AEL style stacked chiller.
Alabama Heat Exchangers is an engineered-to-order fabrication and repair company, that has been in business since 1986. Heat Exchanger World spoke to President and CEO Ricky Lightcap, Jr., to learn more about the family company culture, the different processes and capabilities, and how Alabama Heat Exchangers continues to provide unmatched quality and customization to its clients.
By Sara Mathov, Heat Exchanger World
A family company was founded
Alabama Heat Exchangers is a family business, and always has been. “My mother and father started the company in 1986. After many years working in the industry and listening to the needs of his clients, my father decided to start his own heat exchanger company. His first job for this new company was re-tubing a heat exchanger in his own garage. Shortly after that, they opened a small office, and a few years later moved into what is now our current location in Theodore, Alabama,” said Lightcap.
Over the years, the company has grown to have the reputation it does today. “I started here a long time ago in high school sweeping floors and doing deliveries, eventually getting to know welding and fitting and taking over the lead in QC for 6 years and then moving into the role of CEO,” stated Lightcap. “We have grown a lot and continue to do so, but we do not forget our company values, and one of those values is family. We hire families. We have always had siblings working here and families working together. It is a different dynamic than most companies, but one we are proud of.”
“We are an engineered-to-order setup. We do custom manufacturing, where we get specifications from an end user, for a heat exchanger for example, to meet certain performance that they need.”
Processes and specialties
