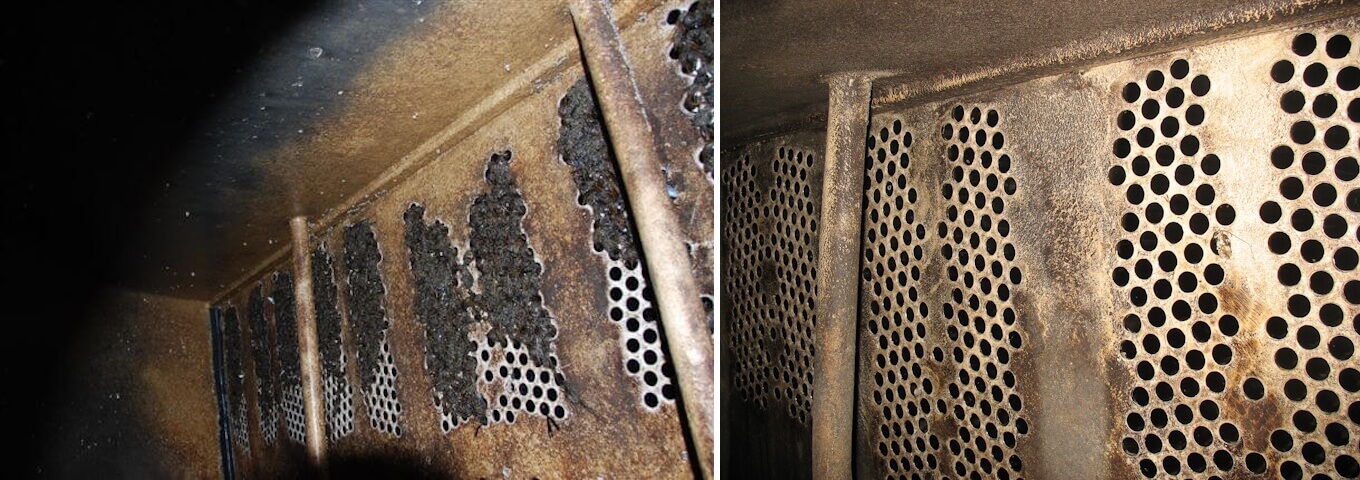
Research pilot project
“Research has proven the effectiveness of Blueterm®, but as a small player in a global chemical industry dominated by a handful of very large manufacturers, it’s challenging to break into the market,” explains Stefan.
Eventually, the team decided to go it alone, marketing Blueterm® themselves.
“While there has been a great deal of interest from power companies, it’s critical that we carry out more research to prove the effectiveness and raise awareness. In the summer of 2021, we carried out a Proof of Concept with seawater at a power plant on the Maasvlakte in the Netherlands. A test rig was built inside a container with a cooling water bypass, and an independent company carried out the study and compiled the results. We had our Proof of Concept within a few months and began promoting the product.”
How does it work?
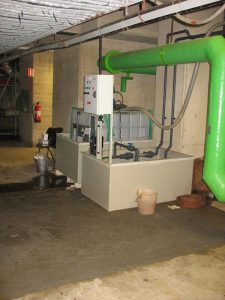
Blueterm® is a unique patented formulation intended to treat open or semi-closed industrial cooling water circuits supplied with sea, fresh or brackish water. It effectively prevents the development of micro and macro biofouling (oysters, mussels, barnacles, hydras, etc.). The reduction of biofilm and sludge generated by macro biofouling reduces the phenomenon of bio-corrosion and therefore industrial maintenance.
Blueterm® is an organic formulation dissolved in water. It is a combination of a long-chain aliphatic amine with a highly specific exopolysaccharide (EPS). The synergistic effect makes the treatment extremely efficient compared to traditional methods. Moreover, Blueterm® contains no oxidizing components, quaternary amines, aromatic compounds or heavy metals.
The amine penetrates the biological membranes and the biofilm. This integration disrupts the coherence of the biological structure and leads to the destruction of the membranes. This is fatal for micro-organisms and for macro-organisms; the treatment causes a stress condition that is sufficient to prevent their permanent settlement. At the proper concentrations and duration, it is ultimately also fatal for macro-organisms (barnacles, hydras, etc). However, the aim of the treatment is to prevent fouling while reducing chemical use to a minimum.
The EPS acts as a surfactant that ensures that the active substance reaches the places where the problems arise. This means that you do not have to treat the entire water flow but only the surfaces of the system.