Alabama Heat Exchangers offers many services: drafting and engineering; machining, welding, and fitting; and service, repair, and quality control. “We start the design process from there. We then do thermal engineering, size the heat exchanger, and get approval from the client to ensure it is what they want. Then, we do mechanical design to ASME Standards and move into the purchasing phase, acquiring all the needed materials. Once they arrive, QC performs thorough inspection before issuing to production, and we then begin building, fitting, welding, machining, testing and finishing until we have a completed custom piece of equipment ready to meet our customer’s production needs. This process can begin further along in the process as well as we see many ‘in-kind’ replacements and vessels and reactors.”
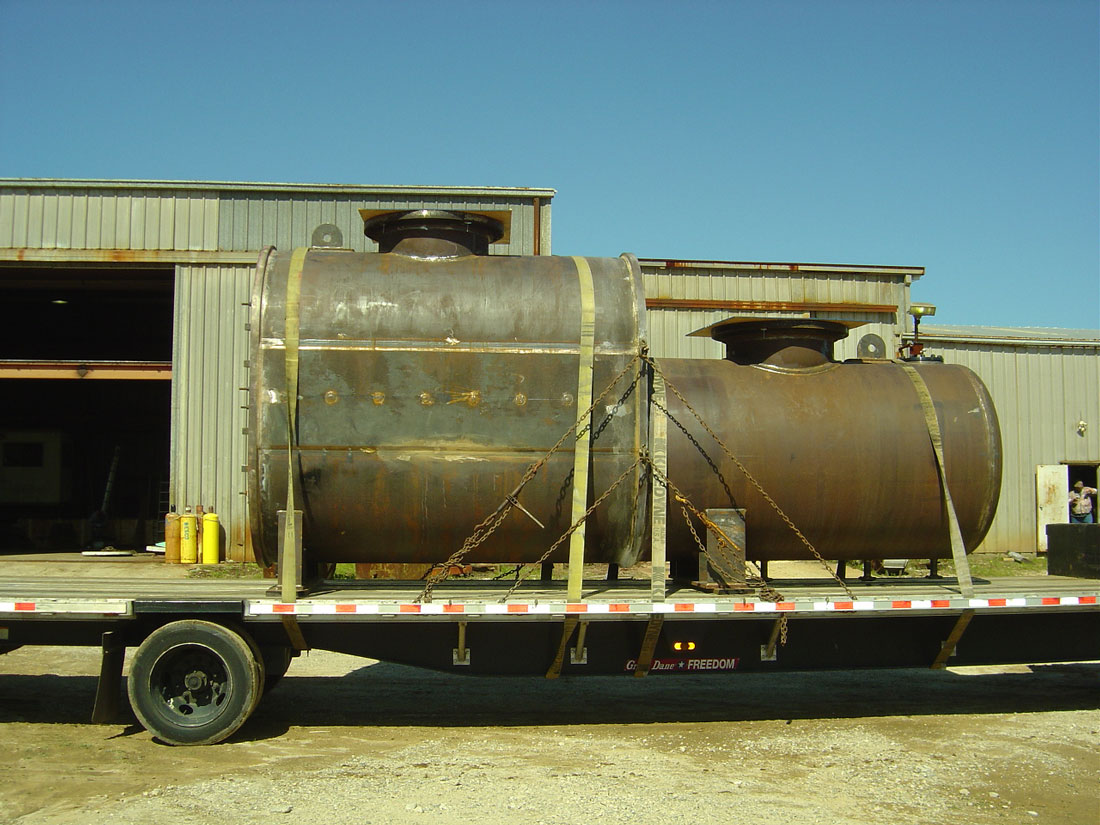
The welding capabilities of the company include a wide array of alloys, from carbon and stainless steel, to nickel alloys, Hastelloy, and more. “We do a lot of dissimilar welding as well. This is all carefully monitored by our quality control process, ” he continued.
Alabama Heat Exchangers can meet just about any non-destructive testing requirements provided by either end user or whichever standard is governing construction (mostly ASME). The company uses a mix of both in-house and third party testing depending on the requirement.
“It is important to highlight that we not only meet, but exceed the code. We view code requirements as the level at which the bar is set, and we always go above the bar. This is woven into the fabric of our culture as a top-quality mindset. Everybody here, from our experts to someone sweeping the floors, knows that quality matters, and knows our code,” stated Lightcap.
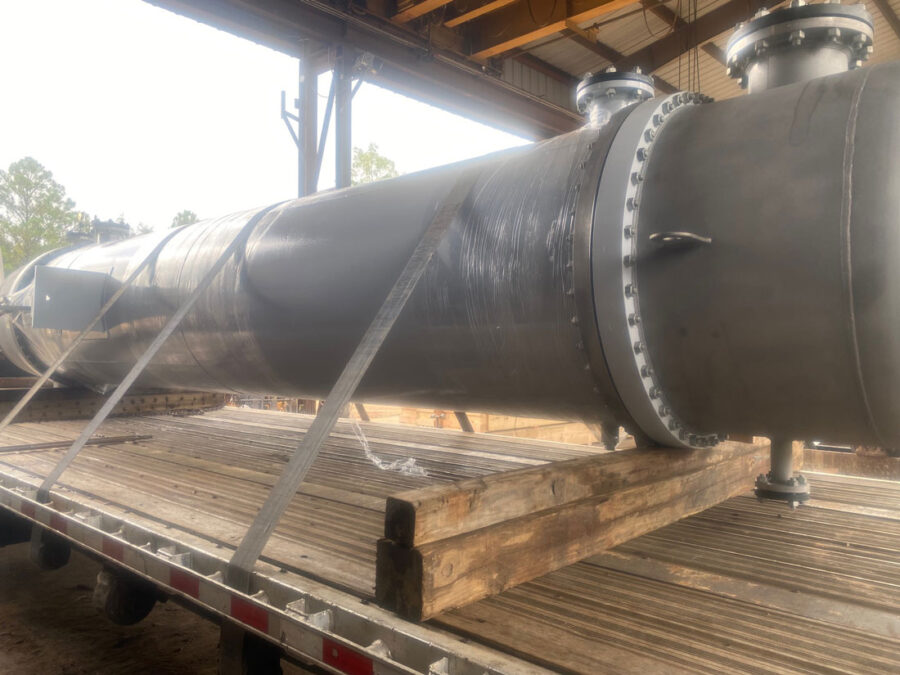
Unmatched quality and speed
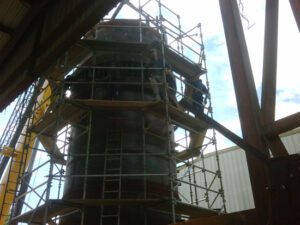
One unique element of Alabama Heat Exchangers is that most new fabrication is made from scratch, and customized to meet the end user’s requirements. “We are also known for going out to take field measurements, to ensure a piece of equipment can be replaced with the exact specifications. We fabricate a replacement that fits perfectly back into place without the client needing to adjust any piping,” said Lightcap.