Environmental & economic advantages
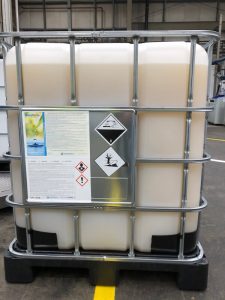
Stefan highlights how Blueterm® can help companies and operators reach their Sustainability Development Goals (SDG) while saving money. “This is a simple drop-in product, which enters the system and creates a film layer on every surface, preventing the attachment of biofilm and biological organisms such as mussels, larvae, barnacles, etc. The film is maintained by dosing a very small amount of the product daily. We are confident that it can also reduce anti-scaling chemicals and reduces microbiological induced corrosion, but for the power generation market and Termanox’s target, biofouling is the primary concern,” explains Stefan.
The advantages include:
- Biodegradable,
- Creates no by-products,
- 95% less chemical required than chlorine,
- Reduces operator’s CO2 footprint, storage footprint, and transportation footprint, when compared with chlorine by 95%,
- Made from natural renewable resources,
- Active compounds can be produced CO2 neutral,
- Non-reactive compound,
- Dosage time just 30 to 60 min/day,
- Simple drop-in product.
“Power stations use vast quantities of chlorine and other highly reactive, toxic chemical compounds to fight biofouling. These chemicals are ultimately discharged into the surface water, where they continue to react and create toxic by-products, some even more harmful than chlorine. Desk research indicates that Blueterm® has a PNEC (Possible No Effect Concentration) value similar to chlorine, which means it is as toxic to biological organisms in water treatment systems as chlorine. However, it produces no by-products, is readily biodegradable, and all components in the biodegradable chain are less toxic than the original product.”
But most significantly, comparing Blueterm® to chlorine, 95% less chemical is required to achieve the same antifouling effect, dramatically reducing risk, transportation costs, and storage. “That means 95% less handling of a chemical product,” explains Stefan. “For a typical power station, that means 95 % fewer trucks delivering to your plant. Furthermore, power plants routinely store many tons of chlorine on site, which is hazardous, requires permits, and is a risk for accidents and human health.”
“There is also a significant environmental saving in the production of Blueterm® vs chemicals such as chlorine because it is based on naturally occurring compounds with a far lower environmental impact than chlorine, and it is produced using far less energy while generating much less CO2.”
Monitoring biological & environmental impact
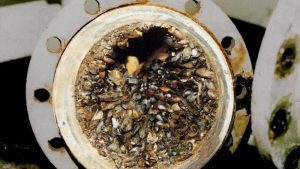
Stefan is keen to emphasize the environmental benefits of Blueterm®, and Termanox is willing to invest in extensive monitoring to gather data on its effects.
“Ideally, you would only start adding an antifouling product to a water system when fouling starts,” explains Stefan. “We can do this by monitoring the system, adding the product at the perfect moment, and then monitoring its effect to minimize eventual discharge into surface waters. In our next pilot project, we will conduct extensive monitoring to measure the environmental effects in the receiving water where the cooling water is discharged, the concentration of chemicals, etc, to study its behavior effects based on actual measurements. We aim to achieve as close to zero discharge into the surface water as possible while maintaining effectiveness. This is a completely new approach; power plants currently discharge the maximum allowed levels of chlorine and other chemicals into the surface water.”
“We want this technique to become known and accepted around the globe and to prove that it’s greener than the current treatments. Hopefully, we will soon find a partner to embark on this exciting journey with us,” concludes Stefan. “There are so many possibilities worldwide.” .
Looking for a pilot project
Today, the Termanox team is looking for a site to prove their product on a larger scale, and they have funding to pay for it. “The potential applications are vast; wherever there is water cooling, there is biofouling. At this stage, we want to focus on the power industry to run a pilot project to prove the technology,” explains Stefan.
Termanox has received funding from the Dutch government to pay an operator to hold trials on a larger scale than those carried out so far. “Our aim is to run trials on a large site, possibly a seawater system, on a non-critical part of the cooling system. We’re looking for a site anywhere worldwide,” explains Stefan.
Interested parties are invited to contact Stefan Spaas at tel: +31 6 51 12 17 69, email: s.spaas@termanox.com or via the Termanox website www.termanox.com
About this Featured Story
This Featured Story was first published in Heat Exchanger World Magazine in April 2024. To read more Featured Stories and many other articles, subscribe to our print magazine.
Featured Stories are regularly shared with our Heat Exchanger World community. Join us and share your own Featured Story on Heat Exchanger World online and in print.