“Our mantra is to keep the customer up and running,” he said. “Customers come to us because of the depth of our technical knowledge. We are the go-to for ASME codes, safety, and more. Customers feel comfortable in our hands, and this helps us stand out.” Alabama Heat Exchangers’ main customer base is specialty chemical manufacturers. Other applications include paper mills, power generation, marine, petrochemical, and clean energy/alternative fuel initiatives.
“We have many years of experience with all of these different alloys, and we always stand behind our work. We are all about keeping the end user up and running.”
Not backing down from a challenge
Referring back to their mantra, to keep the customer up and running, and keeping downtime to a minimum, Alabama Heat Exchangers has multiple examples of going above and beyond expectations of their customers. Lightcap recalled when a paper mill sent a fairly large heat exchanger, about 30 feet long and 5 feet in diameter, all 304L stainless steel, for a re-tube. However, when it arrived, they found stress-corrosion cracking throughout the entire exchanger, making the equipment barely operational. “After telling the customer they essentially needed a new heat exchanger, they came back saying they would need it in four weeks. So, I spoke with my team and we agreed to get it done, and we shipped on time. The end user was well pleased as they did not lose any days on their shutdown window. We are very proud of that, and we just made it happen.” For reference, normal turnaround on a similar job is estimated at about three months.
“Another project we are proud of was when a plant wanted to add three feet of vertical length to a 15-foot diameter tank in place on site. First, we developed a plan of action. Then, we fabricated a new section of the tank. We cut the original tank and, using a portable water jet system, put the new assembly in place. The customer was so pleased because everything fit within a 32nd of an inch, over the entire 15-foot diameter,” shared Lightcap.
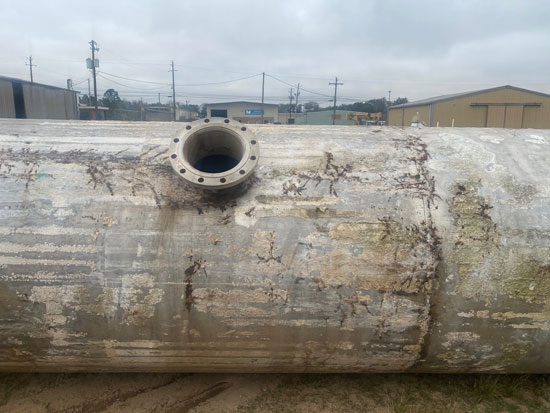
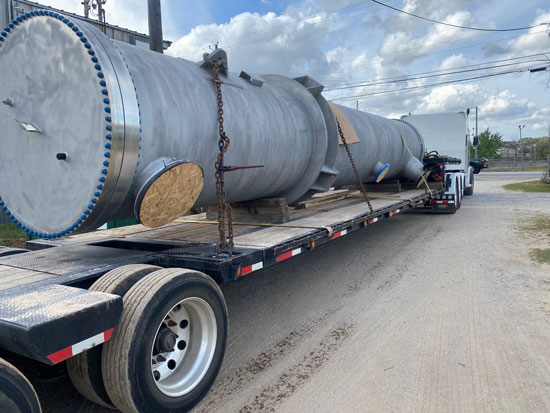
Clean energy and emissions
Lightcap said there has been a large increase in clean energy projects, including biodiesel plants, CO2 scrubbers, and custom equipment to meet emission requirements.
“We have done projects at several universities and new green start-ups, all related to clean energy emissions and research,” he said.
One of the first initiatives that was highlighted was wind energy, said Lightcap. “Using compressed air for wind farms, in times without wind, was something we played a part in. We built tanks, pumps, and ASME code equipment, to help with the pilot version of this. We then scaled it up and built the full-size version, that still exists in Texas as one of the largest single-piston pumps ever built, at 14-feet diameter and 40 feet tall.”
“Our mantra is to keep the customer up and running.”
“We are going to play a big role in building these custom pieces of equipment for companies that have great ideas of how to harness energy. We are excellent at following specifications, codes, and safety, along with a very high-level skill in welding, machining, and fabricating.
Combined with our get it done, and get it done right attitude, we will provide great support for companies in clean energy initiatives.”
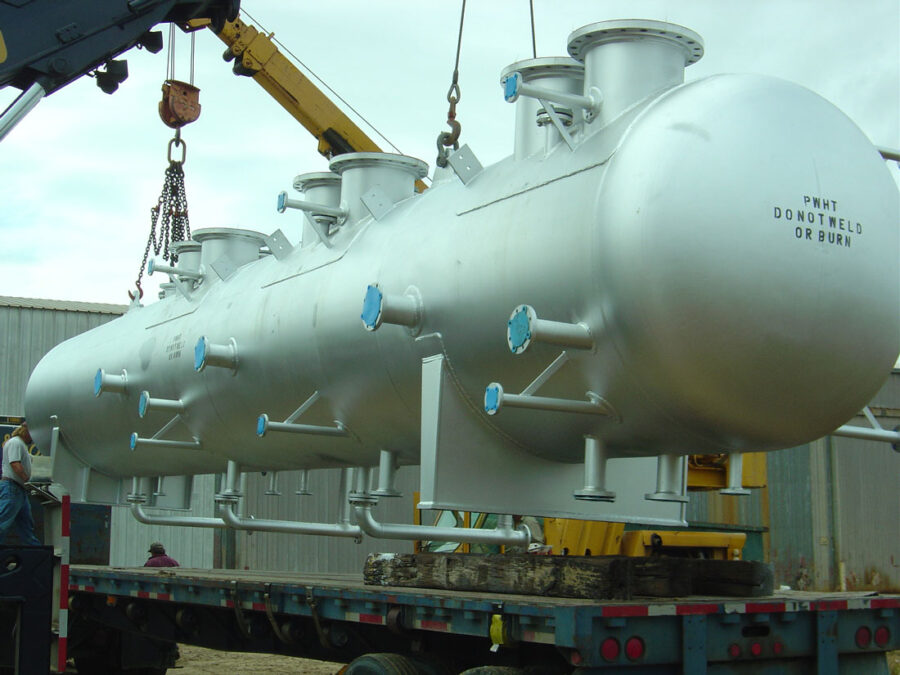
The future of Alabama Heat Exchangers
Going forward, Alabama Heat Exchangers will continue to grow and expand. “We have been around the same size facility for about 30 years, and we are ready to take the company to a higher level. Because of that, I plan to expand into different regions. We have always built equipment that has gone all over the world, but I would like to start expanding our presence, starting in the Houston and Louisiana areas,” said Lightcap.
“Over the years, we have stayed in a smaller area radius, where most of our work is done. We are now at the point where I want to bring our skills and expertise to a larger area, and maintain a greater reach. The company is growing, and I am excited to be leading that initiative,” concluded Lightcap.
About this Featured Story
This Featured Story was first published in Heat Exchanger World Magazine in July/August 2022. To read more Featured Stories and many other articles, subscribe to our print magazine.
Featured Stories are regularly shared with our Heat Exchanger World community. Join us and share your own Featured Story on Heat Exchanger World online and in print.